有机硅浆渣水解处理工艺和副产物及其应用的制作方法 [0002] 有机硅浆渣(以下简称浆渣),是在甲基氯硅烷单体合成过程中采用湿法除尘经 200°C?300°C温度进行闪蒸,得到一种固液体积比约为3 :7的带有流动性的液固混合物。 楽 禮:中的液相部分主要是沸程80?215°C,以娃一娃键、娃一碳一娃键、娃一氧一娃键为主 的高沸点氯硅烷混合物,固相主要为细硅粉和铜、锌等催化剂。由于浆渣中固相部分催化 剂活性较高,液相部分高沸物极易与水发生反应,如果暴露在空气中,就会与空气中的水发 生水解反应,产生大量的氯化氢和氢气等气体,甚至会发生燃烧或爆炸,对环境造成严重污 染。 [0003] 为解决浆渣的潜在风险,国内通常将浆渣与过量水进行水解反应,水解过程中会 产生大量的稀盐酸和固体渣。该方法存在以下问题:一是每吨浆渣将产生的约5吨浓度 1%?8%的稀盐酸量,并且含碳、铜、有机硅聚合物等杂质,实现再次利用的难度较大、成本 较高;二是水解后的固体渣易结块,固体渣内包含的氯化氢不易清除,使固体渣显酸性,在 环境温度高,天气湿度大的情况下仍然会燃烧。经水解处理后的浆渣可降低浆渣储存中安 全环保风险,但不能彻底清除。因此浆渣的处理问题一直是现代有机硅生产技术中的技术 瓶颈。
[0004] 本发明所要解决的第一个技术问题是提供一种易操作、稀盐酸产生量少的有机硅 浆渣水解处理工艺。 [0005] 为解决上述技术问题,本发明采用的技术方案包括以下步骤:
[0006] A、将浆渣与固化剂混合;
[0007] B、加水,完成水解反应;
[0008] 其中,所述的固化剂的作用是吸附或固定浆渣中的液体部分改善水解效果,同时 可中和浆渣水解过程中产生的盐酸;因此所述固化剂宜采用不与浆渣反应,能中和盐酸的 固体;优选碳酸钙、碳酸钠、二氧化硅中至少一种;
[0009] 步骤A浆渣与固化剂混合时,以浆渣中浆渣高沸质量计算,所述浆渣高沸为浆渣 中的液相部分,按质量比计,浆渣高沸:固化剂=1 : 2?1 : 0. 5 ;
[0010] 步骤B加水量以浆渣高沸与水按质量比计,浆渣高沸:水=1 : 1?1 : 0.4。
[0011] 具体的,步骤B中水解条件为温度50°C?120°C、真空度-O.OlMpa?_0.08Mpa。 水解温度过高,浆渣存在燃烧甚至爆炸的风险。
[0012] 更进一步的,上述技术方案可优选两种技术方案如下:
[0013] 技术方案(一):
[0014] A、将浆渣与固化剂混合;
[0015] B、加水,完成水解反应;
[0016] 其中,所述的固化剂的作用是吸附或固定浆渣中的液体部分改善水解效果,中和 浆渣水解过程中产生的盐酸;因此所述固化剂为不与浆渣反应,能中和盐酸的固体;优选 碳酸钙、碳酸钠、二氧化硅中至少一种;
[0017] 步骤A浆渣与固化剂混合时,以浆渣中浆渣高沸质量计算,所述浆渣高沸为浆渣 中的液相部分,按质量比计,浆渣高沸:固化剂=1 : 1?1 : 0. 5 ;
[0018] 步骤B加水量以浆渣高沸与水按质量比计,浆渣高沸:水=1 : 1?1 : 0.4。
[0019] 其中,在步骤B前,将经步骤A混合后的物料加入pH调节剂中;其中,pH调节剂以 浆渣中浆渣高沸质量计算,按质量比计,浆渣高沸:pH调节剂=1 : 0. 7?1 : 0.3。
[0020] 具体的,步骤A所述的将浆渣与固化剂混合是在搅拌的同时加入。浆渣和空气接 触易反应结块,且固化剂含有水分,如加完后再搅拌混合,浆渣中易产生结块,不易粉碎。为 避免产生结块,应将浆渣加入到固化剂、pH调节剂中,否则底部的浆渣可能因混合不均匀导 致结块产生,不利于后续工序且存在安全风险。
[0021] 具体的,步骤B中水解条件为温度50°C?120°C、真空度-0. OlMpa?-0. 08Mpa。 水解温度过高,浆渣存在燃烧甚至爆炸的风险。
