一种高致密度复杂形状陶瓷制品的热压烧结方法【技术领域】[0001]本发明属于陶瓷材料制备成型方法【技术领域】,特别涉及一种高致密度复杂形状陶瓷制品的热压烧结方法。[0002]热压烧结工艺是陶瓷或粉末冶金行业常用的烧结工艺之一,其基本流程是,首先将需要烧结的陶瓷粉料倒入钢制模具中,以一定的压力使之形成一个约35%~40%理论密度的陶瓷坯体,然后将该坯体装入事先准备好的高强度石墨模具中,并将其放入热压烧结炉内,通过高强石墨压头,一边加热一边加压,在高温、高压下实现陶瓷粉体的高致密度烧结,实际生产中也常将陶瓷粉体直接装入石墨模具进行烧结,图1是SiC陶瓷热压烧结示意图。与普通烧结相比,热压烧结的优点:①存在明显的晶界滑移传质和挤压蠕变传质,烧结速率加快,烧成时间减少;②可降低烧结温度,减小晶粒长大;③最终产品的密度和力学性能高。表1是不同方法烧结的SiC陶瓷性能对比,由此可知热压烧结是制备高致密度碳化硅陶瓷的最有效途径。[0003]但众所周知,热压烧结工艺也有明显的缺点,受工艺方法的影响通常只能烧结形状简单制品,如板状类、四方形块状类、圆柱状类型的陶瓷产品,因而其应用范围也受到严重制约。随着科学技术的快速发展,各行业对高致密度、复杂形状陶瓷制品的需求越来越多,采用冷等静压成型+机械加工或凝胶注模等成型技术和无压烧结工艺虽然可以得到复杂形状的陶瓷部件,但在很多情况下无法满足对陶瓷部件高致密度的要求,而且复杂形状陶瓷部件的无压烧结需要缓慢和精细的控温技术,长时间的高温烧结会促使晶粒长大,降低陶瓷零件的力学性能。如果采用热等静压后处理技术提高无压烧结坯体的密度则会大大增加制造成本。[0004]本发明的目的在于提供一种高致密、复杂形状陶瓷制品的热压生产方法,通过本发明的热压烧结陶瓷工艺技术,可以克服上述传统热压只能制造简单板状类的陶瓷产品的现状,可生产出具有复杂结构、高致密度的陶瓷产品。
[0005]本发明利用BN陶瓷等模具材料在高温下不和目标陶瓷发生化学反应的特性,通过调整模具材料的配方使模具材料和目标陶瓷材料在高温高压下实现同步收缩,确保目标陶瓷的复杂形状得以保留,这是本发明的技术要点。该发明摒弃了传统的钢制模具成型陶瓷坯体的工艺,通过本发明,可制备高致密度、复杂形状的陶瓷制品。[0006]针对现有技术不足,本发明提供了一种高致密度复杂形状陶瓷制品的热压烧结方法。
[0007]—种高致密度复杂形状陶瓷制品的热压烧结方法,首先将模具材料通过凝胶成型工艺制备成所需的具有特定形状的模具,然后将需要烧结的目标陶瓷粉体采用凝胶成型技术制备成含有固相成分的浆料,注入上述模具内形成复合热压坯体;所得复合热压坯体通过热压烧结后去除残留的模具材料,最终获得具有特定的结构、密度、性能的目标陶瓷制品O
[0008]所述模具材料在烧结条件下不与目标陶瓷材料发生反应、且能够通过机械或化学方法加工去除。
[0009]所述模具材料为BN、BN与SiC的复合材料、BN与Al2O3的复合材料、BN与Si3N4的复合材料、BN与其他陶瓷的复合材料、石墨或石墨与陶瓷的复合材料。
[0010]所述将模具材料通过凝胶成型工艺制备成所需的具有特定形状的模具的具体方法为:将选定的模具材料粉体通过凝胶成型工艺制备成浆料;根据要烧结的陶瓷零件的形状和尺寸,考虑加工余量和热压方向的收缩率,采用机械加工或3D打印技术制备型芯与零件形状匹配的塑料或金属模具;所述塑料或金属模具内腔尺寸应和热压模具内套尺寸相配合;将已配制的模具材料浆料注入已加工的塑料或金属模具内,加热到60°C~80°C,恒温一定时间直到其凝胶固化成型,取出模芯获得所需的具有特定形状,由模具材料制备的模
