专利名称::具有良好退绕性能的弹性纱线的卷绕方法:使用弹性纱线(例如聚氨酯纱线)的缺陷之一是,纱线之间的粘附力会引起不均匀退绕。在最坏的情况下,不均匀退绕导致外层退绕纱线与内层巻绕纱线之间物理性能的差异,甚至因此导致最终产品的不均匀性。换句话说,不均匀退绕使各巻绕部分的绝对值和波动幅度不同。同时,由于对弹性纱线的需求快速增加,为提高生产率做了很多努力,其中之一是将常规的旋转退绕(RTO,rollingtake-off)方法改成能够连续处理的轴向退绕(0ET0,over-endtake-off)方法。可将菱形花纹织物(di即er)使用的斯潘德克斯(Spandex)作为典型实例。在轴向退绕处理中,通过换筒纱尾连接的纱线巻装能够连续使用,从而在产品生产时获得较高的效率。然而,轴向退绕处理的缺陷是在换纱时,最先巻绕在筒管上的层形成带状物,该层的宽度窄于最后的巻绕宽度。结果,为了使用轴向退绕处理而应用换筒纱尾时,最内层所形成的带状物和不均匀的退绕张力导致断线,导致最终产品的物理性能差巳升。
本发明要解决的技术问题因此,本发明的目的是提供一种方法,在该方法中,络纱机的机头与络纱机的筒管接触,使筒管以一定速度旋转,从而使最先巻绕在筒管上的层具有与正常巻绕层相同的巻绕宽度,以及具有与其他层相同的收縮率。而且,相同的巻绕宽度能避免形成带状物,并获得均匀的退绕张力。技术方案为了解决上述问题,根据本发明的优选实施例,弹性纱线的巻绕方法包括第一步,络纱机机头上升,位置交换装置使绕好的弹性巻与空筒交换位置,空筒处于巻绕位置;第二步,络纱机机头下降,使由络纱机支撑的摩擦辊与空筒接触;第三步,使摆动导纱器环绕巻绕位置处旋转的空筒,以将弹性纱线固定,同时,绕好的弹性纱线巻装由引入丝防止板遮蔽,该引入丝防止板位于等待巻绕位置的筒管架所在一侧;第四步,位于络纱机机头上部的第一上导纱器移动,使弹性纱线朝向空筒的前部移动,并且,第二上导纱器移动使弹性纱线向横动装置移动,同时,纱线分离板(其一侧固定在横动装置侧面)开始工作,以将弹性纱线从横动装置分离,从而在空筒上形成换筒纱尾;第五步,绕好的弹性纱线巻装停止旋转,使巻的弹性纱线被摆动导纱器切断,以在空筒上巻绕;以及第六步,第一上导纱器、第二上导纱器及纱线分离板返回各自的初始位置,以及,弹性纱线返回往复导纱器,并以正常宽度巻绕。根据本发明的另一个优选实施例,弹性纱线巻绕方法的特征在于在形成换筒纱尾时,摩擦辊和空筒接触以使空筒旋转,使空筒上最初巻绕层的宽度与最后巻绕层的宽度相同。根据本发明的又一个优选实施例,由筒管的侧缝和斜缝巻绕弹性纱线的初始部分。根据本发明的又一个优选实施例,提供根据上述方法生产的弹性纱线巻装,这种弹性纱线巻装中最初巻绕层的宽度与最后巻绕层的宽度相同。优点本发明的优点在于为采用轴向退绕处理连续使用纱线巻装的生产厂家提供质量稳定的产品,尤其是菱形花纹织物生产商。图1示出使用常规弹性纱线络纱机进行落纱的流程图(旋转退绕处理)。图2示出弹性纱线的常规落纱机(轴向退绕处理)。图3示出使用根据本发明一个实例的弹性纱线络纱机进行落纱的流程图。图4示出根据图3的弹性纱线络纱机的筒管。