双辊薄带连铸用陶瓷侧封板及其制备方法【技术领域】,具体地指一种双辊薄带连铸用陶瓷侧封板及其制备方法。[0002]薄带连铸是钢铁带材工业生产领域内的一项革命性短工艺流程,它从根本上改变了钢铁工业薄型钢材的生产过程,取消了连铸(铸锭)、粗轧、热连轧及相关的加热、切头等一系列常规工序,开创了将钢水经中间包直接浇注并直接轧制成数毫米厚的薄型板材的高效、节能、环保的最新型技术和工艺。[0003]侧封技术是双辊薄带连铸技术中最关键的一环,是影响薄带连铸过程中铸带质量和工艺稳定性的关键因素,侧封起到约束金属液体,促进薄带成型,保证薄带边缘质量等作用。目前,主要有电磁侧封、气体侧封和固体侧封三种侧封方式,其中气体侧封作为一种新的侧封技术刚刚被人提出,大多处于基础理论研究阶段。电磁侧封技术存在设备复杂,磁场不易控制,技术水平远未达到工业化生产的要求。固体侧封是目前技术最成熟、也是最接近实用条件的一种侧封方法。[0004]目前,国内外研究和开发的固体侧封板绝大部分都不能满足工业生产的要求,如:《Ceramic plates for side dams of twin-drum continuous strip casters》 (Nose 等人,美国专利US7208433)使用的是一种利用稀土石榴石、塞隆以及BN (氮化硼)复合材料制备陶瓷侧封板,专利中报道该种侧封板具有较低的热导率(热导率< 10W/m.K),并且具有较好的抗热震性倉((Pressure-sintered polycpystalline mixed materials with abase of hexagonal boron nitride, oxides and carbides〉〉(Sindlhauser 等人,美国专利US4885264)对氮化硼-氧化物基复合材料和氮化硼-非氧化物复合材料制备陶瓷侧封板进行了研究,实验中在BN-ZrO2基体中分别加入了 SiC、ZrC,在真空条件下于1500~1800°C热压烧结制备成陶瓷复合材料。这两种材料的性能测试结果如下:分别达到理论密度的94%和95%,热导率分别为18ff(m.K)14ff(m.K)(1000°C ),测试结果同时还发现,制成的这两种侧封板材料很致密,且具有很好的耐磨性、抗热震性和抗侵蚀性。《Compositematerial)) (Guillo等人,美国专利US6667263)以六方氮化硼一氧化物(Al、Mg、S1、Ti的氧化物)为基体,加入氮化物(Al、S1、Zr、Ti的氮化物),在真空状态下热压烧结制备了陶瓷侧封板复合材料。实验结果表明,BN-Al2O3-Si3N4性能最好,Al2O3和Si3N4形成了固溶体,使材料具有好的抗热震性、耐磨性、耐蚀性和非润湿性。《Ceramic plate for side weir oftw in-drum type continuous casting apparatus》(Takeuchi 等人,美国专利 US6843304)制备了 BN-AlN-Si3N4-Al (或Al的等价物)陶瓷侧封板复合材料,其热导率小于8W(m.Κ)-1,抗热震性能和抗钢水侵蚀性能良好。《薄带连铸用侧封板及制造方法》(许宏杰和田守信,中国专利CN102161082A)利用氮化硼、硼化锆、石墨以及碳纤维制备了薄带连铸用陶瓷侧封板,该专利中报道其热导率为22W.(m.K)-1,抗氧化性能和耐磨损性能较好。《双辊薄带连铸侧封板及其制作方法》(田守信等人,中国专利CN101648260A)利用一种氮化硼材质的面板和一种铝硅系保温隔热材料的基板制作了一种复合侧封板,该专利中报道该种复合侧封板的保温性能良好。《一种用于薄带连铸侧封板的陶瓷复合材料及其制备方法》(王玉金等人,中国专利CN102173792A)该专利中系统报道了利用氮化硼、碳化物、氮化物以及氧化物作为侧封板的制作方法,该专利所制备的侧封板致密度为94%~99%,室温抗弯强度为260~420MPa,断裂韧性为3~8MPa.m1/2。