亘.N 9
[0011]或采用冷等静压方法先制备模具材料坯体,再通过数控机床将其加工成所需形状的模具。
[0012]所述目 标陶瓷粉体为SiC、Si3N4、AIN、A10N、氧化铝或氧化锆等的陶瓷粉体材料或复合粉体材料。
[0013]所述复合热压坯体整体热压烧结后,通过喷砂工艺去除残留的模具材料,最终获得具有特定结构、密度、性能的目标陶瓷制品。
[0014]本发明的技术特征在于:
[0015]a.选择与需要烧结的目标陶瓷材料在高温下不发生化学反应的模具材料,该模具材料烧结后应易于通过机械或化学方法去除,可选用BN、BN与SiC的复合材料、BN与Al2O3的复合材料、BN与Si3N4的复合材料、石墨或石墨与陶瓷的复合材料等作为模具材料。
[0016]b.将选定的模具材料粉体通过凝胶成型工艺制备成浆料。
[0017]c.根据要烧结的陶瓷零件的形状和尺寸,考虑一定的加工余量和热压方向的收缩率,采用机械加工或3D打印技术制备型芯与零件形状相似的塑料或金属模具。该塑料或金属模具内腔尺寸应和热压石墨模具内套尺寸相配合。
[0018]d.将步骤b中已配制的模具材料浆料注入步骤c中已加工的塑料或金属模具内,加热到60°C~80°C,恒温一定时间使之凝胶固化成型,取出模芯获得所需的具有复杂形状,由模具材料制备的模具。
[0019]e.将需要烧结的目标陶瓷粉体(SiC、Si3N4、氧化铝或氧化锆粉体材料等)采用先进的凝胶成型技术制备成高固相含量的浆料,注入上述模具内,凝胶固化后形成复合热压坯体。
[0020]f.将步骤e中获得的复合热压坯体装入热压石墨模具内,整体热压烧结后,通过喷砂工艺去除前述的模具材料,最终获得具有复杂结构、高密度、高性能的目标陶瓷制品。
[0021]在上述技术特征中,模具材料也可通过冷等静压成型和机械加工制备步骤d中所述的模具。
[0022]本发明的技术特征,也可先配制目标陶瓷粉体的凝胶注浆料,按照与步骤c相同的技术加工塑料或金属模具,该塑料或金属模具内腔与零件形状相似。将已配制的目标陶瓷粉体凝胶注浆料注入塑料或金属模具,并凝胶成型;然后以此为型芯将模具材料用凝胶注工艺浇注到外围,形成步骤e中所述的复合热压坯体。
[0023]本发明的有益效果为:
[0024]本发明方法充分利用了凝胶注工艺和热压工艺的技术特点,提供了一种既能制备复杂形状,又能稳定获得高致密度陶瓷制品的热压生产技术,是传统热压工艺的创新。
[0025]图1为SiC陶瓷热压烧结示意图;
[0026]其中图1中的1-1为耐热钢制成的带水冷结构的上压头,起到向热压的SiC陶瓷传递压力的作用;1-2为石墨上压头,起到直接压制SiC陶瓷的作用;1-3为收到热压的SiC陶瓷;1-4为石墨下压头,作用与1-2相同;1_5为石墨外套,起到约束热压SiC陶瓷的作用;1-6是石墨发热体,起到加热SiC陶瓷的作用;1-7为耐热钢制成的带水冷结构的下压头,作用与1-1相同。
[0027]图2为本发明实施例1凝胶铸SiC和BN制备工艺流程图;
[0028]图3为浇注模具材料和目标陶瓷的铝合金外套结构示意图,其中图3a为铝合金外框的主视图,图3b为铝合金外框的俯视图;
