专利名称:采用套管法制造光纤预制棒外包层的方法光纤预制棒是制造光纤的原材料。为了保证预制棒的高纯度和拉制后光纤的低损耗,目前光通信领域内预制棒均采用气相沉积法制造。对于目前应用最为广泛的G.652单模光纤,几乎所有的光功率均在芯层和内包层中传输,因此预制棒芯层和内包层(芯层和内包层合在一起称为芯棒)的制造决定了拉制后光纤的光学性能,而预制棒外包层,从成本考虑,可以采用原材料纯度相对较低,工艺相对简单的方法制造。目前预制棒芯棒制造工艺主要有VAD (轴向气相沉积)、OVD (外部气相沉积)、MCVD (改进的化学气相沉积)和PCVD (等离子化学气相沉积),而外包层制造工艺主要有火焰水解法、套管法等。目前预制棒大尺寸化已成为降低成本的有效方法,不仅可以减少多根预制棒的头尾损耗,而且可以增加连续生产时间,提高原材料利用率。国内、外光纤预制棒制造商相继采用大套管制造预制棒外包层。目前套管最大直径可达180-200_,与芯棒组合后单根预制棒拉丝长度达到6000km以上。然而对于剖面结构复杂的光纤制造,如多模光纤、色散补偿光纤等,管内沉积法(MCVD和PCVD)为主流工艺。然而管内沉积法由于受沉积管尺寸的限制,难以直接制造大尺寸光纤预制棒。为了进一步增大光纤预制棒的外径,提高生产效率、降低成本,套管法被认为是初期投入成本小、生产周期短并可充分利用现有设备的最佳选择之一。专利号为US4668263的美国专利公`开了一种套管法制造光纤预制棒外包层的方法,如图1所示。套管4的两端安装在玻璃车床的卡盘7上,套管4的一端与旋转接头8相连。真空泵10通过一个控制阀9连接到旋转接头8上。芯棒I安装在套管4内部的突起部分5。安装好之后,喷灯6在套管4的一端加热,从而使套管4塌缩到芯棒I上。芯棒I和套管4保持同步旋转,喷灯6沿着套管4缓慢移动,使套管4完全塌缩到芯棒I上形成实心的预制棒。在这种方法中,由于车床上的卡盘7夹住套管4的两端,从而使卡盘7两端的套管4无法塌缩到芯棒I上而造成浪费。与上述方法不同的是,专利号为US4596589的美国专利将辅助玻璃棒13的一端焊接到芯棒I上,如图2所示,另一端安装在车床尾座12的卡盘上(图中未示出)。套管4的一端安装在头座11的卡盘上,为了保证芯棒I与套管4相对固定,在套管4的头部圆周上设置了至少三个凹陷部14,从而使芯棒I的一端焊接在套管4的内壁上,套管的凹陷处仍留有间隙15,使套管4塌缩时气体能够顺利的排出,如图3所示。虽然这种方法避免了套管4其中一端材料的浪费,但套管4的另一端被头座11的卡盘夹住,喷灯无法移到该处,塌缩完成后仍需要去除。其次,这种方法在塌缩的最初阶段,由于套管4靠近尾座12的一端与大气连通导致无法抽真空,塌缩较为困难。此外,为了确保制造的光纤预制棒的同心度,塌缩开始时,需要特别注意将套管4和芯棒I的轴线调整成一条直线,并且在塌缩的过程中保持不变。该方法刚开始塌缩时,套管4靠近尾座12的一端处于悬空状态,套管4在高温下软化塌缩到芯棒I上的过程中,容易造成套管4和芯棒I的同心度偏差
本发明要解决的技术问题和提出的技术任务是克服现有套管法制造光纤预制棒外包层存在浪费套管等缺陷,提供一种可充分利用套管的采用套管法制造光纤预制棒外包层的方法。为此,本发明的采用套管法制造光纤预制棒外包层的方法,其具有,其特征是包括以下步骤: 将芯棒焊接到辅助玻璃棒上,在焊接处设置外径增粗部分;将辅助玻璃棒安装在尾座卡盘上;将用以形成外包层的套管一端焊接到把手管上,把手管安装在头座卡盘上并通过旋转接头连接真空泵,所述的尾座卡盘与头座卡盘同心; 将整根芯棒同心地插入到套管内,使芯棒的外表面和套管的内表面之间形成环形间隙,令所述的外径增粗部分封住套管的一端; 用喷灯加热套管焊接把手管的一端形成至少三个凹陷部用以定位固定芯棒临近把手管的一端避免芯棒偏心,凹陷部处留有间隙;用喷灯加热所述的外径增粗部分及套管被封住的一端将套管的该端封闭; 通过所述的真空泵向所述的环形间隙施加持续的负压,通过所述尾座卡盘、头座卡盘带着套管、芯棒转动,轴向移动喷灯加热所述的套管和芯棒令套管塌缩到芯棒上形成实心的光纤预制棒。