专利名称:聚偏氟乙烯和偏氟乙烯-六氟丙烯共聚物共混纳米纤维聚合物电解质膜及其制备方法随着经济的发展和社会的进步,人类在创造财富的同时也面临着天然能源等减少 问题,因此国家提出了“节能减排”的政策。开发绿色的新能源材料与技术就成为了科研工 作者的研究热点。锂离子电池具有高比能量、长循环寿命、无记忆效应、能快速充放电等优 点,是绿色环保型无污染的二次电池,符合当今各国能源环保方面的发展需求,在各行各业 中的使用量也迅速增加。通常的锂离子二次电池由正/负极材料、电解液、隔膜以及电池外壳包装材料组 成。隔膜是液态锂离子二次电池的重要组成部分,在电池中起着防止正/负极短路,同时在 充放电过程中提供离子运输电通道的作用,其性能决定了电池的界面结构、内阻等,直接影 响电池的容量、循环性能以及安全性能等特性,性能优异的隔膜对提高电池的综合性能具 有重要的作用。目前,锂离子电池中广泛使用的隔膜为Celgard法生产的微孔膜。隔膜的材 料主要有聚丙烯(PP)、聚乙烯(PE)单层微孔膜,以及由PP和PE复合的多层微孔膜。 US4, 138,459,3,843,761采用拉伸工艺制备出低结晶度的高取向PP或者PE,再高温退火获 得高结晶度的取向薄膜。这种薄膜先在低温下进行拉伸形成银纹等缺陷,再高温下使缺陷 拉开,形成微孔。采用PP,PE等非极性材料制成的隔膜有低的表面能,在锂离子电池使用的 极性碳酸酯类电解液中具有很好的浸润,但是膜的孔隙率较低,吸液率低,因此离子电导率 低。从结构上看,锂离子电池中的液态电解液有可能泄漏而存在安全隐患。近年来出 现了聚合物锂离子电池,其中的聚合物电解质膜既起到隔膜的作用,同时也起到电解质的 作用。其中使用的聚合物电解质膜有固体电解质、凝胶电解质、多孔聚合物电解质膜。固体 聚合物电解质的研究可以追溯到1973年,Wright等人(Fenton D E,Parker J Μ, Wright P V. Complexes of alkali metalions with poly (ethylene oxide). Polymer,1973,14 589-591.)发现聚醚碱金属盐复合物有离子导电性,聚氧化乙烯(PEO)是一种高度结晶的 聚合物,结晶部分会阻碍锂离子的迁移,因此在温度40 100°C时,电导率为10_8 10_4S/ cm,限制了其在室温下的实际应用。降低聚合物的结晶度或向聚合物中加入增塑剂可以提 高聚合物电解质的电导率,因此提出了凝胶电解质。凝胶聚合物电解质是由聚合物基体、 增塑剂以及锂盐形成的凝胶态体系,它具有液体电解质体系中的隔膜与离子导电载体的功 能。至今研究的用于聚合物锂离子电池的聚合物主要有如下几种类型聚醚系[主要为聚 氧化乙烯(ΡΕ0)],聚丙烯腈(PAN)系、聚甲基丙烯酸甲酯(PMMA)系、聚偏氟乙烯(PVDF)系、聚氯乙烯(PVC)和其它类型,作为高分子主体与各种非质子溶剂混合,可以制得一系列在20°C时电导率在0. 1 lX10_3S/cm之间的凝胶态聚合物电解质。方法是在加热温度高于 聚合物玻璃化转变温度以上时,将聚合物与溶剂和锂盐混合形成均勻高粘度的液体,然后 用溶液浇铸的方法成膜,加压冷却后制备电解质膜。但是该制备方法要求整个过程都在无 水无氧的手套箱中进行,所有的原材料必须经过严格干燥处理,工艺条件比较苛刻。