专利名称:低温练漂剂及其制备方法和前处理工艺的制作方法 棉纤维上含有0.4-1.2%的果胶质、0.4-1.2%的蜡质、1.0-1.9%的蛋白质、0.7-1.6%的灰分及少量的色素等天然杂质,称之为棉纤维的天然共聚物。这些杂质主要存在于棉纤维的角质层和初生胞壁中。它们的存在使棉具有疏水性,阻碍了染料的渗透和扩散。加之纺纱线进行上浆,人为地施加了浆料、抗静电剂和润滑剂。在染整时必须将杂质、浆料、油剂通过退浆、煮练、漂白三道工序予以去除,以保证棉的润湿、渗透性和白度,为后续染色、印花、整理创造必要条件。为了达到去除上述棉纤维内部与外部的杂质的目的,人们对棉和棉混纺织品的前处理通常采用如下传统工艺与相关技术条件(一)、以高温强碱煮练为主的退浆、煮练、漂白的前处理工艺该前处理工艺目前主要包括三种类型,具体如下(A)采用烧碱(氢氧化钠属强碱)与表面活性剂为煮练剂,双氧水为退浆剂与漂白剂的退、煮、漂同浴(即三合一工艺)的工艺路线; (B)采用烧碱与表面活性剂为煮练剂,亚氯酸钠为漂白剂的煮练、漂白分浴工艺;(C)采用烧碱与表面活性剂为煮练剂,先经次氯酸钠漂白后,再通过双氧水联合漂白的煮练、漂白分浴工艺;上述三种工艺路线均采用强碱与表面活性剂作煮练剂,其原理是利用以烧碱作为蛋白质、果胶、油蜡的水解剂和皂化剂,再用表面化活性剂将分解物乳化和分散而从棉纤维上去除。但这些反应都必须在高温下进行,因此传统煮练工艺都是在100℃,甚至135℃的高温高压设备中进行,另外,烧碱与纤维反应生成纤维钠及其他污物很难从织物上洗除,就必须用高温95℃热水大量冲洗,污水排放量也随之增加,则是总工艺的能耗及水量大量增加。由于选择三种不同漂白剂及其不同的漂白方法,其中以(B)种亚氯酸钠漂白白度最佳,但其分解物二氧化氯毒性很大,腐蚀设备与环境污染严重,损害人体健康;以(C)种采用次氯酸钠白度对环境最差,且还不能与煮练同浴进行,因而在氯漂之后通常增加一道工序氧漂处理,用于弥补不足之处,则使整个工艺流程长、能耗大,用水及排水量均增加等缺点;(A)种是采用双氧水漂白白度居中,用双氧水为漂白剂,还可将退浆、煮练和漂白三工序合为一,缩短时间,提高效益,但在低温时双氧水分散出的有效成分很慢,因而,双氧水的漂白作用须在95℃以上才能发挥。总之,这三种退浆、煮练和漂白的工艺类型均要求高温强碱,练漂时间为60-90分钟,耗用蒸汽量达1吨棉约需耗去了5~6吨蒸汽,占整个染整用汽量的60%左右。(二)、低温冷轧堆的练漂工艺该工艺是通过棉织物浸轧高浓度烧碱、双氧水和表面活性剂溶液,轧后打卷,冷堆16-24h,利用浓度高、反应时间长来达到反应的目的,但分解出来的杂质牢固地附在织物上,非用高温强力洗涤不可。因此练漂质量达不到中、高档产品的要求,使用受到限制。另外,因仍使用烧碱,它会与纤维素反应生成纤维素钠,不易从纤维上洗下来,练漂后必须反复用水洗涤,耗水量很大,练漂用水量约占整个染整用水量的50%左右,也相应地增加了污水排放量。节约用水,减少排污量,降低能耗已成为全球的共识,因此低温练漂工艺已成为当今研究的又一新热点现将已形成的专利归纳如下(1)采用生物酶进行低温煮练的专利如中国专利CN03118780.3《医用棉复合酶煮练氧漂工艺》;中国专利ZL0218527.5《一种全棉或涤/棉针织物氧化浸渍生物酶间隙前处理工艺》。