专利名称:用于连续浇铸金属锭的模块化铸模系统及方法本发明涉及一种改进的模块铸模系统和方法,用于熔融金属的垂直连续浇铸,如铸铝,以提供凝固的圆形截面铸锭以便进一步加工成金属半制成品。更具体地说,本发明涉及一种铸模装备,它和一种立式的用于铝、镁及其合金的直接急冷浇铸系统的结合使用。对于那些熟悉直接急冷浇铸技术的人员,对下述事实已经熟知即当铸模的长度很短,而且对要求铸造的每个具体的产品的合金,直径和浇涛速度都已精确地协调过,则具有最高的表面质量和内部质量的铸锭是能够浇铸出来的。例如在马库宾(McCubbin)的美国专利4,071,072号中所示。仅仅采用长度很短的其值约为10至40毫米的铸模,应用直接急冷效果就能够用以克服铸锭与铸模之间由于所形成的空气隙(air-gap)所造成的不可避免的损失。有许多新型铸模的设计就是根据上述原理进行的,这些新型铸模同样地都能够使铸锭具有很高的表面和内部质量。但是,所有这些新型铸模的设计,其特点都是结构复杂,采用贵重的材料,必须具有严格的制造公差,因而根据此所能铸造的仅仅是特定的合金和特定的直径的高质量铸锭,为此要求所设计和制造的铸模的使用范围是很窄的。不象在浇铸很大的矩形截面,同时铸件的数量也很少的那样,主要市场的需求是从小到中等直径即由125至250毫米范围的圆截面的铸锭。为了获得高的生产率,必须同时浇铸许多个铸锭,如24至96个。因此,对于一个生产合金的种类和铸锭的直径范围都很宽,而且使用新一代的铸模能够浇铸出很高质量的铸锭的工厂来说,其铸模装备的费用是非常高的。本发明的目的是提供一套简化的铸模系统,该系统能够铸造出很高质量的铸锭同时又可以大幅度地降低铸模装备的成本。本发明在最广义的方面涉及一种用于连续浇铸金属锭的模块化铸模系统。它包括一个空心筒体,该筒体适于安装在一个浇铸台上。一个环形挡水圈可拆卸地安装在上述筒体的下部,该挡水圈具有一个中央开口,成型的金属锭就由此开口通过,挡水圈设有冷却水通道,以便将冷却水由筒体沿径向向内流过,并对着通过中央开口的成型铸锭向内并向下排放。一个环形模体可拆卸地安装在筒体内紧靠在挡水圈的上面,而且该模体具有一个成型空腔,用于形成一个金属铸锭,该成型空腔的直径比挡水圈略小一点。一个用于熔融金属的注入口设置在紧靠在铸模的上方,该注入口带有一个或几个绝热环,可拆卸地安装在筒体内并且其外径要小于筒体的内径。一个压力环可拆卸地安装在筒体内的筒体内表面与绝热环外表面之间的一个环形间隙内。最后,一个盖板用于安装在注入口和压力环的上面,并将盖板紧固在筒体的顶部,以便将铸模系统各个构件压在一起。这样对各构件构成紧密的配合。一个用于向铸模送入润滑油的环形导油板安装在紧靠在模体的上面并与筒体的注油口连在一起。本发明的模块化铸模系统,当生产不同的合金种类和/或铸锭尺寸时仅仅需要更换其中的某些模块化另件,而不要每次都把整个的结构进行更换。这样则根据要生产的铸锭的直径或者合金种类,它可能只需要更换二至三个模块化另件就够了,而不是象现在通常所采用的把整个铸模结构都更换掉。这就对生产许多不同直径和合金种类的铸锭所要求的铸模装备,提供很大的节约。对本发明进行说明的各个附图
图1是本发明的一个实施例的部件分解图;
图2是组装的铸模系统一个实施例的一个剖视图;
图3是本发明的另外一个实施例的一个剖视图;
图4是本发明的其它另外一个实施例的一个剖视图,图2所示一个模块化铸模系统的设计用于铸造一种152毫米直径的铸锭,铸模的长度为20毫米。一个浇铸台根据要铸造的产品的直径的大小可以包括最多达96个单个铸模。由浇铸台底板10和顶板11所支持的是一个空心筒体12,该筒体是内部构件的主要支持结构。这种筒体12借助一个0型圈32以密合保持在浇铸台底板的一个孔内,并借助0型圈30保持在顶板的一个孔内。用螺栓27紧固在顶板11上。
筒体12的底部包含一个向内的凸台13,在其顶部边缘,形成一个环形支持肩部14。支持在支持肩部14上的是一个环形挡水圈15,最好是用钢制成。此挡水圈设置有水通道用于将冷却水由筒体12的进水口17输送到挡水圈的内边缘。在那里将水朝内并向下喷射到从铸锭模中显露出来的成型铸锭上。
