专利名称:新型晶片锯割系统的制作方法常规线锯装置通常包括多个线,其相对于要被锯割的铸锭或工件而沿单一方向移动。线锯装置通常被用于电子产业,以锯割包括铁磁体、石英以及矽土的铸锭,以获得材料薄片,例如多硅或单晶硅,或甚至新型材料,例如GaAs,InP, GGG或其他石英、合成蓝宝石以及陶瓷材料。相较于诸如金刚石盘锯割的其他技术,材料的高价使得线锯更具吸引力。在公知的装置中,由平行的多个圆筒组件构成了锯割区域。这些圆筒(被称为线引导)刻有槽,其界定了线层之间的间隔,即片的厚度。要被锯割的工件被固定在支撑体上,其垂直于线层移动。工件的移动速度界定了切割速度。线的更新以及对其张力的控制在用于线的所谓管理区域中发生,其位于铸锭或工件被切割的锯割区域之前。影响切割的研磨剂是固定在线(例如用于金刚石线)上的磨料,或以片或浆的形式设置的自由磨料。线仅起用于磨料的承载体的作用。在对要被锯割成薄片的工件进行切割期间,张紧线被线导引圆筒导引并张紧。对于大量的应用,锯割片(也被称为晶片),相较于要被锯割的工件的横截面或直径,具有极小的厚度。锯割片因此具有柔性,并且能够屈曲并弯曲以与相邻片接触。这种屈曲对于切割的精度以及平坦性而言是不希望的,并且会在锯割片的表面上造成波动、条纹以及不希望的不规则。这些甚至达到数微米的不规则足以导致片不能够被用于特定应用,例如用于太阳能产业以及用于半导体的硅。片的形变甚至会导致微裂纹及裂纹,特别是接近片被连接至其支撑体的耦合点的位置处。线锯技术已经在形成光伏型衬底的处理中获得优势。光伏(PV)或太阳能电池是将太阳光直接转换为直流(DC)电能。常规PV电池包括小于约0.185mm厚的p型硅晶片、衬底或片,具有布置在P型衬底的顶部上的η型硅材料的薄层。总体上,基于硅衬底的太阳能技术采用两种主要策略来通过PV太阳能电池来降低太阳能电力的成本。一种方式是增大单结器件(即,每单位面积的电能输出)的转换效率,而另一种方式是降低与制造太阳能电池相关的成本。因为由转换效率引起的效率成本降低会受到基本热力学以及物理限制的限制,故可能的增益量取决于基本技术优势,例如这里公开的各方面。其他实现商业可用太阳能电池策略在于降低形成太阳能电池所需的制造成本。为了满足这些挑战,大体需要满足以下太阳能电池处理要求:1)需要改进用于衬底制造设备所有成本(CoO)(例如,高系统输出能力,高机器工作时间,廉价机器,廉价消耗成本),2)需要增大每处理周期的处理面积(例如,减少每Wp的处理),以及3)形成层的品质以及膜堆叠形成处理需要被很好地控制,以有效地制造高效能太阳能电池。因此,需要成本有效地形成并制造用于太阳能电池应用的薄硅衬底。[0007]此外,随着对太阳能电池装置的需求的持续增长,存在以下趋势,即通过增大衬底产出来降低成本,增大太阳能电池衬底的尺寸以增大在太阳能电池工作期间能够被收集的电量,增大晶片锯系统的产出(MWatts/yr),减小消耗成本,改进在衬底上执行的沉积处理的品质。为了降低衬底的形成成本,希望设计新型锯割系统以及晶片锯割处理次序,以具有较高的衬底产出以及改进的晶片锯割处理产量。发明内容着眼于此,提供了根据独立权利要求1的晶片锯割系统以及根据权利要求8的对晶片锯割系统中的铸锭进行锯割的方法。根据从属权利要求、具体描述以及附图,可以了解其他优点,特征,方面以及详细特征。本发明大体上提供了一种晶片锯割系统,包括铸锭输入模块、铸锭输出模块、两个或多个线锯腔,其分别包括两个线引导圆筒;至少一个线,其被布置横跨两个所述线引导圆筒;支撑台,其被构造以接收单一铸锭;以及铸锭定位系统,其被构造以将布置在所述支撑台上的所述单一铸锭压靠至所述至少一个线;以及机器人,其被构造以在所述铸锭输入模块、所述两个或更多线锯腔中至少一者以及所述铸锭输出腔之间传输所述单一铸锭。