专利名称:用于从烃进料中脱除钙和钠的分段催化剂体系的制作方法本发明涉及适用于从烃进料中脱除钙和钠地、包括至少二个催化剂段的催化剂体系和应用此体系的方法。更具体地说,该催化剂体系的第一催化剂段有效地脱除存在于烃进料中的钙和不溶于油的钠,而第二催化剂段则有效地脱除存在于烃进料中的油溶性有机钠,以保护其他催化剂。使用此催化剂系统的方法包括使含钙和钠的烃进料在加氢脱金属条件下通过催化剂体系。大多数量质原油都含有相当量的有机金属(如镍和钒)化合物。其中,有些是以不溶性盐的形式存在的,可用一般的过滤和脱盐的方法脱除,然而大部分是以有机金属化合物形式存在的,不能脱除,并继续留在催化剂床层上。它们沉积在催化剂颗粒的外表面的紧下面,给炼制带来许多问题。其结果是堵塞催化剂的孔道和使催化剂失活。人们提出了从石油进料中脱除油溶性镍和钒有机金属化合物的各种方法。一种方法是经常更换中毒的催化剂,但这很浪费,使催化剂不能得到充分的利用,成本昂贵。近年来,炼油工作者研制了多种加氢脱金属(HDM)催化剂,以保护活性更高的加氢脱硫、加氢脱氮或加氢裂化催化剂。一般在含污染物的进料通过催化剂床层与活性催化剂接触之前前,先使其与HDM催化剂接触,使金属沉积,尤其是采用具有不同孔径大小、载体组成和金属含量的不同催化剂的分段催化剂的复杂方法,可以得到比使用单一催化剂的方法更为有效的结果。大多数分段方法都需要使烃进料先与具有金属容量的大孔催化剂接触,再与小孔催化剂和更多的催化金属接触,以脱除硫和其它有机金属属。这样含污染物的进料先与低活性的催化剂接触,因而能够使进料在金属沉积之前更完全地透入催化剂。当含污染物较少的原料继续通过催化剂床层时,它与可促使硫和其它有机金属沉积的较高活性的催化剂接触。因此,对于含有可透入催化剂内部的金属(如镍和钒)的任何进料,都会有一种理想的催化剂分段,这种分段可使这些催化剂在反应器顶部到底部都得到最有效的利用。当石油进料中含铁时,遇到更为复杂的问题。这种铁或以油溶性有机金属化合物的形式存在,或以无机化合物(例如硫化铁或氧化铁)的形式存在。与靠近催化剂颗粒外表面沉积的镍和钒相反,它优先沉积在催化剂颗粒之间的间隙即空隙体积中,特别是沉积在加氢催化剂床层顶部的空隙体积中。其结果通过床层的压降急剧增大并使反应器堵塞。一般说来,解决油溶性和不溶于油的铁在催化剂颗粒外层沉积的问题的方法有两种。一种方法对这两种铁都是有些效果的,它是控制用于每单位空隙体积的特定尺寸催化剂的数量。目的是使催化剂床层中的催化剂颗粒逐渐变小,以使床层的沿油流方向的空隙体积逐渐减小。这样可使床层上部比床层下部具有更多的空隙体积供铁沉淀。虽然整个床层可以使用相同组成的加氢催化剂,但是从床层的顶部到底部催化剂颗粒的大小和形状是不同的,这是为了使沿油流通过床层的垂直方向的空隙体积逐渐下降。另一旨在解决油溶性有机铁的沉积问题的方法是变化存在于通过催化剂床层方向的活性加氢催化剂的量。其目的是通过变化催化剂结晶结构的组成,以使沿进料流方向的整个床层的加氢催化活性提高。例如,前面几段的催化剂的催化金属含量比其后诸段的小。通过逐段逐渐提高催化剂活性,可使铁沉淀的分布遍及整个床层。这可将局部空隙体积的损失降到最小,因而可减少压降。以前从事这方面工作的科技人员曾公开过用于脱金属和脱硫的其它分段催化剂体系。例如,Bridge的美国专利第3,663,434号公开了在脱硫催化剂床层之前采用一分段催化剂床层,先脱金属然后再脱硫。