专利名称:表面处理的方法及其设备的制作方法本发明涉及一种通过用一个流化床炉子处理一种材料使之表面上生成一层钛、钒、铌、钽、铬、锰、钨、钼等的碳化物、氮化物或碳氮化物或这样的一种元素与一种基体元素的固溶液的方法及使用于该方法的设备。通过用一个硫化床处理一种材料,使之表面上生成一层碳化物或氮化物的方法是公知的,例如,在先于本申请案申请的日本专利申请号昭57-213749(专利申请公开号昭59-107990)和申请号昭59-108054(专利申请公开号昭60-251274)的日本专利中所公开的方法。所说的方法包括1.把一种由一种高熔点材料(如氧化铝)(以后指一种流态化剂)、一种金属或它的含一种生成碳化物或氮化物的元素的合金(以后是指表面层形成剂)的粉末和一种在或在低于处理温度下能升华或能蒸发的卤化铵或金属卤化物(以后指一种活化剂)的混合物组成的处理剂用流化气如氩气进行流态化;2.把一种处理材料放入流化层中并在该被处理材料表面上生成一种碳化物、氮化物或碳氮化物。当表面层形成剂反应时,碳化物形成元素的卤化物气体放出,并且该活化剂气体与被处理材料中的碳反应时生成碳化物;而当以同样方法生成的氮化物生成元素的卤化物的气体与钢中的氮或导入流化层的氮反应时,生成氮化物。在这个方法中使用的活化剂应当是在或在低于处理温度下能升华或能蒸发的,以防止该处理剂的凝固,从而保持流化状态。因此,在处理剂长期使用期间,活化剂部分逃逸使表面层形成性能降低。所以,生成的碳化物或氮化物层的厚度可能随着处理时间的流逝而减小。作为一种克服这样一个问题的对策,本申请人已经申请了日本专利,申请号为昭60-220925。尤其,在这个早先的申请中,把一种层形成剂和一种活化剂的一种混合物粉末装入一个由多孔材料制成的容器,使之与一种被处理材料在一个由一种流化剂构成的流化层中一起处理并用于该处理过程中。当由层形成剂和活化剂构成的混合物粉末的层生成性能下降时,把该容器从炉子中取出,换上新的层形成剂和活化剂混合物粉末,再重新放入流化层中去。但是,在这种方法中,当层形成性能下降时,每次得调换层生成剂和活化剂的混合物粉末,这样就需要一个复杂的程序,如混合两种粉末、从容器中移去用废的粉末等等,并可能经常中断该涂布操作。因此,本发明的一个目的是提供一种通过应用一个流化层使在一个被处理的物质表面上生成一层表面层(如碳化物层或其它的表面层)的方法,其中处理剂的层形成性能被保持或当这种性能下降时能恢复,因而,能实现经济有效的处理及用于该处理过程的一种设备。根据本发明,上述目的的实现可通过用一种表面处理方法,包括在一个流化床炉子中处理一种由高熔点材料(如氧化铝)粉末和一种用以生成一种碳化物、氮化物、碳氮化物或固体溶液的金属粉末或一种它们的合金的粉末组成的处理剂;把一种流化气(如氩气)导入流化床炉以流化处理剂并形成一个流化层;在该流化层中处理被处理的材料以及向流化层中导入一个定量的卤化物;这样就能在加热时在被处理的金属表面上生成一层该金属的碳化物、氮化物、碳氮化物或固体溶液层。本发明的表面处理方法可以通过一种也是根据本发明的设备来实现,该设备包括一个用来在由一种高熔点材料粉末和一种用来生成一种碳化物、氮化物、碳氮化物的金属粉末或一种它们的合金粉末组成的一种处理剂的流化层中形成所说的表面层的炉体;一个用来加热流化层的加热炉;一根与炉体外部相连的卤化物供给管和一根卤化气体喷射管(安装于炉体内,即在流化层内,低于被处理的材料并高于或低于气体扩散板)。这个卤化物气体喷射管与卤化物供应管相连并在它的外表面上有多个开口进入流化层以喷射出一种卤化物气体。从下面的描述中,并如果结合附图,并在其中给出了较好实施例,本发明上述的其它的目的、特征及优点会变得更清楚。图1至图5用于说明本发明实施例。图1是一个处理设备的示意图;