根据晶片锯割系统的实施例,铸锭输入模块、铸锭输出模块以及两个或更多线锯割腔被可传输地耦合至传输腔。根据晶片锯割系统的实施例,机器人被耦合至传输腔。根据晶片锯割系统的实施例,两个线导引圆筒的长度是310_至370_。根据晶片锯割系统的实施例,两个或多个锯割腔被构造用于一次锯割一个铸锭。根据晶片锯割系统的实施例,两个或多个锯割腔被构造用于锯割一个铸锭,其一次设置有310mm至370mm长度的负载。本发明的实施例还提供了一种方法,用于在晶片锯割系统中锯割铸锭,包括:将单一铸锭从输入模块传输至相对于传输腔的传输区域布置的多个线锯腔中一者;对所述线锯腔内的所述单一铸锭进行锯割,其中,锯割所述单一铸锭包括:从布置在所述传输腔中的机器人接收所述单一铸锭;使所述单一铸锭抵靠横跨两个线引导体布置的线层;并且相对于所述单一铸锭来移动所述线层;并且从所述线锯腔向输出模块移动所述锯割铸锭。为了更详细地理解本发明的上述特征,可通过参考实施例来对以上简要描述的发明进行更详细的描述,一些实施例在附图中示出。但是,应当注意,附图仅示出本发明的典型实施例,因此不应对其范围构成限制,本发明可涵盖其他等同实施例。图1A是根据这里描述的一个实施例的晶片锯割系统的立体图。图1B是根据这里描述的一个实施例的可在晶片锯割系统中使用的机器人装置的立体图。图2是根据这里描述的一个实施例的晶片锯割系统的立体图。图3A是可在根据这里描述的一个实施例的晶片锯割系统中使用的晶片锯割腔的侧视图。图3B是在根据这里描述的一个实施例的晶片锯割腔的晶片锯割区域中布置的铸锭的立体图。图3C是可在根据这里描述的一个实施例的晶片锯割系统中使用的晶片锯割腔的侧视图。图3D是可在根据这里描述的一个实施例的晶片锯割系统中使用的晶片锯割腔的侧视图。图4是可在根据这里描述的一个实施例的晶片锯割系统中使用的晶片锯割腔的立体视图。图5是在根据这里描述的一个实施例的晶片锯割腔中使用的线导引组件的侧视图。图6A是可在根据这里描述的一个实施例的晶片锯腔中使用的晶片锯割腔的侧视图。图6B是根据这里描述的一个实施例的图6A中所示的晶片锯割腔的另一侧视图。图7A是可在根据这里描述的一个实施例的晶片锯割系统中使用的晶片锯割腔的侧视图。图7B是根据这里描述的一个实施例的图7A中所示的晶片锯割腔的另一侧视图。为了清楚起见,在合适的情况下,已经使用了相同的参考标号来表示图中相同的元件。无需多言,可以想到一个实施例中的特征可被加入其他实施例。本发明大致提供了一种晶片锯割系统,其包括多个线锯腔,其分别可独立锯割铸锭以形成薄衬底。晶片锯割系统可被用于基于较大工件(例如铸锭,基体或块)来形成不同类型的衬底或晶片,例如太阳能电池衬底,半导体衬底或其他有用衬底。在一个构造中,晶片锯割系统被构造用于接收晶体硅(C-Si)铸锭并且执行形成干净衬底所需的全部处理步骤。为了方便讨论并避免混乱,词语“铸锭”在这里用于广义地指较大工件或未切割器件,其将在晶片锯割系统中被锯割。图1A是晶片锯割系统100的立体图,其包括多个线锯腔300,布置在中央传输腔125上并/或连接致中央传输腔125。在一个示例中,为了改进产出及腔工作时间,晶片锯割系统100包括至少六个线锯腔300,其可独立地锯割铸锭。但是,可以使用更少或更多数量的线锯腔300。以下结合图3A-3D,4,6A-6B以及7A-7B示出并描述了可在晶片锯割系统100中使用的线锯腔300的各种构造。