上述两专利均利用以果胶酶与其他酶组成复合酶,对棉纤维进行低温煮练,该处理虽避免了传统工艺中所采用强碱强酸等化学助剂对棉纤维的损伤及高耗能的缺点,但因生物酶处理效果不佳,因此两专利均在酶处理的基础上,另增加了一道高温双氧水漂白,以弥补前者不足;又因酶是不耐高温、强碱及双氧水的,因而只能采用煮漂二浴法,未能达到降低能耗的目的,另外生物酶均有较强的专一性,导致其使用范围受限。(2)使用双氧水漂白活化剂进行低温漂白的专利如美国专利USP.6743761(2004.6.11)与USP.6830591(2004.12.14)上述两专利均使用了双氧水漂白活化剂壬酰氧苯磺酸盐(NOBS)或四乙酰乙二胺(TAED),由于这两种双氧水漂白活化剂均能激化其双氧水漂白有效分解率,大大降低双氧水分解温度,从而达到降低双氧水漂白的使用温度。前者采用NOBS与等摩尔比的双氧水一起在烧碱和表面活性剂存在下,与淀粉酶联合使用进行棉纤维70℃退浆与漂白一浴法,获得与传统工艺相同的白度和退浆率;后者使用TAED或NOBS于55-80℃进行棉的双氧水漂白,但此法中NOBS及TAED活化剂用量高达2点/升,温度越低则用量越高,增加了加工成本;另外,这些专利仅解决了双氧水低温漂白的难点,并未解决低温煮练的难点,因而更不可能实现棉的退、煮、漂三合一(即同浴)低温前处理工艺。
(3)以用于棉及棉混纺织品的退、煮、漂三合一的前处理工艺的低温练漂剂为目标的研究成果或专利目前尚未发现。
本发明的目的是在于提供一种低温练漂剂,以解决现有技术存在的上述问题,本发明的练漂剂除具有普通练漂剂的应有特性外,它还同时具有降低漂白处理温度与降低煮练处理温度的双重性能,且所制备的练漂剂易水洗、稳定性高、储存方便、使用量少,但效果明显,能改善坯布质量问题(减少破洞),可广泛用于棉与棉的混纺各类纺织品的退、煮、漂三合一(即同浴)的低温前处理的加工;也可分别取代传统相关助剂用于传统的煮练、漂白或练漂二合一的各类前处理工艺,提高传统工艺的原有质量水平;同时本发明练漂剂适用于各种常规的纺织品前处理加工设备上应用。
本发明的另一个目的是提供上述低温练漂剂的制备方法。
本发明还有一个目的是提供上述低温练漂剂的前处理工艺,包括用于棉与棉混纺各类纺织品,在各种常规纺织品前处理加工设备上进行的退,煮,漂三合一浸渍法的低温前处理工艺;全棉针织物的退,煮,漂三合一冷轧堆的低温前处理工艺;低温练漂剂取代传统相关助剂用传统煮练,漂白或练漂二合一的前处理工艺;其中所述各类纺织品为针织、机织、棉花、棉条及棉纱中任意一种;所述各种常规纺织品前处理加工设备为筒子染纱机、溢流喷射染机、绞盘或绳状染机等。
本发明低温练漂剂是由助剂QR2010、助剂QR2011及助剂QR2020三种分别制成的助剂所构成的混合助剂,按重量百分比上述三种助剂分别由以下组分组成