具体实施例方式本发明涉及一种采用轴向退绕处理退绕的弹性纱线的巻绕装置和方法,更特别地,本发明涉及一种巻绕装置和方法,其中,绕好的纱线巻装移入等待巻绕位置,在转移纱线时,络纱机机头进行升降,以及,络纱机的摩擦辊与筒管接触并使筒管旋转。下面详细描述本发明。常规地,弹性纱线络纱机使具有两个筒管架的转动架板旋转,以交换筒管架的位置,并且,当纱线巻装完成巻绕时,弹性纱线络纱机进行转移纱线的处理以进行后续的纱线巻绕。旋转退绕处理以上述方式进行。然而,在轴向退绕处理中,将纱线的初始部分巻绕在空筒的外端部,并且,纱线的尾部,即包脚纱(b皿chyarn),巻绕在空筒的端部。因此,能够容易地发现纱线的初始部分以连续地更换纱线巻装。韩国专利公开No.95-11301披露了一种通过旋转退绕处理退绕的产品的落纱流程,以及,韩国专利公开No.2003-77800披露了一种通过轴向退绕处理退绕的产品的落纱流程。图1示出韩国专利公开No.95-11301的落纱流程。如图1(a)所示,弹性纱线巻装4绕好时,转动架6旋转以使绕好的纱线巻装4与空筒7交换位置,如图l(b)所披露的。如图l(c)中所示,转动架6旋转使空筒7通过巻绕位置"A"旋转至中间位置"M",并停在位置"M"。下一处理是移动摆动导板9,以使弹性纱线3绕过空筒7,以及,载有绕好的纱线巻装4的筒管架5突然停止,以使弹性纱线3松弛,从而弹性纱线3紧贴空筒7的表面。弹性纱线3贴附在空筒7的表面时,由于空筒7与绕好的纱线巻装4之间的张力,出现断线,接着,后面的弹性纱线巻绕在被前面的弹性纱线3紧贴的空筒7上,藉此完成纱线从绕好的纱线巻装到空筒的转移过程。随后,摆动导板9回位,并如图l(d)和图l(e)所示,通过横动装置(traversedevice)2的往复移动,使空筒7返回巻绕位置"A"以进行巻绕。图2示出韩国专利公开No.2003-77800的弹性纱线络纱机。该现有技术披露的方法中,使用改进的摆动导纱器700,通过轴向退绕处理,对巻绕的弹性纱线巻装进行退绕,而不是旋转退绕处理。如图l(c)所示,在将纱线从绕好的纱线巻装4转移至空筒7时,图2中摆动导纱器700能够使纱线的初始部分巻绕在空筒的外端。然而,在如图1和图2所示的落纱方法中,由摆动导纱器(图1(c))进行纱线转移时,纱线被连续转移以供巻绕。在此情况下,由于摩擦辊没有与筒管接触,最初的巻绕宽度比最终的巻绕宽度窄50%以上。结果,在筒管的中间形成较厚的带状物。对筒管上的最初巻绕层进行轴向退绕处理时,较厚的带状物会引起断线。此外,韩国专利公开No.2005-0103081披露了一种生产纱线巻装的方法,可用于轴向退绕处理,其中,筒管上最初巻绕层的物理性能与其他层的相同。然而,在此情况下,因为在纱线的转移过程之后,络纱机的机头再次上升,以形成换筒纱尾,从而导致纱线浪费。而且,在转移纱线(图l(c))的通常过程中,为了切断绕好的纱线巻装4的末端,空筒7的旋转速度比摩擦辊快10%,利用两个筒管间的张力导致断线。然而,在此情况下,由于巻绕过程在高于通常速度的情况下进行,纱线的收縮率也高于正常部分。结果,在通过轴向退绕处理退绕时,造成产品物理性能的差异。图3是示出根据本发明的一个实例用于轴向退绕处理的弹性纱线巻绕方法的流程图。