专利名称:材料处理和设备的制作方法材料处理和设备本发明涉及材料处理方法,并且还涉及用于实现材料处理的设备。本发明针对的问题涉及材料处理,以便所述材料能够被有效地分解成非常小的尺寸。先前我们已描述了一种设备,所述设备包括在圆柱形腔体(cavity)内的旋转转子以实现将颗粒研磨成小尺寸。在澳大利亚专利AU2005204977中描述的在先设备的实例提供了颗粒尺寸的一定程度的减小,但在许多情况下相对低效,并且还不能实现颗粒减小到如所需要的程度。
我们已经发现通过对设备和方法进行相对适度的改变,能够获得改善的处理效率。本发明的一个形式在于一种减小颗粒尺寸的颗粒处理方法,所述方法包括以下步骤将待处理颗粒引入到设备,其中所述设备设有腔室,所述腔室具有大体上圆柱形部分,和旋转转子,同轴放置在所述大体上圆柱形部分内;所述旋转转子限定在两个共环形圆柱形空间之间;至少两个叶片,所述至少两个叶片围绕所述转子的周边等距离分隔开,且每一叶片都从所述转子延伸并且限定位于所述大体上圆柱形部分的内壁与每一叶片的各自的外边缘之间的分隔间隙,存在支撑并且限定在各自叶片之间的空间的一个或多个涡流,并且所述大体上圆柱形部分的至少一些所述内壁具有摩擦诱导表面。本发明的进一步形式在于一种设备,所述设备包括腔室,所述腔室具有圆柱形部分,和旋转转子,同轴放置在所述圆柱形部分内;至少两个叶片,所述至少两个叶片围绕所述转子的周边等距离分隔开,且每一叶片都从所述转子延伸并且限定位于所述圆柱形部分的内壁与各自叶片的外边缘之间的分隔间隙,存在支撑并且限定空间或在各自叶片之间的空间的一个或多个涡流,并且所述圆柱形部分的至少一些内壁具有摩擦诱导表面;用于待处理颗粒进入所述腔室的入口和用于经处理颗粒的出口,所述出口与所述入口间隔开。本发明还在于处理材料由所述设备引入并处理。本发明还在于根据本文的所述方法材料的颗粒尺寸已被减小。迄今,在圆柱形部分上已有光滑内壁。已经发现通过引入摩擦诱导表面,显著提高了处理尺寸减小工艺的效率。所述摩擦诱导表面可位于大体上圆柱形腔室的圆周的间隔位置处,或者在另一个例子中,所述摩擦诱导表面可以围绕所述圆周为连续的。摩擦诱导表面的一个实例包括任意形状部分,伸入支撑和限定空间的至少一些涡流。与所述方法和设备有关的发现是其颗粒处理看起来与进入并且经受涡流内的高能的力有关。这种作用还与以下事实有关,涡流包括较高压部分和较低压部分,进入所述涡流的颗粒会经受诱导干燥的低压环境。这种干燥效果不一定限于水,并且已经发现通过工艺引入的材料在保持的水分上有显著减少。认为此机制包括真空蒸发和也许再凝结,而从颗粒中分离,然后捕捉在气流中,所述气流携带从固体颗粒中分离出的液体蒸汽。摩擦诱导表面的实例包括任意沉积的附着颗粒材料。已经观察到所述摩擦诱导材料的加入看起来不直接作用于通过设备处理的颗粒,只是似乎通过流体介质的相对吸引来诱导的间接作用,通过所述流体介质的相对吸引,所述工艺具有它们的涡流,所述涡流通过叶片与摩擦诱导表面之间捕捉的空气的相对运动,涡流自身始终保持和维持在旋转模式。此也通过以下事实表明,所述事实为迄今为止对任何摩擦诱导表面做过的实验显 示非常小的磨损。