助剂QR2010复合有机溶剂 20-30%乳化剂 1-2.5%精练剂 20-30%水 37.5-59%在助剂QR2010混合乳液中,所述复合有机溶剂为四氯化碳、醋酸酯类化合物及烷基苯类化合物,三者按质量比为1-3∶0.5-1∶0.1-0.5配制而成复合有机溶剂,其中所述醋酸酯类化合物为醋酸乙酯、醋酸丁酯、醋酸异丁酯、醋酸戊酯、醋酸辛酯或醋酸异辛酯中任意一种;所述烷基苯类化合物为甲苯、二甲苯或三甲苯中任意一种;所述乳化剂为脂肪醇聚氧乙烯醚、蓖麻油聚氧乙烯醚、脂肪醇硫酸酯盐或脂肪醇聚氧乙烯醚硫酸酯盐中任意一种;所述精练剂为脂肪醇聚氧乙烯醚磷酸酯盐。
由于助剂QR2010乳液中,采用复合有机溶剂联合精练剂(碱剂)于低温下将蜡质、浆料、油剂、蛋白质、果胶进行萃取水解、皂化,再由乳化剂乳化分散而去除,因而本发明解决了低温煮练难点,为实现棉的退、煮、漂三合一同浴低温前处理工艺创造了必要条件。
助剂QR2011氢氧化钾 20-40%碳酸盐 10-30%渗透剂 2-10%水 20-68%在助剂QR2011混合碱液中,所述碳酸盐为碳酸钠、碳酸钾或碳酸氢钠中任意一种;所述渗透剂为脂肪醇聚氧乙烯醚、脂肪醇聚氧乙烯醚硫酸酯盐或脂肪醇聚氧乙烯醚磷酸酯盐中任意一种。由于助剂QR2011混合液中,采用氢氧化钾代替原用烧碱,减少了与纤维素反应生成纤维素钠的问题,使练漂后的污物很容易从组织物上洗除,从而减少了必须高温(95℃)洗的缺点,既节约能源,又节约用水和减少污水排放量,同时由于本发明碱剂选用了含铁离子较少与pH低的氢氧化钾,因而杜绝双氧水漂白时坯布易产生破洞,造成重大损失的坯疵的发生。
助剂QR2020双氧水酰类活化剂 10-20%双氧水腈类活化剂 5-15%助洗剂 65-85%在助剂QR2020混合物中,所述双氧水酰类活化剂为壬酰氧苯磺酸盐(NOBS)、四乙酰乙二胺(TAED)、N-酰基己内酰胺或乙酰化葡萄糖中任意一种;双氧水腈类活化剂为甜菜碱酰胺乙氨基腈盐酸盐;助洗剂为泡沸石。由于助剂QR2020混合物中,采用复合活化剂,即双氧水酰类活化剂与双氧水腈类活化剂,激化了双氧水分解活力,使双氧水的有效利用率提高,分解温度降低,从而达到低温漂白、去除色素的目的,同时比国外专利报道的用单个活化剂的用量大大降低,仅是国外用量的1/7至1/5,而效果显著提高,使双氧水漂白白度接近亚氯酸钠漂白水平。
本发明低温练漂剂的制备方法是首先分别各自配制助剂QR2010、助剂QR2011及助剂QR2020,并分别单个助剂的形式储存,使用时再按各自所需用量与双氧水共同配制成退、煮、漂三合一的前处理液,或者分别各自取代相关的助剂参与传统的煮练、漂白或练漂二合一的前处理液配制,现分别将三种助剂具体可由下述各自的方法制得(1)助剂QR2010的制备方法(a)按上述质量比将四氯化碳、醋酸酯类化合物及烷基苯类化合物混合后,制成复合有机溶剂混合液;(b)按上述重量百分比向该溶液中加入乳化剂;
(c)将该溶液搅拌10分钟后逐滴加入水,经乳化制得初步的油/水乳液;(d)按上述重量百分比向该溶液中加入精练剂;(e)以搅拌速度为1000~1200转/分,搅拌时间为30~45分钟高速搅拌乳液,与此同时升高乳液的温度,具体为50~60℃,并逐步滴完余下的水,即制成混合有机溶剂稠状乳液。