多孔聚合物电解质源于1994 年 Bellcore (Pasquier A D, Warren P C, GozdzA S, Amatucci G G. Plastic PVDF-HFP electrolyte laminates prepared by aphase-inversion process. Solid State Ionics,2000,135 :249_257.)公司研发的塑料 锂离子聚合物电池,采用聚偏氟乙烯-六氟丙烯共聚物(PVDF-HFP)为聚合物基体,与聚偏 氟乙烯(PVDF)相比,由于在偏氟乙烯(VDF)基团上引入了六氟丙烯(HFP)基团与其共聚, 降低了 PVDF的结晶度,因而有利于被液体电解质溶胀,另一方面,PVDF-HFP具有一定的结 晶度而提供了足够的机械强度。Bellcore技术是先将PVDF-HFP增塑,紧接着除去增塑剂制 备得到多孔膜,然后用液体电解质再次溶胀而形成聚合物电解质。1995年Gozdz (USPatent No 5296318)采用邻苯二甲酸二丁酯(DBP)为增塑剂,将DBP与PVDF-HFP溶解在丙酮 中,浇铸成膜后采用二乙醚萃取DBP,再用LiPF6-EC-DMC活化后得到的电解质的电导率为 0. 2Xl(T3S/cm(25°C )。电纺丝技术是一项生产纳米纤维的快速、简便、易操作且形式多样的技术,用电纺 丝技术制备的超细纤维具有比表面大,孔隙率高,纤维径细,质轻和形貌均一等特点。由于 存在这些优点,电纺丝越来越受到人们的好评与关注,广泛的应用于组织工程,药物控制释 放,电解质膜,过滤等领域。综上所述,聚合物电解质膜不仅要有高的电导率,还要有热稳定性、化学稳定性、 机械强度高等,要达到这些要求,与聚合物材料本体的性质有关,也与聚合物电解质膜的成 膜过程等工艺相关。要提高聚合物电解质膜的电导率,可以采取降低聚合物的结晶度着手, 因此,在采用PVDF基电解质的基础上提出了 PVDF-HFP共聚物基电解质,降低了 PVDF的结 晶度的同时其机械强度也得到了保证。但是当电解液的温度升高时,PVDF-HFP膜在碳酸酯 类液体电解质中的溶胀率大,易变形,甚至完全溶解,导致电池短路等。另外,多孔聚合物电 解质膜的导电机理是聚合物膜孔中吸附的液体电解质和聚合物的无定形部分溶胀的电解 质共同作用的,提高聚合物膜的孔隙率是提高聚合物膜的吸液率的一种有效方法。根据上面的介绍,为了提高聚合物电解质膜的电导率,本发明采用静电纺丝法制 备纳米纤维膜活化后得到聚合物电解质膜。同时为了解决偏氟乙烯-六氟丙烯共聚物膜在 电解液中变形和溶解的问题,本发明采用聚偏氟乙烯与偏氟乙烯-六氟丙烯共聚物共混制 备共混聚合物电解质膜。得到的共混电解质膜孔隙率高,比表面积大,吸液率高,并且由于 聚偏氟乙烯的存在,即使偏氟乙烯-六氟丙烯共聚物溶胀或者溶解也不会使电池短路,提 高了电池的安全性。
本发明的目的是提供静电纺丝法制备的聚偏氟乙烯和偏氟乙烯-六氟丙烯共聚 物共混纳米纤维聚合物电解质膜,以解决现有的锂离子电池电解质膜中存在的电解液吸收 率低、电导率低、强度差、电解质膜在高温时在电解液中溶解而使电池不安全等问题,促进安全、高性能的锂离子电池技术的发展。本发明的再一目的是提供一种聚偏氟乙烯和偏氟乙烯-六氟丙烯共聚物共混纳 米纤维聚合物电解质膜的制备方法。