一种高效节能型硬硅钙石绝热制品的制造方法[0002]现有耐温100(TC的硅酸钙绝热板,都是采用如下生产技术:磨细或/和天然硅粉与石灰乳或/和氢氧化钙粉按Ca0/Si02摩尔比0.9^1.0的比例混合,在10-30倍重的水中、在1.2~2.0MPa的压力下动态水热反应,制成合成料浆,再添加纸浆、玻纤等增强纤维,混匀,在带滤水孔的模具内压制成型,烘干即是成品。由于现有生产技术的限制,作为原材料的硅粉不能很细,D5tl—般为14-30 μ m,否则生产的合成料就难以或无法压制成型,或板材严重收缩变形。因此,板材的密度一般为170-270kg/m3,平均温度400°C时的导热系数一般为0.10 ff/(m.K)左右,甚至更大。[0003]在硅酸钙绝热板使用领域,由于技术进步,工业窑炉要求在设备基础和外形尺寸不变或变化很小的情况下,在原有的基础上加大产能,降低能耗,这就需要高效绝热材料。按水泥工业的要求,综合能耗在现有的基础上要降低16.7%,这一点现有的硅酸钙绝热板无法达到,其主要原因是现有硅酸钙绝热板的微观结构中孔径较大,基本在30(T3000 nm之间,绝热材料孔径大在绝热方面存在如下不利因素:一、气体分子在其中很容易蹿动,分子之间碰撞几率增多,增加了传热;二、孔径大,开孔率大,空隙之间相互连通,辐射传热就通畅,不利于绝热。
[0004]本发明所要解决的技术问题是,提供一种高效节能型硬硅钙石绝热制品的制造方法,生产的高效节能型硬硅钙石绝热板除了具有强度高、耐温高的性能外,特别具有优异的绝热性能。[0005]为了实现上述目的,本发明采取的技术方案是: 一种高效节能型硬硅钙石绝热制品的制造方法,其特征在于包括如下步骤: 1)、将硅质原料和钙质原料按Ca/Si摩尔比0.90-l.05在水中进行配料,混合均匀,制备入爸料;其中娃质原料磨细至D5tl < 5 μ m, 一般在3 μ m左右;其中钙质原料为石灰乳、氢氧化钙粉和电石渣粉中的一种或者两种以上按任意比例混合;所用石灰乳、氢氧化钙粉和电石渣粉要求沉降值在250-300 ml之间; 2)、将入釜料注入带搅拌的合成釜内并加水至水/固重量比12~30,通蒸汽加热,至釜内压力超过1.2 MPa时开始保温,保温3-5小时,之后降温至常压,即得合成料浆;
3)、在合成料浆中添加合成料浆重量1.5~5 %的天然纤维浆、合成料浆重量1.5~5 %的玻璃纤维,混匀,在带滤水孔的模具内压制成型,烘干即是高效节能硬硅钙石绝热原板;
4)、在上述高效节能硬硅钙石绝热原板外部均匀涂刷一层胶,紧接着整体覆上铝箔,待胶凝固后即得高效节能型硬硅钙石绝热板。另一种包覆铝箔的方式是:将步骤2)所制备复合板套进铝箔袋内,封口,抽真空。[0006]第2)步中,通蒸汽加热,至釜内压力1.5~2.0 MPa,保温3.5~5小时。
[0007]第2)步中,加热和保温过程中每间隔5~30分钟搅拌30秒飞分钟。
[0008]所述的娃质原料是SiO2含量不小于95 %的娃砂和娃粉中的一种或者两种按任意比例混合。
[0009]所述的天然纤维浆是普通造纸用纸浆、竹浆和棉绒浆中的一种或者两种以上按任意比例混合。
[0010]所述的玻纤是经短切的玻璃纤维,长0.5~3 cm。
[0011]所述的铝箔是纯铝箔或覆纸铝箔或覆玻璃纤维布铝箔。
[0012]本发明的积极效果在于:
本发明以动态法为基础,①大幅度降低硅质原料的粒度,提高其反应活性;②通过挑选完全烧透的活性较低的石灰或由此生产的氢氧化钙粉或/和电石渣粉并适当陈化,降低钙质原料的反应活性,使两种原料的反应活性相匹配,从而使生成的组成合成料二次粒子的一次粒子更加细长,减小材料孔径,增大热阻,从而大幅度降低导热系数。同时,为了增强绝热效果,并使板材具有表面防水功效,在外包覆一层铝箔。
