一种建筑垃圾再生高活性矿物掺合料及其制备方法[0002]传统水泥工业是能源、资源消耗巨大以及环境负荷严重的行业,开发新型辅助性胶凝材料,可在一定程度上取代部分水泥,减少水泥产量,从而降低能源、资源消耗和环境负荷,具有十分重要的意义。与此同时,冶金、陶瓷、电镀、电池等行业每年产生大量的工业废渣,这些废渣的随意堆放,占用大量宝贵的土地资源,同时其中的部分重金属还容易对环境产生二次污染,而每年由旧建筑物、工程结构拆除等原因产生数量惊人的建筑垃圾,这些建筑垃圾的弃置堆放,同样存在浪费土地资源、造成环境污染的问题。[0003]对于建筑垃圾的回收利用,目前,主要集中在回收建筑垃圾中的粗细骨料,利用其制备再生骨料并应用于混凝土,对其中的水泥石组分基本上处于不利用的状态,对于一些活性不高的工业废渣也只是作为普通的回填材料,利用价值不高,同时对于一些废弃混凝土再生胶凝材料的开发,也由于其中的f-CaO含量过高而产生安定性不良的问题,从而使再生胶凝材料的应用受到限制。分析表明,建筑垃圾中的水泥石等活性组分或含钙、铝等潜在活性的工业废 渣(锂尾渣、钒渣、铬铁渣),经一定的工艺改性处理后,具有重要的再生资源化利用价值。一方面,建筑垃圾中的水泥石相中含有相当数量的未水化水泥颗粒,遇水将重新具备胶凝能力,同时,水泥水化产物中的C-S-H、CH、钙矾石、单硫型硫铝酸钙等经高温处理后均具备一定的再水化胶凝性能。另一方面,含钙、铝等潜在活性的工业废渣(锂尾渣、钒渣、铬铁渣)进行物理和化学活性激发后,可生产出高活性矿物掺合料,代替粉煤灰、矿粉等矿物掺合料。第三,主流的矿物掺合料粉煤灰、矿粉已逐渐成为稀缺资源,开发利用建筑垃圾制备的高活性矿物掺合料,可以变废为宝,符合国家可持续发展战略,具有广阔的市场应用空间。因此,基于缓解环境压力和节能减排降碳等方面考虑,迫切的需要开发一种建筑垃圾和工业废渣再生矿物掺合料及其制备方法。
[0004]本发明的目的在于提供一种利用建筑垃圾、冶金废渣、漂珠等固体废弃物的再生高活性矿物掺合料及其制备方法,该方法成本低廉、工艺简便、废弃物回收利用率高。[0005]为实现上述目的,采用技术方案如下:[0006]一种再生高活性矿物掺合料,由煅烧渣石粉50~70wt%和高炉矿渣粉30_50wt%混合而成;其中,所述锻烧渣石粉的制备过程如下:[0007]取水泥石粉70~98wt%、冶金废渣O~25wt%和漂珠I~5% wt混合,向其中加入占水泥石粉、冶金废渣和漂珠三者总质量10-15%的水均化后烘干得到渣石粉;将所得渣石粉在800°C~1000°C温度区间锻烧15~20min得到煅烧渣石粉;所述水泥石粉由废弃混凝土破碎后得来。[0008]按上述方案,所述水泥石粉由如下方法制备而来:将废弃混凝土破碎后分离砂衆和碎石,分离出来的砂衆进一步破碎成小于8_粒径的颗粒,接着粉磨至比表面积大于300m2/kg得到水泥石粉。
[0009]按上述方案,所述冶金废渣含硅量在40~60wt%。
[0010]按上述方案,所述的煅烧渣石粉比表面积为350~450m2/kg。
[0011]按上述方案,所述高炉矿渣粉的比表面积为450~500m2/kg,7天活性指数不小于75%,28天活性指数不小于95% (活性指数按国家标准GB/T18046-2000规定)。 [0012]一种再生高活性矿物掺合料的制备方法,包括如下步骤:
[0013]将废弃混凝土破碎得到水泥石粉;
[0014]取水泥石粉70~98wt%、冶金废渣O~25wt%和漂珠I~5% wt混合,向其中加入占水泥石粉、冶金废渣和漂珠三者总质量10-15%的水均化后烘干得到渣石粉;将所得渣石粉在800°C~1000°C温度区间锻烧15~20min得到煅烧渣石粉;