Bridge的美国专利第3,696,027号还公开了采用含有分段催化剂床层的催化剂体系脱金属和脱硫的方法。床层的分段情况依次为含大孔度较高的催化剂颗粒床层、大孔度低的催化剂颗粒床层、加氢活性低的催化剂颗粒床层和加氢活性高的催化剂颗粒床层。因此,“分段”这个术语用于本技术,这里是指由具有不同的金属容量和加氢活性的不同类型催化剂颗粒所组成的特殊HDM催化剂床层,其目的是使整个催化剂体系沿进料流的方向逐渐变化。例如一个特定床层可以包括几种在物理性质和化学组成上不同的催化剂颗粒。此外外,我们用“金属容量”这词表示在标准条件下催化剂能够保留的金属量。“大孔”这个术语用于本技术,这里是指催化剂颗粒中直径约大于1000
的孔,或开口,或孔道。这类孔的形状一般是不规则的,孔径仅仅用来表示孔的开口大小的近似值。中孔这个术语用于本技术,这里是指开口直径小于1000
的孔。不过,中孔的直径通常是在40
到400
的范围内。
通用的脱除镍、钒和铁的方法,一般是沿进料流通过分段床层的方向大孔度逐渐下降,中孔度逐渐升高。早期的工作者发现,大孔度与催化剂颗粒的金属容量(保留从含镍、钒和铁污染物的烃进料中脱除出来的金属的能力)有密切关系。在靠后的诸催化剂段中,最好主要是中孔催化剂。业已发现,这些催化剂与表面积较小的且基本上是大孔结构的催化剂相比,加氢催化活性要高得多。因此,在分段催化剂系统中可以利用上述两种现象,以便有效地脱除重质进料中的镍、钒和铁。
当钙和钠之类的金属存在于烃进料中时,进一步增加问题的复杂性性。这些金属以各种形式存在。典型的情况是以金属氧化物、硫化物、硫酸盐或氯化物(表现为这类金属的盐)的形式存在。但它们也可能以油溶性有机金属化合物(包括环烷酸金属盐)的形式存在。本发明特别涉及此最复杂的金属污染物问题。
通用的脱盐技术容易鉴别和脱除不溶于油的金属钙盐和钠盐,如果不脱除它们,那末它们就会沉积在间隙内,并迅速形成压降。但我们对可溶性有机金属化合物知道得还不十分清楚,我们不能通过一般的方法脱除这类钙和钠的化合物。况且,上述那些催化剂体系虽然对脱除铁、镍和钒来说是有效的并不能控制油溶性钙和钠沉淀的有害影响。
我们曾发现,钙一般是优先沉淀在催化剂颗粒之间的空隙体积中,从而使通过床层的压降大增,使反应器的效率大大降低。此外,我们还发现,钠的性质不同于迄今所遇到的任何其它金属这是令人惊奇的。特别是钠会深入催化剂颗粒。这样,钙沉积物使通过催化剂床层的压降增大,而钠的作用则是封闭催化剂颗粒内的活性部位,并使催化剂减活。我们工作的结果使人们清楚地看到不可能用一般的分段体系有效地从含有钙和钠的油中脱除这两种金属。因此我们必须设计一种能有效地从含烃进料中脱除钙和钠的分段催化剂体系,设计时应考虑到诸如催化剂颗粒的形状、大小、孔隙度和表面活性之类的因素。因此,本发明的目的就是提供这样一种体系。
本发明涉及一种能从含有至少1ppm钙和1ppm钠的烃进料中脱除钙和钠的分段催化剂体系。该体系包括至少两个催化剂段,其特征是沿进料流通过分段催化剂体系的方向的孔隙度逐渐减少,活性逐渐提高,表面积与体积之比逐渐增大。
本发明公开了一种采用分段催化剂体系使含钙和钠化合物的烃原料加氢脱金属并减少压降和催化剂减活程度的方法。此方法包括在有氢气的情况下,使进料在加氢脱金属条件下通过第一和第二催化剂颗粒段。
此外,本发明还公开了一种选择分段催化剂体系所用催化剂的方法,该方法包括五个步骤
(a)测定以油溶性化合物形式存在于烃进料中的钙和钠的量。
