高强螺栓摩擦型连接结构及其连接节点性能优化方法 [0002] 目前建筑钢结构中,高强螺栓摩擦型连接节点是最为常见的栓接节点形式之一。 一般情况下,高强螺栓摩擦型连接节点的连接处构件接触面有四种不同处理方法,对应的 抗滑移系数也不同,但整体都偏小。因为抗滑移系数不高,所以目前使用的高强螺栓摩擦型 连接节点的抗剪承载力也不高,满足不了部分特殊工程的要求。并且,这些连接节点防腐蚀 性能差,连接构件接触面容易发生腐蚀,接触面一旦发生腐蚀,连接节点承载性能将急剧下 滑。所以在建筑钢结构竣工后,仍然需要长年定期维修与保养,造成很大浪费。
[0003] 本发明要解决的问题在于提供一种提高高强螺栓摩擦型连接节点抗剪承载力和 防腐蚀性能的优化方法,旨在解决抗剪承载力不足、防腐蚀性能差,而且需要长年维修养 护,造成浪费等的缺陷。 [0004] 本发明的目的是这样实现的:一种高强螺栓摩擦型连接结构,包括若干钢梁和连 接盖板,所述连接盖板的外表面设有喷铝层,所述连接盖板通过螺栓分别固设于若干对接 的钢梁上,所述钢梁的连接处设有喷漆层,所述连接盖板覆盖于所述喷漆层上。 [0005] 进一步地,所述钢梁为工字型钢,其数量为两根,所述连接盖板固设于所述两根工 字型钢的腹板上。 [0006] 进一步地,所述连接盖板的数量为两块,其分别固设于所述若干对接钢梁的连接 处两侧。
[0007] 上述高强螺栓摩擦型连接结构的连接节点性能优化方法,包括以下工艺步骤:首 先,在若干待连接钢梁的连接处喷涂漆层、在连接盖板的外表面上喷涂铝层;然后,将所述 连接盖板通过高强螺栓固设于若干对接的钢梁的连接处。
[0008] 进一步地,所述若干待连接钢梁的连接处先进行喷砂或喷丸工艺处理后,再喷涂 漆层。
[0009] 进一步地,所述漆层为无机富锌漆层。
[0010] 进一步地,所述连接盖板的外表面先进行喷砂或喷丸工艺处理后,再进行喷涂铝 层。
[0011] 进一步地,所述喷铝工艺采用线材火焰喷涂,采用氧-乙炔焰作为热源,铝线材作 为嗔涂材料。
[0012] 进一步地,喷铝层b分3?4道完成,每层喷铝层b厚度均匀,前一层与后一层进 行90°或45°交叉喷涂。
[0013] 本发明的有益效果是:与现有技术相比,该高强螺栓摩擦型连接节点的性能优化 方法在腹板的连接处喷涂漆层,连接盖板的外表面喷涂铝层,连接盖板通过高强螺栓分别 固设于若干对接的钢梁上,具有以下的技术效果:
[0014] 1、连接盖板与待连接的钢梁的接触面分别为喷漆层和喷铝层,喷漆层和喷铝层形 成的摩擦面具有较高的摩擦系数和抗滑移系数,从而增加了连接盖板与待连接的钢梁的摩 擦系数和抗滑移系数,从而提高了连接节点的抗剪承载力。
[0015] 2、热喷涂铝对钢铁基体有双重保护作用。一方面,可以像涂料那样(尤其是经过 封闭处理的涂层)起着物理覆盖作用,将钢铁与水和空气等腐蚀介质隔离开来,从而起到 防护作用。另一方面,由于铝的电化学性能比较活泼,电极电位比铁低,在这个腐蚀电池中, 铝是负极,铁则为正极,铝失去电子,变成离子进入电介质溶液中而被腐蚀,其自由电子流 向钢铁,使钢铁极化而受到保护。因此,使连接节点具有较强的整体耐腐蚀性。
[0016] 3、由于喷涂时铝呈熔融液滴喷射到经过糙化处理的钢铁表面上,熔滴有较大的热 能,获得比有机涂料层更牢固的结合强度,而且铝是一种活性很强的金属,很容易与氧结 合,生成一层致密、坚硬的氧化保护层,有效地防止铝涂层进一步氧化,具有更长的保护周 期,不需要长年维修保养,避免了人工成本浪费。
[0017] 图1是本发明高强螺栓摩擦型连接结构的立面示意图;