(2)助剂QR2011的制备方法(a)按上述重量百分比将氢氧化钾与碳酸盐溶解于水中,形成碱溶液;(b)按上述重量百分比将渗透剂加入到上述溶液中;(c)将该溶液加热至60℃,搅拌30~40分钟;(d)在继续搅拌的同时,开动外环水,使该溶液冷却至室温;(e)经过滤去杂、出料制得碱剂的混合液。
(3)助剂QR2020的制备方法按上述重量百分比将双氧水酰类活化剂、双氧水腈类活化剂与事先已粉碎的助洗剂这三种化学品均放入捏和机内均匀混合,为防止物尘飞扬,在混合的同时则不断喷淋水雾,混合时间为30~50分钟,最后经烘干得30~40(目)的固体粉末。
本发明低温练漂剂的前处理工艺是包括以下三种(一)全棉或棉混纺织品的退,煮,漂三合一浸渍法的低温前处理工艺工艺流程浸渍退,煮,漂液→排液→水洗→排液→中和去氧;浸渍将1份重量的全棉或棉混纺物浸渍于15份重量的已配制好的退、煮、漂浸渍液中,在浸渍温度为40~80℃条件下,经浸渍60~90分钟后,排出浸渍残液,即得经前处理后的全棉或棉混纺物,其中所述退、煮、漂浸渍液是由助剂QR2010 0.8~1.2克/升,助剂QR2011 2.5~3克/升及助剂QR2020 0.4~1.5克/升,三个助剂与双氧水(100%)2~10克/升共同配制而成的,所述全棉或棉混纺物为针织物、梭织物、棉花、棉条或棉纱中任意一种;上述前处理工艺所用设备为筒子染纱机、溢流喷射染机、绞盘或绳状染机中任意一种。
水洗将上述已经处理但仍带有浓前处理浸渍液的全棉和棉混纺物,先用温度为60℃的请水洗,15分钟后再排残液;中和去氧将上述已热水洗过的全棉和棉混纺物,先经酸中和其残碱,并用常规方法去除其残留双氧水,再经干燥后,可直接用于染色加工,所得纺织物经检测,其烘干(105℃)毛效为14厘米以上/30分钟,白度为80~84%。
(二)全棉针织物的退,煮,漂三合一冷轧堆的低温前处理工艺工艺流程 浸轧→堆置→热水洗→温水洗→酸中和;浸轧将全棉针织坯布浸入储有按比例配的浸轧液的浸液槽,再经轧机均匀地轧去多余的浸轧液轧后打卷,得到含有轧余率为130--150%的浸轧液的全棉针织坯布卷,其中,所述配制浸轧液为助剂QR2010 3~4克/升,助剂QR2011 16~20克/升,助剂QR20202~4克/升,双氧水(100%)22~25克/升;堆置在室温下将含有浸轧液全棉针织坯布卷堆置2~4小时;热水洗将上述以堆置完毕的针织坯布卷,在助剂QR20110.6克/升与助剂QR2010 0.5克/升的洗液内进行热洗处理,其工艺条件为洗涤温度为90~95℃,洗涤时间为10~20分钟;温水洗将上述经热洗后全棉针织坯布,再进一步用温水洗涤,其洗涤温度为60℃,洗涤时间为20分钟;中和再次水洗,并用酸中和至PH=6~7的水进一步洗涤后排液,烘干制得经退,煮,漂三合一冷轧堆的低温前处理的全棉针织坯布,经检测,其烘干(105℃),毛效为18~20厘米/30分,白度为80~84%。
(三)低温练漂剂取代传统相关助剂用于传统煮练,漂白或练漂二合一的前处理工艺(A)将助剂QR2010添加于传统工艺中取代精练剂,其用量为1~1.5克/升,用以提高坯布毛效(即毛细管效应);(B)将助剂QR2011添加于传统工艺中取代烧碱(氢氧化钠),其用量为2.5~4克/升,以提高坯布的易洗性,节约用水和消灭氧漂破洞;(C)将助剂QR2020添加到传统浸渍工艺中,其用量为0.3~0.4克/升,以缩短练漂时间或降低练漂温度;或添加到传统冷轧堆工艺中,其用量为2~4克/升,以缩短堆置时间。