作为优选技术手段:在改进的化学气相沉积设备上制造光纤预制棒的外包层。所述的芯棒采用管内气相沉积法制造。所述的套管为纯石英玻璃管。所述外径增粗部分的外径不小于套管的内径。所述的环形间隙为0.5-3_。所述套管塌缩到芯棒上时喷灯的温度为1900-2200°C。所述芯棒的长度与所述套管的长度相同。本发明的有益效果是:本发明方法可以充分利用现有的改进化学气相沉积设备,不需要额外的设备投资。与现有技术相比,本发明方法通过芯棒焊接辅助玻璃棒和套管焊接把手管,使整根套管完全塌缩到芯棒上,避免了套管材料的浪费,降低了生产成本。其次,通过对辅助玻璃棒和芯棒连接处的外径增粗部分的设置,套管开始时可以比较容易地塌缩到芯棒上,节省了生产时间。最后,本发明在套管和芯棒的同心度控制上更为简单,从而保证了所制造的光纤预制棒具有较好的几何尺寸。
图1是现有技术套管塌缩到芯棒上的示意 图2是另一种现有技术套管塌缩到芯棒上的示意 图3是本发明把手管与套管焊接后凹陷部的截面放大示意 图4是根据本发明的套管塌缩到芯棒上的示意 图5是套管塌缩到芯棒上之后得到的预制棒的截面示意 图6是根据本发明实施例2芯棒与套管焊接后凹陷部的截面示意 图中标号说明:1-芯棒,2-芯层,3-内包层,4-套管,4’ -外包层,5-突起部分,6-喷灯,71-头座卡盘,72-尾座卡盘,8-旋转接头,9-控制阀,10-真空泵,11-头座,12-尾座,13-辅助玻璃棒,14-凹陷部,15-间隙,16-辐射高温计,17-粉尘收集箱,18-把手管,19-外径增粗部分。
将芯棒焊接到辅助玻璃棒上,在焊接处设置外径增粗部分;将辅助玻璃棒安装在尾座卡盘上;将用以形成外包层的套管一端焊接到把手管上,把手管安装在头座卡盘上并通过旋转接头连接真空泵,所述的尾座卡盘与头座卡盘同心(该段所述步骤为实施本发明方法的准备工作,所述操作在具体实施时可视情形调整先后顺序);
将整根芯棒同心地插入到套管内,使芯棒的外表面和套管的内表面之间形成环形间隙,令所述的外径增粗部分封住套管的一端;
用喷灯加热套管焊接把手管的一端形成至少三个凹陷部用以定位固定芯棒临近把手管的一端避免芯棒偏心,凹陷部处留有间隙;用喷灯加热所述的外径增粗部分及套管被封住的一端将套管的该端封闭(该段步骤所述的形成至少三个凹陷部避免芯棒偏心与加热外径增粗部分及套管被封住的一端将套管的该端封闭在具体实施时可改变顺序);
通过所述的真空泵向所述的环形间隙施加持续的负压,通过所述尾座卡盘、头座卡盘带着套管、芯棒转动,轴向移动喷灯加热所述的套管和芯棒令套管塌缩到芯棒上形成实心的光纤预制棒。具体的:在改进的化学气相沉积设备上制造光纤预制棒的外包层。所述的芯棒采用管内气相沉积法制造。所述的套管 为纯石英玻璃管。所述外径增粗部分的外径不小于套管的内径。所述的环形间隙为0.5-3mm。所述套管塌缩到芯棒上时喷灯的温度为1900_2200°C。所述芯棒的长度与所述套管的长度相同。下面将参照附图详细描述本发明的优选实施方案。改进的化学气相沉积设备如图4所示,车床上的头座11和尾座12分别安装有卡盘7,为了防止沉积和缩棒过程中石英玻璃管变形,两个卡盘7必须同心。车床上装有一个载着氢氧焰喷灯6以恒定速度运动的拖板(图中未示出),并安装有辐射高温计16随喷灯6一起运动。根据来自辐射温度计16的信号控制氢气和氧气的流量,从而能够达到保持加热区的温度的目的。