(b)用微探针分析法评定上述油溶性钙和钠化合物的反应性;
(c)根据上述钙的评定结果,确定在规定的温度、压力和空间速度条件下达到所要求的脱钙率所须采用的催化剂的孔隙度、表面活性、形状和大小;
(d)根据钠的评定结果,确定在所规定的温度、压力和空间速度条件下达到所要求的脱钠率所须采用的催化剂的孔隙度、表面活性、形状和大小;
(e)研制一种兼有步骤(c)和(d)中所确定的各种参数的分段催化剂体系。
图1表示典型的第二段催化剂的徽探针的外形图。
图2、3和4表示典型第一和第二段催化剂的钙和钠边缘扫描图。
本发明的方法是使烃进料在加氢脱金属条件下与包括至少两个催化剂段的催化剂体系接触。催化剂体系的第一段能有效地脱除存在于烃进料中的钙和不溶于油的钠,而第二催化剂段则能有效地脱除油溶性钠。
进料
本发明的进料可以是含有溶于其中的钙和钠的任何烃进料。一般还含有相当量的镍、钒和铁。它们是含有1ppm以上的钙和1ppm以上钠的那些进料,最好是含有3ppm以上的钙和钠。它们一般含有20ppm以上的其它金属,例如镍、钒和铁。此外,它们一般含有1.0%(重量)以上的硫,而且常常超过2.0%(重量)。适用于本发明的进料可以是原油、拔头原油、常压或减压渣油和合成原料方法所产生的液体,如由煤、油砂和油页岩产生的液体。例如,我们试验了由中华人民共和国取得的、经过二次脱盐的胜利2号原油减压渣油。该减压渣油含36ppm左右的钙,10ppm左右的钠,54ppm左右的镍、钒和铁。
催化剂
本发明的加氢脱金属催化剂体系包括至少两个不同的催化剂段。但是最好是采用两个以上的催化剂段。各段可以有一层或多层催化剂颗粒。分段是这样进行的,即是使待加氢处理的进料,在有一系列孔隙度逐渐下降、活性逐渐提高和表面积与体积之比逐渐增大的HDM催化剂存在下与氢气接触。
对于二段体系,第一段脱除烃进料中的钙和不溶于油的钠,第二段脱除油溶性有机钠。对于含有特定量的钙和钠的原料,我们必须仔细选择诸如催化剂的孔隙度、表面活性、形状和大小之类的参数,以得到所要求的催化剂活性分段。
我们能够沿进料流的方向降低诸催化剂段中的空隙度,以实现催化剂分段。前面的诸段最好是孔较大的催化剂,因为污染金属沉积在催化剂表面,过一定时间会堵塞催化剂孔。较大的孔便于烃进料扩散到催化剂的内部。但是,一般说来,我们使活性表面积减少,其结果是催化剂活性中心减少。
我们用水银孔度计测定催化剂颗粒内的孔径分布。压汞技术是根据孔越小、将水银压入孔中所需的水银压力越大这一原理。因此,如果我们将抽去了空气的样品放置在水银中,然后逐渐提高压力并记录下每提高一次压力时所减少的水银体积,那末我们就能确定孔径分布。压力与水银在压力下通过最小孔的孔径之间的关系如下式所示
γ=-2σCOS θ/ρ
式中
γ=孔半径,
σ=表面张力,
θ=接触角,
ρ=压力。
所用的压力高达60,000磅/平方英寸(表压),接触角为140°时,孔直径在35~10,000
的范围内。
在本发明的一个二段体系的实施方案中,第一段催化剂的特点是其孔体积分布为直径大于1000
的孔至少占孔体积的10%(较好是至少15%,最好是20%);表面积在约50平方米/克到约200平方米/克的范围内,较好是在约80平方米/克到约150平方米/克,最好为约100平方米/克到约130平方米/克。第二段催化剂的特点是其孔体积分布为直径大于1000
的孔占体积的30%以下,较好是20%以下,最好是10%以下;中孔平均直径在约80