[0022] 具体的,步骤B中所述的加水是在搅拌的同时加水,加水在0. 5?2h内完成。浆 渣水解属于放热反应,通过控制加水速度以控制浆渣的水解温度。雾状水与物料接触更好, 水解更完全,故优选采用喷雾方式加水。
[0023] 技术方案(二 )
[0024] A、将浆渣与固化剂混合;
[0025] B、加水,完成水解反应;
[0026] 其中,所述的固化剂的作用是吸附或固定浆渣中的液体部分改善水解效果,中和 浆渣水解过程中产生的盐酸;因此所述固化剂为不与浆渣反应,能中和盐酸的固体;优选 碳酸钙、碳酸钠、二氧化硅中至少一种;
[0027] 步骤A浆渣与固化剂混合时,以浆渣中浆渣高沸质量计算,所述浆渣高沸为浆渣 中的液相部分,按质量比计,浆渣高沸:固化剂=1 : 2?1 : 0. 5 ;
[0028] 其中,在水解后按质量比浆渣高沸:pH调节剂=1 : 0.15?1 : 0. 02加入pH 调节剂;
[0029] 步骤B加水量以浆渣高沸与水按质量比计,浆渣高沸:水=1 : 1?1 : 0.4。
[0030] 步骤B中水解条件为温度50°C?100°C、真空度-0. 01?-0. 08Mpa。
[0031] 具体的,步骤A中所述的将浆渣与固化剂混合是在搅拌固化剂的同时加入浆渣。 浆渣和空气接触易反应结块,并且固化剂含有水分,如加完后再搅拌,会产生结块,不易粉 碎。为避免产生结块,应将浆渣加入固化剂中,否则底部的浆渣可能因混合不均匀导致产生 结块,不利于后续工序且存在安全风险。
[0032] 具体的,步骤B中所述的加水是在搅拌的同时加水,加水在0. 5?2h内完成。浆 洛水解属于放热反应,控制加水速度以控制浆洛的水解温度。雾状水与物料接触更好,水解 更完全,故优选以喷雾方式加水。
[0033] 具体的,步骤B中水解条件为温度50°C?100°C、真空度-0. OlMpa?-0. 08Mpa,水 解温度过高,浆渣存在燃烧甚至爆炸的风险。
[0034] 其中,固化剂与浆渣搅拌混合,使浆渣由液体转变为固体或者糊状,水解后产生的 盐酸与固化剂反应,减少稀盐酸的量,相应的减少废酸排放量;加入pH调节剂升高所得固 体渣的pH值,减小固体渣运输储藏中的安全风险。若步骤A中固化剂添加量过少,混合后 仍会为液体,则会影响水解效果;若添加量过高会增加处理成本。pH调节剂加入量过高,会 增大处理成本;加入量过低则固体渣pH达不到要求,无法达到降低储存运输中的安全风险 的目的。
[0035] 步骤B中加水量过低会导致水解后物料显酸性,需加入大量的pH调节剂调节,导 致处理成本增加;加水量过高会导致产生大量稀盐酸,增大废酸排放量,浪费水资源。
[0036] 具体的,上述技术方案中水解过程中产生的气体经吸收塔吸收后,得盐酸。
[0037] 具体的,技术方案(一)和技术方案(二)中的pH调节剂是氧化钙、氢氧化钠、氢 氧化钙中至少一种,其作用是中和残余盐酸并升高固体渣pH。
[0038] 除上述有机硅浆渣水解处理工艺外,本发明还提供上述两种浆渣水解处理得到的 固体渣。
[0039] 本发明方法水解后得到的固体渣可以应用于分离回收铜、制砖、制水泥等,不仅节 约了成本,同时降低了环境污染。
[0040] 本发明技术方案中加入的固化剂和pH调节剂,能减轻浆渣水解时对设备的腐蚀 和环境污染、解决了因水解后固体渣显酸性导致储存中存在安全环保风险的问题。控制水 解时加水量在按质量比浆渣高沸:水=1 : 1?1 : 0.4范围内以减少稀盐酸产生量。
[0041] 本发明水解处理工艺中产生的少量盐酸气体通过洗涤塔水洗,当洗涤水的盐酸浓 度达到22% -30%时收集回收,洗涤塔中洗涤水可循环使用,不会排放大量的稀盐酸水,每 吨浆渣产生约200 kg浓度为22%?30%盐酸和pH = 7?12的疏松固体渣。
[0042] 有益效果
[0043] 1、本发明方法工艺处理过程简单,易操作;
[0044] 2、本发明方法改善了浆渣在水解时产生大量的盐酸气体导致腐蚀设备的情况,也 降低了废酸的排放量,减轻了对环境的污染;
[0045] 3、控制加水量,使浆渣水解后无稀盐酸水产生;
