高压坐便器自动成型系统的制作方法【技术领域】,尤其是一种高压坐便器自动成型系统。[0002]传统的卫生洁具高压注浆设备在生产过程中,坐便器本体、坐便器圈体都是单独成型,然后人工进行粘结组装,组装时要经过多次的搬倒、运输以及粘结等多道工序,不但效率低,而且需要大量的人力,已经不适合现代化的生产节奏,在生产技术快速发展的今天,很有必要建立现代化的自动生产设备,以满足生产的需要。[0003]同时,现有技术中采用石膏模型微压注浆的生产方式,虽然产品能够一次成型,但是每套模型每天只能注浆一次,效率低下,空间利用率低,而且模型尺寸大,非常笨重,模具合模、锁紧、开模、脱模工序均需采用人工助力机械逐个操作,操作起来麻烦,成品率低,对员工身体素质、操作熟练程度要求很高;另外,模型需通过高温干燥,能源消耗较大。从传统的成型工序的这些缺陷来说,建立自动化的生产设备也是非常必要的。
[0004]本发明要解决的技术问题是提供一种高压坐便器自动成型系统,实现坐便器本体和坐便器圈体同时成型,并且能够自动化粘接,大大提高生产效率,降低能耗,提高成品率。[0005]为解决上述技术问题,本发明所采取的技术方案是:一种高压坐便器自动成型系统,包括底座、门形主框架、喷泥装置、坐便器本体高压成型机、坐便器圈体高压成型机以及移载机,所述门形主框架一侧的两个支腿与底座铰接,其另外一侧两个支腿借助于倾斜油缸与底座铰接,所述四个支腿与底座之间铰接轴的轴线相互平行,所述坐便器本体高压成型机和坐便器圈体高压成型机均设于门形主框架内侧,所述喷泥装置固定设于门形主框架一侧,所述移载机借助于轨道设于门形主框架另外一侧。[0006]所述坐便器本体高压成型机包括上型推进板、侧型推进板、侧型加压油缸、下型推进板、下型油缸、侧型气缸、高压成型机线性导轨、坐便器本体模具、上型油缸、侧型锁、侧型小车、上下型加压油缸;上型推进板借助于坐便器本体行走小车设于主框架横梁下方,下型推进板位于上型推进板正下方、且与坐便器本体高压成型机线性导轨连接,侧型推进板分别位于主框架的左右两侧,上型油缸竖向固定于坐便器本体行走小车上,其下端与上型推进板铰接,下型油缸缸体与主框架连接,活塞杆与下型推进板连接,侧型气缸对称设置两套,两套侧型气缸的缸体均与主框架两端支腿之间的小横梁连接,活塞杆与侧型推进板铰接,侧型加压油缸位于其中一块侧型推进板上,侧型锁位于另外一块侧型推进板上、且位于两块侧型推进板之间,侧型锁轴线与侧型加压油缸轴线重合,两套双出杆的上下型加压油缸安装在两个侧型推进板上表面上,所述门形主框架两端支腿之间设有侧型小车滑轨,所述两个侧型推进板下端均设有与侧型小车滑轨配套的侧型小车。
[0007]所述坐便器圈体高压成型机包括坐便器圈体模具和开合锁模装置,所述开合锁模装置包括圈体上型推进板、圈体下型推进板、圈体上型油缸、圈体加压油缸和圈体倾斜气缸,所述圈体上型推进板借助于圈体行走小车设于门形主框架横梁下方,圈体下型推进板位于圈体上型推进板的正下方、且与圈体上型推进板之间设置圈体加压油缸,所述圈体下型推进板两端与门形框架外侧支架铰接,所述圈体倾斜气缸位于圈下型推进板下方,圈体倾斜气缸的缸体与门形主框架外侧支架铰接,其活塞端部与圈下型推进板一端下部铰接。
[0008]所述圈体上型油缸竖向设置,其缸体与圈体行走小车连接,其活塞杆下端铰接吊架,所述吊架下方固定设有四套呈矩形水平布设的悬挂气缸,四套悬挂气缸的轴线相互平行、且活塞杆端部均向内设置,四套悬挂气缸相互之间的间距与圈体上型推进板上表面设置的四套吊耳相互之间的间距相同。