根据本发明的络纱机包括摩擦辊500、横动装置2、筒管7、两个筒管架5、位置交换装置6、络纱机机头600、摆动导纱器9、第一上导纱器70、第二上导纱器80、纱线分离板90和引入丝防止板60。横动装置2与络纱机机头600相邻,并包括往复导纱器(traverseguide)101,用于执行弹性纱线3的往复运动。此外,筒管7安装在各筒管架5上,筒管7是巻绕弹性纱线的纸筒或塑料筒。如图4所示,筒管7的侧缝200形成于空筒周面外端,弹性纱线的初始部分巻绕侧缝200上。空筒7的侧缝200是用于巻绕纱线初始部分的细槽,防止在纱线初始部分的巻绕过程中弹性纱线弹出。根据本发明,在侧缝200的一侧形成斜缝201。当第一上导纱器70、第二上导纱器80和纱线分离板90操作时,弹性纱线3嵌入斜缝201内,以有助于纱线移至空筒7的转移过程。同时,两个筒管架5分别安装在位置交换装置6的巻绕位置(M)和等待巻绕位置(N),筒管7可放在用于弹性纱线3巻绕处理的各筒管架内。通过例如电机(未示出)的驱动力,使位置交换装置6围绕旋转轴旋转,在转移纱线时,位置交换装置6使巻绕位置(M)处的筒管架与等待巻绕位置(N)处的筒管架交换位置。此外,摩擦辊500与筒管在巻绕位置(M)紧密接触,以驱动筒管,并且在进行纱线转移时,络纱机机头600支撑往复导纱器101和摩擦辊500,以进行上升和下降运动。第一上导纱器70位于络纱机机头600上部,并使弹性纱线向着筒管7的前部移动。第二上导纱器80位于第一上导纱器70的顶部,并将弹性纱线推向横动装置2,使位于筒管7前部的弹性纱线3能够嵌入筒管侧缝200。纱线分离板90的一侧安装在横动装置的一个表面上,操作第一上导纱器70和第二上导纱器80以使弹性纱线嵌入筒管侧缝时,纱线分离板90向前移动,从而使弹性纱线3从往复导纱器101分离。纱线转移时,绕好的弹性纱线巻装4移动至等待巻绕位置(N)之后,摆动导纱器9移动,同时环绕处在巻绕位置(M)的空筒7。在绕好的弹性纱线巻装的纱线末端巻绕在空筒7上时,摆动导纱器9环绕高速旋转的空筒7几秒钟。结果,纱线被摆动导纱器和弹性纱线之间的摩擦切断。引入丝防止板60位于等待巻绕位置的筒管架所在一侧,防止在摆动导纱器9切断纱线时由于摩擦形成的绒毛被带入绕好的纱线巻装7或带入新巻绕筒管7。根据本发明的弹性纱线巻绕方法的特征在于随着络纱机机头600的上升,位置交换装置使绕好的弹性巻与空筒交换位置,使空筒位于巻绕位置;络纱机机头下降,使得由络纱机支撑的摩擦辊与空筒接触;摆动导纱器环绕于空筒(在巻绕位置旋转)外侧,以固定弹性纱线,同时,引入丝防止板(位于等待巻绕位置的筒管架所在一侧)遮蔽绕好的弹性纱线巻装;位于络纱机机头上部的第一上导纱器移动,使弹性纱线朝向空筒前部移动,然后,位于第一上导纱器上部的第二上导纱器移动,使弹性纱线朝向横动装置移动,同时,纱线分离板(其一侧固定在横动装置的侧面)运行,将弹性纱线从往复导纱器中分离,以在空筒上形成换筒纱尾;绕好的弹性纱线巻装停止旋转,将巻装的弹性纱线切断以巻绕在空筒上;并且,第一上导纱器、第二上导纱器和纱线分离板回位到各自的初始位置,以及,弹性纱线返回往复导纱器,以标准巻绕宽度进行巻绕。下面,将参照图3具体描述根据本发明的弹性纱线巻绕方法。