专利名称:一种用等离子弧精炼硅的工艺方法本发明涉及一种用等离子弧作为热源的精炼硅的工艺方法,本方法特别适用于制备其纯度足以供冶金和太阳能电池使用的硅。目前使用的制备硅的典型方法,是在埋入式电弧炉中通过使含二氧化硅(SiO2)的材料与某种含碳的固体还原剂发生还原反应来生产硅的,其中所用的含二氧化硅的材料可以是石英,熔凝的硅石或气态硅石,还原剂材料可以是焦炭、煤、木片或其它含碳材料。整个的还原反应为一般认为,上述的反应实际上包含着一系列的化学反应,其最重要的有在反应温度下,一氧化硅(SiO)是一种气态物质,如果反应不完全,它可能会以某种蒸气的形式损失掉。Muller等人在Scand.J.Metall.,1(1972)的145~155页中给出了利用碳还原反应从二氧化硅中制取硅时的Si-O-C化学物系的理论上的平衡条件,并对此进行了描述。但按Muller等人给出的平衡条件,在大气压力和1819℃的温度下,一氧化硅的分压必须大于或等于0.67个大气压时,上述的反应式(5)描述的反应才会发生,才能生成硅。Johannson和Eriksson在J.Electrochem.Soc.Solid State Science and Technology,1312(1984)的365~370页中对Si-O-C物系作了进一步地描述和定义。Johannson和Eriksson认为,压力对该化学反应是有影响的,并指出,在理论上,为了达到接近100%的硅产率,从而使原材料的利用率达到最大限度,5个大气压是最优选的压力。用埋入式电弧炉生产硅在产业界已经有许多年了,但一般认为,在这样一个系统中存在有几个固有的缺点。在目前的埋入式电弧炉中,通常是将二氧化硅和含碳的还原固体装载到炉子的顶部,随着反应的进行,在埋入式电极的低端、炉子的底部会形成一个中空。熔化了的硅收集在中空的底部,在中空的顶部是一层反应物、中间产物和产品硅的混合体,在这层的上面是形态可变的固体反应物和中间产物。由于埋入式电弧炉里的热传导和质量输运均不良,使得电能利用率和原料利用率降低,其所消耗的能量约为理论值的3倍。这样高的能量消耗与作为付产品的一氧化碳气的损失有关,因为后者把传给含碳还原剂的能量带走了。热传导和质量输运的不良是由几个因素造成的,例如,在这种炉中,反应物和中间产物之间的固相-固相和固相-气相的质量输运限制了炉中的热传导和质量输运的效率。而且,易挥发的SiO会同反应过程中的气体付产品一起排出而造成材料的损失。据估计,在目前的埋入式电弧炉中,因排出的SiO造成的损失大约是最终硅产量的10%~20%。一氧化硅还会再次氧化而形成SiO2。因此,SiO的逃逸并不仅仅是材料损失的问题,还会阻碍整个工艺过程的进行,而且从反应系统逃逸出的SiO2又会形成悬浮于空中的微粒而污染环境,因而必须将它们收集起来处理掉,这又是相当困难的事情。在目前的埋入式电弧炉中,制备硅的流程中还有力学上的问题。例如,固体流要向下运动,而与其逆流的向上运动的气体阻碍着固体流进入反应中空,由于在反应中空上方的层状混和物会产生桥接现象,从而使添加的固体反应物的输运受到该现象的阻碍而停顿下来。该桥接现象的出现还与上述的固体靠近垂直的电极有关,并且与在炉子上段比较凉的区域中形成的粘性中间产物有关。因而需要从炉子的顶端为受到阻碍的固体反应物打通输运通路,需要频频地打开反应器,捣碎或“烧碎”上述的固体并使其向下运动。