晶片锯割系统100大致包括输入模块102、中央传输腔125、中央机器人120、输出模块110、系统控制器128以及多个线锯腔300,其被布置在形成于中央传输腔125上的各处理位置103-108处。在一个实施例中,线锯腔300分别安装在中央传输腔125上,或连接致中央传输腔125。线锯腔300通常被安装在中央传输腔125上或连接致中央传输腔125,使得线锯腔300彼此分别振动地隔离开,并且与中央传输腔125隔离开,以避免在锯割期间产生的振动对其他相邻腔中一者中的晶片锯割处理产生影响。图1B是机器人装置(例如,中央机器人120)的立体图,其可连接致中央传输腔125,以从布置在晶片锯割系统100中的各类处理腔传输未处理以及已处理铸锭。在处理过程中,未切割铸锭通过中央机器人120经由传输区域从输入模块102被传输致线锯腔300中一者。然后,在线锯腔300中被锯割之后,锯割铸锭被传输至输出模块110。在一个实施例中,清洗站(未示出)(例如,图2中的参考标号209)被布置在处理位置103-108中一者内,并被用于在其被中央机器人120传输至输出模块110之前从锯割铸锭清除浆液材料。中央机器人120大致包括机器人装置,例如图1B所示的SCARA机器人或六轴机器人,并且至少包括一个端部效应器121,122,其能够拾取铸锭并且将铸锭从一个腔传输至晶片锯割系统100中的另一腔。在一个实施例中,中央机器人120包括至少两个端部效应器121以及122,其可被用于传输铸锭通过晶片锯割系统100。在该构造中,第一端部效应器121可被用于从输入模块102接收未切割铸锭(例如,干净工件),并且第二端部效应器122可被用于从线锯腔300向输出模块110传输锯割铸锭(例如,湿、脏以及易碎器件)。第二端部效应器122可包括支撑盘元件(例如,柔性刷类元件(未示出)),其连接至端部效应器122以在传输过程中支撑易碎切割晶片或衬底。在一个实施例中,端部效应器121及122的一部分被构造以与安装板376 (图4)(其上安装有铸锭317)配合,以确保可靠地传输未切割及已锯割铸锭通过晶片锯割系统100。输入模块102大体包括一个或更多存储架(未示出),其被构造以接收已经被接合至安装板376的未切割型铸锭317 (图3A及图4)。在一个实施例中,安装板376包括陶瓷材料,其包括形成在其中的多个流体槽(未示出),以允许在铸锭317上已经执行了晶片锯割处理期间及/或以后的热交换及/或冲洗流体流入。输出模块110大致包括一个或更多存储架(未示出),其被构造以在已经于铸锭317上执行了晶片锯割处理之后接收铸锭317以及安装板376。输出模块110还可包括冲洗装置(例如,DI水传输系统)或冲洗站,其能够保持锯割铸锭潮湿,由此在锯割处理中使用的浆液将不会在处理铸锭上干燥。在一个实施例中,输出模块110可包括冲洗装置/系统,其清洁锯割铸锭,以移除在形成的衬底的表面上发现的任何污染物。大体上,系统控制器128被用于控制一个或多个部件以及在晶片锯割系统中执行的处理。系统控制器128被大体上设计以便于晶片锯割系统的控制以及自动化,并且具体包括中央处理单元(CPU)(未示出),存储器(未示出)以及支持电路(或I/O)(未示出)。CPU可以是任何形式的计算机处理器中的一种,其被用于工业设置,以控制各种系统功能、衬底运动、腔处理、处理正时以及支持硬件(例如,传感器、机器人、电动机、正时装置等),并且监控处理(例如,化学浓度、处理变量、腔处理时间、I/O信号等)。存储器连接至CPU,并且可以是可用存储器中一种或多种,例如随机访问存储器(RAM),只读存储器(R0M),软盘、硬盘或任何其他形式的本地或远程数字存储器。