到约400
的范围内,较好是约100
到约300
,最好是约180
到250
;表面积在约80平方米/克到约300平方米/克的范围内,较好为约100平方米/克到约200平方米/克,最好为约100平方米/克到约120平方米/克。
此外,还可以改变催化剂段的表面活性使催化剂的活性逐渐提高,其做法是改变加在所用催化剂载体上的催化剂金属的类型和数量。催化金属可以是周期表中的ⅥB族或Ⅷ族金属〔根据纯化学和应用化学国际协会的1970年规定(1970 Rule of the International Union of Pure & Applied Chemistry)〕。尤其宜选用Ⅷ族金属中的钴和镍以及ⅥB族金属中的钼和钨。上述金属可以单独使用或组合使用(例如,钴-钼、钴-钨或镍-钼)。
本发明的一个二段体系实施例方案中,第一段催化剂的特点是,浸渍在载体上的Ⅷ族金属量低于3.5%(重量),较好是低于3.0%(重量),最好是低于2.5%(重量);ⅥB族金属的量低于8.0%(重量),较好为低于6.0%(重量),最好为低于4.0%(重量)。
第二段催化剂的特点是,Ⅷ族金属的含量为至少0.7%(重量),较好为至少1.0%(重量),最好为至少1.3%(重量);ⅥB族金属的含量为至少3.0%(重量),较好为至少4.0%(重量)和最好至少为6.0%(重量)。
催化剂颗粒的形状和大小同样对催化剂活性有影响。尺寸较大的颗粒会抑制金属透入并降低外表面积与催化剂体积之比。但它们会因加大HDM床层中的空隙而减少压降。催化剂颗粒的形状也会影响压降、金属透入、外表面积与催化剂体积之比和床层空隙度。
用于第一段的催化剂的制备
制备本发明的典型的第一段催化剂时用氧化铝作载体。这种氧化铝可用任何通用的方法来制备。例如,制备本发明氧化铝载体的详细说明请见Laine等的美国专利第4,392,987号(公布日期1983年7月12日)和Sanchez等的美国专利第4,179,408号(公布日期1979年12月18日)。本发明引用此两专利作为参考材料。
此后,可以通过任何适用的方法,特别是催化制备技术中常用的浸渍法,将典型的第一段催化剂所需的催化组分(Catalytic agent)加入氧化铝载体。适用于本发明的催化组分有ⅥB金属(尤其是钼和钨)和Ⅷ族金属(尤其是钴和镍)。
催化组分的量(按纯金属计)必须在组合物的约2%(重量)到约11%(重量)的范围内。上述金属可以以化合物形式(例如,氧化物或硫化物),也可以以元素的形式存在于最终的催化剂中。
关于将催化组分加入氧化铝载体情况的详细说明请见Tamm的美国专利第4,341,625号(公布日期1982年7月27日)、第4,113,661号(公布日期1978年9月12日)和第4,066,574号(公布日期1978年1月3日)。本发明引用这些专利作为参考材料。
用于第二段的催化剂的制备
制备本发明的典型的第二段催化剂时也是用氧化铝作载体。例如,关于适用于此类催化剂的载体的详情参见Tamm的美国专利第4,113,661号。本发明引用此专利作为参考材料。
此后,可以通过任一适用的方法,特别是通过催化剂制备技术中常用的浸渍法,将此类催化剂所需要的催化组分加入氧化铝载体内。ⅥB族金属(特别是钼和钨)和Ⅷ族金属(特别是钴和镍)都是适用于本发明的催化组分。
催化组分量(按纯金属计)应在组合物的约4%到约11%(重量)的范围内。催化组分可以以化合物的形式(例如,氧化物或硫化物),也可以以元素的形式存在于最终的催化剂中。