[0009]所述本体行走小车包括本体行走小车减速机、同步带,、主动轮、从动轮以及小车主体;所述的圈体行走小车包括圈体行走小车减速机、圈体行走小车主动轮、圈体行走小车从动轮、同步带以及小车主体;所述本体行走小车减速机和圈体行走小车减速机分别安装在门形主框架横梁两端、且均与横梁上表面上设置的行走轨道滑动配合,本体行走小车减速机和圈体行走小车减速机均通过带传动机构驱动小车主体运动。
[0010]所述喷泥装置包括机械手、机械手底座、喷泥压力罐和喷泥嘴,机械手安装于机械手底座上,喷泥嘴固定于机械手腕部,喷泥压力罐出口与喷泥嘴用软管连接。
[0011]所述移载机包括移载机框架、驱动装置、移载机直线导轨、取坯叉子和升降气缸,驱动装置包括移载机减速机、移载机主动轮和移载机从动轮;取坯叉子在移载机框架前方,驱动装置在移载机框架下方,升降气缸在移载机框架中心,移载机直线导轨固定设于移载机框架前方侧面;移载机减速机通过链传动机构与移载机从动轮连接,所述取坯叉子与移载机直线导轨滑动配合,所述升降气缸的活塞杆顶端与取坯叉子下端铰接。
[0012]本发明的有益效果如下:
(I)通过在系统中同时设置坐便器本体高压成型机和坐便器圈体高压成型机,单独操作,通过使用模具注浆成型,摒弃现有的石膏模具成型方法,大大提高作业效率和成品率。
[0013](2)本发明通过自动化控制实现坐便器本体和坐便器圈体自动化粘接,在同一系统内集成成型和粘接工序,提高作业效率,避免在不同系统中成型和粘接过程中的搬运,降低劳动强度。
[0014](3)本发明还通过设置移载机实现粘接成型的坐便器自动搬运移位,提高系统自动化生产程度。
[0015]图1是本发明主视图;
图2是本发明左视图;
在附图中:1-圈体共注坐便器高压成型机、2-喷泥装置、3-移载机、4-门形主框架、5-本体行走小车、6-传动组件、7-主动轮、8-从动轮、9-同步带、10-坐便器本体高压成型机、11-上型推进板、12-侧型推进板、13-侧型加压油缸、14-下型推进板、15-下型油缸、16-侧型气缸、17-高压成型机线性导轨、18-坐便器本体模具、19-上型油缸、20-带座轴承、21-倾斜油缸、22-坐便器圈体高压成型机、23-圈体上型推进板、24-圈体下型推进板、25-悬挂气缸、26-圈体倾斜气缸、27-圈体上型油缸、28-圈体行走小车、29-取坯叉子、30-驱动装置、31-移载机减速机、32-移载机框架、33-移载机直线导轨、34-升降气缸、35-移载机主动轮、36-移载机从动轮、37-机械手底座、38-机械手、39-喷泥压力罐、40-喷泥嘴、41-圈体行走小车减速机、42-侧型锁、43-坐便器圈体模具、44-侧型小车、45-轨道、46-本体行走小车减速机、47-圈体行走小车主动轮、48-上下型加压油缸、49-圈体加压油缸、50-底座。
[0016]下面结合附图和对本发明作进一步详细的说明。
[0017]综上所述,本发明公开了一种高压坐便器自动成型系统,通过将坐便器本体高压成型机和坐便器圈体高压成型机集成到同一系统中,并且实现坐便器本体和坐便器圈体自动化粘接和移位,大大提高作业效率和成品率,降低劳动强度,其具体方案如下:
一种高压坐便器自动成型系统(参见附图1和附图2),包括底座50、门形主框架4、喷泥装置2、坐便器本体高压成型机10、坐便器圈体高压成型机22以及移载机3,所述门形主框架4 一侧的两个支腿与底座50铰接,其另外一侧两个支腿借助于倾斜油缸21与底座50铰接,所述四个支腿与底座之间铰接轴的轴线相互平行,所述坐便器本体高压成型机10和坐便器圈体高压成型机22的上型均借助于驱动装置可滑动地设于门形主框架4内侧,所述喷泥装置2固定设于门形主框架4 一侧,所述移载机3借助于轨道45设于门形主框架4另外一侧,门形主框架内设置坐便器本体高压成型机和坐便器圈体高压成型机,两者同时独立成型,然后通过设于门形主框架的本体行走小车和圈体行走小车移动成型部件,并将两者对位以后进行粘接,粘接完成的坐便器可以使用移载机移至下一工序,设备启动后全自动运行,无需搬运和人工粘接,一方面提高工作效率,另外一方面提高成品率,降低劳动强度。