图2是用于该设备的活化后气体的喷射管的平面图;
图3是沿图2中Ⅲ-Ⅲ线的横截面图;
图4是说明另一个活化剂气体喷射管的实施例的平面图;
图5是沿图4中Ⅴ-Ⅴ线的横截面图。
加入到流化层中用以保持层形成性能的活化剂可以是一种或多种卤化铵、金属卤化物和碱金属或碱土金属卤化物,它们在或在低于处理温度下是能升华的或能蒸发的。该活化剂的熔点可以高于或低于处理温度。该活化剂通常被连续地以固体状态,如粉末态加入。另外,该活化剂也可以从一开始加入到流化剂中。卤化铵可以包括如NH4Cl、NH4Br、NH4F、NH4I和NH4BF4。金属卤化物可以包括如TiF4、VCl3、VF3和FeCl3。碱金属和碱土金属卤化物可以包括如NaCl、KCl、KBF4和NaBF4。被加入的活化剂的量可以随意地选择,可以从以流化剂和层形成剂的总重量为基准的0.05~20%(重量),以得到一个足够厚度的表面层,而且这样一个量的活化剂可以约一分钟到4小时的间隙周期地加入,也可以非周期地加入。如果活化剂的加入量少于0.05%,那么它就得被频繁地加入,因而从工业观点出发就需要一个自动加入装置。另一方面,如果活化剂的加入量超过20%,放出的气体量增加会引起麻烦,如阻塞管子。为了减少废气量以便只需提供较小和较简单的废气处理装置,把每次的加入量减小并以0.1%到0.2%的量连续不断地加入的方法是理想的。因为活化剂在处理温度下升华、蒸发或被熔化,对活化剂的形状没有特别的限制。通常,根据处理的方便性,它以粒状、柱状或块状形式被应用。
通过一个附加的装置来加入活化剂,例如,如图1所示。如图2和图3所示,该装置包括一根活化剂供应管6和几根喷射活化剂气体的管7。该装置安装于流化层4中被处理的材料3下面。多根气体喷射管7相互之间安排为一个预先确定的角度以使气体流动均匀。如果,“在一个与流化气流动方向垂直的平面上的卤化物气体喷射管与卤化物供给管的总横截面积”与流化层的垂直横截面积的比太大的话,均匀的流化状态就不再保持。实际上,这个比不大于1/3是实际上较好的。在这个范围内,管7的直径可以增大或管7的数量可以增加。管6和管7的横截面形状可以是圆形的、椭圆形的或方形的。最好要选择管7的长度使之对于流化层的中心位置来说尽可能的点一点对称。对活化剂喷射管7的较低的表面形成大量的小孔。该小孔的数量、直径和分布的决定应使保持气体的流动均匀。例如,处于靠近活化剂供给管的位置处的小孔的直径和数量可以比处于离供给管远的位置上的小孔的直径和数量小一些和少一些以使在流化层横截面上的活化剂气体浓度均匀,这样是理想的。活化剂供给管的一端延伸出炉子外,并与一个活化剂供料漏斗8相连。贮存于漏斗8中的活化剂的粒10或其它被杆9推动并落入活化剂供给管6。当活化剂到达被加热到高于其升华或蒸发温度的位置时便升华或蒸发。该管子是紧密地闭合的以防止活化剂气体逸出外面或外部大气侵入炉子内。