分段法
在本发明方法中,必须分成几个催化剂段,以便在有一系列活性较高的加氢处理催化剂存在的情况下使要进行加氢处理的进料与氢气接触。最好是按上述的空隙度、表面活性、形状或大小等参数中的一个或几个参数分段,以得到所需要的催化剂活性。至少必须分为二个催化剂段,但最好是多于二个。例如,可以将高活性催化剂与低活性催化剂混合以建立一个中等活性的中间段。在该方案中,第一段产生与第二段催化剂接触的第一物流,第二段产生与第三段催化剂接触的第二物流,第三段产生脱金属物流。此外,此体系还可以(不是必须的)包括脱硫催化剂段,使脱金属物流与脱硫催化剂接触。
加氢脱金属条件
第一和第二催化剂段按固定床操作。使二个催化剂段在一反应器中流通。在两个段之间不需要任何其它含ⅥB族或Ⅷ族金属的催化材料。例如,它们可以是不分开的或仅被多孔载体材料或反应器内部设施分开。不过最好是在床层之间填有廉价的载体催化剂,例如,浸渍了占总金属量10%(重量)以下的金属的氧化铝。
第一和第二段的加氢脱金属条件可以是相同的或不同的。对于特别重的进料,第一段的加氢条件应该苛刻一些。一般说来,加氢脱金属条件包括温度,在约500°F到约900°F的范围内,较好是约600°F到约800°F,最好是约650°F到约770°F;总压在约1000磅/平方英寸(表压)到约3500磅/平方英寸(表压)的范围内,较好是约1200磅/平方英寸到3000磅/平方英寸(表压),最好是约1600磅/平方英寸(表压)到约2800磅/平方英寸(表压);氢分压在约800磅/平方英寸(表压)到约2800磅/平方英寸(表压)的范围内,较好是约1000磅/平方英寸(表压)到约2500磅/平方英寸(表压),最好是约1500磅/平方英寸(表压)到2200磅/平方英寸(表压);空间速度,在约0.1到约3.0的范围内,较好是约0.3到约2.0,最好是约0.5到约1.7。
下面列举本发明实施例。列举实施例的意图是为了说明本发明的有代表性的实施方案和在实验室所得的分析结果。熟悉此技术的人员可以理解,本发明的其它实施方案能够在不背离本发明的主要特点的情况下取得相同的结果。
实施例
在下而介绍的试验中,使用了三种催化剂,称之为催化剂A、B和C。
催化剂A中直径大于1000
的大孔占催化剂孔体积的40%;催化剂A的表面积为150平方米/克。此外还含有2.0%(重量)的镍。催化剂颗粒为直径为1/16英寸的小球。
催化剂B中直径大于1000
的大孔占催化剂孔体积的40%催化剂B的表面积为150平方米/克。此外,还含有1.0%(重量)的钴和3.0%(重量)的钼。催化剂颗粒为直径为1/16英寸的小球。
催化剂C的中孔平均直径为210
;平均表面积为120平方米/克。此外,还含有1.5%(重量)的钴和6.5%(重量)的钼。催化剂颗粒为直径为1/32英寸的园柱体。
我们对催化剂A、B和C进行试验的目的,是为了确定需要用哪些催化剂和用多少量来组成分段催化剂体系,以用于从烃进料中脱除钙和钠。
第一步是测定特定进料中以油溶性化合物形式存在的钙和钠的量。我们选用由中华人民共和国获得的、经二次脱盐的胜利2号原油减压渣油作分析。采用常规方法测定了原料的性质,所得结果概括于表1中。特别是所测得的钙含量为26ppm,钠含量为10ppm。
表1
用于试验的减压渣油馏分
>538℃(>1000°F)液体;%(体积) 100