[0013]通过大幅度降低低活性硅质原料的粒度、提高其反应活性,选取较低沉降值(即较低活性)的钙质原料或通过工程措施降低高活性钙质原料的沉降值,使两种原料的反应活性相匹配,从而使生成的组成合成料二次粒子的一次粒子更加细长,毛栗状二次粒子缠绕搭接更加牢固,①二次粒子较大,利于沉淀和滤水,压型正常,烘干时板材收缩极小,没有变形微观结构中材料孔径大幅度减小,热阻增大。
[0014]所述的钙质原料是钙石灰或由钙石灰转化而来的氢氧化钙粉或电石渣粉,其沉降值要在25(T300 ml之间。若沉降值小于250 ml,制得的合成料中的一次粒子相对粗、短,合成料显微孔径粗大,板材密度较大,得到的硬硅钙石绝热板绝热效果不佳;若沉降值大于300 ml,制得的合成料中的一次粒子和二次粒子都细小,不易沉淀和滤水,压型困难,且干燥过程中板材极易收缩、变形,难以得到平整的硬硅钙石绝热板。
[0015]根据晶体生长相关理论,原材料越细,组成合成料二次粒子的一次粒子就越细长,在板材气孔率和密度不变的情况下,其孔径就小,上述不利因素就得以抑制,当孔径小到300 nm以下,特别是60 nm以下,就达到了纳米范畴,气体分子被凝结,气体传热大大减少,反映在材料的宏观性能上,其绝热效果显著提高。
[0016]采用本发明制作的高效节能型硬硅钙石绝热板,孔径分布范围为6(T300 nm,大多数孔径在100~200 nm,具有优异的绝热效果。平均温度400°C时的导热系数约为0.07 W/(m.K),比普通硅酸钙板的约0.1Off/ (m.K)低约30 %。
[0017]采用本发明制作的高效节能型硬硅钙石绝热板,属无机材料,耐热温度高,长期使用物理化学性能稳定,能很好地满足水泥窑、电解铝槽及其它工业窑炉对材料性能的需要。
[0018]采用本发明制作的高效节能型硬硅钙石绝热板,包覆有铝箔,铝箔有隔潮防水、反射热量的功效。制品在运输、施工和使用过程中,能够隔潮防水,在打耐火浇注料时,不用再做防水处理,简化了施工,节省了防水材料,消除了防水材料及其包装物对环境的污染。其次,铝箔具有反射辐射传热-隔绝气体窜流减少传热的功效,经测试,随温度不同,其导热系数比没覆铝箔的板材降低疒20 %。同时,真空吸附铝箔的板材,由于材料内有一定的真空度,可以减少空气传热,增强板材的绝热效果。另外,包覆铝箔的板材品相美观,机械强度有所增加。
[0019]图1是本发明实施例二所得到的密度为0.33 g/cm3的硬硅钙石绝热板的孔径尺寸分布。
[0020]图2是本发明实施例一的合成料显微镜下状态图。
[0021]图3是本发明实施例二的合成料显微镜下状态图。
[0022]图4是本发明对比例一的合成料显微镜下状态图。
[0023]图5是本发明对比例二的合成料显微镜下状态图。
[0024]下面结合实施例对本发明作进一步说明。
[0025]实施例一
(I)、将硅砂、硅质球石和水按重量比1:2:0.8的比例加到磨机内,磨细至D5tl = 5.0μ m,放磨得磨细硅粉 。
[0026](2)、将生石灰加到5倍重的75°C水中,搅拌消化,过筛出渣,静置,除上部多余的水,搅匀,得固体物含量为26 %的石灰乳。对生石灰的要求是所制备石灰乳的沉降值为250~300 ml ο
[0027](3)、将磨细硅粉与石灰乳按干料重46.3:53.7的比例配料,此时Ca/Si摩尔比为
0.90,混合均匀,制备成固体物含量在20-40 %之间的入釜料。如入釜料固含量过高应加水调整。
[0028](4)、将上述入釜料注入带搅拌的合成釜内并加水至水/固重量比30。通蒸汽加热,至釜内压力1.2 MPa开始保温,保温6小时。之后降温至常压,即得合成料浆,合成料浆显微镜下状态见图2。通汽加热过程中每隔5分钟搅拌5分钟,保温过程中每隔30分钟搅拌30秒钟,转速为133转/分。
[0029](5)、在上述合成料浆中添加3 %天然纤维纸浆和3 %的玻纤,混匀,在带滤水孔的模具内压制成型,烘干即是高效节能硬硅钙石绝热原板。料浆滤水、成型性和板材烘干过程中尺寸收缩情况见表1。