本发明与现有技术相比有如下优点(1)由于本发明的低温练漂剂具有降低漂白处理温度与降低煮练处理温度的双重特性,因而首次打破了不能在低温下必须在高温100℃以上对全棉与棉混纺织品的退煮漂三合一的前处理工艺条件的禁区,实现了在温度为40~80℃下对全棉与棉混纺物的进行退煮漂三合一的前处理的可能性。
(2)本发明不仅实现了退浆,煮练,漂白三工序均能用低温处理,而且均使三工序在同浴与同一温度下进行三个工序的处理,因此本发明的前处理工艺效果明显.具体有如下几个方面1)总能耗低,从原1吨棉耗蒸汽量5~6吨降到1.2~3.5吨,若使用40℃工艺仅耗用1吨多蒸汽,节能更可观,一般蒸汽耗用量降低40~80%;2)用水量低,因本助剂易水洗,因而减少水洗次数,特别是筒子纱的练漂,从原水洗20次改为8次,使原有1吨棉用水量从60吨降至30吨,排水量也相应减少,一般用水量、排水量减少30~50%;3)质量明显提高,老工艺其毛效一般仅3~6厘米/30分,而本发明处理过坯布的毛效可达10~20厘米以上/30分钟,这时为后工序染色提高质量打好基础,可使染色均匀,减少染花,在筒子纱染色尤为明显;4)加工时间少,如冷轧堆加工,从原有堆量时间16~24时缩短4小时,可实现在同一生产班次内自漂自染的优点;5)减少坯布疵点,由于减剂改用氢氧化钾铁离子较少且PH低,不会出现氧漂破洞,又由于处理温度低于100℃,可减少莱卡棉混纺物练漂时造成的死绉印;6)双氧水活化剂用量仅是原有的1/7至1/5,降低成本,效果显著提高,使双氧水漂白白度接近亚氯酸钠漂白水平。
(3)则须调整助剂用量,可在前处理温度为40~80℃之间内选择任意温度下处理,为印染厂选择最佳工艺创造了条件。
(4)本发明低温练漂剂及前处理工艺的适用面广,灵活性好,对各类全棉与棉混纺产品均适用,同时适用各种常规前处理加工设备上应用,不仅适用退煮漂三合一工艺,而且也可用在传统煮练,漂白与练漂的前处理工艺上,特别是适合于当前多品种小批量交货期短的生产。
(5)本发明所用化学品均属环保型。
实施例1低温练漂剂的制备方法(A)助剂QR2010的制备复合有机溶剂30%平平加(乳化剂) 1%脂肪醇聚氧乙烯醚磷酸酯盐(精练剂)20%水 49%a)将四氯化碳、醋酸辛酯与二甲笨按质量比为1∶0.8∶0.2混合配制成有机溶剂混合液;b)向上述混合液中加入按重量百分比为1%的平平加(乳化剂);c)搅拌10分钟后逐滴滴加入水,经乳化剂得初步的油/水乳液;
d)向上述混合乳液中加入按重量百分比为20%的精练剂;e)以搅拌速度为1100转/分,搅拌时间为40分钟高速搅拌乳液,与此同时升高乳液的温度至55℃,并逐步滴完余下的水,即制成混合有机溶剂稠状乳液。
(B)助剂QR2011的制备方法氢氧化钾 30%碳酸镁 20%(渗透剂)脂肪醇聚氧乙烯醚磷酸酯盐 10%水 40%a)按重量百分比为30%的氢氧化钾与重量百分比为20%的碳酸镁溶解于水中,形成碱溶液;b)按重量百分比为10%的渗透剂加入到上述溶液中;c)将该溶液加热至60℃,搅拌30~40分钟;d)在继续搅拌的同时,开动外环水,使该溶液冷却至室温;e)经过滤去杂、出料制得碱剂的混合液。