硫,%(重量) 3.0
氮,%(重量) 0.88
MCRT,%(重量) 18.3
沥青质(热庚烷不溶物),%(重量) 6.5
粘度,100℃,厘沲 3270
金属,ppm
Ni/V 36.0/5.1
Fe 27.1
Ca 41.7
Na 10.1
然后是建立一个催化剂固定床层。该催化剂固定床层由10cc催化剂A、10cc催化剂B和10cc催化剂C组成。然后,在有氢气的情况下,使减压渣油在下述反应条件下与催化剂接触。反应条件为液时空速(LHSV)1.68,总压2500磅/平方英寸(表压),氢分压1950磅/平方英寸(表压),5000标准立方英尺/桶760°F。此体系试验了760小时。
试验之后,用徽探针分析法分析用去的催化剂。图1示出了催化剂的区间扫描图。数据表明,钠分布情况良好。催化剂的氯含量低,表明钠沉积物不是氯化钠。因此,钠一定是以油溶性的形式存在,我们发现在所有的金属中,钙的分布最差。
图2、3和4是催化剂A、B和C的钠和钙的边缘扫描比较图。催化剂C的钠沉积量比催化剂A或B的钠沉积量高。这意味着催化剂上的金属对脱钠来说是个重要的参数。催化剂A和B的钙沉积非常相似,比催化剂C深得多。
根据这些结果,可以断定催化剂A和B最适合于脱钙;还可以断定催化剂C既最适合于脱钠,也适用于脱镍和钒。因此分段催化剂体系的第一段用催化剂A和B的混合催化剂脱钙,第二段仅用催化剂C脱钠。
根据上面的分析,我们用催化剂A、B和C组成了一个二段催化剂体系。第一段的体积占体系的67%,由三层催化剂颗粒组成。第一层用的是催化剂A,占30%(体积)。第二层用的是混合催化剂(催化剂A和催化剂B两者的体积比为50∶50),占20%。第三层用的是催化剂B,占17%(体积)。第二段占体系的33%,含一层催化剂C。
第一段一般是大孔的,目的是脱钙和脱除任何其它的一般重金属,例如,铁、钒和镍。第二段一般是非大孔的,目的是既脱钠和脱除任何残余的重金属。
表2
用于第二次试验的减压渣油
>538℃(>1000°F)的液体,%(重量) 81
硫,%(重量) 2.8
氮,%(重量) 0.85
MCRT,%(重量) 16.0
沥青质(热庚烷不溶物),%(重量) 5.7
粘度,100℃,厘沲 1107
金属,ppm
Ni 31
V 4
Fe 22
Ca 58
Na 11
组成此体系之后,在有氢气的情况下,使性质如表2所示的进料与此体系接触。所用的加氢脱金属条件如下液时空速0.54,氢分压2000磅/平方英寸(表压),开始试验温度为750°F。
在上述条件下使原料接触之后,我们发现钙减少70%以上,基本上没有钠以及其它重金属。
提供了一种用于从含有至少1ppm钙和1ppm 钠的烃进料中脱除钙和钠的分段催化剂体系。该体 系包括二个催化剂段。该体系的特征是,在进料流通 过体系的方向孔隙度逐渐降低,活性逐渐提高,表面 积与体积之比逐渐增大。还公开了使用该体系的方 法和选择该体系中所用的催化剂的方法。
用于从烃进料中脱除钙和钠的分段催化剂体系制作方法
- 专利详情
- 全文pdf
- 权力要求
- 说明书
- 法律状态
查看更多专利详情
下载专利文献
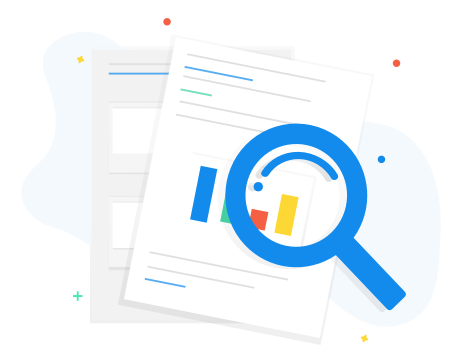
下载专利
同类推荐
-
黄艰生朴淳五M.菲尼
您可能感兴趣的专利
-
M.菲尼M.菲尼黄锡生, 陈冲肖建庄, 林壮斌
专利相关信息
-
常贵, 卢新社楼凤鸣文亮, 衡永志刘德元