专利名称:浸入式耐火浇注口的制作方法本发明涉及的是用于将熔融金属,特别是钢水,在铸模内铸成薄板件的连续浇铸的浸入式耐火浇注口,铸模在上部中央最好是漏斗状的。在浇注口封闭的底部前面,壁上有位置横向相对的流出口,它们面朝着铸模的狭窄的侧面。这种已知的浸入式浇注口(“炼钢文献”,第八期“连续铸钢”,第21页)与开在底部的浇注口相比更为优越,因为通过将浇注口喷流分开和偏转,可以在铸模中防止对结晶不利的湍流。然而,其缺点是,在充满铸模的过程中,金属飞溅到模壁的上部并在其上结块,因此,浇铸薄壳的形成可能受阻并引起破裂。而且,熔融金属不是以可能的最佳状态分布。特别是到达上部的熔融金属太少,结果朝这一部分产生一个温度降。这在铸件的横断面上产生不均匀结晶。虽然可以使用插入流出口的配流管以将熔融金属送到铸模的离浇注口甚至更远的部位(德国书2,250,048号),然而,此时在紧靠浸入式浇注口的部位,有一个从浸入式浇注口出来的熔融金属不能直接到达的区域。本发明所依据的目标是提供一种浸入式浇注口,其类型在介绍中已提到,在该浇注口中,金属在浇铸开始的时候不会向上飞溅并在被冷却的模壁上结块,在通常的浇注过程中,熔融金属在铸模横断面上的分布比已知的浸入式浇注口效果更好。按照本发明,由于各流出口在上部有一个从浇注口壁上凸起的屋顶状导向件,以及在下部,有一个由底部和/或浇注口壁部形成的分离缘,该目标可以达到。在注模过程中,导向件防止熔融金属向上飞溅到被冷却的模壁的上部并在上面结块。当铸模被填充时,导向件保证熔融金属甚至达到铸模的狭窄的侧边的上部区域,这样,不会在此产生一个温度较低的区域。但是由于在下部的分离缘,熔融金属也能直接到达低于浸入式浇注口的部位,这样,熔融金属就在铸模的整个横断面上均匀地分布。按照本发明的一个实施例,如果各个屋顶状导向件延伸到下部的位于流出口两侧的分离缘的话,将会有助于熔融金属的均匀分布以及因此产生的铸模横断面上的温度的均匀分布。同时,在一个特别优越的实施例中,导向件侧向部分的自由缘到浇注口壁的距离,从导向件上部区域到位于流出口下部区域的分离缘,持续地减小。在一个合适的设计中,各分离缘位于一个垂直于浇注口的轴延伸的平面上。流出口上部应制成拱形。导向件本身最好与相关的流出口的形状相匹配。各流出口的内宽从上部朝分离缘逐步增加的话,这样熔融金属的均匀分布甚至能进一步得到改善。分离缘应当在浇注口的整个内宽上延伸。为保证熔融金属能更好地达到铸模的窄壁的上部,按照本发明的一个实施例,位于流出口之上的导向件的部分与其上面的浇注口的壁部形成一个锐角。一个大于70°的角已被证明是合理的。
如果底部在中心向浇注口内部朝上弯曲形成降至流出口的导向面,这对流动是有利的。
按照另一些实施例,流出口的内宽至多与决定铸件尺寸的铸模的宽侧壁下部之间的距离相等。
这样,在涉及到准备用于宽而薄的板形件浇铸模的场合,足够的熔融金属能被导入铸模,浸入式浇注口可如已知的那样,具有一个椭园形的横截面。在这种情况下,流出口开在壁部的具有较小曲率半径的部分。
本发明参考表示一个实施例的附图在下面加以详细说明。这些附图是图1表示的是依靠浸入式浇注口连续浇注薄板件的铸模,这是一个通过铸模的狭窄侧壁的纵向剖面。
图2表示的是按照图1的铸模,这是一个通过其宽侧壁的纵向剖面,图3表示的是图1的浸入式浇注口的沿轴向的剖面,图4是图3中沿流出口方向的浸入式浇注口的局部视图,图5是图3中沿剖切线Ⅴ-Ⅴ所得到的浸入式浇注口的横剖面。