软件指令及数据或被编码并存储在存储器中以对CPU发出命令。支持电路也连接至CPU以通过常规方式来支持处理器。支持电路或包括高速缓存、电源、时钟电路、输入/输出电路、以及子系统等。由系统控制器128可读的程序或计算机指令确定可在衬底上执行何种任务。优选地,伴随在晶片锯割系统中的各线锯腔300中执行的各种晶片锯割配方任务以及各种晶片锯割腔处理配方步骤,程序是可由系统控制器128读取的软件,其包括编码以执行与监控相关的任务,执行并控制运动、支持以及/或在晶片锯割系统中对铸锭的定位。图2是线性晶片线锯系统200的立体图,其包括多个线锯腔300,其布置在传输腔225上并/或连接至传输腔225。大体上,可将任何数量的线锯腔300布置在线性机器人220的任一侧上,以实现希望的系统产出。在一个示例中,对于改进的产出以及腔可用性,晶片线锯系统200包括布置在一侧的至少六个线锯腔300,或均匀分布在传输腔225的两侧。但是,可以使用更少或更多数量的线锯腔300。晶片线锯系统200大体包括输入模块202、传输腔225、线性机器人220、输出模块210、系统控制器128以及多个线锯腔300,其被布置在形成于传输腔225上的各个处理位置203-206以及212-215处。在一个实施例中,线锯腔300被分别安装在传输腔225并连接至传输腔225。线锯腔300通常被安装在传输腔225上并连接至传输腔225,使得如上所述线锯腔300被彼此振动隔离开并且与传输腔225隔离开。以下结合图3A-3D,4,6A-6B以及7A-7B示出并讨论可在晶片锯割系统100以及/或200中使用的线锯腔300的各种构造。如上所述,输入模块202以及输出模块210大体类似于输入模块102以及输出模块110,因此不再下面复述。线性机器人220被用于从输入模块202向线锯腔300中一者传输未切割铸锭,随后在执行了锯割处理之后,锯割铸锭被传输至清洁站209或输出模块210。在一个实施例中,清洁站209被用于在来自锯割铸锭的浆液材料被线性机器人220传输至输出模块210之前清洁并干燥浆液材料。机器人220大体上包括常规机器人装置,例如SCARA机器人或6轴机器人,其被构造以沿轨道221 (即,图2中的方向“M”)移动,轨道221被布置在传输区域中,该传输区域在晶片线锯系统200的长度上扩展。大体上,线性机器人220具有至少一个端部效应器(未示出),例如上述端部效应器121,122,其能够拾取铸锭并且将铸锭从晶片线锯系统200中的一个腔传输至另一腔。图3A是可在晶片锯割系统中使用的线锯腔300的侧视图,例如上述晶片锯割系统100以及200。图3B是铸锭317的立体图,通过线锯腔300中的各自动部件使铸锭317抵靠布置在线锯腔300的锯割区域318中的线323的层319,可以部分地锯割铸锭317。参考图3A,锯割腔大体包括框305、安装在框305上使得其旋转轴线彼此平行布置的线导引圆筒321以及322,以及用于使铸锭317抵靠线323的层319的致动器组件310。线323从供应轴326被接收,然后围绕线导引圆筒321,322缠绕,以在锯割区域318中形成平行线的至少一层319。然后使线323返回至合适的接收装置,例如接收轴327。导引圆筒321或322中至少一者连接至驱动电动机328 (图4),其适于沿单一方向(或,优选地,以往复运动方式(例如,前进第一距离然后后退第二距离(例如,第一距离〉第二距离)))移动布置在锯割区域318中的线323。线导引圆筒321以及322可被一个或多个轴承329 (图4)支撑,其被连接至线张紧系统(未示出),其适于通过相对于另一个导引圆筒来移动一个导引圆筒来使线323实现希望的张力。