这种电弧炉的碳电极是不断损耗的,这即增加了最后产品硅中的杂质含量,又增加了产品硅的成本。在传统的电弧炉中,碳电极是制备硅时的主要杂质来源。而且据估计,硅的制造成本中的大约10%是由于碳电极的和与电极有关的其它问题而增加上的。用等离子弧炉代替电弧炉有许多优点。根据上述反应流程,反应是吸热反应,且消耗的能量约占整个反应过程的能量消耗的50%。在等离子弧炉中,由于SiO2和含碳材料是直接馈入到高能等离子弧中,因而使热和质量的输运能增加到最大的限度,从而促进了生成SiC的反应。碳化硅的高效率生成又将进一步促进随后的生成硅的反应,即促进由反应表示的反应过程的进行。SiO2的熔化和SiC的生成的同时进行,也有助于改善质量输运。通过改变反应器的布置构成也有助于消除前述的“桥接现象”,不再需要为了进行“烧碎”而定期打开炉子。这样,炉子就可以是封闭的,而且可以在加压下工作。炉子的封闭构成有助于付产品的回收及原先损失掉的、气体付产品中的能量的回收。由于不再使用原先在电弧炉中使用的碳电极,从而使最后产品硅的纯度大大提高。用等离子弧处理金属氧化物的一种方法已由Foex在美国专利3257196(1966、6、21)中公开。Foex的方案是把要处理的材料压缩在一个容器里,该容器可以绕其中心轴旋转,并沿轴向形成有一个等离子弧可以穿入的腔。等离子弧可以作为运载工具把反应物运到固体反应物区域内。Foex的方案是根据设计一可旋转反应器的需要而提出的,而且该反应器的断续供料装置要比本发明的连续供料装置复杂的多。此外,Foex的方案采用了用把粉末状金属氧化物压入旋转反应器中并利用离心力使粉末保持在反应器里的方法,而不是将粉末状金属氧化物不断地馈入到等离子射流中的方法。在Foex方案中,反应区是在致密的坚实的固体表面上,而不是象本发明中所描述的在多孔的固体填充物上。本发明采用了连续供给粉末状的反应物到等离子弧区中的方法。上述种种差异对本发明装置的热传导和质量输运的效率的提高有着明显的作用。Coldwell和Roques在J.Electrochemical Soc.,124(11)(1977)的1686~1689页中描述了一个由二氧化硅和碳粉加压成型的棒在等离子弧中的反应过程,他们还描述了射频感应式等离子体的应用。如下所述,与感应等离子体相连系的大流量气体对生成硅的还原反应是一个阻碍因素。他们还指出了由于感应等离子体所必需的大流量气体而引起的种种困难。产品硅呈气态,要用骤冷的方法回收,而回收的硅至多超不过骤冷产物的33%,他们认为,因为在该条件下的等离子弧中的生成物的高反应性,这样低的硅回收率已经是可能达到的最好结果了。同本发明的连续生产工艺相比,Coldwell和Roques的方法是断续填料式的生产工艺方法。此外,Coldwell和Roques方案中的工作温度规范要比本发明的高得多,从而使离开反应区的硅呈蒸气状态。这相当高的温度规范完全改变了系统的化学和热力学平衡,这使得它同本发明是不能类比的。
Stramke等人在德国公开专利申请2924584(1981、1、15)中描述了一个使硅石或硅通过还原气氛的等离子焰的过程。该方案并不是为了进行二氧化硅的碳还原反应(这和本发明不同),而是为了对硅石或硅中的杂质进行还原,使其从硅材料中去掉。文中提到的还原气体有氢(H2)、甲烷、乙烷、乙稀以及其它的饱和或不饱和的低分子碳氢化合物。