图3(a)示出第一步,其中,纱线巻绕完成。当巻绕完成时,络纱机机头600上升,并且在绕好的弹性纱线巻装4与空筒7交换位置后,络纱机机头600下降。当络纱机机头600下降时,摩擦辊500与空筒7紧密接触,并且,由络纱机机头支撑的往复导纱器101也下降。图3(b)示出第二步,其中,在绕好的弹性纱线巻装4与空筒7交换位置后,摆动导纱器9保持弹性纱线3,使绕好的弹性纱线巻装4的纱线末端能够巻绕在空筒7上,同时,操作引入丝防止板60。—般地,绕好的弹性纱线巻装4的纱线末端由摆动导纱器9巻绕在空筒7上时,摆动导纱器9环绕高速旋转的空筒7几秒种。这样能够通过摆动导纱器9和弹性纱线之间的摩擦将纱线从绕好的纱线巻装切断。然而,摩擦可能会形成绒毛,并且在某些情况下,纱线绒毛可能被带入绕好的纱线巻装4或新的巻绕筒管。由于这个原因,本发明额外提供用于引入丝防止板60以解决上述问题。图3(c)是落纱的第三步,其中,第一上导纱器70使弹性纱线3朝向筒管前部移动,以使弹性纱线3能够嵌入筒管侧缝200。第一上导纱器在绕好的弹性纱线巻装4和空筒7—起旋转后的一秒钟内运行。在此情况下,横动装置2的往复过程继续进行。如图4所披露的,用于轴向退绕处理的弹性纱线筒管在其一侧具有侧缝200,以形成换筒纱尾,附加地,筒管还具有斜缝201。当第一上导纱器70、第二上导纱器80和纱线分离板90运行时,使弹性纱线3嵌入斜缝201,以有助于纱线朝向空筒7转移的过程。通过此过程,空筒7和绕好的纱线巻装4不需要以高速旋转来转移纱线,并且当执行纱线转移过程时,能够避免在筒管上的最初巻绕层具有过高的收縮率。另外,通过使用上述侧缝200和斜缝201准备弹性纱线时,多种纱线末端同时转移,藉此获得具有相同数量换筒纱尾的弹性纱线。图3(d)示出落纱的第四步,其中,第二上导纱器80将由第一上导纱器70移到筒管侧部的弹性纱线3推向横动装置2,以使弹性纱线能够嵌入侧缝200。同时,纱线分离板90向前移动,以将弹性纱线从往复导纱器101分离。纱线分离板90在第一上导纱器70开始运行后的一秒钟内操作。图3(e)是落纱的第五步,其中,绕好的弹性纱线巻装4停止旋转。这样是为了保持纱线张力,以使绕好的弹性纱线巻装4的纱线末端能够巻绕在空筒7上。随着绕好的弹性纱线巻装4停止旋转,弹性纱线3巻绕在空筒7上。此过程在第一上导纱器70开始工作后1.8秒执行,即,在第二上导纱器80开始运行后0.8秒执行。图3(f)是落纱的第六步,其中,随着绕好的弹性纱线巻装4停止旋转,弹性纱线3从绕好的弹性纱线巻装4切断,以巻绕在空筒7上。引入丝防止板60能够避免带入纱线绒毛。图3(g)和图3(h)分别为落纱的第七步和第八步,其中,执行返回初始位置的操作。用于将弹性纱线3嵌入筒管侧缝200的纱线分离板90和第一上导纱器70回位。一旦图3(f)中的绕好的纱线巻装4停止旋转,纱线分离板90回位,并且,一旦纱线分离板90回位,第一上导纱器70开始其回位过程。图3(i)是落纱的第九步,其中,第二上导纱器80回位。由于第二上导纱器80而被推向横动装置2的弹性纱线3返回到往复导纱器101,以正常宽度在空筒上往复运动。此过程在第一上导纱器回位后的0.8秒钟内执行。