当供应的活化剂到达供给管的高温区时,由于活化剂的升华或蒸发产生的活化剂气体因其膨胀能力而通过配置于活化剂气体喷射管7的下表面上的小孔71喷出活化剂气体。在这种情况下,也可以向管6供应一种惰性气体或其它类似气体以有利于活化剂气体喷出。而且,活化剂气体喷射管可以是如图4所示的环形。这种情况下,活化剂气体喷射管7可以安装在低于气体扩散板12的下面,而与管7相连的活化剂供应管6可以装在炉体1的外面。此外,可以通过用一个位于炉子外的附在活化剂供应管的某一位置处的加热器使被推向内部的活化剂颗粒或其它形式活化剂在加入到炉子前气化。
用作流化剂的高熔点材料粉末应当是惰性的且不与被处理材料中的组分金属反应,用于通常的热处理中的这些材料的任一种,如三氧化二铝、二氧化硅、二氧化钛、二氧化锆等等可以被应用。高熔点材料可以单独被用,也可以以它们的二种或三种的混合物形式使用。
构成层形成剂用作碳化物或氮化物形成元素的金属涉及那些能易于与碳和/或氮键合形成碳化物、氮化物或碳氮化物的金属,典型地可以包括Ⅳa族元素的钛、Ⅴa族元素的钒、铌和钽、Ⅵa族之素的铬和Ⅶa族元素锰。还有,用于形成一种固体溶液的金属可以涉及那些易于与基体元素形成一种固体溶液的金属,典型的为钛和铬。此外,含有这样一些金属的合金也可以被用作层形成剂,它们包括如Fe-V、Fe-Nb、Fe-Cr等铁合金。为了生成复合物或两层或更多层的碳化物或氮化物,可以以混合物形式使用二种或更多种形成碳化物、氮化物、碳氮化物或固体溶液或合金的元素金属。
无论是高熔点材料粉末还是用来形成碳化物或其它的元素的金属粉末的颗粒大小希望选择在60目到350目的范围内。如果颗粒大小比60目粗,为了流化处理剂需要大量的流化气。如果它比60目粗,流化气的流速会变得太高。结果是放出卤化物气体在流化层中的停留时间太短,从而要求大量的活化剂以使卤化物气体存在于流化层中。另外,如果流速太高,卤化物气体没有足够的时间与被处理的材料反应并在当它不能进行层的形成时被排出。相反,颗粒大小比350目细也是不理想的,因为这样的粉末会被浮起造成处理的困难。
根据条件,处理剂的粉末可能堵塞流化气的入口而妨碍正常流化。然而,可以把粗颗粒(粒子大小为5×20目)的氧化铝或其它高熔点材料置于气体入口和处理剂粉末之间。层形成剂量最好在处理剂总量的1~50%(重量)。如果这个量超过50%(重量),则流化剂有可能会变紧密而使流化态不能保持。说到被处理的材料,在生成碳化物或碳氮化物层的情况下可以是含碳、烧结碳化物和主要由石墨构成的含碳材料的铁、镍和钴。当被处理材料中所含的碳和处理剂中的碳化物形成元素互相键合时,在被处理材料的表面上就形成了碳化物。在被处理的材料中含至少0.2%的碳是合适的。如果碳含量小于0.2%,可能难以形成碳化物层,或者可能需要一个长的时间以形成一层具有实际可接受厚度的碳化物层。另外,如果被处理的材料是一种不含碳的金属,可能通过使用另一个炉子或在同一个流化床炉子中预先对材料进行涂布处理,接着再进行按本发明的涂布处理来实现该材料的碳化。在后一种情况中,通常实施碳化处理时,先供给氮气或氩气,同时还供给甲醇或其它类似物质,然后再在供应氩气的同时加入活化剂。
在形成氮化物层的情况中,并不总是需要被处理的材料含有碳,因而各种金属材料,如铁、镍和钴、烧结碳化物和如氧化物那样的非金属材料,如三氧化二铝和烧结陶瓷可以被使用。在这种情况下,使用一种含氮气体作为流化气以通过在含氮气体和处理剂中的氮化物形成元素之间键合的方式在被处理材料的表面上形成一种氮化物。如果被处理材料中含碳,则形成一层碳氮化物。