为了更好的理解本发明,现在将参照实施方式来描述本发明,所述实施方式将借助附图来描述,其中图I是根据第一实施方式的设备的局部剖透视图;图2是穿过与图I的设备相同的设备的截面的侧视图;图3是根据第一实施方式的设备的去除了顶部的俯视图;图4是根据第二实施方式的设备的局部剖截面的透视图;图5是设备去除了顶部的俯视图,所述设备是根据第二实施方式的设备;图6是根据第二实施方式的切掉了部分和示出相对于向外延伸叶片的摩擦诱导段的排列的截面的放大俯视图;图7是根据第一实施方式的、从壁的排列和向外延伸叶片的相对位置的上方观看时的局部剖截面图;图8示出了现有技术中叶片与光滑内壁的位置关系的实例。实施方式的描述现在将详细参照附图,特别参照表示第一实施方式的附图,具有腔室1,所述腔室I包括由转子3共轴旋转所限定的圆柱形部分。转子3由轴杆4支撑,所述轴杆4由在5处典型地示出的轴承支撑。转子3被防松螺母6固定在适当位置中。转子3设成为由连接到轴杆4的装置可旋转地驱动,所述装置未在图中示出,但是在这种情况下,所述装置包括通过适合成套的滑轮和皮带连接的电动机,以便以一转速来驱动例如250mm直径的转子,所述转速被选择为适用于正被处理的材料,但所述转速通常在12000rpm至20000rpm的范围内。似乎相关的速度是转子的周长处产生的相对速度,发现200km/hr至1200km/hr是有益的。腔室I进一步通过具有上部板7、另一板(further plate)8和限定于两者之间的圆柱壁2限定。转子3具有圆柱形外部尺寸,并且包括多个向外延伸的叶片9,所述多个向外延伸的叶片9在每种情况下具有从转子的顶部延伸到转子11的底部的伸长的矩形尺寸,在每种情况下所述多个向外延伸叶片9被放置成围绕转子3的直径以相同距离分隔开。这些叶片9被在12处典型地示出的多个螺钉紧固。(这些叶片通过装配至互锁槽而紧固在替代的布置中)外壁2具有多夹套13,以便限定水冷(或者,适当加热)空间14,由于进出套管14的诸如16和17处这样的导管,水被引导通过所述水冷空间14。按照类似的方式,由于另一壁(further wall)18和入口导管19和出口导管20也实现对板7进行水冷(或加热)。在这种情况下,待处理的材料竖直通过入口 1,所述入口 I在设备的中心并且与轴杆4的轴线共轴。已经处理过的材料的出口在这种情况下通过罩盖出口 20的收集来引导,其中自与轴杆4的轴线相距相同的直径处的、板8的周围的间隔位置处设有多个这样的罩盖出口。 设有阻气门21,所述阻气门21设置在处理间隙22的下方,并被设置为以便对空气的通路和在处理空间22以外的正被处理的颗粒材料提供某种程度的限制。所述阻气门21包括上表面,所述上表面向竖直的轴线方向倾斜,以便对气流和颗粒提供一些适度的摩擦或阻塞,但是限于某种程度。至此所描述的设备具有处理并且实现颗粒分解的目的,所述颗粒在设备的入口处送入并在其出口处收集,所述出口具有位于转子的外周区域与圆筒的内壁之间的其间区域。转子3的速度即所谓的旋转速度,转子的直径和从转子突出的叶片、叶片的深度和这些叶片的分开的程度被选择为实现材料的高效分解为非常小的尺寸。对设备如何工作的分析表明每个叶片沿着旋转路径时,由于叶片的形状和分离的程度,在每一叶片的后面空气会引起湍流,并且发现设备使用时,实现了高度的脱水,这被认为是在每一叶片的后面立刻形成有涡流,并且进入这种涡流的高真空中心,或者也许进入和离开这种涡流会有冲击,这似乎具有高效的分解和脱水。因此,为了更有效地特别是当装载颗粒时诱导和维持这种涡流,已发现这可以通过增加圆柱形壁2的内侧的摩擦诱导特性来实现。在一种情况下,所述增加圆柱形壁2的内侧的摩擦诱导特性是通过使任意形状和位置的硬颗粒附着到如在23处所示的外壁来实现的。