(C)助剂QR2020的制备方法N-乙酰葡萄糖(双氧水酰类活化剂)20%甜菜碱酰胺乙氨基腈盐酸盐(双氧水腈类活化剂) 10%泡沸石 70%按重量百分比为20%的N-乙酰葡萄糖、10%甜菜碱酰胺乙氨基腈盐酸盐与70%泡沸石,双氧水酰类活化剂、双氧水腈类活化剂与事先已粉碎的助洗剂这三种化学品均放入捏和机内均匀混合,为防止物尘飞扬,在混合的同时则不断喷淋水雾,最后经烘干得30~40(目)的固体粉末。
实施例2.32s全棉筒子纱(80℃)练漂双氧水(27.5%) 6.0ml/LQR2010 1.0g/LQR2011 2.5g/LQR2020 0.5g/L
浴比1∶15温度80℃时间70min水洗次数2次白度80.9%毛效14.8cm工艺流程40℃时配液,升温到80℃,练漂70min→排液→热水洗(60℃×15min)排液→冷水洗(包括酸中和及去氧处理、而后加染料染色)对比实例在同一设备上,相同织物的传统工艺双氧水(27.5%) 6.0ml/L36°Be′NaOH 4.0ml/L精练剂 1.0g/L氧漂稳定剂 1.0g/L螯合剂 1.0g/L浴比 1∶15温度 100℃时间 40min水洗次数 5次白度 79%毛效 8.2cm工艺流程40℃时配液,升温到100℃,练漂60min→排液→热水洗(95℃×15min)→排液→热水洗(80℃×5min)→排液→冷水洗→排液→冷水洗→排液→酸中和及去氧处理,而后加染料染色。
实施例3.全棉21s纱毛巾及32s线毛巾的(80℃)练漂与增白工艺参比实例(老工艺)低温练漂实例(新工艺)双氧水(27.5%) 15.0ml/L15.0ml/LQR2010 / 1.0g/LQR2011 / 2.5g/LQR2020 / 0.5g/L26°Be′NaOH10.0ml/L/精练剂 0.5g/L /氧漂稳定剂701 4.0g/L /六偏磷酸钠 0.5g/L /棉用增白剂 0.36%(o.w.f.) 0.36%(o.w.f.)浴比1∶12 1∶12
温度100℃ 80℃时间120min(线毛巾) 90min(线毛巾)140min(纱毛巾) 90min(纱毛巾)水洗次数6次 2次白度85%89%毛效6.0cm 18cm实施例4.全棉莱卡汗布(32s×20D OP)(80℃)练漂工艺参比实例(老工艺) 低温练漂实例(新工艺1) 低温练漂实例(新工艺2)双氧水(35%) 4.0ml/l 4.0ml/l6.2ml/l精练剂 0.3g/l/ /稳定剂SIFA 0.53g/l / /除油剂ESN 1.3g/l/ /(36°Be′)NaOH 4.0g/l/ /QR2010 / 1.0g/l 1.0g/lQR2011 / 3.0g/l 3.0g/lQR2020 / 0.5g/l 0.5g/l温度 100℃ 80℃ 80℃时间 45min 70min 70min浴比 1∶15 1∶15 1∶15水洗次数 3次 1次1次白度 78% 80% 84%毛效 8.0cm 14cm 15cm实施例5.