一种带肋背楞及其成型方法 [0002] 近年来,随着我国节能降耗、节能减排的为基本国策的推广和人民素质的提高,人 们的环保意识与审美观点都在发生变化。在建设工程中,清水混凝土结构的应用越来越广 泛。在传统的建筑模板体系中,需用大量的木材,但是周转次数少,材料消耗大,施工中工人 随意切割,浪费严重,而且效果远远不能达到清水混凝土的标准。同时,传统的模板施工工 艺管理难度大,施工效率低。 [0003] 采用钢质模板可以在一定程度上解决上述问题。但是,钢质模板在施工中,需要在 其外侧使用高强度背楞来支撑。现有技术中,采用C型钢背楞来支撑钢质模板。 [0004] 但是,混凝土施工环境复杂,背楞需要承受各种力的作用。现有的C型钢背楞抗扭 和抗弯等性能均不尽人意,往往在施工现场发生变形,不得不报废,带来了巨大的损失。 [0005] 另外,C型钢背楞在施工过程中不可能不沾上混凝土,特别是C型槽中往往会淤积 混凝土。在下次使用时,C型钢沾上的混凝土不仅给安装、运输、存放带来了极大的麻烦,也 会影响精度和工程质量。
[0006] 本发明的目的是解决现有的背楞在使用过程中发生变形,大量报废的问题。
[0007] 为实现本发明目的而采用的技术方案是这样的,一种带肋背楞,包括一根中空的、 横截面为矩形的钢管,以下简称矩形钢管。该矩形钢管的长度不限、边长为L和G,L和G可 以相等。所述矩形钢管的四个侧面中,至少一个侧面具有压痕。即所述矩形钢管的四个侧 面中,可以是:只有一个侧面有压痕、两个对称的侧面有压痕、三个侧面有压痕或四个侧面 均有压痕。
[0008] 进一步,所述矩形钢管其中一个侧面的宽度为L,即该矩形钢管的其中一个边长为 L。该侧面上的压痕的宽度K = 0. 3L?0. 75L。
[0009] 进一步,所述矩形的钢管的壁厚为D,所述压痕的深度d = 0. 6D?0. 7D。
[0010] 本发明还公开一种带肋背楞的成型方法:将一根中空的矩形钢管至于水平台面 上,所述矩形钢管宽度为L的一个侧面朝上。
[0011] 所述矩形钢管上方,具有一个钢质滚轮。所述滚轮安装在转轴上。所述滚轮的外 边缘的宽度为S,其中S < L。
[0012] 调整所述滚轮的位置,使得所述滚轮的轴向与矩形钢管的长度方向相互垂直,所 述滚轮的外边缘与矩形钢管朝上的那个侧面接触。对所述滚轮的转轴施加向下的作用力。 使用所述滚轮反复碾压所述矩形钢管朝上的一个侧面,使得所述矩形钢管的一个侧面上被 碾出深度为d的压痕。
[0013] 本发明的技术效果是毋庸置疑的。该背楞具有很好的力学性能。可以适应模板施 工中复杂的环境,应对各方面的冲击。流转的时间常,报废率极低。更好的是,本本发明的 背楞只会是在表面沾上混凝土,不会像C型背楞那样在内部淤积大量混凝土。而表面沾上 混凝土很容易被清理掉,不会影响背楞的下次使用。
[0014] 图1为本发明背楞的立体图;
[0015] 图2为本发明背楞的截面图;
[0016] 图3为加工本发明背楞的滚轮的示意图; 图4是实施例1的矩管A的横截面示意图; 图5为矩管抗弯测试示意图; 图6是实施例1的矩管A抗弯测试中位移分析; 图7是实施例1的矩管A抗弯测试中的Mises应力云图; 图8为矩管抗扭测试示意图; 图9是实施例1的矩管A抗扭测试中位移分析; 图10是实施例1的矩管A抗扭测试中的Mi ses应力云图; 图11是实施例1的矩管A抗扭测试中总体转角云图; 图12是实施例1的矩管B的横截面示意图; 图13是实施例1的矩管B抗弯测试中位移分析; 图14是实施例1的矩管B抗弯测试中的Mi ses应力云图; 图15是实施例1的矩管B抗扭测试中位移分析; 图16是实施例1的矩管B抗扭测试中的Mi ses应力云图; 图17是实施例1的矩管B抗扭测试中总体转角云图; 图18是实施例2的矩管A的横截面示意图; 图19是实施例2的矩管A抗弯测试中位移分析; 图20是实施例2的矩管A抗弯测试中的Mises应力云图; 图21是实施例2的矩管A抗扭测试中位移分析; 图22是实施例2的矩管A抗扭测试中的Mises应力云图; 图23是实施例2的矩管A抗扭测试中总体转角云图; 图24是实施例2的矩管B的横截面示意图; 图25是实施例2的矩管B抗弯测试中位移分析; 图26是实施例2的矩管B抗弯测试中的Mises应力云图; 图27是实施例2的矩管B抗扭测试中位移分析; 图28是实施例2的矩管B抗扭测试中的Mises应力云图; 图29是实施例2的矩管B抗扭测试中总体转角云图。 