在此情况下,与常规络纱机不同,本发明的络纱机在纱线转移到空筒后的1秒至2秒内以正常宽度往复运动,从而,能够从最初巻绕层开始以正常宽度进行巻绕过程。特别地,在本发明图3(a)的步骤中,在络纱机机头600上升使绕好的弹性纱线巻装4与空筒7交换位置后,络纱机机头600下降至初始位置。在此情况下,由络纱机机头支撑的往复导纱器101和摩擦辊500同时下降,藉此,能够在与摩擦辊接触的空筒上以正常巻绕宽度来巻绕纱线。因此,在通过轴向退绕处理生产产品例如菱形花纹织物的情况下,能够获得具有均匀退绕性能的最内层,而没有断线。而且,本发明能避免筒管的最内层形成带状物。图3(j)是落纱的最后一步,其中,摆动导纱器9和引入丝防止板60回位。随着这两个部件的回位,绕好的纱线巻装的落纱处理完成。这样生产的弹性纱线巻装具有如下特征筒管上的最初巻绕层的宽度与初始层的巻绕宽度相同,从而使最初巻绕层的纱线收縮率不高于其他层。另外,根据本发明,通过轴向退绕处理生产的纱线巻装的连续使用不会导致换筒纱尾的断线,使筒管上的最初巻绕层和后巻绕层之间不存在物理性能差别,从而保持均匀的退绕张力。下面参照实例进一步详细说明本发明。实例是用于例示说明的目的,并不用于限制本发明的范围。以如下方式测量上述弹性纱线的基本物理性能、收縮率和退绕张力。强度和伸长率7使用MEL仪器,织物样品长10cm,拉伸强度为100cm/min,测量样品断开时的强度和伸长率。还测量在200%伸长率下施加给纱线的载荷(200%模量)。收縮率(%)在弹性纱线巻装上画一条线,之后使用皮尺测量巻绕的弹性纱线巻装的周向长度(LO)。然后,将弹性纱线巻装退绕,以测量标记长度(Ll)。由下式计算收縮率(%):收縮率(%)=(L0-L1)/L0*100[OO58]退绕张力在支柱上悬挂弹性纱线,并且将弹性纱线筒管和退绕张力装置的第一导纱器之间的距离调整为大约45cm。以100m/min的速度测量高速退绕时的退绕张力,以10m/min的速度测量低速退绕时的退绕张力。换筒纱尾的成功率估计使用轴向退绕设备,弹性纱线巻装最内层的端部与巻前端部相连,以评估连续退绕时结头处换筒纱尾的成功率。对每种条件重复此过程10次。〈实例1>使聚四亚甲基醚二醇和亚甲基二苯基异氰酸酯聚合以制备预聚合物,乙二胺和丙二胺作为增链剂同其他添加剂一起加入,以制备密度为37%的聚合物。该聚合物是用于制备常规弹性纱线的很多聚合物中的一种。通过常规的干式纺丝方法,将聚合物制备成840旦的聚氨酯弹性纱线,以供巻绕。巻绕装置如图3所示,该巻绕装置能够获得均匀的退绕张力。表1示出以上述方式制成并巻绕的聚氨酯弹性纱线的物理性能测量结果。〈比较例1>比较例1与实例1的不同之处在于,弹性纱线通过轴向退绕处理的络纱机(图2)以传统方法来巻绕。[表1]从外层取弹性纱线样品。<table>tableseeoriginaldocumentpage8</column></row><table>[表2]从最初巻绕层取弹性纱线样品。<table>tableseeoriginaldocumentpage8</column></row><table>如表1所示,通过使用改进的络纱机巻绕,能够获得优良性能的退绕,并且,筒管上弹性纱线的最初巻绕层与外层具有相同的收縮率和物理性能。