本发明的聚偏氟乙烯和偏氟乙烯-六氟丙烯共聚物共混纳米纤维聚合物电解质 膜是由静电纺丝法制备得到的,所述的共混纳米纤维聚合物电解质膜是含有电解液的共混 纳米纤维膜,所述的共混纳米纤维膜是由聚偏氟乙烯和偏氟乙烯_六氟丙烯共聚物共混纳 米纤维材料构成;其中,聚偏氟乙烯占共混纳米纤维膜的质量百分比含量为50 90%,偏 氟乙烯-六氟丙烯共聚物占共混纳 米纤维膜的质量百分比含量为10 50% ;构成共混纳 米纤维膜中的聚偏氟乙烯和偏氟乙烯-六氟丙烯共聚物共混纳米纤维与聚偏氟乙烯和偏 氟乙烯-六氟丙烯共聚物共混纳米纤维之间的孔隙率为45 80%。本发明的共混纳米纤维聚合物电解质膜的吸液率为210 360%。所述的电解液是LiPF6-EC/DMC/DEC,即由溶质LiPF6及溶剂碳酸酯乙烯酯(EC)、二 甲基碳酸酯(DMC)和二乙基碳酸酯(DEC)构成;其中在浓度为1摩尔的LiPF6-EC/DMC/DEC 中的溶剂碳酸酯乙烯酯二甲基碳酸酯二乙基碳酸酯的重量比为1 1 1。所述的聚偏氟乙烯和偏氟乙烯-氟丙烯共聚物共混纳米纤维的直径为300 700nmo所述的聚偏氟乙烯和偏氟乙烯-六氟丙烯共聚物共混纳米纤维与聚偏氟乙烯和 偏氟乙烯-六氟丙烯共聚物共混纳米纤维之间的孔径为0. 2 10 μ m。所述的聚偏氟乙烯的重均分子量为2X 107g/mol。所述的偏氟乙烯-六氟丙烯共聚物的重均分子量为4. 77X 105g/mol。所述的共混纳米纤维聚合物电解质膜的厚度为25 60 μ m。本发明的聚偏氟乙烯和偏氟乙烯-六氟丙烯共聚物纳米纤维聚合物电解质膜的 制备方法包括以下步骤1)纺丝液的配制将聚偏氟乙烯、偏氟乙烯-六氟丙烯共聚物溶解于N,N_ 二甲基甲酰胺和丙酮的混 合溶剂中,在45 50°C下磁力搅拌24 48小时后得到澄清透明的聚偏氟乙烯和偏氟乙 烯-六氟丙烯共聚物的共混纺丝溶液;其中,共混纺丝溶液的质量浓度为8 14%,聚偏氟 乙烯与偏氟乙烯-六氟丙烯共聚物的质量比为1 1 9 1。2)静电纺丝法制备聚偏氟乙烯和偏氟乙烯_六氟丙烯共聚物共混纳米纤维膜将步骤1)制备的聚偏氟乙烯和偏氟乙烯_六氟丙烯共混纺丝溶液置于静电纺丝 设备的注射器中,固定好与注射器相连通的喷丝头(可为不锈钢针头)与滚筒接收器(可 为抛光不锈钢滚筒)之间的距离,待纺丝时所需的温度和湿度达到条件后,在注射泵的作 用下共混纺丝溶液以恒定的流量注射进喷丝头中,在喷丝头与接地的滚筒接收器之间施加 一定的高压,共混纺丝溶液在静电作用下产生射流,在滚筒接收器上得到共混纳米纤维膜, 干燥;通过控制共混纺丝溶液的流量和纺丝时间来控制共混纳米纤维膜的厚度,可制备得 到共混纳米纤维膜的厚度为25 60 μ m。3)在充满氩气的手套箱中,水分< lppm,O2 < Ippm ;将步骤2)由聚偏氟乙烯和 偏氟乙烯_六氟丙烯共聚物制备得到的共混纳米纤维膜,在室温(一般为10 25°C )下 浸泡于浓度为1摩尔的LiPF6-EC/DMC/DEC(其中溶剂碳酸酯乙烯酯(EC) 二甲基碳酸酯(DMC) 二乙基碳酸酯(DEC)的重量比为1:1:1)电解液中(一般为30 60分钟), 取出,得到聚偏氟乙烯和偏氟乙烯_六氟丙烯共聚物共混纳米纤维聚合物电解质膜。 所述的混合溶剂中的N,N-二甲基甲酰胺与丙酮的质量比为7 3。步骤2)所述的喷丝头与滚筒接收器之间的距离为7 17cm。步骤2)所述的纺丝时的温度为18 60°C,湿度为35 80%。步骤2)所述的共混纺丝溶液的流量为0. 