在本实施方式中,这个表面完全设置在圆柱形壁2的所有内表面的周围。在一种情况下,这样的表面由固定在基质中的碳化硅颗粒组成。观察到在使用时所述表面(所述表面为摩擦诱导表面,但是可以称为粗糙表面)不会对正被处理的材料有强力磨削效果。效率的改善似乎是由摩擦诱导表面捕捉引起的,并且使在各个叶片9后面正被引入的、且具有高度摩擦诱导的涡流进一步旋转,涡流自身和将要被承载的颗粒材料的负载将会更强烈。在迄今为止的试验中,当使用根据所述实施方式的这种工艺来研磨材料时,观察到摩擦诱导表面23具有极小的研磨效果,这又导致的结论是,它不是一种与待处理材料的直接作用的材料,而是引起更积极和更有效的涡流的一种间接作用。在比较使用光滑壁与摩擦诱导表面或粗糙壁时,所述作用导致与许多材料有关的效率的改善,并且还导致由于设备的使用而能够减小颗粒的尺寸,且在某些情况下,这些颗粒在尺寸上小到5微米以及更小。在效率上改善的程度随不同材料的处理而变,但是在一些情况下,效率改善了至少100%,也就是说,在对比先前的不包括摩擦诱导表面的情况时,至少对于相同转速和电源可以处理两倍的材料量。第二实施方式包括腔室40 (第一实施例包括腔室40)、入口 41、由轴杆43支撑的转子42、限定圆柱形腔室45的外壁44、具有多个罩盖出口 47的多个矩形且伸长的叶片46。与第一实施方式的不同在于在外壁44内侧上的磨擦诱导表面由分离的段组成,所述段的每一个都具有外表面49,所述外表面49由以固定在基质中的突出任意分隔和形状的颗粒组成的外表面49,由此所述外表面49附着到狭长楔形部件50。这些部件50放置在围绕周长的分隔位置处,所述分隔位置等距离间隔开,所述距离等于在各个叶片46之间的间隔。 然后再一次,第二实施方式的作用是诱导和帮助维持在各个平行叶片46的后面的涡流,但是它们具有的优点是因为它们能够作为段分离地放置,所以它们如果损坏能首先较便宜地制造和替换。形状是略微楔形,所述略微楔形具有最靠近壁44的内表面的前沿,同时一部分沿下游方向从前沿向外突出。可考虑的是通过具有某种程度上受保护的前边缘,这将使保持粗糙部在适当位置的任何焊接基质或涂覆材料发生剥离的可能性降至最小。在某种程度上令人惊讶的是,包括所述分离段还导致相当于将粗糙表面或摩擦诱导表面全部围绕内周长放置时所经历的改善。然后再一次,设备包括其他部分,包括阻气门51。图8是现有技术的图,在图8中,为了得到最好的分解效果,外边缘60与光滑内壁61间隔的距离确实非常小,并且在这种情况下是3mm,但是当然发现具有摩擦诱导或粗糙表面时所述距离会增加,并且在一些情况下仍然得到减小到5微米的精细的颗粒,并且还具有合适的脱水的优点。实例II. 5mm直径的铜线被切成7mm长,并且用作进料进入不包括摩擦诱导表面的设备。光滑壁的水冷圆筒被用作具有倾斜部分的研磨腔室的外壁,且倾斜部分用作低于转子的深度的部分阻气门。在转子上方的重叠是3mm。转子的直径是200mm。三个叶片紧固到转子的外周,围绕转子的直径等间距分隔开,并且从转子突出17mm。每一叶片的形状和尺寸是相同的,通常是矩形的,并且每一叶片在其顶部最外沿和底部最外沿是斜切的。顶部斜角尺寸从边缘9mm且从上向下斜切5mm。在底部的斜角从下向上12臟,并且从外边缘5mm。当设备以14,000RPM的转速旋转时送进铜线进料,先前已经发现所述转速有益于这种特定设置和材料。此将铜材料分解为具有90微米的平均颗粒尺寸的200微米以下的小块。