[0015]将煅烧渣石粉50~70wt%和高炉矿渣粉30_50wt%混合得到再生高活性矿物掺合料。
[0016]按上述方案,混合物料的粉磨系统采用Φ1.83X8.0m磨机,磨内钢球的最大直径为50mm,入磨原料的含水率控制在2~3%,原料尺寸控制在I~3_。
[0017]按上述方案,所述冶金废渣含硅量在40~60wt%。
[0018]按上述方案,所述的煅烧渣石粉比表面积为350~450m2/kg。
[0019]按上述方案,所述高炉矿渣粉的比表面积450~500m2/kg,7天活性指数不小于75%,28天活性指数不小于95% (活性指数按国家标准GB/T18046-2000规定)。
[0020]本发明中渣石粉在煅烧之前加水混合再烘干可以使水泥石粉中的Ca(OH)2与高活性硅质原料反应或漂珠产生更多的C-S-H,同时,由于反应消耗了一些水泥石粉中的Ca(OH)2,一定程度上减少了再生矿物掺合料中CaO的含量。
[0021]水泥石粉在煅烧过程中受热分解,C-S-H中相当部分[SiO4]四面体链(Q1、Q2)断裂,形成孤立的[SiO4]四面体(Q°),并且脱水相中f-CaO含量有效降低,并生成了 i3-c2s。
[0022]本发明的有益效果:
[0023]针对再生矿物掺合料需水量大、f-CaO含量高等问题,将含硅40~60wt%的冶金废渣取代部分水泥石粉,并加入适量水充分均化、烘干、煅烧、粉磨再次均化可以有效降低再生胶凝材料中的f-CaO含量,并使脱水相中形成更多具有水化胶凝能力的β -C2S,降低再生矿物掺合料水化需水量,并提高后期水化活性。
[0024]加入少量的漂珠与富集在骨料颗粒周围的氢氧化钙发生火山灰反应,提高后期水化反应程度,生成具有胶凝性质的产物,加强了薄弱的过渡区,对改善混凝土的各项性能有显著作用,显著地提高矿物掺合料的后期水化活性。
[0025]利用了建筑垃圾、冶金废渣、漂珠等固体废弃物,且配料简单,制造成本低,生产容易,活性高,能取代粉煤灰、矿粉等矿物掺合料,在配制高性能混凝土中能有效将低水泥用量,适用于工业化生产和使用。
[0026]以下实施例进一步阐释本发明的技术方案,但不作为对本发明保护范围的限制。[0027]废弃混凝土制备水泥石粉过程:
[0028]废弃混凝土破碎后分离砂浆和碎石,将分离出来的砂浆进一步破碎成小于8_粒径的颗粒,接着粉磨至比表面积大于300m2/kg得到水泥石粉。
[0029]再生高活性矿物掺合料的制备过程:
[0030]取水泥石粉70~98wt%、冶金废渣O~25wt%和漂珠O~5% wt混合,向其中加入占水泥石粉、冶金废渣和漂珠三者总质量10-15%的水均化后烘干得到渣石粉;将所得渣石粉在800°C~1000°C温度区间锻烧15~20min得到煅烧渣石粉。
[0031 ] 采用湿混的方法处理原材料可以使水泥石粉中的Ca (OH) 2与高活性硅质原料冶金废渣和漂珠反应产生更多的C-S-H,同时,由于反应消耗了一些水泥石粉中的Ca(OH)2,一定程度上减少了再生矿物掺合料中CaO的含量。进一步的,水泥石粉在受热分解过程中C-S-H中相当部分[SiO4]四面体链(Q1、Q2)断裂,形成孤立的[SiO4]四面体(Q°),并且脱水相中f-CaO含量有效降低,并生成了 i3_C2S。
[0032]将煅烧渣石粉50~70wt%和高炉矿渣粉30_50wt%混合得到再生高活性矿物掺合料。