图中:矩形钢管1、待加工面2、压痕3。
[0017] 下面结合附图和实施例对本发明作进一步说明,但不应该理解为本发明上述主题 范围仅限于下述实施例。在不脱离本发明上述技术思想的情况下,根据本领域普通技术知 识和惯用手段,做出各种替换和变更,均应包括在本发明的保护范围内。
[0018] 实施例1 :
[0019] 准备两根尺寸相同的矩形钢管(下文简称矩管)。这两根矩管的长度为1000mm, 横截面为48mm*38mm(即矩管的其中两个相对的侧面的宽度38mm,另外两个相对的侧面的 宽度48mm),厚度为2. 2mm,材料Q235钢。两根尺寸相同的矩形钢管的性能参数如下:
[0020] 将其中一根矩管记为矩管A,另一根矩管记为矩管B。
[0021] 参见图4,图中数值的单位为mm,将所述矩管A的两个相对的侧面加工出压痕。即 对所述矩管A的、宽度为38mm的两个侧面加工出深度为1. 5mm、宽度为18mm的压痕,其加 工的方式可以是滚压加工。
[0022] 实施例中,加工出压痕的方式是:将置于水平台面上,矩管A的上方具有一个滚 轮。所述滚轮的轴向垂直于矩管A的长度方向。对所述滚轮的转轴施加坚直向下的力,并 使得所述滚轮的外圆在矩管A朝上的侧面(宽度为38mm)的中心来回滚压,使得该侧面上 被碼出压痕。
[0023] -、通过上述加工,使得矩管A(图4)两面带肋后,对矩管A进行力学性能测试:
[0024] 1、抗弯计算:
[0025] 参见图5, ANSYS模型简述:两个集中荷载,大小均为1KN,作用在被测矩管(在该 材料的简支梁模型)上1/3处。
[0026] 建模分析结果如下:
[0027] 1)位移分析结果如图6,最大位移0· 00147mm。
[0028] 2)Mises应力云图如图7,最大应力0· 068MPa。
[0029] 2、抗剪计算:
[0030] 参见图8,ANSYS模型简述:被测矩管(在该材料的模型)一端固端,另一端为悬臂 端。对悬臂端施加力矩作用(大小1KN),分析结果如下:
[0031] 1)位移分析结果如图9,最大位移3. 497mm。
[0032] 2)Mises应力云图如图10,最大应力114. 504MPa。
[0033] 3)总体转角云图如图11,最大转角0. 223rad。
[0034] 二、矩管B (图12)不进行任何加工,进行力学性能测试:
[0035] 1、抗弯计算:
[0036] 参见图5, ANSYS模型简述:两个集中荷载,大小均为1KN,作用在被测矩管(在该 材料的简支梁模型)上1/3处。建模分析结果如下:
[0037] 1)位移分析结果如图13,最大位移0· 00142mm。
[0038] 2)Mises应力云图如图14,最大应力0· 0657MPa。
[0039] 2、抗剪计算:
[0040] 参见图8,ANSYS模型简述:被测矩管(在该材料的模型)一端固端,另一端为悬臂 端。对悬臂端施加力矩作用(大小1KN),分析结果如下:
[0041] 1)位移分析结果如图15,最大位移3. 746mm。
[0042] 2)Mises应力云图如图16,最大应力124. 551MPa。
[0043] 3)总体转角云图如图17,最大转角0· 234rad。
[0044] 两种截面(图4和图12)的数据对比分析如下:
[0045] 从抗弯角度而言,经过滚压加工的矩管(截面如图4)与未经过加工的矩管(截面 如图12)相比,最大应力和最大变形变化不大,对抗弯性能影响不大。但是从抗扭角度而 言,经过滚压加工的矩管(截面如图4)与未经过加工的矩管(截面如图12)相比,施加同 样的荷载,最大位移,最大应力和最大转角均明显减小,显著提高了抗扭性能。提高了模架 的使用安全性及经济效益。
[0046] 实施例2 :
[0047] 准备两根尺寸相同的矩形钢管(下文简称矩管)。这两根矩管的长度为1000mm, 横截面为48mm*38mm(即矩管的其中两个相对的侧面的宽度38mm,另外两个相对的侧面的 宽度48mm),厚度为2. 2mm,材料Q235钢。两根尺寸相同的矩形钢管的性能参数如下:
[0048] 将其中一根矩管记为矩管A,另一根矩管记为矩管B。
[0049] 参见图18,图中数值的单位为mm,将所述矩管A的两个相对的侧面加工出压痕。即 对所述矩管A的、宽度为38mm的两个侧面加工出深度为1. 5mm、宽度为13mm的压痕,其加工 的方式可以是滚压加工。
[0050] 实施例中,加工出压痕的方式是:将置于水平台面上,矩管A的上方具有一个滚 轮。所述滚轮的轴向垂直于矩管A的长度方向。对所述滚轮的转轴施加坚直向下的力,并 使得所述滚轮的外圆在矩管A朝上的侧面(宽度为38mm)的中心来回滚压,使得该侧面上 被碼出压痕。
[0051] 一、通过上述加工,使得矩管A(图18)两面带肋后,对矩管A进行力学性能测试:
[0052] 1、抗弯计算:
[0053] 参见图5, ANSYS模型简述:两个集中荷载,大小均为1KN,作用在被测矩管(在该 材料的简支梁模型)上1/3处。
[0054] 建模分析结果如下:
[0055] 1)位移分析结果如图19,最大位移0· 00148mm。
[0056] 2)Mises应力云图如图20,最大应力0· 0694MPa。
[0057] 2、抗剪计算:
[0058] 参见图8,ANSYS模型简述:被测矩管(在该材料的模型)一端固端,另一端为悬臂 端。对悬臂端施加力矩作用(大小1KN),分析结果如下:
[0059] 1)位移分析结果如图21,最大位移3. 518mm。
[0060] 2)Mises应力云图如图22,最大应力114MPa。
[0061] 3)总体转角云图如图23,最大转角0. 220rad。
[0062] 二、矩管B(图12)不进行任何加工,进行力学性能测试:
[0063] 1、抗弯计算:
[0064] 参见图5, ANSYS模型简述:两个集中荷载,大小均为1KN,作用在被测矩管(在该 材料的简支梁模型)上1/3处。建模分析结果如下:
[0065] 1)位移分析结果如图13,最大位移0· 00142mm。
[0066] 2)Mises应力云图如图14,最大应力0· 0657MPa。
[0067] 2、抗剪计算:
[0068] 参见图8,ANSYS模型简述:被测矩管(在该材料的模型)一端固端,另一端为悬臂 端。对悬臂端施加力矩作用(大小1KN),分析结果如下:
[0069] 1)位移分析结果如图15,最大位移3. 746mm。
[0070] 2)Mises应力云图如图16,最大应力124. 551MPa。
[0071] 3)总体转角云图如图17,最大转角0. 234rad。
[0072] 两种截面(图18和图12)的数据对比分析如下:
[0073] 从抗弯角度而言,经过滚压加工的矩管(截面如图18)与未经过加工的矩管(截 面如图12)相比,最大应力和最大变形变化不大,对抗弯性能影响不大。但是从抗扭角度而 言,经过滚压加工的矩管(截面如图18)与未经过加工的矩管(截面如图12)相比,施加同 样的荷载,最大位移,最大应力和最大转角均明显减小,显著提高了抗扭性能。提高了模架 的使用安全性及经济效益。
[0074] 实施例3 :