[0029]图4为SiC陶瓷上模芯结构示意图(用于凝胶铸模目标陶瓷成型时使用),其中图4a为SiC陶瓷上模芯的主视图,图4b为SiC陶瓷上模芯的剖面图(A-A面,旋转了 180度);
[0030]图5为SiC陶瓷下模芯结构示意图(用于凝胶铸模目标陶瓷成型时使用),其中图5a为SiC陶瓷下模芯的俯视图,图5b为SiC陶瓷下模芯的主视图;
[0031]图6为成型模具材料BN用上压头或下压头结构示意图,其中图6a为BN用上压头或下压头的俯视图,图6b为BN用上压头或下压头的主视图;
[0032]图7为凝胶干燥后的SiC和BN复合凝胶体结构示意图,其中图7a为SiC和BN复合凝胶体的俯视图,图7b为SiC和BN复合凝胶体主视剖面图(B-B面),图中的7-1为模具材料BN,7-2为目标材料SiC,7-3为为模具材料BN ;
[0033]图8为本发明实例中完成的复杂截面的SiC产品结构示意图;其中图8a为SiC产品的俯视图,图8b为SiC产品的主视剖面图(C-C面)。
[0034]本发明提供了一种高致密度复杂形状陶瓷制品的热压烧结方法,下面结合附图和对本发明做进一步说明。
[0035]实施例1
[0036]凝胶铸SiC和BN的制备工艺流程如图2所示:
[0037]制备凝胶铸SiC陶瓷和BN陶瓷的工艺步骤如下:
[0038](1)配置单体溶液:
[0039]将丙烯酰胺(AM)单体和交联剂亚甲基双丙烯酰胺(MBAM)按一定比例配制溶于去离子水中配制好单体溶液;其中单体溶液中含AM为11.4wt%、含MBAM为lwt%、含纯净水87.6wt%。将配好的单体溶液溶解充分,用滤纸过滤后密闭在玻璃容器中待用。
[0040](2)配置分散剂溶液:[0041]按10g柠檬酸氨(DAC) +90g水的比例将柠檬酸氨(DAC)和水混合溶解充分后,将配好的分散剂液溶解充分,用滤纸过滤后密闭在玻璃容器中待用。
[0042](3)混料:
[0043]a.用天平称取5kg氧化锆磨球,氧化锆球的直径为Φ 6mm,放入容积为5L的立式搅拌磨中;
[0044]b.用天平和移液管量取两份720g单体溶液;
[0045]c.用天平和滴管量取两份40ml分散剂;
[0046]d.加入极少量除泡剂;(加入占单体溶液重量的0.05%除泡剂,本例中加入的是二
甲基硅油水乳液,其含油量为30%)
[0047]e.分别称量2.304kg SiC粉体和1.584kg BN粉体,分别加入到先前配制好的不同720g的单体液中。此时SiC和BN单体溶液的体积浓度都是50vol%。(2304/3.2=720cm3)(1.584/2.2=720cm3)。其中SiC陶瓷的理论密度是P SiC=3.2 (g/cm3),BN陶瓷的理论密度是 P bn=2.2 (g/cm3);
[0048]f.对SiC和BN单体浆料分别进行搅拌球磨4h,使浆料分散均匀。
[0049](4)料浆处理:
[0050]把搅拌均匀的单体浆料(SiC单体浆料或BN单体浆料)分别用150目筛网过滤掉磨介及杂质,用塑料瓶或玻璃瓶密封后保存在0°c的冰箱里面待用。
[0051](5)铸模模具准备:
[0052]采用铸铝做为浆料的模铸工具,包括外套(见图3)、上下模芯(见图4,5,6),其中模芯分为两套,一套是完成复杂截面模芯,通过机械加工或3D打印技术完成,另一套是平板模芯,采用机械加工完成,来保证成型胶体的受压面平整。
[0053](6)浇铸SiC浆液的处理:
[0054]除浆料中的空气,压入的上模芯直到浆料中无气体排出,与浆料完全接触;将SiC单体浆液从冰箱里取出400g,加入过硫酸铵3g~4g,用磁力搅拌器搅拌均匀后(根据浆料的多少,尽量控制时间和温度,避免浆料在注入模具之前,发生凝胶反应)倒入预先准备好的铸铝模具中,其中上下模芯采用带有复杂截面的模芯(见图4,5),先将带复杂截面的下模芯(图5)放入铸铝模套(图3)中,然后倒入带引发剂——过硫酸铵的SiC单体浆料,将带复杂截面的上模芯(图4)用手动的方式,轻轻压入铸铝模套(图3)中,上模芯带有排气结构通道,便于排除模具中的气体。
[0055](7) SiC浆料的凝胶处理:
[0056]将铝模中的SiC浆料铸铝模具一同放入80°C的烘干箱中,在80°C温度下,放置30min后,取出铸铝模具,拿出上模芯(图4),检查SiC浆料的凝胶状态,用手指轻触SiC胶体,如果已经具有弹性且不发生变形即可。
[0057](8) BN单体浆料的处理和铸模:
[0058]重复第(6)操作步骤,把SiC浆料换成BN浆料,把上下模芯更换成平板模芯(图6),将BN浆料100g,注入铸铝模具中,使BN浆料充满已凝胶的SiC胶体上,将平板上下模芯(图6)依次压入铸铝模套(图3)中,直到平板模芯(图6)接触到BN浆料为止。再放入烘干箱(烘干箱的温度设置在60~80°C )中做BN浆料的凝胶化处理30min。
[0059](9)烘干处理:[0060]将已经凝胶好的SiC和BN复合凝胶体,从铸铝模具中脱出,放在室内无阳光直射的地方阴干,室温温度控制在10~25°C范围内,过高的温度可能引起坯体开裂,阴干好的复合坯体,即可装入下一步的热压工序。
[0061]热压烧结工艺步骤:
[0062](I)把干燥后的SiC和BN复合凝胶体(见图7),采用常规的SiC热压工艺,装入石墨模具中,即可完成SiC和BN复合凝胶体的烧结。
[0063](2) SiC和BN复合凝胶体的热压烧结与单一的SiC热压烧结所不同的是,SiC是所需要的产品材料,BN是保证SiC最终产品的形状需要,两种材料在热压烧结过程中,保持着同步烧结收缩状态。
[0064]后期SiC和BN复合烧结体的处理:
[0065](I)将热压烧结好的SiC和BN复合体,通过平面磨床磨出两个大面,也就是说,将烧结过程中附着在烧结体上面的碳纸磨掉,露出两端的BN材质。
[0066](2)将完成步骤(1)的SiC和BN复合烧结体,用压力0.2Mpa~IMpa的喷砂机喷枪,以80-150目的SiC钢砂为主,用水做载体,对其进行去除BN的处理,由于BN和SiC在高温热压烧结中,不发生化学反应,因此很容易就可也从复合体中清除。SiC复杂截面的热压烧结体如图8所示。
[0067](3)将完成步骤(2)的只剩下呈现复杂结构的SiC热压烧结材料,可根据需要进行必要的机械加工,一个符合要求的具有复杂结构的致密的SiC热压烧结的陶瓷产品,就生产出来了。
[0068]表1不同烧结方法的碳化硅陶瓷材料物理性质数据表
[0069]
一种高致密度复杂形状陶瓷制品的热压烧结方法
- 专利详情
- 全文pdf
- 权力要求
- 说明书
- 法律状态
查看更多专利详情
下载专利文献
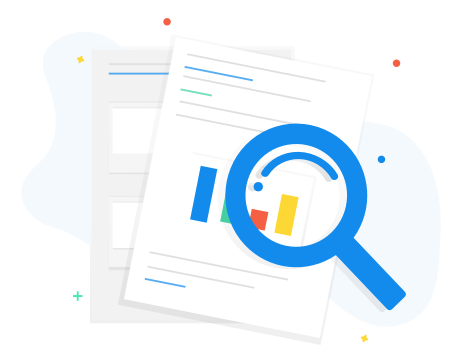
下载专利
同类推荐
-
R·A·博伊哥, G·P·佩桑斯基
您可能感兴趣的专利
-
刘庆华
专利相关信息
-
刘庆华C·S·霍格, C S 霍格C·S·霍格, C S 霍格俞金建