在处理过程中,系统控制器128可监控驱动电动机328的转矩,以确定通过致动器组件310施加至铸锭317的力。在一个实施例中,在布置在晶片锯割系统100,200中的各个线锯腔300中,一次仅布置并锯割单一铸锭317。认为利用线的单一层319来处理单一铸锭具有远胜于现有线锯割系统的优势,即利用相对较低线锯割速度(例如,铸锭运动速度200-400 μ m/min以及线速度15m/s)通过一次锯割多个铸锭来使铸锭产出最大化。在单一铸锭晶片锯割腔中的铸锭317的“负载”或长度374 (图3B)成比例地少于在现有晶片锯割系统中处理的铸锭317的数量,可以通过增加线速至少达一定比例量,使单一铸锭晶片线锯腔300的产出等于现有晶片锯割腔。在一个示例中,使用常规线锯腔来以约200 μ m/min的铸锭运动速度来一次性处理四个铸锭,而这里描述的创造性构造用于以至少800 μ m/min的铸锭运动速度来锯割单一铸锭,由此实现了类似的晶片锯割产出。在线锯腔300中一次锯割单一铸锭是有利的,原因如下。首先,例如通过仅使用两个导引圆筒321,322 (图3A)而非通常的四个导引圆筒(与常规线锯装置类似,具有缠绕全部四个导引圆筒的线),一次锯割一个铸锭317可极大简化导引圆筒321,322的安装、对准以及结构构造。其次,两个导引圆筒321,322系统的惯性从大于两个线导引容纳系统被大大地降低,由此能够使用已经被证实能够延长线寿命的往复线运动(例如,在需要从线锯割处理去除线之前),并且由此缩短腔维护时间。在一个实施例中,通过利用低质量密度材料(例如,碳填充增强聚合物或其他类型合成材料)来有利地减小线导引圆筒321,322的惯性。第三,由于减小线层跨度的能力或线导引圆筒321,322之间的缝隙307 (图3A),因为一次仅处理单一铸锭,故在两个导引圆筒线锯割系统中,线平行度、线间距(例如,线之间的间隔)以及线弯曲的变化在晶片锯割处理期间大大降低。线平行度、线间距以及线弯曲的减小的变化将改进线锯处理的总厚度变化(TTV),由此改进了锯割处理产能以及/或允许可靠地形成较薄晶片。较薄锯割晶片被用于形成下一代太阳能电池以及半导体器件。因此,根据一个实施例(其可与这里描述的其他实施例结合),铸锭长度可以是310mm至370mm,例如330mm至350mm。因此,可以实现锯割速度、晶片数量、产量以及锯割装置的复杂性之间的利益折衷,以改进CoO。在一个实施例中,通过临时支撑体,单一铸锭317被安装在支撑台312上,例如安装板376(图3A以及图4)。通过使用致动器组件310,支撑台312沿Z方向垂直移动,致动器组件310可包括柱311以及电动机315,其适于在锯割过程中将铸锭317抵靠至线323的单一层319。线导引圆筒321,322的外围被雕有槽333 (图5),其界定了线的相邻线层319之间的间距,因此界定了锯割片的厚度。这些片通过槽或锯割缝隙317A彼此分离开(图3B)。根据一些实施例,其可与这里描述的其他实施例结合,槽被构造,形成170 μ m或以下的晶片厚度,例如HOym至170μπι,例如160 μ m。因此,通过增加利用一次切割来制造晶片的数量,所有成本可进一步被降低。因此,方法的其他实施例可包括:对170μπι或以下的晶片进行锯割,例如140μπι至170 μ m,例如160 μ m。线323被线导引圆筒321,322拉伸并导引且张紧,以往复运动或连续单方向运动。