从一次送进的147gms中,20gms保持为直径2mm的大球,并且由于一旦停止送料在设备中没有足够材料来保持研磨工艺进行,因此这些大球在研磨结束时留在腔室中。然后第二次送料,旋转速度增加到19,000RPM,并且尺寸降低到100微米,平均尺寸为50微米。实例2第二实例研磨铜线时,通过外壁上的摩擦诱导表面材料进行,所述摩擦诱导表面材料用于第二次运行。I. 5mm直径的铜线被切成7mm长,并且用作进料进入研磨设备。光滑壁的水冷圆筒用作研磨腔室的外壁,所述研磨腔室具有显著地低于转子的深度的45度锥。在转子上方的重叠是3mm。转子的直径是200mm。三个叶片从转子突出的深度为17mm,并且这些叶片等间距分隔开。叶片的形状是斜切的顶部和底部,顶部斜角的尺寸为距边缘9_且从上向下斜切5mm。在底部的斜角是从下向上12臟,并且距外边缘5mm。当设备以14,000RPM的转速工作时送进铜线进料,这将铜材料分解成200微米以下的小块,平均颗粒尺寸为90微米。从147gms中,20gms保持为直径2mm的大球,并且由于一旦停止送料,在设备中没有足够材料来保持研磨工艺进行,因此这些大球在研磨结束时留在腔室中。然后圆筒的外壁的区段由具有摩擦诱导表面的部分替代,在这种情况下,所述部分添加到外圆筒。这些斜坡是匹配转子的深度(75_)的圆筒的壁的全深度,且结束在倾斜表面阻气门的顶部的正上方。这些部分的宽度是25mm,材料的表面的斜角是3. 5度沿与转子的方向相同的方向流动。铜线第二次经受19,000RPM的研磨。减小尺寸到最终的60微米,平均为3微米。摩擦诱导表面造成提供处理材料尺寸上的显著减小,从而提供了增强的效果并且增加的效率。实例3沸石使用沸石代替铜作为进料重复相同的操作。进料是3_任意形状沸石的砾石。光滑壁的水冷圆筒用作研磨腔室的外壁,所述研磨腔室具有显著地低于转子的深度的倾斜表面阻气门。在转子上方的重叠是3mm。转子的直径是200mm。三个叶片从转子突出的深度为17mm,并且这些转子等间距分隔开。叶片的形状是斜切的顶部和底部。顶部斜角的尺寸为距边缘9mm且从上向下斜切5mm。在底部的斜角是从下向上12臟,并且距外边缘5mm。沸石经受19,000RPM研磨,并且大尺寸是10微米,平均尺寸为5微米。然后重复摩擦诱导表面的部分被添加到外圆筒的情况的测试。这些部分每一个是伸入大体上圆柱形空间的任意形状部分,并且是匹配转子的深度(75mm)的圆筒的壁的全深度,且结束在倾斜表面阻气门的顶部的正上方。这些部分的宽度是25mm,这些部分的每一个的锥度是是3. 5度以沿与转子的方向相同的方向流动。所述沸石经受研磨。进料是3_沸石,并且转子速度是19,000RPM,最终尺寸是7微米并且平均是I. 5微米。·这再一次公开了附加摩擦诱导材料的优点。
本发明公开了一种用于超细粉磨的方法和设备,使用转子在相容的圆柱形壳体中快速旋转,其中在圆柱形表面上的摩擦诱导表面有助于研磨效果的改善。
材料处理和设备制作方法
- 专利详情
- 全文pdf
- 权力要求
- 说明书
- 法律状态
查看更多专利详情
下载专利文献
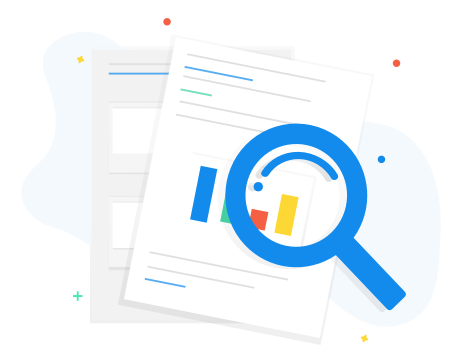
下载专利
同类推荐
-
奉明明马蒂亚斯·布兰德尔马蒂亚斯·布兰德尔新津洋司郎新津洋司郎新津洋司郎新津洋司郎
您可能感兴趣的专利
-
新津洋司郎加藤行加藤行曹仁镐, 韩东柱崔昌奎
专利相关信息
-
刘光明何玉明章小龙, 茅建刚朱秀红王建设, 王琳壮晓健