[0075] 准备两根尺寸相同的矩形钢管(下文简称矩管)。这两根矩管的长度为1000mm, 横截面为48mm*38mm(即矩管的其中两个相对的侧面的宽度38mm,另外两个相对的侧面的 宽度48mm),厚度为2.2mm,材料Q235钢。两根尺寸相同的矩形钢管的性能参数如下:
[0076] 将其中一根矩管记为矩管A,另一根矩管记为矩管B。
[0077] 参见图24,图中数值的单位为mm,将所述矩管A的两个相对的侧面加工出压痕。即 对所述矩管A的、宽度为38mm的两个侧面加工出深度为1. 5mm、宽度为28mm的压痕,其加工 的方式可以是滚压加工。
[0078] 实施例中,加工出压痕的方式是:将置于水平台面上,矩管A的上方具有一个滚 轮。所述滚轮的轴向垂直于矩管A的长度方向。对所述滚轮的转轴施加坚直向下的力,并 使得所述滚轮的外圆在矩管A朝上的侧面(宽度为38mm)的中心来回滚压,使得该侧面上 被碼出压痕。
[0079] -、通过上述加工,使得矩管A(图24)两面带肋后,对矩管A进行力学性能测试:
[0080] 1、抗弯计算:
[0081] 参见图5, ANSYS模型简述:两个集中荷载,大小均为1KN,作用在被测矩管(在该 材料的简支梁模型)上1/3处。
[0082] 建模分析结果如下:
[0083] 1)位移分析结果如图25,最大位移0· 00151mm。
[0084] 2)Mises应力云图如图26,最大应力0· 0698MPa。
[0085] 2、抗剪计算:
[0086] 参见图8,ANSYS模型简述:被测矩管(在该材料的模型)一端固端,另一端为悬臂 端。对悬臂端施加力矩作用(大小1KN),分析结果如下:
[0087] 1)位移分析结果如图27,最大位移3. 668mm。
[0088] 2)Mises应力云图如图28,最大应力114.6MPa。
[0089] 3)总体转角云图如图29,最大转角0· 229rad。
[0090] 二、矩管B(图12)不进行任何加工,进行力学性能测试:
[0091] 1、抗弯计算:
[0092] 参见图5, ANSYS模型简述:两个集中荷载,大小均为1KN,作用在被测矩管(在该 材料的简支梁模型)上1/3处。建模分析结果如下:
[0093] 1)位移分析结果如图13,最大位移0· 00142mm。
[0094] 2)Mises应力云图如图14,最大应力0· 0657MPa。
[0095] 2、抗剪计算:
[0096] 参见图8,ANSYS模型简述:被测矩管(在该材料的模型)一端固端,另一端为悬臂 端。对悬臂端施加力矩作用(大小1KN),分析结果如下:
[0097] 1)位移分析结果如图15,最大位移3. 746mm。
[0098] 2)Mises应力云图如图16,最大应力124. 551MPa。
[0099] 3)总体转角云图如图17,最大转角0. 234rad。
[0100] 两种截面(图24和图12)的数据对比分析如下:
[〇1〇1] 从抗弯角度而言,经过滚压加工的矩管(截面如图24)与未经过加工的矩管(截 面如图12)相比,最大应力和最大变形变化不大,对抗弯性能影响不大。但是从抗扭角度而 言,经过滚压加工的矩管(截面如图24)与未经过加工的矩管(截面如图12)相比,施加同 样的荷载,最大位移,最大应力和最大转角均明显减小,显著提高了抗扭性能。提高了模架 的使用安全性及经济效益。
一种带肋背楞及其成型方法
- 专利详情
- 全文pdf
- 权力要求
- 说明书
- 法律状态
查看更多专利详情
下载专利文献
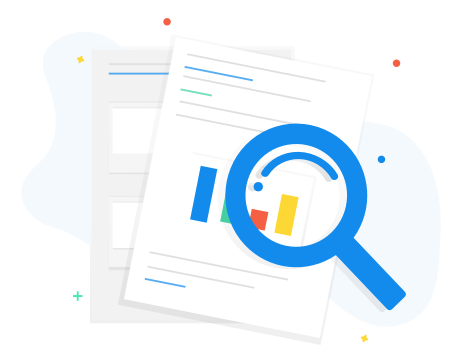
下载专利
同类推荐
-
彭威秦升益秦升益秦升益王小锋
您可能感兴趣的专利
-
李欢欢迈克尔·R·贝里根迈克尔·R·贝里根孟宪安慧 张, 李洪盛刘必成
专利相关信息
-
方世峰, 张锦方世峰, 张锦方世峰, 张锦方世峰, 张锦