该线323可包括弹性钢,具有包括0.1mm至0.2mm之间的直径,由此锯割硬材料的铸锭,或更具体成份的铸锭,例如组II1-V以及I1-VI,GGG (钆镓石榴石),蓝宝石等的元素的成份,成为约300 μ m或以下的片,或优选地用于下一代衬底达180 μ m或以下的厚度。研磨剂大体上是商业产品,例如金刚石、碳化硅、氧化铝或其他有用材料,其被用于改进铸锭锯割处理。研磨剂可被固定至线323,或处于自由状态,其在液体(例如,PEG)中悬浮,例如浆液,其用作研磨颗粒的传输。为了减小线锯腔300的不工作时间,在一些实施例中,希望焊接,或接合新的线至大概完全使用的线323的端部,其被布置在供应轴326上,由此允许线锯割腔,以连续处理铸锭317,而无需取下以替换掉使用的线323。线锯腔300通常被设置有保持装置377,其被布置以在锯割过程中以保持一部分或全体锯割片317B (例如,未形成的衬底)大致彼此平行,使得在锯割片过程中将锯割缝隙317A的宽度保持为大致恒定。图3C是线锯腔300的侧视图,其具有致动器组件310,包括铸锭定位系统340。铸锭定位系统340大体上包括轨道341以及一个或多个线性电动机342 (示出了两个),其被构造以分别沿轨道341移动,以使得臂343、支撑台312以及铸锭317相对于线323的层319移动。在该构造中,线性电动机342相对于彼此以及相对于轨道341的运动可被用于沿Z方向来移动铸锭317,并可相对于线323的层319为铸锭317提供倾斜度。相对于一次性抵靠线323的全部表面(这会导致线偏离形成在线导引圆筒321,322上的槽333,并/或损坏),在锯割处理的初始阶段相对于线323改变铸锭317的角度或铸锭317的倾斜度的能力对于允许锯割缝隙317A被均匀地形成在铸锭317上非常重要。图3D是线锯腔300的侧视图,其包括具有铸锭定位系统350的致动器组件310。铸锭定位系统350大致包括杆353的两个“双杆联接”,其连接至基板313、支撑台312以及一个或更多线性电动机342,其被构造用于分别移动各个双杆联接。在处理过程中,致动器352被构造以相对于线323的层319移动支撑台312以及铸锭317。在该构造中,因各致动器352引起的运动而造成的双杆联接的相对运动被用于沿Z方向移动铸锭317,并且相对于线323的层319为铸锭317提供倾斜度,如下所述,这非常重要。图4是具有自动浆液传输系统380的线锯腔300的侧视图。自动浆液传输系统380大致包括浆液补充源381、浆液供给罐382、构造用于向线323及/或铸锭317输送浆液的浆液传输管路390,391、浆液返回罐383、浆液热交换装置384 (例如,流体型热交换器)以及浆液泵386,其通过阀389从浆液返回罐383向浆液供给罐382移动包含浆液的研磨齐IJ。在一个实施例中,浆液供给罐382包括搅拌机构385,其被构造用于搅拌浆液“S”。在晶片锯割系统100,200的一种构造中,浆液传输系统380是中央系统,其被构造用于将需要量的浆液输送至在各个线锯腔300中被锯割的铸锭317。在晶片锯割系统100,200的另一构造中,分离自动浆液传输系统380被布置在各线锯腔300处,以允许在锯割过程中对向铸锭317的浆液输送进行单独控制。如上所简述,在线锯腔300的一个实施例中,流体传输系统375被构造以向形成在安装板376中形成的槽(未示出)输送流体,例如DI水,冷却剂或气体,以在已经完成了晶片锯割处理之后,在处理或冲洗片(或衬底)过程中冷却铸锭317。图5是线导引体321,322的侧视图,其被构造以在于线锯腔300上执行维护活动过程中进行迅速替换。