卤化物SiCl4、GeCl4、P0Cl3等蒸汽混合物与高纯O2 —起作为制造石英系玻璃的原料。氢气和氧气被用来加热石英玻璃管。供气系统主要作用是精确地控制上述蒸汽混合物和气体的流速。每个沉积层的卤化物蒸汽混合比应该按程序设定值加以控制,而燃烧气体则是通过来自测量石英玻璃管表面温度的辐射温度计16的信号进行控制。通常用质量流量计控制载流气体的流速,从而达到控制卤化物气体的流量。由于废气中含有SiO2粉尘和氯气,所以在排入大气之前必须除去这些有害物质。通常由粉尘收集箱17清除废气中的SiO2颗粒。废气的流量是由靠近沉积管出气端的压力调节阀来控制的,因此由传感器测量的沉积管压力能保持恒定。芯棒I在改进的化学气相沉积设备上沉积、熔缩完成之后,从尾部拉断。芯棒I含有芯层2和内包层3,并具有特定的折射率剖面。为了控制拉制后光纤的水峰,芯棒I内包层3的直径与芯层2直径比(b/a)控制在2.0以上,优选的在3.0以上,更优选的在4.0以上。芯棒I必须具备较好的平直度,如果弯曲度超过lmm/m,需要进行校直处理。然后将制造好的芯棒I焊接到辅助玻璃棒13上(该步骤可在另一台车床上完成),并在焊接处设置一个外径增粗部分19 (材质为石英玻璃,设置的方法是对焊接处加热,从一端或两端施加一个挤压力,使焊接处增粗),使其外径不小于套管4内径。对芯棒I进行火焰抛光消除表面的杂质;将辅助玻璃棒13安装在车床的尾座卡盘72上。接着,将套管4焊接到把手管18上,把手管18安装在MCVD车床的头座卡盘71上(尾座卡盘与头座卡盘同心),并通过旋转接头8连接到真空泵10。焊接过程中需要确保把手管18和套管4的同心度。套管4在使用前需要进行酸洗处理,并进行火焰抛光。然后,将带有辅助玻璃棒13的芯棒I缓慢向头座11方向移动,使整根芯棒I同心地插入到套管4内部,芯棒I和辅助玻璃棒13的外径增粗部分19封住套管4 一端。芯棒I和套管4的间隙为0.5-3mm,优选为0.5-2mm。引用专利号为US4596589的美国专利的方法,在套管4的头部圆周上设置至少三个凹陷部14,从而使芯棒I的一端焊接在套管4的内壁上,套管4的凹陷处仍留有间隙15,使套管4塌缩时气体能够顺利的排出。利用喷灯6加热外径增粗部分及套管被封住的一端,使其完全闭合。安装完成之后,同步转动尾座卡盘72、头座卡盘71,将喷灯6移到芯棒I和辅助玻璃棒13的连接处对套管4进行加热,温度控制在1900-2200°C。开启连接于旋转接头上8的真空泵10,使套管和芯棒间隙15内处于负压状态。套管4在高温下由于表面张力的作用和负压作用下软化塌缩到芯棒I上。芯棒I的另一端被凹陷部14固定,因此不会由于高温软化而发生耷拉触碰到套管4的内壁上。喷灯6沿着套管4缓慢移动,使套管4完全塌缩到芯棒I上,喷灯6的移动速度为5-20mm/min。增大套管和芯棒间隙15内的负压,可以加快套管4的塌缩。如果套管和芯棒的间隙15过大,可以通过提高喷灯6温度和降低喷灯6移动速度来提高塌缩效率。塌缩完成之后的预制棒截面图如图5所示,预制棒含有芯层2、内包层3和外包层(由套管塌缩形成) 。根据所得预制棒的外包层的直径与芯层2的直径的比值,采用本发明的方法进一步制造预制棒的外包层。最后将套管完成后的预制棒采用常规的方法拉制成光纤。以下通过两个实施例对本发明做具体说明。实施例1:
外径为20mm、长度为IOOOmm的芯棒I由改进的化学气相沉积法制造完成。然后将制造好的芯棒I焊接到辅助玻璃棒13上,并在焊接处设置一个外径增粗部分19,该外径增粗部分19的最大外径为24_。对芯棒I进行火焰抛光消除表面的杂质。经过酸洗处理的套管4的外径为30mm、内径为24mm、长度为1000mm,—端焊接到把手管18上,把手管18安装在头座卡盘71上并通过旋转接头连接真空泵。将辅助玻璃棒13安装在车床的尾座卡盘72上。然后,将整根芯棒I同心地插入到套管4内部直至外径增粗部分封住套管的一端,套管4内壁与芯棒I外径的间隙15为2mm。套管4上与把手管18焊接的一端圆周上设置3个凹陷部14,从而使芯棒I的一端能够焊接在套管4的内壁上,如图3所示。利用喷灯6加热使套管4与芯棒I外径增粗部分19完全闭合。安装完成后,旋转同步卡盘7,转速为45rpm。将喷灯6移到芯棒I和辅助玻璃棒13的连接处进行加热,温度控制在2050°C。开启连接于旋转接头上8的真空泵10,使套管和芯棒间隙15内的压力为-1.5bar。套管4在高温下软化塌缩到芯棒I上。喷灯6沿着套管4向头座11方向缓慢移动,速度为8mm/min,使套管4完全塌缩到芯棒I上。本实施例光纤预制棒拉制成光纤后,其几何尺寸参数符合GB/T12357.1中Ala类多模光纤要求。实施例2
外径为25_、长度为1200mm的芯棒I由等离子化学气相沉积法制造完成。经过酸洗处理的套管4的外径为32mm、内径为27mm、长度为1200mm,—端焊接到把手管18上,把手管安装在头座卡盘上并通过旋转接头连接真空泵。然后将制造好的芯棒I焊接到辅助玻璃棒13上,并在焊接处设置一个外径增粗部分19,该外径增粗部分19的最大外径为30mm。将辅助玻璃棒13安装在车床的尾座卡盘72上,并对芯棒I进行火焰抛光消除表面的杂质。然后,将整根芯棒I同心地插入到套管4内部直至外径增粗部分封住套管的一端,套管4内壁与芯棒I外径的间隙15为1mm。套管4上与把手管18焊接的一端圆周上设置4个凹陷部14,从而使芯棒I的一端能够焊接在套管4的内壁上,如图6所示。利用喷灯6加热使套管4与芯棒I外径增粗部分19完全闭合。安装完成后,旋转同步卡盘7,转速为45rpm。将喷灯6移到芯棒I和辅助玻璃棒13的连接处进行加热,温度控制在2000°C。开启连接于旋转接头上8的真空泵10对套管和芯棒间隙15抽真空,使套管和芯棒间隙15内的压力为-2.5bar。套管4在高温和负压状态下塌缩到芯棒I上。喷灯6沿着套管4向头座11方向缓慢移动,速度为12mm/min,使套管4完全塌缩到芯棒I上。本实施例光纤预制棒拉制成光纤后,其几何尺寸参数符合GB/T 9771.5中B4类单模光纤要求。需要说明的是, 上述实施例的方式仅限于描述实施例,但本发明不只局限于上述方式,且本领域的技术人员据此可在不脱离本发明的范围内方便的进行修饰,因此本发明的范围应包括本发明所揭示的原理和新特征的最大范围。
本发明公开了一种采用套管法制造光纤预制棒外包层的方法,属于光纤制造技术,现有套管法制造光纤预制棒外包层存在浪费套管等缺陷,本发明将芯棒焊接到辅助玻璃棒上,在焊接处设置外径增粗部分,将整根芯棒同心地插入到套管内,使芯棒的外表面和套管的内表面形成环形间隙;套管圆周上设置至少三个凹陷部分固定芯棒;利用喷灯加热封闭套管和芯棒的外径增粗部分,并向环形间隙施加负压;移动喷灯加热套管和芯棒将套管塌缩到芯棒上形成实心的光纤预制棒。套管利用率高;本发明可以充分利用现有的改进化学气相沉积设备,不需要额外的设备投资,可降低生产成本和节省生产时间;本发明方法制造的光纤预制棒具有较好的几何尺寸。
采用套管法制造光纤预制棒外包层的方法
- 专利详情
- 全文pdf
- 权力要求
- 说明书
- 法律状态
查看更多专利详情
下载专利文献
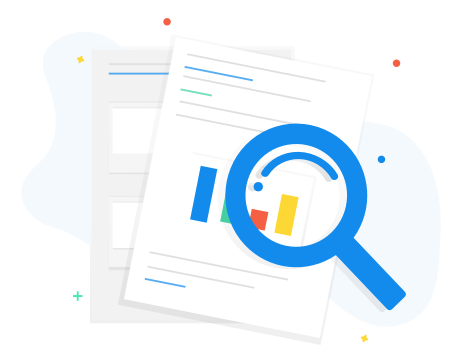
下载专利
同类推荐
-
刘建, 陈超刘建, 陈超刘建, 陈超刘建, 陈超刘建, 陈超刘建, 陈超
您可能感兴趣的专利
-
刘建, 陈超黄靓刁晓翔刘建, 陈超平野正晃
专利相关信息
-
张璐璠吴廷贤罗文勇