紧挨着进水口和挡水圈上面的是一个模体18。模体18内圆筒壁26具有生产所要求的非常高的表面和内部质量的圆截面铸锭合适的结构尺寸。模体18的外圆柱形壁的设计要满足借助0的型圈31在筒体12内进行密配合的要求。水通道16的一部分是由模体18的底端部的一部分和挡水圈的顶端端部的一部分之间的一个间隙形成的。此间隙最好是在铸模内形成若干向上的环形通道,以便通过水对模体进行冷却。
一个环形导油板19紧挨在模体18的上面,而且此导油板在底部端面上具有若干沟槽,以便用于将润滑油通过它流入模体18的内壁26。油液通过筒体12的上部法兰21上的进口20导入。
一个环形压力环22,最好用钢制件,以密合方式安装在筒体内紧挨着导油板19的上面。此压力环22对模体18和挡水圈15施加压力,把它们牢固地夹紧在一起。它包括一个O型密封环34,位于油液进口20的上面,对压力环22和筒体12之间提供牢靠的密封。在O型密封环34的下面向下延伸的是一个环形间隙35,油液由它向下流向导油板19。在压力环22的底端部包括另外一个O型环33,为压力环22和导油板19之间提供密封,由此可以保证油液只能沿着模体18的顶端部流动。紧挨着压力环22的内圆筒壁安装着绝热环23,最好是用陶瓷绝热材料制成。最后,在所有的组装件上面安装有一个盖板24,它是用螺栓25拧在筒体12的法兰21上的。拧紧螺栓25,将上述的铸模组装件的各个构件都牢固地保持在使用状态下的正确的相对关系。为在组装件内提供一定的弹性,将若干高弹性体弹簧28安装在盖板24和压力环22之间的空隙处。这就保证了将一个均匀的压力通过压力环22传递到模体18和挡水圈15上。借助一个可压缩的绝热垫圈29,如Fibrefrax,安装在盖板24和绝热环23之间就可以对组装件提供进一步的弹性。
假如组装件改为铸造一种较大尺寸的铸锭,如具有178毫米直径的,则另件15,18和19就要用另件15a,18a和19a所取代,如图3所示。
可以看出,挡水圈15a具有一个与挡水圈15直径相等的外径,但具有较大的内径。模体18a也具有一个与模体18相等的外径,同时还具有一个比模体18为大的内径,其值为178毫米。导油板19a也具有一个与导油板19相等的外径并具有一个较大的内径。当生产的铸锭直径在152至178毫米之间时,不需要改换压力环22、绝热环23和盖板24。
当合金的成分变更时,既便产品的直径不变也可能需要变更模体的长度。这样,图4显示一个铸模组装件,在该组装件中的模体18b与图3中所示的模体18a的直径相等,但具有较大的长度,其值为40毫米。它需要有一个不同的挡水圈15b,这样使模体18b和挡水圈15b加起来的总长度保持不变。不需要在结构上进行其它更改。
应当懂得,本发明不受上面所具体描述的特点和各实施例的限制,
但在不违背其构思精神情况下可以通过其它途径予以实现。
一种连续浇铸金属锭的模块化铸模系统和方法。系统包括a)安装在浇铸台上的空心筒体,b)装在筒体内的环形挡水圈,有中央开口,成型铸锭由此通过,并设有冷却水道,对成型铸锭排放冷却水,c)装在筒体内紧靠在挡水圈上面的环形模体,d)熔融金属注入口,包括绝热环,装在筒体内紧靠在模体上面,e)装在筒体内的压力环,f)把铸模系统压缩在一起的盖板。这些环形元件可根据待浇铸的铸锭直径和金属成分的要求,更换元件内径或长度。
用于连续浇铸金属锭的模块化铸模系统及方法
- 专利详情
- 全文pdf
- 权力要求
- 说明书
- 法律状态
查看更多专利详情
下载专利文献
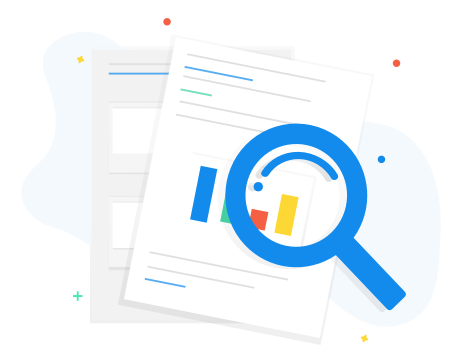
下载专利
同类推荐
-
尼尔·B·布赖森牛茂C·S·马德杨成锐
您可能感兴趣的专利
-
计苓, 杨健拉里R·希戴拉, 拉里R 希戴拉朴淳五周泽良M.菲尼
专利相关信息
-
拉尔夫·埃贡·凯塞, 贝亚特·马泰斯J·F·香利J·F·香利冯春燕