总体而言,国内外对侧封板材质均进行了大量的研究,国外侧封板少部分已经进行了商品化生产,国内的侧封板研究尚处于实验室研究和模拟实验当中,还未能生产出符合使用要求的陶瓷侧封板,此关键技术仍然制约着薄带连铸的工业化进程。国外所制备的侧封板虽然优于国内侧封板,但是或多或少存在如抗钢水化学侵蚀性不佳,抗热震性差以及耐磨性差等问题。综合性能较优的侧封板,其长时间使用过程中仍然会存在上述问题。这是因为,一般情况下,在保证侧封板具有好的抗热震性的同时,不能保证侧封板具有低的热导率,这就使得侧封板表面很容易产生冷块,从而导致侧封板被磨损,缩短寿命。另一个方面,在烧结大体积高致密度的侧封板时,很难使得侧封板物相组成及微观组织均一,这就使得侧封板内部出现热膨胀不匹配,从而导致侧封板在使用过程中发生热震破坏。侧封板选用材质如果与钢水非润湿性差,则侧封板在使用过程中更容易与钢水发生侵蚀破坏。因此,研究和开发高性能陶瓷侧封板材料对薄带连铸的工业化生产具有重要意义。[0005]因此,研究和开发高性能陶瓷侧封板材料对薄带连铸的工业化生产具有重要意义。
[0006]本发明的目的就是要提供一种双辊薄带连铸用陶瓷侧封板及其制备方法,本发明通过开发新型侧封板新的配方组成,并调整其制备方法使得侧封板同时具有耐高温、强度高、抗热震以及热导率低的性能。[0007]为实现此目的,本发明所设计的双辊薄带连铸用陶瓷侧封板,其特征在于,该陶瓷侧封板的化学成份按质量百分数计为:六方氮化硼粉(h-BN) 40~75%、Si3N4粉10~45%、锆莫来石粉10~30%、TiN粉3~15%和添加剂0.5~10%,其中,所述添加剂为Y2O3、工业Al203、Mg0和轻质碳酸镁中的一种或几种的组合。
[0008]进一步地,所述六方氮化硼粉占所述陶瓷侧封板的重量百分比优选为40~60%。
[0009]进一步地,所述添加剂为Y2O3粉,Y2O3粉占所述陶瓷侧封板的重量百分比为5%。
[0010]或者,所述添加剂为Y2O3粉、工业氧化铝粉和MgO粉,其中,Y2O3粉占所述陶瓷侧封板的重量百分比为2%,工业氧化铝粉占所述陶瓷侧封板的重量百分比为2%,MgO粉占所述陶瓷侧封板的重量百分比为1%。
[0011 ] 或者,所述添加剂为Y2O3粉、工业氧化铝粉和轻质碳酸镁粉,其中,Y2O3粉占所述陶瓷侧封板的重量百分比为1.5%,工业氧化铝粉占所述陶瓷侧封板的重量百分比为2.5%,轻质碳酸镁粉占所述陶瓷侧封板的重量百分比为1%。
[0012]一种双辊薄带连铸用陶瓷侧封板的制备方法,其特征在于,它包括如下步骤:
[0013] 步骤1:将六方氮化硼粉、Si3N4粉、锆莫来石粉、TiN粉和添加剂分别用球磨机采用湿法球磨法进行球磨处理至少24小时,球磨处理过程中的球磨溶剂为无水乙醇或纯度为95%以上的工业酒精,分别形成六方氮化硼浆料、Si3N4浆料、锆莫来石浆料、TiN浆料和添加剂浆料,该球磨处理过程中控制六方氮化硼浆料、Si3N4浆料、锆莫来石浆料、TiN浆料和添加剂浆料中固体颗粒粒度均为0.1~10 μ m,然后再将六方氮化硼浆料、Si3N4浆料、锆莫来石浆料、TiN浆料和添加剂浆料分别烘干形成六方氮化硼粉料、Si3N4粉料、锆莫来石粉料、TiN粉料和添加剂粉料,所述添加剂为Y2O3、工业Al203、Mg0和轻质碳酸镁中的一种或几种的组合;
[0014]步骤2:按质量百分数为:六方氮化硼粉料40~75%、Si3N4粉料10~45%、锆莫来石粉料10~30%、TiN粉料3~15%、添加剂粉料0.5~10%选取步骤I中烘干处理后的粉料,并通过球磨机将上述六方氮化硼粉料、Si3N4粉料、锆莫来石粉料、TiN粉料和添加剂粉料进行湿法球磨混合处理,湿法球磨混合处理中采用的球磨溶剂为无水乙醇,湿法球磨混合处理直至六方氮化硼粉料、Si3N4粉料、锆莫来石粉料、TiN粉料和添加剂粉料混合均匀,无分层出现,即形成混合浆料;