[0046] 4、水解后固体渣疏松显碱性,降低了固体渣在储存、运输过程中的安全风险。
[0047] 下面结合对本发明作进一步说明。
[0048] 本发明采用的技术方案包括以下步骤:
[0049] A、将浆渣与固化剂混合;
[0050] B、加水,完成水解反应;
[0051] 其中,所述的固化剂的作用是吸附或固定浆渣中的液体部分改善水解效果,同时 可中和浆渣水解过程中产生的盐酸;因此所述固化剂宜采用不与浆渣反应,能中和盐酸的 固体;优选碳酸钙、碳酸钠、二氧化硅中至少一种;
[0052] 步骤A浆渣与固化剂混合时,以浆渣中浆渣高沸质量计算,所述浆渣高沸为浆渣 中的液相部分,按质量比计,浆渣高沸:固化剂=1 : 2?1 : 0.5;
[0053] 步骤B加水量以浆渣高沸与水按质量比计,浆渣高沸:水=1 : 1?1 : 0.4。
[0054] 具体的,步骤Β中水解条件为温度50°C?120°C、真空度-0. OlMpa?-0. 08Mpa。 水解温度过高,浆渣存在燃烧甚至爆炸的风险。
[0055] 更进一步的,上述技术方案可优选两种技术方案如下:
[0056] 技术方案(一):
[0057] A、将浆渣与固化剂混合;
[0058] B、加水,完成水解反应;
[0059] 其中,所述的固化剂的作用是吸附或固定浆渣中的液体部分改善水解效果,中和 浆渣水解过程中产生的盐酸;因此所述固化剂为不与浆渣反应,能中和盐酸的固体;优选 碳酸钙、碳酸钠、二氧化硅中至少一种;
[0060] 步骤A浆渣与固化剂混合时,以浆渣中浆渣高沸质量计算,所述浆渣高沸为浆渣 中的液相部分,按质量比计,浆渣高沸:固化剂=1 : 1?1 : 0. 5 ;
[0061] 步骤B加水量以浆渣高沸与水按质量比计,浆渣高沸:水=1 : 1?1 : 0.4。
[0062] 其中,在步骤B前,将经步骤A混合后的物料加入pH调节剂中;其中,pH调节剂以 浆渣中浆渣高沸质量计算,按质量比计,浆渣高沸:pH调节剂=1 : 0. 7?1 : 0.3。
[0063] 具体的,步骤A所述的将浆渣与固化剂混合是在搅拌的同时加入。浆渣和空气接 触易反应结块,且固化剂含有水分,如加完后再搅拌混合,浆渣中易产生结块,不易粉碎。为 避免产生结块,应将浆渣加入到固化剂、pH调节剂中,否则底部的浆渣可能因混合不均匀导 致结块产生,不利于后续工序且存在安全风险。
[0064] 具体的,步骤B中水解条件为温度50°C?120°C、真空度_0. OlMpa?-0. 08Mpa。 水解温度过高,浆渣存在燃烧甚至爆炸的风险。
[0065] 具体的,步骤B中所述的加水是在搅拌的同时加水,加水在0. 5?2h内完成。浆 渣水解属于放热反应,通过控制加水速度以控制浆渣的水解温度。雾状水与物料接触更好, 水解更完全,故优选采用喷雾方式加水。
[0066] 技术方案(二 )
[0067] A、将浆渣与固化剂混合;
[0068] B、加水,完成水解反应;
[0069] 其中,所述的固化剂的作用是吸附或固定浆渣中的液体部分改善水解效果,中和 浆渣水解过程中产生的盐酸;因此所述固化剂为不与浆渣反应,能中和盐酸的固体;优选 碳酸钙、碳酸钠、二氧化硅中至少一种;
[0070] 步骤A浆渣与固化剂混合时,以浆渣中浆渣高沸质量计算,所述浆渣高沸为浆渣 中的液相部分,按质量比计,浆渣高沸:固化剂=1 : 2?1 : 0. 5 ;
[0071] 其中,在水解后按质量比浆渣高沸:pH调节剂=1 : 0.15?1 : 0.02加入pH 调节剂;
[0072] 步骤B加水量以浆渣高沸与水按质量比计,浆渣高沸:水=1 : 1?1 : 0.4。
[0073] 步骤B中水解条件为温度50°C?100°C、真空度-0. 01?-0. 08Mpa。