5 9ml/h。步骤2)所述的高压是7 15kV的高压。步骤2)所述的纺丝时间是1 3小时。步骤2)所述的滚筒接收器的转速为5 500rpm。所述的干燥是在60 80°C的烘箱中干燥。本发明的聚偏氟乙烯和偏氟乙烯-六氟丙烯共聚物共混纳米纤维聚合物电解质 膜的吸液率达到210 360%,室温电导率能够达到3. 04X 10_3S/cm。本发明的纳米纤维聚 合物电解质膜的孔隙率高,比表面积大,用作锂离子电池电解质膜材料,具有吸液率高,与 正负极粘结牢固,且力学性能优良。图1.本发明实施例2中聚偏氟乙烯和偏氟乙烯_六氟丙烯共聚物共混纳米纤维 膜的表面SEM图。图2.本发明实施例3中聚偏氟乙烯和偏氟乙烯_六氟丙烯共聚物共混纳米纤维 膜的表面SEM图。图3.本发明实施例6中聚偏氟乙烯和偏氟乙烯-六氟丙烯共聚物共混纳米纤维 膜的表面SEM图。<formula>formula see original document page 7</formula>
(3)吸液率室温下,将剪取一定大小的步骤2)制备的聚偏氟乙烯/偏氟乙烯_六氟丙烯共聚 物纳米纤维膜称其质量为(Hi1),将该膜在电解液中浸泡60分钟,取出后在两片滤纸间轻轻除去膜表面多余的电解液,称重为m2。吸液率的计算式如下
<formula>formula see original document page 8</formula>(4)电导率室温下,本发明的聚合物电解质膜的电导率采用交流阻抗法测定,将聚合物电解 质膜夹在两个不锈钢电极之间,采用Solartron SI1287电化学界面仪结合SI1255B频率响 应仪,HP2192a分析仪测试,应用下式计算聚合物电解质膜的电导率<formula>formula see original document page 8</formula>其中,σ为聚合物电解质膜的电导率(S/cm),d为聚合物电解质膜的厚度(cm),Rb 为聚合物电解质膜的本体电阻(Ω),A为聚合物电解质膜与电极接触的有效面积(cm2)。实施例中优选采用的聚偏氟乙烯的重均分子量为2X107g/mol ;偏氟乙烯-六氟 丙烯共聚物的重均分子量为4. 77X 105g/mol。实施例1将5. 6g聚偏氟乙烯和2. 4g偏氟乙烯-六氟丙烯共聚物溶解在64. 4gN, N- 二甲基 甲酰胺和27. 6g丙酮中,溶液的总浓度为8wt%,聚偏氟乙烯与偏氟乙烯-六氟丙烯共聚物 的质量比为7 3,溶剂中N,N-二甲基甲酰胺与丙酮的质量比为7 3,在50°C下磁力搅拌 48小时后得到澄清透明的纺丝溶液,过滤后静置脱泡。聚偏氟乙烯/偏氟乙烯-六氟丙烯共 聚物共混纺丝液置于静电纺丝设备的注射器中,调整与注射器相连的喷丝头与滚筒接收器 之间的距离为13cm,待温度为20士2°C,湿度为80%时,在注射泵的作用下纺丝液以lml/h 恒定的流量注射进喷丝头中,在喷丝头与接地的滚筒接收器之间施加的电压为llkV,滚筒 接收器的转速为5rpm,在接收器上得到共混纳米纤维膜,纺丝时间为2. 5小时,制备的共混 纳米纤维膜的厚度为45士2 μ m,聚偏氟乙烯和偏氟乙烯-氟丙烯共聚物共混纳米纤维的直 径为530nm,该膜中的聚偏氟乙烯和偏氟乙烯-六氟丙烯共聚物共混纳米纤维与聚偏氟乙 烯和偏氟乙烯_六氟丙烯共聚物共混纳米纤维之间的平均孔径为2. 21 μ m。