[0015]步骤3:采用喷雾造粒机对上述混合浆料进行造粒处理,得到粉料,上述采用喷雾造粒机对混合浆料进行造粒处理的过程中控制粉料的粒径范围在0.5mm以下的占10~30%,粒径范围在0.5~1.5mm的占40~80%,粒径范围大于1.5mm的占10~30% ;
[0016]步骤4:将上述造粒处理所得到的不同粒径的所有粉料放入混料机中混合均匀,得到混合粉料;
[0017]步骤5:将混合粉料放入石墨模具中,采用热压烧结工艺烧结制备侧封板坯体,热压最终烧结温度为1400~1900°C,热压烧结工艺最终烧结时对应的气氛压力为5~IOOMPa ;
[0018]步骤6:将上述烧结后的侧封板坯体采用切割机以及磨床进行加工处理,即得到双辊薄带连铸用陶瓷侧封板。
[0019]进一步地,所述步骤2的湿法球磨混合处理的球磨时间为12~96小时。
[0020]本发明的有益效果:采用新型陶瓷配方和制备方法,制造的双辊薄带连铸用陶瓷侧封板具有较高的致密度、耐火度以及抗折强度,充分保证在使用过程中不会软化。同时,本发明的侧封板具有低的热导率和良好的抗热震性能,保证侧封板在使用过程中能够较好的抵抗钢水热冲击,延长侧封板使用寿命。本发明相对于传统侧封板,由于采用了新的陶瓷配方组成,在制备工艺中对原料以及各种工艺参数做到了精细化控制,从而使得所制备的侧封板内部物相组织均匀、侧封板热膨胀系数以及热导率小。宏观上表现为侧封板的抗热震性能、抗钢水侵蚀性能以及耐磨性能相对于传统侧封板更加优异。因而,可有效提高侧封板的使用寿命以及使用稳定性,因而可降低薄带连铸生产成本,具有明显的经济效益。
[0021]本发明的陶瓷侧封板的致密度为93~99%,耐火度为1700~1800°C,室温抗折强度为 200 ~300MPa,热导率为 15 ~25W/(m.Κ)(室温),同时,具有 RT (room temperature室温)至1100°C之间,水冷30次不破裂的抗热震性能。上述参数与现有的侧封板相比说明本发明具有耐高温、抗热震性好、热导率低的特点。
[0022]图1是实施例3制备的双辊薄带连铸用陶瓷侧封板样品断面放大2500倍的扫描电子显微照片。
[0023]以下结合附图和具体实施例对本发明作进一步的详细说明:
[0024]一种双辊薄带连铸用陶瓷侧封板,该陶瓷侧封板的化学成份按质量百分数计为:六方氮化硼粉40~75%、Si3N4粉10~45%、锆莫来石粉10~30%、TiN粉3~15%和添加剂0.5~10%,其中,所述添加剂为Y2O3、工业A1203、MgO和轻质碳酸镁中的一种或几种的组合。采用这种配比,可以充分利用六方氮化硼材料本身所具有的优良特性,耐高温性、润滑性、低的热膨胀系数以及极好的化学稳定性。六方氮化硼具有类似于石墨的层片状结构,只有在300kPa的氮气压力下于3000°C以上熔化,在高温下无软化现象,因而,热压六方氮化硼制品具有较高的使用温度和抗烧蚀性能。故采用六方氮化硼粉为主要原料,辅助低膨胀系数的Si3N4等原料制备复合多相陶瓷,可获得耐高温、抗热震以及抗侵蚀的陶瓷侧封板。
[0025]上述技术方案中优选的,所述六方氮化硼粉占所述陶瓷侧封板的重量百分比优选为40~60%ο
[0026]一种双辊薄带连铸用陶瓷侧封板的制备方法,它包括如下步骤:
[0027]步骤1:将六方氮化硼粉、Si3N4粉、锆莫来石粉、TiN粉和添加剂分别用球磨机采用湿法球磨法进行球磨处理至少24小时(充足的球磨时间可以保证颗粒的粒度,而细的颗粒粒度可以增加原料的比表面积,从而提高原料的活性),球磨处理过程中的球磨溶剂为无水乙醇或纯度为95%以上的工业酒精,分别形成六方氮化硼浆料、Si3N4浆料、锆莫来石浆料、TiN浆料和添加剂浆料,该 球磨处理过程中控制六方氮化硼浆料、Si3N4浆料、锆莫来石浆料、TiN浆料和添加剂浆料中固体颗粒粒度均为0.1~10 μ m,然后再将六方氮化硼浆料、Si3N4浆料、锆莫来石浆料、TiN浆料和添加剂浆料分别烘干形成六方氮化硼粉料、Si3N4粉料、锆莫来石粉料、TiN粉料和添加剂粉料,所述添加剂为Y2O3、工业A1203、MgO和轻质碳酸镁中的一种或几种的组合;
[0028]步骤2:按质量百分数为:六方氮化硼粉料40~75%、Si3N4粉料10~45%、锆莫来石粉料10~30%、TiN粉料3~15%、添加剂粉料0.5~10%选取步骤I中烘干处理后的粉料,并通过球磨机将上述六方氮化硼粉料、Si3N4粉料、锆莫来石粉料、TiN粉料和添加剂粉料进行湿法球磨混合处理,湿法球磨混合处理中采用的球磨溶剂为无水乙醇,湿法球磨混合处理直至六方氮化硼粉料、Si3N4粉料、锆莫来石粉料、TiN粉料和添加剂粉料混合均匀,无分层出现,即形成混合浆料;通过采用湿法球磨混合,可以使得各原料可以相互之间充分分散混合,便于在烧结过程中形成均匀的物相;
[0029]步骤3:采用喷雾造粒机对上述混合浆料进行造粒处理,得到粉料,上述采用喷雾造粒机对混合浆料进行造粒处理的过程中控制粉料的粒径范围在0.5mm以下的占10~30%,粒径范围在0.5~1.5mm的占40~80%,粒径范围大于1.5mm的占10~30% ;通过喷雾造粒机可以获得均匀的球形颗粒,而且便于控制颗粒的粒径。采用不同粒径的颗粒形成级配,便于压制成型;
[0030]步骤4:将上述造粒处理所得到的不同粒径的所有粉料放入混料机中混合均匀,得到混合粉料;
[0031]步骤5:将混合粉料放入石墨模具中,采用热压烧结工艺烧结制备侧封板坯体,热压最终烧结温度为1400~1900°C,热压烧结工艺最终烧结时对应的气氛压力为5~IOOMPa;控制烧结温度和压力在上述范围可以获得致密度高的陶瓷。[0032]步骤6:将上述烧结后的侧封板坯体采用切割机以及磨床进行加工处理,即得到双辊薄带连铸用陶瓷侧封板。
[0033]上述技术方案的步骤I在球磨处理过程后,利用粒度分析仪对球磨后得到的六方氮化硼浆料、Si3N4浆料、锆莫来石浆料、TiN浆料和添加剂浆料进行测试,检测上述各个浆料的粒度是否均为0.1~10 μ m。
[0034]上述技术方案中,所述步骤2的湿法球磨混合处理的球磨时间为12~96小时。
[0035]实施例1:步骤I中将六方氮化硼粉、Si3N4粉、锆莫来石粉、TiN粉和Y2O3粉分别用球磨机采用湿法球磨法进行球磨处理30个小时,球磨溶剂为无水乙醇,球磨处理过程中控制六方氮化硼浆料、Si3N4浆料、锆莫来石浆料、TiN浆料和Y2O3浆料的粒度均为2 μ m ;
[0036]步骤2中从步骤I的粉料中按质量百分数为:六方氮化硼粉料55%、Si3N4粉料15%、锆莫来石粉料15%、TiN粉料10%、Y2O3粉料5%选取待湿法球磨混合处理的粉料,所述湿法球磨混合处理的时间为12小时;
[0037]步骤3中采用喷雾造粒机对混合浆料进行造粒处理的过程中控制粉料的粒径范围在0.5mm以下的占15%,粒径范围在0.5~1.5mm的占60%,粒径范围大于1.5mm的占25% ;
[0038]步骤5中热压最终烧结温度为1750°C,热压烧结工艺最终烧结时对应的气氛压力为 20MPa ;
[0039]经测试,本实施例1得到的一种双辊薄带连铸用陶瓷侧封板材料的性能如下:
[0040]实施例1的陶瓷侧封板致密度为95%,耐火度为1700°C,抗折强度为260MPa (室温),热导率为20W/(m.Κ)(室温),同时,具有RT (room temperature室温)至1100°C之间,水冷30次不破裂的抗热震性能。以上测试结果说明本实施例1具有耐高温、强度高、抗热震性好以及热导率低的特点。