在一个实施例中,线导引包含组件包括线导引体321,322,与形成在线导引体321,322上形成的支撑表面503配合的轴承502以及与形成在线导引体321,322上的支撑表面504配合的轴承504。由于在线导引体321,322各端部处使用的轴承的位置、形状以及类型,当线导引体被磨损时,可以迅速对其进行替换。因此,根据本发明的各个方面,这里公开的晶片锯割系统可包括夹持组件,用于连接至线锯的圆柱形线引导体以切割晶片。夹持组件可包括轴侧连接器,其适于连接至线锯的轴,该轴具有旋转轴线。轴侧连接器包括外表面,其垂直于轴线,并且适于抵靠线引导体的补充连接器的补充外表面,以及外表面与轴线之间的圆锥表面,该圆锥表面相关于轴线对称布置,并且适于抵靠线引导体的补充圆锥表面。还可以是用于将圆柱形线引导体连接至线锯的轴的夹持组件包括外表面,其垂直于轴线并且适于抵靠轴的补充连接器的补充外表面,以及外表面与轴线之间的圆锥表面,该圆锥表面相关于轴线对称布置,并且适于补充连接器的补充圆锥表面。线锯适于切割晶片。轴具有旋转轴线。根据实施例,夹持组件的外表面是平坦的。此外,或替代地,根据实施例,夹持组件的外表面与圆锥表面相邻。其可以是环形。[0055]可以是外表面的一部分被布置在一定距离处,其是从轴线至轴侧连接器的径向外边缘的径向距离的至少约65%,70%, 75%或80%。外表面可以是环状,可以是外表面选择性地包括1,2,3或4个部分。轴侧连接器的圆锥表面可包括可形变材料。大体上不限于任意实施例,圆锥表面可包括1,2,3或4个圆锥部分。根据实施例,夹持组件的轴侧连接器是中空的。轴侧连接器可以是母连接器。夹持组件可包括连接至轴侧连接器的轴。夹持组件可保持机构,其通常从液压系统、气压系统、螺丝以及其组合中选出。根据实施例,夹持组件的圆锥表面可被安装至线引导体。外表面可与圆锥表面相邻。圆柱形线引导体可碳纤维增强型聚合物部分。图6A及图6B是线锯腔300的侧视图,如上所述,其可被用于晶片锯割系统100,200。参考图6A-6B,线锯腔300大致包括框601、安装在框601上的线导引体321,322、供应轴326、接收轴327、铸锭支撑元件铸锭支撑元件611以及其他腔以及上述浆液组件。在该构造中,铸锭支撑元件611被构造以引导并支撑铸锭317,其被抵靠至线层319 (图3A)。图7A及图7B是线锯腔300的侧视图,其被用于晶片锯割系统,例如上述晶片锯割系统100以及200。参考图7A-7B,线锯腔300大致包括框601、安装在框601上的导引圆筒321,322、供应轴326、接收轴327、铸锭定位系统350以及上述其他腔及浆液组件。在本构造中,结合图3D所述的上述铸锭定位系统350被构造以引导并支撑铸锭317,同时其被抵靠至线层319 (图3D)。在一个构造中,浆液供给罐382被布置在铸锭定位系统350上,或位于其上方。虽然以上涉及本发明的实施例,但不脱离本发明的基本范围,可以构思出本发明的其他及进一步实施例,并且本发明的范围由所附权利要求决定。
新型晶片锯割系统制作方法
- 专利详情
- 全文pdf
- 权力要求
- 说明书
- 法律状态
查看更多专利详情
下载专利文献
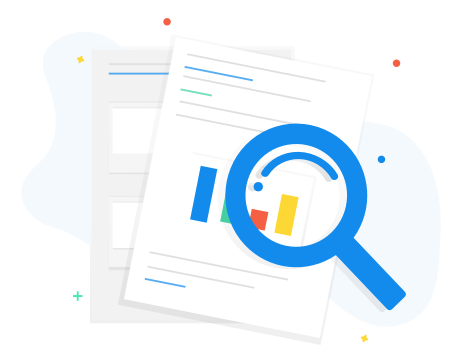
下载专利
同类推荐
-
安德烈亚斯·施密特安德烈亚斯·施密特安德烈亚斯·施密特裴明, 郑诗阳裴明, 郑诗阳裴明, 郑诗阳李跃萍, 员健
您可能感兴趣的专利
-
张军冯雨萌冯雨萌冯雨萌乔格·莫斯南格, 迪特尔·里特
专利相关信息
-
丹尼尔·埃文斯丹尼尔·埃文斯小山和里, 市桥正英小山和里, 市桥正英A·H·小欧文斯A·H·小欧文斯A·H·小欧文斯