Dahlberg等人在美国专利4377564(1983、3、22)中描述了一种使用二氧化硅和还原剂在等离子弧中制备硅的方法。在等离子弧中,硅是以气态方式生成的,并通过在基体上沉积或冷凝的方式从气态反应混合物中回收硅。关于其产量没有报导。但这个技术方案看来与上述的Coldwell和Roques的方案存在有同样的缺点。文中提到的还原剂有碳、氢、碳氢化合物、氮、一氧化碳(CO)、卤素,及水蒸气。
Santen和Edstrom在美国专利4439410(1984、3、27)中公开了一种把硅石和某种优选的还原剂注入到一气体等离子体中而制备硅的工艺方法。已加热的进料和高能等离子气被引导到一个已填充有固体还原剂的反应腔中,使硅石熔化后并还原成硅。其反应气体包括有由H2和CO构成的混合物,该混合气体可以重复使用并可以用作等离子弧的送载气体。文中提到的还原剂有碳氢化合物(天然气)、煤粉、焦炭粉、炭黑、原油焦和其它等等。
在研究Santen和Edstrom的书时,人们会发现其中有前后矛盾的地方。首先,发明说明书中公开,其使用的等离子炉是一个感应式等离子炉,而在发明说明书中并没有记载如何用电弧装置产生等离子体的方法,但是这一点却记载在
权利要求
1.一种利用气体等离子体作为能源的生产硅的工艺方法,该方法包括(Ⅰ)利用转移弧的结构布置,在反应器中产生一气体等离子弧,这种结构产生等离子体所需的气体量最小;(Ⅱ)把二氧化硅和固体还原剂直接馈入到反应器和等离子弧中;(Ⅲ)借助等离子气体把二氧化硅和固体还原剂载到反应器的反应区中;(Ⅳ)从反应区域中回收熔化态的硅和气体付产品。
2.如权利要求
1所述的方法,其特征在于馈入二氧化硅和固体还原剂的方式是,先馈入二氧化硅和固体还原剂的混合物,再馈入二氧化硅;馈入方式也可以以相反的程序进行。
3.如权利要求
2所述的方法,其特征在于馈入的二氧化硅和固体还原剂的混合物中的二氧化硅和固体还原剂的比率是这样控制的,即使其中的碳对二氧化硅的克分子当量比超过化学计算当量的20%。
4.如权利要求
2所述的方法,其特征在于馈入的二氧化硅和固体还原剂的混合物中的二氧化硅和固体还原剂的比率是这样控制的,即使其中的碳对二氧化硅的克分子当量比超过化学计算当量的1%~10%。
5.如权利要求
2所述的方法,其特征在于馈入二氧化硅的量是这样控制的,即使碳与二氧化硅的总体比率基本上等于总体反应的化学计算当量。
6.如权利要求
1所述的方法,其特征在于馈入的二氧化硅和固体还原剂的混合物是一种化合混合物。
本发明公开了一种利用气体等离子体作能源的生产硅的工艺方法,该方法包括a)利用转移弧结构布置,在反应器中产生一气体等离子弧,这种结构产生等离子体所需的气体量最小;b)把二氧化硅和固体还原剂直接馈入到反应器和等离子体中;c)借助等离子体把二氧化硅和固体还原剂载到反应器的反应区中;d)从反应区中回收熔化态的硅和气体副产品。
一种用等离子弧精炼硅的工艺方法
- 专利详情
- 全文pdf
- 权力要求
- 说明书
- 法律状态
查看更多专利详情
下载专利文献
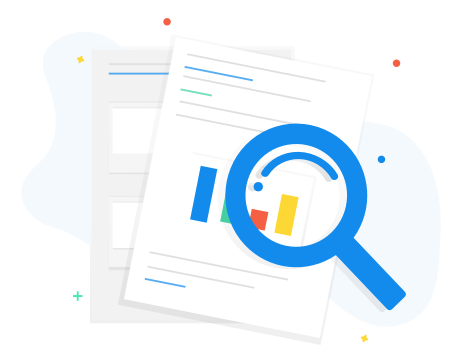
下载专利
同类推荐
-
维叔·达特·道萨耶, 阿尔文·威廉·罗荷尔兹佘志清庄小雄, 徐憬杨伍科杨伍科杨伍科颜钢锋
您可能感兴趣的专利
-
O·阿克塞尔松O·阿克塞尔松O·阿克塞尔松
专利相关信息
-
张显张亚梅