[0030](6)、在上述高效节能硬硅钙石绝热原板外部均匀涂刷一层白乳胶,紧接着整体覆上纯铝箔,待胶凝固后即得高效节能型硬硅钙石绝热板。板材性能见表2。
[0031]实施例二
(I)、将D5tl = 36 μ m娃粉磨细至D5tl = 3.0 μ m,放磨得磨细娃粉。
[0032](2)、将磨细硅粉与沉降值为25(T300 ml的氢氧化钙粉钙质原料按干料重
42.5:57.5的比例配料,此时Ca/Si摩尔比为1.05,混合均匀,制备成固体物含量在20-40 %之间的入釜料。如入釜料固含量过高应加水调整。
[0033](3)、将上述入釜料注入合成釜内并加水至水/固重量比12。通蒸汽加热,至釜内压力2.0 MPa开始保温,保温3小时。之后降温至常压,即得合成料浆,合成料浆显微镜下状态见图3。合成搅拌工艺与实施例一相同。
[0034](4)、在上述合成料浆中添加3 %天然纤维纸浆和3 %的玻纤,混匀,在带滤水孔的模具内压制成型,烘干即是高效节能硬硅钙石绝热原板。料浆滤水、成型性和板材烘干过程中尺寸收缩情况见表1。
[0035](5)在上述高效节能硬硅钙石绝热原板套进铝箔袋内,封口,抽真空,即得高效节能型硬硅钙石绝热板。板材性能见表2。
[0036]对比例一
(I)、将硅砂磨细至D5tl = 9.8 μ m,放磨得磨细硅粉。
[0037](2)、将磨细硅粉与沉降值为25(T300ml的氢氧化钙粉钙质原料按干料重
43.7:56.3的比例配料,此时Ca/Si摩尔比为1.0,混合均匀,制备成固体物含量在20-40 %之间即为入釜料。
[0038](3)、将上述入釜料注入合成釜内并加水至水/固重量比10。通蒸汽加热,至釜内压力2.0 MPa开始保温,保温4小时。之后降温至常压,即得合成料浆,合成料浆显微镜下状态见图4。合成搅拌工艺与实施例一相同。
[0039](4)、在上述合成料浆中添加3 %天然纤维竹浆和3 %的玻纤,混匀,在带滤水孔的模具内压制成型,烘干即是高效节能硬硅钙石绝热原板,不包覆铝箔。料浆滤水、成型性和板材烘干过程中尺寸收缩情况见表1,板材性能见表2。
[0040]对比例二
(I)、将硅粉磨细至D5tl = 5.3 μ m,放磨得磨细硅粉。
[0041](2)、将沉降值为320 ml生石灰加入到5倍重的75°C水中,搅拌消化,过筛出渣,不经过陈化直接使用,除上部多余的水,搅匀,得固体物含量为19 %的石灰乳。
[0042](3)、将磨细硅粉与石灰乳按干料重41.4:58.6的比例配料,此时Ca/Si摩尔比为
1.1,混合均匀,制备成固体物含量在20-40 %之间,即为入釜料。
[0043](4)、将上述入釜料注入合成釜内并加水至水/固重量比19。通蒸汽加热,至釜内压力2.0 MPa开始保温,保温3小时。之后降温至常压,即得合成料浆,合成料浆显微镜下状态见图5。合成搅拌工艺与实施例一相同。
[0044](5)、以下工序除了包覆的铝箔是覆玻纤布铝箔外,其它完全与实施例一相同。
[0045]各实施例的料浆滤水、成型性和板材烘干过程中尺寸收缩情况见表1,板材性能见表2。合成料显微镜下状态图分别见图2~图5。
[0046]表1
一种高效节能型硬硅钙石绝热制品的制造方法
- 专利详情
- 全文pdf
- 权力要求
- 说明书
- 法律状态
查看更多专利详情
下载专利文献
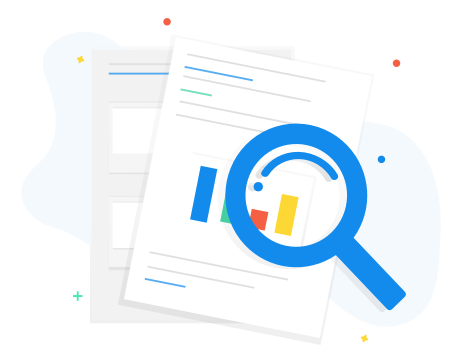
下载专利
同类推荐
-
孙祥云孙祥云杨志杰杨志杰常江, 吴成铁倪刚, 李之瑞
您可能感兴趣的专利
-
吕佩师吕佩师阿布都艾则孜·阿布来提, 艾力江·如苏力翟传伟, 李壮贤翟传伟, 李壮贤翟传伟, 李壮贤翟传伟, 李壮贤
专利相关信息
-
翟传伟, 李壮贤翟传伟, 李壮贤翟传伟, 李壮贤翟传伟, 李壮贤S·W·卡森S·W·卡森