无论在生成碳化物层还是在生成氮化物层的情况中,都可能使用一种先经氮化处理的铁合金材料作为被处理材料。在形成碳化物层的情况下可能形成一层含氮的碳化物层,反之,在形成氮化物层情况下,不用含氮气体作为流化气也能生成氮化物层。
在生成固体溶液层的情况下,用不含碳的金属材料如铁和不锈钢。如已在许多文献中被公知的那样,如果在被处理的材料和供应的气体中没有含有充足的碳或氮的话,作为层形成剂的一部分的那些元素可能扩散进入被处理材料形成一层固体溶液层。
说到流化气,在生成碳化物或固体溶液层的情况中,使用如氩那样的惰性气体;反之,在形成碳氮化物或氮化物层的情况中,用氮或含氮气体,如氨或由它们组成的气体混合物,同时还与氩气一起使用。也可以把小量的氢加入流化气,气体可以是一般纯度的。
流化气可以任何希望的流速供给流化床炉子,只要这流速在能实现充分和良好的流态化的范围内。如果流速太慢,则流态化就会不充分,提供的流化层内的温度分布会不好。另一方面,如果流速太高,耗费的气体量增加,而且会进而引起显著的鼓泡现象使流化过程变困难。
当流化气被送进流化床炉子时,炉子中的处理剂被向上吹起并由于流化气连续流入里面引起的压力而不会落下,这样,形成一层流化层并以漂浮状态移入炉子。
在本发明中用的流化床炉子可以是任一通常用于干燥、煅烧、还原等的流化床炉子。例如,如图1所示,炉子可以是这样的一个流化气入口11,开口于炉体1较低的位置,而且气体扩散板12装在炉子的流化气入口一侧。有一个气体排出口51的盖5连接于炉子上部。此外,炉子也可以是这样的结构炉体与盖子成一整体,在炉体上安装一可以打开的门以装入或移走活化剂气体喷射管和被处理材料。
加热步骤的实现是通过流化层作为加热介质加热流化层。加热的专用方式可以设计为如图1所示的那样,其中包括流化层的流化床炉子插入一个外加热器2(如一个电炉)内部,这样流化层被从外面加热;或者以这样的方式,其中用安装在流化床炉子内的一个加热器直接加热流化层。
加热温度可以在700~1200℃内选择。如果温度低于700℃,则层形成速度显著减低,反之,如果温度高于1200℃,被处理材料的基体可能被破坏,因此这两种情况都是不利的。然而,在如前所述用先氮化处理的铁合金材料作为被处理材料的情况下,处理剂中的碳化物或氮化物形成元素会扩散进入通过氮化处理形成的铁氮化物中去(在含碳的铁合金材料的情况下为铁碳氮化物),该元素与铁发生置换反应形成该元素的氮化物(在含碳的铁合金材料的情况下则形成该元素的碳氮化物)。在这种情况下,虽然在较低的温度下也会形成表面层,仍希望把加热温度选择在400~1200℃内。
处理时间根据被处理材料的组成和将形成的层的组成和厚度在0.5至5小时内选择。在较高的处理温度下一般要求较短的处理时间周期;另一方面,在较低的处理温度下要求较长的处理时间周期。
在本发明中,因为在表面处理步骤中作为活化剂的卤化物是从外部通入流化床内的,所以不再需要通常的混合粉状处理剂、从容器中回收处理剂及混合活化剂的工序,但是表面处理可以连续地进行。另外,因为活化剂可以一点一点地加入,从流化层逸出的卤化物气体量不大,因此可以有利地把废气处理装置做得较小、较简单。此外,该处理剂能被使用一个长时期而不需要调换,而且有价值的碳化物形成元素,如钛和钒的量可以减少。