一个具有一锥形头部的2′的浸入式浇注口2被固定在用于液态金属的浇口盘1的板上。浸入式浇注口2的下端伸入用于铸造大小最好在20-100mm的薄板件的铸模3内。铸模3是由二块相对的宽的侧壁4和两块相对的窄的侧壁5所构成。宽侧壁4和窄侧壁5装有冷却管6。在宽侧壁4的中心,决定铸件尺寸的平行部分7的上面,形成一个浇入区8,它向上增宽成漏斗状,用于容纳浸入式浇注口2的下端。
浸入式浇注口2具有一个椭园形横截面的流道,其下端面通过一底板13而被封闭。紧靠底板13的上面,在相对的具有较小曲率半径的两侧壁部上,设有拱形流出口11。由底板13形成的流出口11的下缘11′位于与浸入式浇注口2的轴线相垂直的平面上,并起着一种分离缘的作用。流出口11在分离缘11′处的最大宽度b等于或小于铸模3的决定铸件尺寸的平行部分7处的宽侧壁之间的内距d。底板13的内表面朝浸入式浇注口2的内部成弧形地向上弯曲,以形成顶点14。导向面14′从向上弯曲部分的顶点14成弧形地下降至分离缘11′。一个屋顶状的导向件15与拱形的流出口11的侧缘及顶缘相接。屋顶状导向件15的侧部15′的自由端11″,从离浇注口最远的上部15″到流出口11的下部的分离缘11′,成一斜角。屋顶状导向件15的上部15″有一个向上倾斜的方向,并与浸入式浇注口的轴线形成一个大于90°-α=70°的锐角。
在浇注开始时,流入浸入式浇注口2的熔融金属被底板13的弯曲部分的顶点14和导向面14′分开并通过流出口11流出。由于这一阶段,铸模还没有被流动衰减的熔融金属所充满,导向件15防止金属向上和向边上飞溅并在被冷却的宽侧边4和窄侧边5上结块。流出的熔融金属进入铸模3,在铸模3的壁上凝结并与一在底部封闭铸模3的挡板9连接。一当上升的浇注面10升到侧面流出口11以上时,即用铸造粉将其复盖。钢在被冷却的宽侧壁4和窄侧壁5上凝固,以形成薄壳体12,其厚度向下持续地增加。依靠由底板13所形成的分离缘11′,从流出口11流出的熔融金属能直接向下流动。各导向件15的侧部防止熔融金属直接流向附近的宽侧壁4,并与向前远远伸出的上部15″一起,保证熔融的金属流被导入位于窄侧壁5附近的上部区域。所有这一切,使在通常浇铸过程中,以这种方式保证了熔融金属对于侧部的最可能好的分布,同时在开始浇铸的时候,防止了熔融金属的飞溅和在被冷却的侧壁上结块。这意味着薄壳12能在整个周边均匀地凝固。
最后,熔融金属的流动以一种特殊的方式被引导向上,这使得消除朝着浇注面10的熔体的杂质成为可能。
本发明涉及的是用于将熔融金属,特别是钢水,在铸模内铸成薄板件的连续浇铸的浸入式耐火浇注口。该浸入式浇注口(2)在其端下由一底板13封闭,并具有两个相对的流出口11。同时,底板13的边缘形成一个对熔融金属的分离缘11′,分离缘11连接拱形流出口11的剩余边缘和一屋顶状的导向件15,导向件15的侧部15′具有从导向件15的上部15″外缘凸出的自由端11″,并朝下部的分离缘11′向下倾斜延伸。
浸入式耐火浇注口制作方法
- 专利详情
- 全文pdf
- 权力要求
- 说明书
- 法律状态
查看更多专利详情
下载专利文献
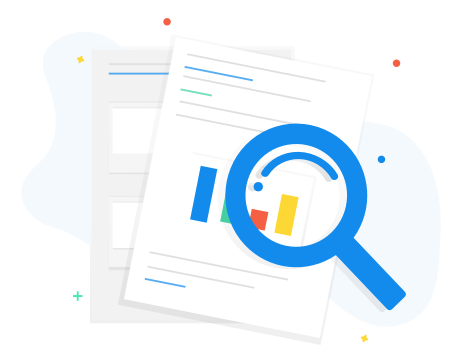
下载专利
同类推荐
-
赫曼·拉克斯, 卡尔·尤里克·科勒赫曼·拉克斯, 卡尔·尤里克·科勒陈永德付伟峰, 窦涛
您可能感兴趣的专利
-
付伟峰, 窦涛付伟峰, 窦涛付伟峰, 窦涛付伟峰, 窦涛T·海因斯沃思赵有恒
专利相关信息
-
顾华志顾华志顾华志张思坦