[0018] 图2是沿图1中A-A线的剖视示意图;
[0019] 图3是沿图1中B-B线的剖视示意图;
[0020] 图4是图1中C部分的局部放大示意图。
[0021] 如图1至图4所示,是本发明中高强螺栓摩擦型连接结构的一较佳实施例,该高强 螺栓摩擦型连接结构包括若干钢梁2和连接盖板1。连接盖板1的外表面设有喷铝层b,连 接盖板1通过螺栓3分别固设于若干对接的钢梁2上。
[0022] 本实施例中,钢梁2为工字型钢,其数量为两根,每一钢梁2包括翼缘21和腹板 22,钢梁2梁端腹板22上开设有标准螺栓孔(图中未示出),钢梁2的连接处设有喷漆层 a。连接盖板1的尺寸和厚度与钢梁2腹板22相适应,其固设于两根工字型钢梁2的腹板 22上,并覆盖于喷漆层a上。连接盖板1上开设有与钢梁2梁端腹板22相应的标准螺栓孔 (图中未示出)。本实施例中,喷漆层a为无机富锌漆层,其具有较好的防腐蚀作用和较强 的附着力。
[0023] 本发明中高强螺栓摩擦型连接节点的性能优化方法为:首先,取两根钢梁2、两块 连接盖板1,在腹板22的连接处进行喷砂或者喷丸工艺后喷涂无机富锌漆形成喷漆层a,连 接盖板1外表面进行全方位喷砂或者喷丸工艺后喷涂铝形成喷铝层b ;然后,取若干高强螺 栓3,将两块连接盖板1通过高强螺栓3分别固设于两根对接的钢梁2的腹板22两侧,将高 强螺栓3依次穿过连接盖板1、钢梁2的腹板22和连接盖板1,并按照设计要求进行拧紧安 装。
[0024] 喷丸与喷砂都是使用高压风或压缩空气作动力,将其高速的吹出去冲击工件表面 达到清理效果,工件表面污物被清除掉,工件表面被微量破坏,表面积大幅增加,从而增加 了工件与喷漆层a、喷铝层b的结合强度。
[0025] 本实施例中,连接盖板1的喷铝层b是通过热喷铝工艺制成的,热喷铝工艺流程 为:先进行除油脱脂,再喷砂除锈、除尘,然后热喷铝,并进行过程中检测和孔隙率检测,最 后对表面进行清理。
[0026] 上述热喷铝前表面处理的具体过程如下:1)喷砂除锈。表面喷铝前进行喷砂除 锈,除锈结果应达到国家规范Sa2. 5级的要求;表面粗糙度达到80 μ m以上;2)除尘处理。 喷砂除锈后应采用吸尘器对金属面进行除尘处理。
[0027] 经喷砂除锈合格的金属表面,不得用手触摸,并尽快进行喷涂,晴天时间间隔不得 超过12h,雨天或潮湿的天气不得超过2h,否则应重新进行表面处理。
[0028] 上述热喷铝采用线材火焰喷涂,采用氧-乙炔焰作为热源,铝线材作为喷涂材料。 喷涂时,供给喷枪的氧气和乙炔的压力和流量应能在规定的工作参数范围内连续调节,每 个氧气与乙炔管道上的接头应拧紧,不得有气体泄漏。氧气纯度> 99. 2%,乙炔气纯度 > 96. 5%。供给喷枪的氧气、乙炔、压缩空气的压力及流量应根据铝丝的熔化程度进行调 整,压力控制范围为:氧气为0. 3?0. 6MPa,常用0. 4MPa;乙炔气为0. 05?0. IMPa,常用 0. 07MPa ;压缩空气为0. 5?0. 6MPa。
[0029] 铝线材必须保持表面清洁、无油、无折痕。铝线材直径为Φ 3mm,铝纯度在99. 5% 以上。
[0030] 喷枪点火时,枪口不能对着被喷金属表面,等火焰、铝丝的送丝速度调整好后,铝 丝的雾化程度达到规定要求时,才能开始喷铝作业。喷铝时,喷枪与工件的喷涂角度为 60?90° ,最小不能低于45° ;喷枪与罐内表面的喷涂距离应为120?150mm,最大距离不 得超过200mm ;喷枪移动速度应为300?400mm/s,移动速度要均匀;铝丝送丝速度为2? 2. 2m/min,以保证错丝能充分烙化。