此外,当有插入和取出被处理材料的自动装置时(如在通常的利用流化层的加热过程中实现的那样),可能实现连续处理。
现在参考实施例来描述本发明。
实施例1
根据本发明的碳化物涂布处理通过利用如图1所示的流化床炉子被实现。该流化床炉子包括一个炉体1,它有一根供给流化气氩气的、开口于其底部的气体给管11;并有一个气体扩散板12,它安装于开口处的略上方,把炉子内部分隔成两部分。一个可拆卸的盖与盖在炉体1的顶部和一根开口于盖5上的与一个用来捕集废气的净气器连通的排气管51。
安装了加热器2,围在炉体1的周围。炉体1包括一个圆柱形壳体,它由耐热的钢制成,直径为60mm,高为800mm。
把1公斤的粉状处理剂置于流化床炉内的气体扩散板12上。该处理剂含60%的氧化铝粉(80-100目)和40%的钒铁粉(含70%钒,100~200目)。然后,供应作为流化气的氩气,压力为1.5公斤/平方厘米,以140厘米/分的流速从气体供给管11进入炉体1。然后,粉状的处理剂被流化形成流化层4。在流化层的较低部位,8根与活化剂供给管6相连的活化剂气体喷射管7(如图2和图3所示)安装在气体扩散板12在上方、活化剂供给管6的内径是9mm,而活化剂气体喷射管7的内径是3mm。还有,每根气体喷射管7有数个小的气体喷射孔71,每个直径0.5mm,位于管7的下表面上的三个位置上。
然后,把两个被处理材料3(合金工具钢SKD11,直径7mm,高50mm)各用一个连接于炉盖内表面的钩子悬挂在流化层的几乎是中心的位置上。然后,把盖5盖到炉体1顶部,紧密封闭,加热流化层到1000℃。
然后把0.4克作活化剂用的氯化铵用液压法模压成圆柱形(直径7mm,高7mm),把许多氯化铵压片装入上述的活化剂供料漏斗8,把上端紧密封闭后,用杆9推动使二块压片落入活化剂供给管。二块氯化铵压片的数量相当于处理剂总重量的0.08%。开始操作1小时后,再供给一块氯化铵压片。经2小时处理后,卸下炉盖,把被处理材料从炉中拿出,然后用油冷却。
然后用上述的同样方式再放二块同样组成和形状的被处理材料到流化层的中心位置上,接着用上述的同样方式进行处理并同时不断供应氯化铵压片。以上述方式重复四次。当用肉眼观察这样得到的表面时,被处理材料上既没有处理剂粘附于其上,也看不出有颜色不均匀之处,而且材料的表面是光滑的。然而,当用显微镜观察其横截面时,可以看到形成了5~6μm厚的均匀的涂层。接着,用X-射线衍射法证明了这一层是由碳化钒(VC)构成的。测定该层的硬度表明其硬度约HV3000。
如上所述仅通过选择性地加入约0.1%的活化剂就能被涂上一个有足够厚度的碳化钒层。
实施例2用1公斤含60%氧化铝粉(80~100目)和40%钛铁粉(100~200目)的处理剂使用一个流化床炉子进行碳化物涂布处理,其中,安装了如图4所示的活化剂气体喷射环13代替了用于例1中的流化床的活化剂气体喷射管7。活化剂气体喷射环13与活化剂供给管6垂直连接。管6的顶端伸出炉子外并与活化剂供料漏斗等以如例1中所示的同样方式相连。活化剂供给管的内径为10mm,而在与喷射环连接部分,其直径减小到5mm。活化剂气体喷射环的外径为55mm,而构成环的管子的内径为5mm。在环的下表面上15个位置上等距离地形成直径各为0.5mm的小孔。