[0041]实施例2:步骤I中将六方氮化硼粉、Si3N4粉、锆莫来石粉、TiN粉、Y2O3粉、工业氧化铝粉、MgO粉分别用球磨机采用湿法球磨法进行球磨处理28个小时,球磨溶剂为无水乙醇,球磨处理过程中控制六方氮化硼浆料、Si3N4浆料、锆莫来石浆料、TiN浆料、Y2O3浆料,工业氧化铝浆料,MgO浆料的粒度均为5 μ m ;
[0042]步骤2中从步骤I的粉料中按质量百分数为:六方氮化硼粉料60%、Si3N4粉料10%、锆莫来石粉料20%、TiN粉料5%、Y2O3粉2%、工业氧化铝粉2%、MgO粉1%选取待湿法球磨混合处理的粉料,所述湿法球磨混合处理的时间为36小时;
[0043]步骤3中采用喷雾造粒机对混合浆料进行造粒处理的过程中控制粉料的粒径范围在0.5mm以下的占20%,粒径范围在0.5~1.5mm的占70%,粒径范围大于1.5mm的占10% ;
[0044]步骤5中热压最终烧结温度为1800°C,热压烧结工艺最终烧结时对应的气氛压力为 30MPa ;
[0045]经测试,本实施例2得到的一种双辊薄带连铸用陶瓷侧封板材料的性能如下:
[0046]实施例2的陶瓷侧封板致密度为97%,耐火度为1750°C,抗折强度为275MPa (室温),热导率为18W/ (m.Κ)(室温),同时,具有RT (room temperature室温)至1100°C之间,水冷30次不破裂的抗热震性能。以上测试结果说明本实施例2具有耐高温、强度高、抗热震性好以及热导率低的特点。
[0047] 实施例3:步骤I中将六方氮化硼粉、Si3N4粉、锆莫来石粉、TiN粉、Y2O3粉、工业氧化铝粉、轻质碳酸镁粉分别用球磨机采用湿法球磨法进行球磨处理32个小时,球磨溶剂为纯度为95%以上的工业酒精,球磨处理过程中控制六方氮化硼浆料、Si3N4浆料、锆莫来石浆料、TiN浆料、Y2O3浆料、工业氧化铝浆料、轻质碳酸镁浆料的粒度均为3 μ m ;
[0048]步骤2中从步骤I的粉料中按质量百分数为:六方氮化硼粉料50%、Si3N4粉料15%、锆莫来石粉料20%、TiN粉料10%、Y2O3粉1.5%、工业氧化铝粉2.5%、轻质碳酸镁粉1%选取待湿法球磨混合处理的粉料,所述湿法球磨混合处理的时间为48小时;
[0049]步骤3中采用喷雾造粒机对混合浆料进行造粒处理的过程中控制粉料的粒径范围在0.5mm以下的占25%,粒径范围在0.5~1.5mm的占60%,粒径范围大于1.5mm的占15% ;
[0050]步骤5中热压最终烧结温度为1850°C,热压烧结工艺最终烧结时对应的气氛压力为 30MPa ;
[0051]经测试,本实施例3得到的一种双辊薄带连铸用陶瓷侧封板材料的性能如下:
[0052]实施例3的陶瓷侧封板致密度为96%,耐火度为1760°C,抗折强度为225MPa (室温),热导率为15W/ (m.Κ)(室温),同时,具有RT (room temperature室温)至1100°C之间,水冷30次不破裂的抗热震性能,水冷30次不破裂的抗热震性能。以上测试结果说明本实施例3具有耐高温、强度高、抗热震性好以及热导率低的特点。
[0053]从图1中 ,可以发现,所制备的侧封板内部组织均匀致密,晶粒细小,绝大部分晶粒均在5μπι以下,这种微观组织结构有助于侧封板强度、导热性能以及抗热震性能的提闻。
[0054]本说明书未作详细描述的内容属于本领域专业技术人员公知的现有技术。
双辊薄带连铸用陶瓷侧封板及其制备方法
- 专利详情
- 全文pdf
- 权力要求
- 说明书
- 法律状态
查看更多专利详情
下载专利文献
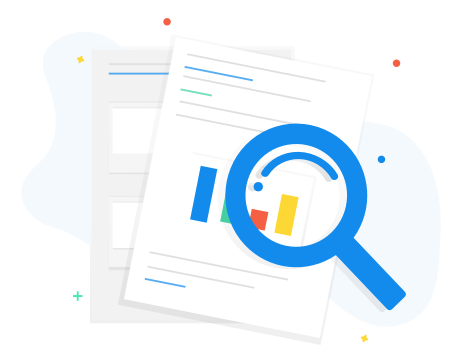
下载专利
同类推荐
-
刘孟名取荣治汤玉斐
您可能感兴趣的专利
-
杨建杨建
专利相关信息
-
孙妙囡孙妙囡王红云王红云