[0074] 具体的,步骤A中所述的将浆渣与固化剂混合是在搅拌固化剂的同时加入浆渣。 浆渣和空气接触易反应结块,并且固化剂含有水分,如加完后再搅拌,会产生结块,不易粉 碎。为避免产生结块,应将浆渣加入固化剂中,否则底部的浆渣可能因混合不均匀导致产生 结块,不利于后续工序且存在安全风险。
[0075] 具体的,步骤B中所述的加水是在搅拌的同时加水,加水在0. 5?2h内完成。浆 洛水解属于放热反应,控制加水速度以控制浆洛的水解温度。雾状水与物料接触更好,水解 更完全,故优选以喷雾方式加水。
[0076] 具体的,步骤B中水解条件为温度50°C?100°C、真空度-0. OlMpa?-0. 08Mpa,水 解温度过高,浆渣存在燃烧甚至爆炸的风险。
[0077] 其中,固化剂与浆渣搅拌混合,使浆渣由液体转变为固体或者糊状,水解后产生的 盐酸与固化剂反应,减少稀盐酸的量,相应的减少废酸排放量;加入pH调节剂升高所得固 体渣的pH值,减小固体渣运输储藏中的安全风险。若步骤A中固化剂添加量过少,混合后 仍会为液体,则会影响水解效果;若添加量过高会增加处理成本。pH调节剂加入量过高,会 增大处理成本;加入量过低则固体渣pH达不到要求,无法达到降低储存运输中的安全风险 的目的。
[0078] 步骤B中加水量过低会导致水解后物料显酸性,需加入大量的pH调节剂调节,导 致处理成本增加;加水量过高会导致产生大量稀盐酸,增大废酸排放量,浪费水资源。
[0079] 具体的,上述技术方案中水解过程中产生的气体经吸收塔吸收后,得盐酸。
[0080] 具体的,技术方案(一)和技术方案(二)中的pH调节剂是氧化钙、氢氧化钠、氢 氧化钙中至少一种,其作用是中和残余盐酸并升高固体渣pH。
[0081] 除上述有机硅浆渣水解处理工艺外,本发明还提供上述两种浆渣水解处理得到的 固体渣。
[0082] 本发明方法水解后得到的固体渣可以应用于分离回收铜、制砖、制水泥等,不仅节 约了成本,同时降低了环境污染。
[0083] 本发明技术方案中加入的固化剂和pH调节剂,能减轻浆渣水解时对设备的腐蚀 和环境污染、解决了因水解后固体渣显酸性导致储存中存在安全环保风险的问题。控制水 解时加水量在按质量比浆渣高沸:水=1 : 1?1 : 0.4范围内以减少稀盐酸产生量。
[0084] 本发明水解处理工艺中产生的少量盐酸气体通过洗涤塔水洗,当洗涤水的盐酸浓 度达到22% -30%时收集回收,洗涤塔中洗涤水可循环使用,不会排放大量的稀盐酸水,每 吨浆渣产生约200 kg浓度为22%?30%盐酸和pH = 7?12的疏松固体渣。
[0085] 本发明还通过以下实例进一步加以说明,但并不因此将本发明的保护范围限制在 实施例之中。
[0086] 实施例1
[0087] 将100重量份的有机硅浆渣(其中含铜、硅粉、高沸物等,固液比=3 : 7)加入到 60重量份碳酸钙,搅拌0. 5h,启动真空系统,控制真空度为-0. 02Mpa,后在0. 5h内加入70 重量份水,控制水解温度为90°C,在继续搅拌2h,停止真空系统;再加入5重量份氧化钙,搅 拌lh,得疏松无结块固体渣,此固体渣中铜含量为4.5%,硅粉为45.8%,pH = 12,可作为 分离回收铜、制砖、制水泥等的原材料。
[0088] 实施例2
[0089] 将100重量份的有机硅浆渣(其中含铜、硅粉、高沸物等,固液比=3 : 7)加入50 重量份碳酸钙,搅拌0. 5h,启动真空系统,控制真空度为-0. 07Mpa,后在lh内加入60重量 份水,控制水解温度为60°C。在继续搅拌2h,停止真空系统;再加入10重量份氧化钙,搅拌
有机硅浆渣水解处理工艺和副产物及其应用制作方法
- 专利详情
- 全文pdf
- 权力要求
- 说明书
- 法律状态
查看更多专利详情
下载专利文献
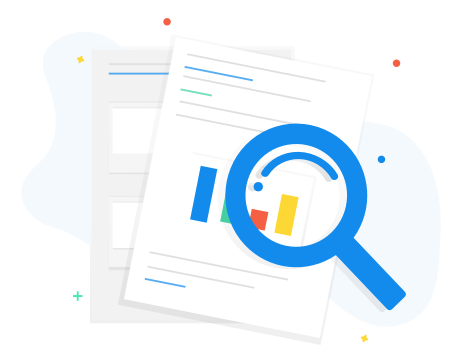
下载专利
同类推荐
-
王建设, 王琳王建设, 王琳刘璐, 杨青峰
您可能感兴趣的专利
-
李世泰徐功达, 杜欢政刘保林应士敏, 李根明
专利相关信息
-
刘国峰刘海洋刘海洋R·迪科西莫