然后,把被处理材料(碳SK4,直径7mm,高50mm)用连接在盖5内表面上的钩子悬挂在流化床的中心位置上。用盖5盖住炉子顶部并紧密封闭,把流化层加热到1000℃。然后,把0.9克作活化剂用的氯化铵粉(80~100目)用液压方法模压成9mm直径和9mm高的圆柱形。把氯化铵压片注入上述的活化剂供料漏斗8,紧密封闭后,用杆9将其推落到活化剂供给管内。氯化铵压片的量相当于处理剂总量的0.09%。开始操作1小时后,再供给一个氯化铵。进行两小时热处理后,把被处理材料从炉子中取出并用油冷却。然后,用氯化铵处理如上所述的同样组成和形状的被处理材料,供应到活化剂供给管内的氯化铵的量与上面所述的一样,并进行2小时的处理。以上述方式重复五次。发现每一个这样方法得到的表面上生成了9~10μm厚的光滑的涂层。用X-射线衍射法分析该涂层,确定该涂层是碳化钛(TiC)涂层。测定涂层的硬度约为3500HV。
实施例3用例1中的流化床炉子进行碳化物涂布和固体溶液层生成处理,使用1公斤的含60%的三氧化二铝粉(80~100目)和20%的铬粉(100~200目)的处理剂。
首先,用与盖子内表面相连的钩子把被处理的材料(碳钢SK4和工业纯铁,每个直径7mm,高50mm)悬挂于流化层的中心位置上。用盖子把炉顶盖上,紧密封闭后把流化层加热到1000℃。然后,把作为活化剂的0.7克溴化铵粉(80~100目)用液压方法模压成圆柱形粒子(直径7mm,高7mm)。把溴化铵粒放入上述活化剂供料漏斗8,紧密封闭该漏斗的上部后,用杆9把一个活化剂粒子推落入活化剂供给管。一个溴化铵粒子相当于处理剂总量的0.07%。操作开始一个半小时后,再供给一个溴化铵粒子。进行2小时热处理后,把被处理材料从炉子中取出并用油冷却。然后,用溴化铵处理如上所述的同样组成的形状的被处理材料,把如上所述的同样量溴化铵供给活化剂供给管内,进行2小时处理。以上述方式重复5次。发现每一个这样得到的被处理材料都有十分光滑的无粉末粘附的表面。而且发现SK4表面形成了厚度为8~9μm的涂层。用X-射线衍射法分析确证这一涂层是碳化铬(Cr7C+3Cr23C6)层。测定该层的硬度为2000HV。而在工业纯铁的情况中,生成了厚度为24~25μm的铬-固体溶液层。用X-射线微分析仪分析该涂层的横截面中的铬的含量,确定铬含量最大为60%。
一种在被处理物质表面上形成—碳化物、氮化物、碳氮化物或固体溶液的表面涂层的方法,包括把由一种高熔点材料的粉末和一种用以形成一种碳化物、氮化物、碳氮化物或固体溶液的金属粉末或一种它们的合金粉末组成的一种处理剂装入一个流化床炉子,把流化气导入流化床炉子以流化处理剂并形成一流化层,把被处理材料装入流化层并且把预定量的卤化物导入流化层;以及用来在被处理材料上形成一表面涂层的一种设备,包括一个用来在处理剂的流化层中形成表面涂层的设备。
表面处理的方法及其设备制作方法
- 专利详情
- 全文pdf
- 权力要求
- 说明书
- 法律状态
查看更多专利详情
下载专利文献
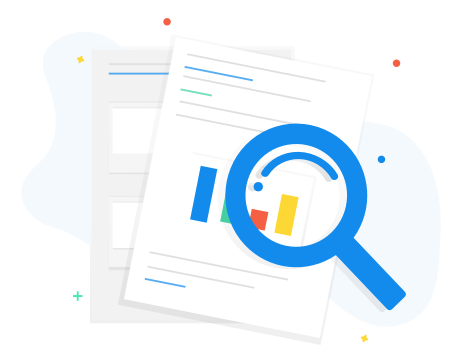
下载专利
同类推荐
-
奉明明马蒂亚斯·布兰德尔马蒂亚斯·布兰德尔新津洋司郎新津洋司郎新津洋司郎新津洋司郎
您可能感兴趣的专利
-
新津洋司郎加藤行加藤行曹仁镐, 韩东柱崔昌奎
专利相关信息
-
刘光明章小龙, 茅建刚朱秀红王建设, 王琳壮晓健壮晓健