换筒纱尾的成功率与生产率紧密相关,换筒纱尾的成功率证明了通过轴向退绕处理纱线巻装的优势。权利要求一种弹性纱线卷绕方法,包括第一步,随着络纱机机头上升,位置交换装置使绕好的弹性纱线卷装与空筒交换位置,使所述空筒位于卷绕位置;第二步,随着所述络纱机机头下降,由所述络纱机支撑的摩擦辊与所述空筒相互接触;第三步,使摆动导纱器环绕所述卷绕位置处旋转的所述空筒,以固定所述弹性纱线,同时,所述绕好的弹性纱线卷装由引入丝防止板遮蔽,所述引入丝防止板安装在等待卷绕位置的筒管架所在一侧。第四步,位于所述络纱机机头的上部的第一上导纱器移动,使所述弹性纱线朝向所述空筒的前部移动,然后,位于所述第一上导纱器上部的第二上导纱器移动,使所述弹性纱线朝向横动装置移动,同时,纱线分离板开始运行,以将所述弹性纱线从所述往复导纱器分离,从而在所述空筒上形成换筒纱尾;第五步,所述绕好的弹性纱线卷装停止旋转,所述卷的弹性纱线被所述摆动导纱器切断,以在所述空筒上卷绕;以及第六步,所述第一上导纱器、所述第二上导纱器和所述纱线分离板返回各自的初始位置,以及,所述弹性纱线返回所述往复导纱器,并以正常卷绕宽度进行卷绕。2.根据权利要求1所述的弹性纱线巻绕方法,其中,在形成所述换筒纱尾的所述第四步中,所述摩擦辊和所述空筒接触并使所述空筒旋转,使所述筒管上的最初巻绕层的宽度与正常巻绕层的宽度相同。3.根据权利要求1所述的弹性纱线巻绕方法,其中,所述弹性纱线的初始部分巻绕在所述筒管的侧缝和斜缝中。4.根据权利要求1至权利要求3中任一权利要求所述的弹性纱线巻绕方法所生产的巻绕弹性纱线巻装,其特征在于最初巻绕层的宽度与最后巻绕层的宽度相同。全文摘要本发明涉及一种通过轴向退绕处理退绕的弹性纱线的卷绕方法。更特别地,本发明涉及一种弹性纱线的卷绕方法,其特征在于当绕好的纱线卷装移入等待卷绕位置时,络纱机机头进行升降,并且,当形成换筒纱尾时,络纱机机头的摩擦辊与空筒接触并使空筒旋转。通过此过程,筒管上的最初卷绕层的卷绕宽度可以与后来卷绕的其他层的卷绕宽度相同。因此,在通过轴向退绕处理连续使用纱线卷装的情况下,可防止换筒纱尾的断线,以及,筒管上最初卷绕层的物理性能不变,并具有均匀的退绕张力。文档编号D01H13/00GK101748527SQ20081017932公开日2010年6月23日申请日期2008年11月28日优先权日2008年11月28日发明者姜渊秀,晋中成,玄尚宗,郑智烨申请人:株式会社晓星
具有良好退绕性能的弹性纱线的卷绕方法
- 专利详情
- 全文pdf
- 权力要求
- 说明书
- 法律状态
查看更多专利详情
下载专利文献
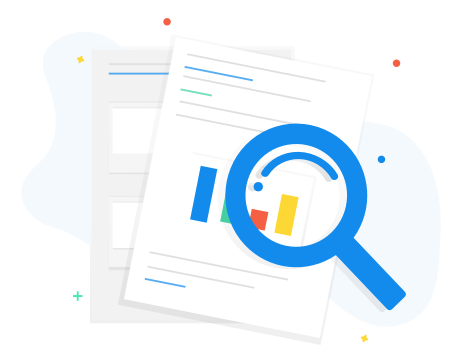
下载专利
同类推荐
-
G·凯勒K·马克马斯特K·马克马斯特K·马克马斯特埃克哈德·松塔格, 延斯·吉里格斯立 谢, 陈虎伟
您可能感兴趣的专利
-
立 谢, 陈虎伟立 谢, 陈虎伟立 谢, 陈虎伟A·R·迪安吉利斯, E·沃利内斯L·特瑟尔L·特瑟尔L·特瑟尔
专利相关信息
-
D·思韦茨, M·克莱因多普拉尔法·B·小塔尔皮拉尔法·B·小塔尔皮拉尔法·B·小塔尔皮拉尔法·B·小塔尔皮