全棉21s汗布(60℃、40℃)练漂工艺参比实例(老工艺) 低温练漂实例(60℃) 低温练漂实例(40℃)双氧水(27.5%) 6.0ml/l 16.0ml/l50ml/l精练剂A0.3g/l/ /抗绉剂A2.0g/l/ /(36°Be′)NaOH 4.0g/l/ /QR2010 / 1.0g/l 1.0g/lQR2011 / 3.0g/l 3.0g/lQR2020 / 0.5g/l 0.5g/l浴比 1∶12 1∶12 1∶12温度 100℃ 60℃40℃时间 60min 80min 80min水洗次数 5次 2次 2次白度 73% 75%70%毛效 8.0cm 13cm11cm
实施例6.全棉针织布冷轧堆练漂工艺参比实例(老工艺) 新冷轧堆练漂实例双氧水(100%) 16-18ml/l 16-18ml/l冷堆剂QR-OK 10g/l /保护碱A-551 5g/l /(36°Be′)NaOH20g/l /低温练漂剂QR2010 / 3-6g/l低温练漂剂QR2011 / 16-20g/l低温练漂剂QR2020 / 2-4g/l浸轧温度 20℃ 20℃轧余率100-120% 100-120%堆置温度 30℃ 30℃堆置时间 20h 4h水洗次数 5次 3次白度 67% 75%毛效 8.0cm 15cm参比实例(老)工艺流程浸轧练漂液→堆置(20h)→热洗(36°Be′NaOH 2g/l,冷堆剂QR-OK 0.5g/l,95℃×15min)→排液→热水洗(80℃×10min)→排液→温水洗(60℃×15min)→排液→冷水洗10min→排液→冷水洗10min,加醋酸中和→排液新冷轧堆练漂实例工艺流程浸轧练漂液→堆置(4-6h)→热洗(36°Be′NaOH 2g/L,QR-20100.5g/L,95℃×15min)→排液→温水洗(60℃×20min)→排液→冷水洗10min,加醋酸中和→排液。
本发明涉及纺织印染行业前处理工艺技术领域内一种低温练漂剂及其制备方法和前处理工艺。该低温练漂剂是由助剂QR2010、助剂QR2011与助剂QR2020所组成的,其中QR2010为四氯化碳、醋酸酯类、烷基苯类、乳化剂与精练剂组成,QR2011为氢氧化钾、碳酸盐与渗透剂组成,QR2020为酰类与腈类活化剂及助洗剂组成,三助剂通过常规方法分别制成单独储存,使用时再与双氧水一起以不同比例配液,可在40~80℃间任意一温度下进行各类棉及棉混纺物的退,煮,漂,能在不同练漂设备上加工,白度80%以上,毛效为10~20厘米;与现工艺相比,双氧水活化剂用量仅是原有的1/7至1/5,总能耗低,用水排水量低,可杜绝氧漂破洞与莱卡练漂折绉等坯疵。
低温练漂剂及其制备方法和前处理工艺制作方法
- 专利详情
- 全文pdf
- 权力要求
- 说明书
- 法律状态
查看更多专利详情
下载专利文献
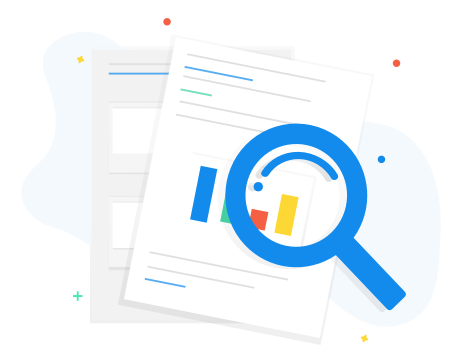
下载专利
同类推荐
-
奉明明马蒂亚斯·布兰德尔马蒂亚斯·布兰德尔新津洋司郎新津洋司郎新津洋司郎
您可能感兴趣的专利
-
刘静, 邓中山加藤行加藤行曹仁镐, 韩东柱崔昌奎
专利相关信息
-
刘光明章小龙, 茅建刚朱秀红王建设, 王琳壮晓健