三片式整体预制透水框架一次成型模具的制作方法[0002]目前,由于透水框架是四面六边形结构,大规模一次成型整体预制较为困难,不易脱模,成本高,尚未有便于施工且效率较好的方法。因此,通常是先采用简单的杆件模具进行混凝土杆件预制,每根杆件的两端均有IOcm左右长度的预留钢筋外露。然后将六根杆件按四面六边形结构进行焊接组装,拼装时将杆件顶端钢筋用电弧焊接,三根交叉钢筋两两搭接单面焊,焊接组装成一个整体。最后,对钢筋外露部分作涂漆防锈处理,先涂一遍防锈漆,再涂两遍调和漆。透水框架焊接预制的这种方法需大量人工,施工工序较多,较为繁琐,整体性较差,易松散,同时防锈涂层容易造成污染,预制成品的外露钢筋也无较好的保护措施,容易在施工抛投过程中挂住抛投人员衣物,造成人员落水,具有极大安全隐患。另外在枯水期时,钢筋外露会影响长江航行船舶的船体从而引发安全事故,而且焊接的外露钢筋长时间在水中浸泡容易脱焊散架,使得透水框架的使用寿命缩短。
[0003]为解决上述技术问题,本发明提供一种三片式整体预制透水框架一次成型模具,该模具结构简单、操作方便。可实现四面六边形透水框架大规模一次成型整体预制,简化整体预制施工工序,提高模具的循环效率,有效的降低预制成本。[0004]本发明采取的技术方案为:三片式整体预制透水框架一次成型模具,包括三个片状模片、内模和钢筋骨架,三个片状模片位于钢筋骨架三边,每一个片状模片是由三个单元板和三个挡板构成的整体呈三角形的模片。所述三个单元板,包括两个设有弧形凹槽的侧板、一个长方形的底板。所述三个单元板两两连接成三角形整体,所述挡板固定连接在所述三个单元板内侧,所述三个挡板两两固定连接成封闭形的三角形框。所述侧板、挡板和底板设有折边,折边上开设通孔,通孔位置设有螺杆,所述内模,由三个等长的长方形模片两两固定连接成整体,内模的底端设有L形折边。所述L形折边向内延伸构成一个振捣平台。[0005]所述挡板两端的长度比单元板边长稍短。所述底板的两端设有垂直挡板。所述侧板、挡板和底板的折边位置设有凹凸槽。所述内模的连接处设有小挡板。所述内模的底端设有L型折边。[0006]本发明三片式整体预制透水框架一次成型模具,模具结构简单,操作方便,可实现四面六边形透水框架大规模一次成型整体预制,极大的简化了整体预制施工工序,减少了模具组装及浇筑的施工时间和人工,提高了模具的循环效率,极大的促进了生产效率,而且整体性好,振捣彻底,气泡少,强度高,不会发生松散现象,另外钢筋不外露,解决了焊接透水框架易造成环境污染、安全隐患大和使用寿命短等问题。
[0007]图1为本发明模具结构示意图;
图2为本发明片状模片结构示意图。
[0008]图3为本发明钢筋骨架结构示意图。
[0009]如图f图3所示,三片式整体预制透水框架一次成型模具,包括三个片状模片1、内模2和钢筋骨架3,三个片状模片I位于钢筋骨架3三边,每一个片状模片I是由三个单元板和三个挡板1.2构成的整体呈三角形的模片。所述三个单元板,包括两个设有半圆形的弧形凹槽1.3的侧板1.1和一个长方形的底板1.4。所述三个单元板两两连接成三角形整体,所述挡板1.2固定连接在所述三个单元板内侧,所述三个挡板1.2两两固定连接成封闭形的三角形框。片状模片I的侧板、挡板和底板的边缘均设有向外的折边4,在折边4上开有U型通孔,并于折边4通孔位置的外侧设有可转动的螺杆,三个片状模片I两两拼接组装时,可将拉杆伸入U型通孔内、并通过螺栓进行拉紧固定。所述内模,由三个等长的长方形模片两两固定连接成整体,内模的底端设有L形折边,L形折边向内延伸构成一个振捣平台5。
[0010]所述挡板1.2两端的长度比单元板边长稍短。所述底板1.4的两端设有垂直挡板
1.5。
[0011]所述折边4的位 置设有防止漏浆的凹凸槽。
[0012]所述内模2的连接处设有小挡板。小挡板对内模2的稳定有作用;另外:混凝土灌入时,一般是从三个角位置,小挡板可以预防混凝土撒漏。
[0013]所述内模2的底端设有L型折边6。
[0014]实施步骤:
I)、刷脱模剂,在组装前对本发明模具进行清洗,在本发明模具内侧刷脱模剂。
[0015]2)、模具组装,将制品的钢筋骨架3正放在平整的预制场地,三个片状模片I放于钢筋骨架3的三边,两两拼接对齐,并通过折边4上的螺杆进行固定。再把已固定好的模具倒立起来,将内模2对齐放于倒立模具中间,并通过折边4和振捣器上的可旋转卡扣进行固定,组装好的三个片状模片I和内模2均通过凹凸槽紧密连接,不会发生漏浆现象。模具组装简单易操作,两个工人一分钟即可完成。
[0016]3)、振捣浇筑,将组装好的模具倒立在铺有薄膜的平整硬化预制场地上,振捣器放于内模2的振捣平台5上,再将搅拌好的混凝土灌入模具中,同时打开振捣器,边灌边振捣,直至最上面的混凝土震荡出浆,最后将混凝土外露部分人工抹平。可一次摆放多个模具同时进行振捣浇筑,两个工人广2分钟即可完成一个,而且振捣效果较好,混凝土密实且气泡少。
[0017]4)、脱模,先把可旋转卡扣松开,将内模2从上面轻轻脱出,然后松开折边4上的螺杆,将三个片状模片I向侧边轻拉,即可轻松将模片取下,整个过程无需移动尚未完全凝固的透水框架,在混凝土构件初凝条件下不会对透水框架造成破坏。该过程极大的缩短了脱丰旲的时间,提闻了 1?具的循环使用效率。
[0018]5)、最后对透水框架按混凝土构件规定进行浇水养护,保证透水框架构件的强度。
三片式整体预制透水框架一次成型模具制作方法
- 专利详情
- 全文pdf
- 权力要求
- 说明书
- 法律状态
查看更多专利详情
下载专利文献
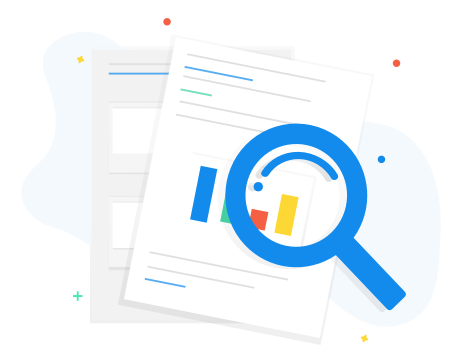
下载专利
同类推荐
-
坂口智, 石川浩树刘建, 陈超刘建, 陈超刘建, 陈超彭威刘建, 陈超
您可能感兴趣的专利
-
刘建, 陈超桥本达也刘升逑秦升益秦升益秦升益刘建, 陈超
专利相关信息
-
刁晓翔刘建, 陈超艾伦·克莱奈特, 约瑟夫·艾尔玛洛维奇田畑宪一王小锋川上祐介, 高阪翔士