将该膜在80°C 的烘箱中干燥后裁剪成一定尺寸大小的膜,由式(1)计算孔隙率,孔隙率为75%。室温(25°C )下,在充满氩气的手套箱中,水分< lppm,O2 < lppm,将已知质量的 聚偏氟乙烯/偏氟乙烯-六氟丙烯共聚物共混纳米纤维膜在浓度为1摩尔的溶质为LiPF6, 溶剂为碳酸酯乙烯酯、二甲基碳酸酯和二乙基碳酸酯的电解液(碳酸酯乙烯酯二甲基碳 酸酯二乙基碳酸酯的重量比为1 1 1)中浸泡60分钟,取出,即得所述的聚偏氟乙烯 /偏氟乙烯-六氟丙烯共聚物共混纳米纤维聚合物电解质膜。采用式(2)计算该膜的吸液 率,根据膜的电导率的测定方法测试并采用式(3)计算该膜的室温电导率。该膜的吸液率 为310%,室温电导率为2. 58X 10"3S/cmo实施例2将7. 2g聚偏氟乙烯和0. 8g偏氟乙烯-六氟丙烯共聚物溶解在64. 4gN, N- 二甲基 甲酰胺和27. 6g丙酮中,溶液的总浓度为8wt%,聚偏氟乙烯与偏氟乙烯-六氟丙烯共聚物 的质量比为9 1,溶剂中N,N-二甲基甲酰胺与丙酮的质量比为7 3,在50°C下磁力搅拌48小时后得到澄清透明的纺丝溶液,过滤后静置脱泡。聚偏氟乙烯/偏氟乙烯_六氟丙烯 共聚物共混纺丝液置于静电纺丝设备的注射器中,调整与注射器相连的喷丝头与滚筒接收 器之间的距离为13cm,待温度为20士2°C,湿度为55%时,在注射泵的作用下纺丝液以Iml/ h恒定的流量注射进喷丝头中,在喷丝头与接地的滚筒接收器之间施加的电压为10kV,滚 筒接收器的转速为5rpm,在接收器上得到共混纳米纤维膜,纺丝时间为2. 5小时,制备的共 混纳米纤维膜的厚度为45 士 2 μ m,聚偏氟乙烯和偏氟乙烯-六氟丙烯共聚物共混纳米纤维 的直径为480nm,该膜中的聚偏氟乙烯和偏氟乙烯-六氟丙烯共聚物共混纳米纤维与聚偏 氟乙烯和偏氟乙烯-六氟丙烯共聚物共混纳米纤维之间的平均孔径为1.87μπι。将该膜在 80°C的烘箱中干燥后裁剪成一定尺寸大小的膜,由式(1)计算孔隙率,孔隙率为70%。
聚偏氟乙烯/偏氟乙烯-六氟丙烯共聚物共混纳米纤维膜所浸泡的电解质溶液及 工艺条件与实施例1相同。得到的聚偏氟乙烯和偏氟乙烯-六氟丙烯共聚物共混纳米纤维 聚合物电解质膜的吸液率和电导率的测定与实施例1相同。该膜的吸液率为290%,室温电 导率为 2. 05 X IO-Vcm0聚偏氟乙烯和偏氟乙烯-六氟丙烯共聚物共混纳米纤维膜的表面SEM图,如图1 所示。实施例3将4. Og聚偏氟乙烯和4. Og偏氟乙烯-六氟丙烯共聚物溶解在64. 4gN, N- 二甲基 甲酰胺和27. 6g丙酮中,溶液的总浓度为8wt%,聚偏氟乙烯与偏氟乙烯-六氟丙烯共聚物 的质量比为1 1,溶剂中N,N-二甲基甲酰胺与丙酮的质量比为7 3,在50°C下磁力搅拌 48小时后得到澄清透明的纺丝溶液,过滤后静置脱泡。聚偏氟乙烯/偏氟乙烯_六氟丙烯 共聚物共混纺丝液置于静电纺丝设备的注射器中,调整与注射器相连的喷丝头与滚筒接收 器之间的距离为13cm,待温度为20士2°C,湿度为55%时,在注射泵的作用下纺丝液以Iml/ h恒定的流量注射进喷丝头中,在喷丝头与接地的滚筒接收器之间施加的电压为10kV,滚 筒接收器的转速为5rpm,在接收器上得到共混纳米纤维膜,纺丝时间为2. 