[0033]煅烧渣石粉和高炉矿渣在混合前分别粉磨至比表面积350~450m2/kg和450~500m2/kg范围可以得到优质的再生高活性矿物掺合料。高炉矿渣活性指数按国家标准GB/T18046-2000规定7天活性指数不小于75%,28天活性指数不小于95%。能够保证再生高活性矿物掺合料具有较高的活性。 [0034]上述过程制备得到的再生高活性矿物掺合料的活性指数不小于80% (强度比值),需水量比90~100% (评价标准参考GB/T1596-2005),比表面积350~450m2/kg(GB/T1596-2005)。
[0035]经过测试发现,所得再生矿物掺合料的放热峰值均出现在水化反应开始的初期,首先,矿物掺合料与水接触即快速放热,出现第一放热峰,此放热峰一方面由水泥石受热分解产生的CaO水化放热形成,另一方面C3AH6及钙矾石的脱水相遇水会迅速大量放热,形成放热峰。随着水化的进行,出现第二放热峰,主要是由于β -C2S水化产生,这种C2S与水泥熟料中的贝利特有所不同,水泥石煅烧过程中产生的C2S呈现一定程度的无定形态,具备较高的反应活性。加入漂珠后,一方面漂珠对活性掺合料颗粒起物理分散作用,相当于降低了单位水胶比,水化速度减慢,降低水化早期放热;另一方面漂珠与富集在骨料颗粒周围的氢氧化钙发生火山灰反应,提高后期水化反应程度,生成具有胶凝性质的产物,加强了薄弱的过渡区,对改善混凝土的各项性能有显著作用。
[0036]实施例1
[0037]利用建筑拆迁回收的废弃混凝土(强度等级C30~C60),将混凝土破碎后分离碎石与砂浆,再将砂浆用颚式破碎机破碎成小于8_粒径的颗粒;然后用球磨机粉磨至比表面积300m2/kg的水泥石粉备用。
[0038]将水泥石粉、冶金废渣和漂珠通过混料机混合均匀(按质量分数计水泥石粉70%、冶金废渣25%、漂珠5% ),加入占三者总质量分数10%的水混合调匀均化、烘干得到渣石粉;所得渣石粉在850°C煅烧20分钟得到煅烧渣石粉;将煅烧渣石粉粉磨至比表面积400m2/kg 备用。
[0039]按质量百分数计,取上述备用煅烧渣石粉50wt%与比表面积450m2/kg的高炉矿渣粉50wt%通过混料机混合均匀即得再生高活性矿物掺合料。
[0040]混合物料的粉磨系统采用Φ 1.83 X 8.0m磨机,磨内钢球的最大直径为50mm,入磨原料的含水率控制在2~3 %,原料尺寸控制在I~3mm。以上参数的设定是优化后粉磨系统控制参数,此时的磨机粉磨效率最高。对于原料的水分含量也有一个最佳范围,水份含量过高,会导致磨机糊磨,水份含量过低,不但降低烘干机产量,增加煤耗,而且降低管磨机
产、质量。
[0041]本实施例所得再生矿物掺合料产品的活性指数85% (强度比值)(活性指数按国家标准GB/T18046-2000规定);需水量比92% (评价标准GB/T1596-2005);比表面积380m2/kg (评价标准 GB/T1596-2005)。
[0042]本实施例所得再生矿物掺合料产品配制C30高性能混凝土,其配合比与性能见表I:
[0043]表1
[0044]
一种建筑垃圾再生高活性矿物掺合料及其制备方法
- 专利详情
- 全文pdf
- 权力要求
- 说明书
- 法律状态
查看更多专利详情
下载专利文献
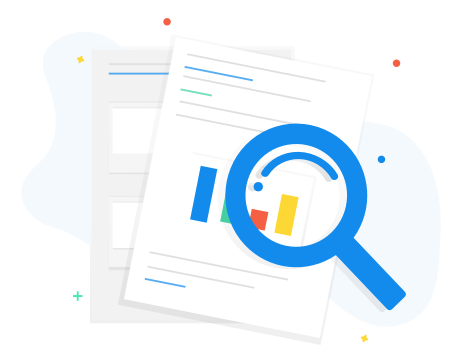
下载专利
同类推荐
-
李安平, 杨宏宜李安平, 杨宏宜李安平, 杨宏宜李安平, 杨宏宜李安平, 杨宏宜
您可能感兴趣的专利
-
李安平, 杨宏宜许发明, 小林敏庆许发明, 小林敏庆杨海涛田福祯
专利相关信息
-
田福祯付伟峰, 窦涛付伟峰, 窦涛付伟峰, 窦涛付伟峰, 窦涛付伟峰, 窦涛付伟峰, 窦涛