[0031] 每层喷铝层b厚度应均匀,一般为100?300μπι,喷铝层b应分3?4道完成。前 一层与后一层必须进行90°或45°交叉喷涂,相邻喷涂区应有1/3宽度的搭接。其分层喷 铝间隔时间不得超过1小时。喷铝时应防止工件表面有局部过热或涂层局部过厚等现象, 喷铝过程中,不得用手抚摸被喷涂的表面。连接盖板1喷铝施工采用由一段开始逐层进行, 板高< 1500mm时,一次性完成喷砂、喷错作业;板高> 1500mm时,每层喷砂部分要留500mm 以上不喷铝,到端部1000mm段时,一次性完成喷砂、喷铝作业。
[0032] 热喷铝施工时,应有专业检查人员进行外观、溶化程度及厚度检查。保证外观合 格、厚度不得低于设计规定的最小厚度值1〇〇 μ m。喷铝层b孔隙率的检查的具体方法如下: 清除喷铝层b表面的油污、尘土并进行干燥,然后用浸有20g/1000ml的氯化钾溶液的试纸 覆盖在喷涂层b上5?lOmin,试纸上出现的兰色斑点不应多于1?3点/cm 2为合格。
[0033] 由于连接盖板1是使用在连接节点上,在保证孔隙率的前提下,喷铝工作完成后 不进行封孔,避免摩擦系数降低。
[0034] 上述热喷铝操作的环境温度不宜低于15°C,相对湿度不宜大于80%,严禁在潮湿 构件表面进行施工,罐内通风排气要畅通,照明要用防爆灯具。
[0035] 本发明高强螺栓摩擦型连接节点的性能优化方法在腹板22的连接处进行喷砂或 喷丸工艺后喷涂无机富锌漆形成喷漆层a,连接盖板1的外表面设有喷铝层b,连接盖板1 通过高强螺栓3分别固设于若干对接的钢梁2上,其具有以下的技术效果:
[0036] 1、连接盖板1与待连接的钢梁2的接触面分别为喷漆层a和喷铝层b,喷漆层a和 喷铝层b形成的摩擦面具有较高的摩擦系数和抗滑移系数,从而增加了连接盖板1与待连 接的钢梁2的摩擦系数和抗滑移系数,从而提高了连接节点的抗剪承载力。
[0037] 2、热喷涂铝对钢铁基体有双重保护作用。一方面,可以像涂料那样(尤其是经过 封闭处理的涂层)起着物理覆盖作用,将钢铁与水和空气等腐蚀介质隔离开来,从而起到 防护作用。另一方面,由于铝的电化学性能比较活泼,电极电位比铁低,在这个腐蚀电池中, 铝是负极,铁则为正极,铝失去电子,变成离子进入电介质溶液中而被腐蚀,其自由电子流 向钢铁,使钢铁极化而受到保护。因此,使连接节点具有较强的整体耐腐蚀性。
[0038] 3、由于热喷涂时铝呈熔融液滴喷射到经过糙化处理的钢铁表面上,熔滴有较大的 热能,获得比有机涂料层更牢固的结合强度,而且铝是一种活性很强的金属,很容易与氧结 合,生成一层致密、坚硬的氧化保护层,有效地防止铝涂层进一步氧化,具有更长的保护周 期,不需要长年维修保养,避免了人工成本浪费。
[0039] 以上所述仅为本发明的较佳实施例而已,并不用以限制本发明,凡在本发明的精 神和原则之内所作的任何修改、等同替换和改进等,均应包含在本发明的保护范围之内。
高强螺栓摩擦型连接结构及其连接节点性能优化方法
- 专利详情
- 全文pdf
- 权力要求
- 说明书
- 法律状态
查看更多专利详情
下载专利文献
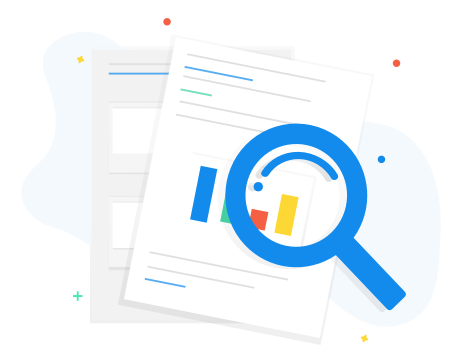
下载专利
同类推荐
-
陈龙云, 林烜陈龙云, 林烜陈龙云, 林烜陈龙云, 林烜陈龙云, 林烜陈龙云, 林烜
您可能感兴趣的专利
-
陈龙云, 林烜陈龙云, 林烜宋述泽, 宋佩萱宋述泽, 宋佩萱宋述泽, 宋佩萱宋述泽, 宋佩萱王惠荣
专利相关信息
-
王强, 周均平王强, 周均平王强, 周均平H·约曼斯, A·亨特H·约曼斯, A·亨特