5小时,制备的共 混纳米纤维膜的厚度为45 士 2 μ m,聚偏氟乙烯和偏氟乙烯-六氟丙烯共聚物共混纳米纤维 的直径为400nm,该膜中的聚偏氟乙烯和偏氟乙烯-六氟丙烯共聚物共混纳米纤维与聚偏 氟乙烯和偏氟乙烯_六氟丙烯共聚物共混纳米纤维之间的平均孔径为4. 42 μ m。将该膜在 80°C的烘箱中干燥后裁剪成一定尺寸大小的膜,由式(1)计算孔隙率,孔隙率为72%。聚偏氟乙烯/偏氟乙烯-六氟丙烯共聚物共混纳米纤维膜所浸泡的电解质溶液及 工艺条件与实施例1相同。得到的聚偏氟乙烯和偏氟乙烯-六氟丙烯共聚物共混纳米纤维 聚合物电解质膜的吸液率和电导率的测定与实施例1相同。该膜的吸液率为360%,室温电 导率为 3. 04 X IO-Vcm0聚偏氟乙烯和偏氟乙烯-六氟丙烯共聚物共混纳米纤维膜的表面SEM图,如图2 所示。实施例4将5. 6g聚偏氟乙烯和2. 4g偏氟乙烯-六氟丙烯共聚物溶解在64. 4gN, N- 二甲基 甲酰胺和27. 6g丙酮中,溶液的总浓度为8wt%,聚偏氟乙烯与偏氟乙烯-六氟丙烯共聚物 的质量比为7 3,溶剂中N,N-二甲基甲酰胺与丙酮的质量比为7 3,在50°C下磁力搅拌 48小时后得到澄清透明的纺丝溶液,过滤后静置脱泡。聚偏氟乙烯/偏氟乙烯_六氟丙烯共聚物共混纺丝液置于静电纺丝设备的注射器中,调整与注射器相连的喷丝头与滚筒接收器之间的距离为13cm,待温度为20士2°C,湿度为55%时,在注射泵的作用下纺丝液以9ml/ h恒定的流量注射进喷丝头中,在喷丝头与接地的滚筒接收器之间施加的电压为15kV,滚 筒接收器的转速为500rpm,在接收器上得到共混纳米纤维膜,纺丝时间为1小时,制备的共 混纳米纤维膜的厚度为50 士 2 μ m,聚偏氟乙烯和偏氟乙烯-六氟丙烯共聚物共混纳米纤维 的直径为670nm,该膜中的聚偏氟乙烯和偏氟乙烯-六氟丙烯共聚物共混纳米纤维与聚偏 氟乙烯和偏氟乙烯-六氟丙烯共聚物共混纳米纤维之间的平均孔径为1.52μπι。将该膜在 80°C的烘箱中干燥后裁剪成一定尺寸大小的膜,由式(1)计算孔隙率,孔隙率为65%。聚偏氟乙烯/偏氟乙烯-六氟丙烯共聚物共混纳米纤维膜所浸泡的电解质溶液及 工艺条件与实施例1相同。得到的聚偏氟乙烯和偏氟乙烯-六氟丙烯共聚物共混纳米纤维 聚合物电解质膜的吸液率和电导率的测定与实施例1相同。该膜的吸液率为240%,室温电 导率为 1. 65 X IO-Vcm0实施例5将8. 8g聚偏氟乙烯和5. 2g偏氟乙烯-六氟丙烯共聚物溶解在77. 4gN, N- 二甲基 甲酰胺和8. 6g丙酮中,溶液的总浓度为14wt%,聚偏氟乙烯与偏氟乙烯-六氟丙烯共聚物 的质量比为7 3,溶剂中N,N-二甲基甲酰胺与丙酮的质量比为7 3,在50°C下磁力搅拌 48小时后得到澄清透明的纺丝溶液,过滤后静置脱泡。聚偏氟乙烯/偏氟乙烯_六氟丙烯 共聚物共混纺丝液置于静电纺丝设备的注射器中,调整与注射器相连的喷丝头与滚筒接收 器之间的距离为13cm,待温度为20士2°C,湿度为55%时,在注射泵的作用下纺丝液以Iml/ h恒定的流量注射进喷丝头中,在喷丝头与接地的滚筒接收器之间施加的电压为13. 5kV, 滚筒接收器的转速为5rpm,在接收器上得到共混纳米纤维膜,纺丝时间为2小时,制备的共 混纳米纤维膜的厚度为50 士 2 μ m,聚偏氟乙烯和偏氟乙烯-六氟丙烯共聚物共混纳米纤维 的直径为520nm,该膜中的聚偏氟乙烯和偏氟乙烯-六氟丙烯共聚物共混纳米纤维与聚偏 氟乙烯和偏氟乙烯_六氟丙烯共聚物共混纳米纤维之间的平均孔径为0. 2 μ m。将该膜在 80°C的烘箱中干燥后裁剪成一定尺寸大小的膜,由式(1)计算孔隙率,孔隙率为60%。聚偏氟乙烯/偏氟乙烯-六氟丙烯共聚物共混纳米纤维膜所浸泡的电解质溶液及 工艺条件与实施例1相同。得到的聚偏氟乙烯和偏氟乙烯-六氟丙烯共聚物共混纳米纤维 聚合物电解质膜的吸液率和电导率的测定与实施例1相同。该膜的吸液率为210%,室温电 导率为 1. 02 X IO-Vcm0实施例6将5. 6g聚偏氟乙烯和2. 4g偏氟乙烯-六氟丙烯共聚物溶解在64. 4gN,N_ 二甲基 甲酰胺和27. 6g丙酮中,溶液的总浓度为8wt%,聚偏氟乙烯与偏氟乙烯-六氟丙烯共聚物 的质量比为7 3,溶剂中N,N-二甲基甲酰胺与丙酮的质量比为7 3,在50°C下磁力搅拌 48小时后得到澄清透明的纺丝溶液,过滤后静置脱泡。聚偏氟乙烯/偏氟乙烯_六氟丙烯 共聚物共混纺丝液置于静电纺丝设备的注射器中,调整与注射器相连的喷丝头与滚筒接收 器之间的距离为17cm,待温度为20士2°C,湿度为55%时,在注射泵的作用下纺丝液以Iml/ h恒定的流量注射进喷丝头中,在喷丝头与接地的滚筒接收器之间施加的电压为15kV,滚 筒接收器的转速为5rpm,在接收器上得到共混纳米纤维膜,纺丝时间为2. 5小时,制备的共 混纳米纤维膜的厚度为45 士 2 μ m,聚偏氟乙烯和偏氟乙烯-六氟丙烯共聚物共混纳米纤维的直径为500nm,该膜中的聚偏氟乙烯和偏氟乙烯-六氟丙烯共聚物共混纳米纤维与聚偏氟乙烯和偏氟乙烯_六氟丙烯共聚物共混纳米纤维之间的平均孔径为3. 51 μ m。将该膜在 80°C的烘箱中干燥后裁剪成一定尺寸大小的膜,由式(1)计算孔隙率,孔隙率为68%。聚偏氟乙烯/偏氟乙烯-六氟丙烯共聚物共混纳米纤维膜所浸泡的电解质溶液及 工艺条件与实施例1相同。得到的聚偏氟乙烯和偏氟乙烯-六氟丙烯共聚物共混纳米纤维 聚合物电解质膜的吸液率和电导率的测定与实施例1相同。该膜的吸液率为280%,室温电 导率为 1. 78 X IO-Vcm0聚偏氟乙烯和偏氟乙烯-六氟丙烯共聚物共混纳米纤维膜的表面SEM图,如图3 所示。
本发明涉及静电纺丝法制备的聚偏氟乙烯和偏氟乙烯-六氟丙烯共聚物共混纳米纤维聚合物电解质膜及制备方法。所述共混纳米纤维聚合物电解质膜是含有电解液的共混纳米纤维膜,共混纳米纤维膜是由聚偏氟乙烯和偏氟乙烯-六氟丙烯共聚物共混纳米纤维材料构成;聚偏氟乙烯占共混纳米纤维膜的质量百分比含量为50~90%,偏氟乙烯-六氟丙烯共聚物占共混纳米纤维膜的质量百分比含量为10~50%;构成共混纳米纤维膜中的聚偏氟乙烯和偏氟乙烯-六氟丙烯共聚物共混纳米纤维与聚偏氟乙烯和偏氟乙烯-六氟丙烯共聚物共混纳米纤维之间的孔隙率为45~80%。本发明膜的吸液率为210~360%,室温电导率能够达到3.04×10-3S/cm。
聚偏氟乙烯和偏氟乙烯-六氟丙烯共聚物共混纳米纤维聚合物电解质膜及其制备方法
- 专利详情
- 全文pdf
- 权力要求
- 说明书
- 法律状态
查看更多专利详情
下载专利文献
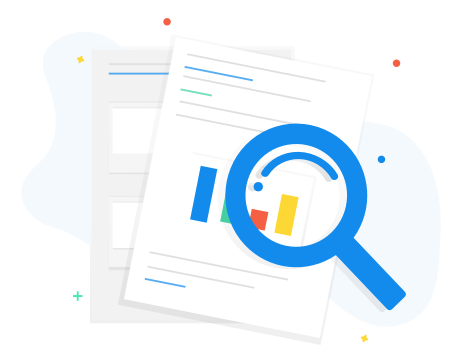
下载专利
同类推荐
您可能感兴趣的专利
-
常惠联, 常万叶D.J.威廉斯E·C·考斯坦赛克德米特里·弗拉基米罗维奇·济宾
专利相关信息