[0018]所述坐便器本体高压成型机10包括上型推进板11、侧型推进板12、侧型加压油缸13、下型推进板14、下型油缸15、侧型气缸16、高压成型机线性导轨17、坐便器本体模具18、上型油缸19、侧型锁42、侧型小车44、上下型加压油缸48 ;上型推进板11借助于坐便器本体行走小车设于主框架横梁下方,下型推进板14位于上型推进板11正下方、且与坐便器本体高压成型机线性导轨17连接,侧型推进板12分别位于主框架4的左右两侧,上型油缸19竖向固定于坐便器本体行走小车上,其下端与上型推进板11铰接,下型油缸15缸体与主框架4连接,活塞杆与下型推进板14连接,侧型气缸16对称设置两套,两套侧型气缸16的缸体均与主框架4两端支腿之间的小横梁连接,活塞杆与侧型推进板12铰接,侧型加压油缸13位于其中一块侧型推进板12上,侧型锁42位于另外一块侧型推进板12上、且位于两块侧型推进板12之间,侧型锁42轴线与侧型加压油缸13轴线重合,两套双出杆的上下型加压油缸48安装在两个侧型推进板12上表面上,所述门形主框架4两端支腿之间设有侧型小车滑轨,所述两个侧型推进板12下端均设有与侧型小车滑轨配套的侧型小车44,坐便器本体高压成型机主要是利用由油缸驱动的模板拼装成的模型进行注浆的,与现有石膏模具相比,生产效率更高。
[0019]所述坐便器圈体高压成型机22包括坐便器圈体模具43和开合锁模装置,所述开合锁模装置包括圈体上型推进板23、圈体下型推进板24、圈体上型油缸27、圈体加压油缸49和圈体倾斜气缸26,所述圈体上型推进板23借助于圈体行走小车28设于门形主框架横梁下方,圈体下型推进板24位于圈体上型推进板23的正下方、且与圈体上型推进板23之间设置圈体加压油缸49,所述圈体下型推进板24两端与门形框架4外侧支架铰接,所述圈体倾斜气缸26位于圈下型推进板24下方,圈体倾斜气缸26的缸体与门形主框架4外侧支架铰接,其活塞端部与圈下型推进板24 —端下部铰接。
[0020]所述圈体上型油缸27竖向设置,其缸体与圈体行走小车28连接,其活塞杆下端铰接吊架,所述吊架下方固定设有四套呈矩形水平布设的悬挂气缸25,四套悬挂气缸25的轴线相互平行、且活塞杆端部均向内设置,四套悬挂气缸25相互之间的间距与圈体上型推进板23上表面设置的四套吊耳相互之间的间距相同,由于圈体成型以后需要和坐便器本体对位,因此其是可以通过倾斜气缸推动器旋转,同时也可以通过悬挂气缸实现与主体对位。
[0021]所述本体行走小车5包括本体行走小车减速机46、同步带9,、主动轮7、从动轮8以及小车主体;所述的圈体行走小车28包括圈体行走小车减速机41、圈体行走小车主动轮47、圈体行走小车从动轮8、同步带以及小车主体;所述本体行走小车减速机46和圈体行走小车减速机41分别安装在门形主框架4横梁两端、且均与横梁上表面上设置的行走轨道滑动配合,本体行走小车减速机46和圈体行走小车减速机41均通过带传动机构驱动小车主体运动。
[0022]所述喷泥装置2包括机械手38、机械手底座37、喷泥压力罐39和喷泥嘴40,机械手38安装于机械手底座37上,喷泥嘴40固定于机械手38腕部,喷泥压力罐39出口与喷泥嘴40用软管连接,机械手通过控制系统控制,其运行轨迹是根据所加工的坐便器尺寸和形状进行设定的。
[0023]所述移载机3包括移载机框架32、驱动装置30、移载机直线导轨33、取坯叉子29和升降气缸34,驱动装置30包括移载机减速机31、移载机主动轮35和移载机从动轮36 ;取坯叉子29在移载机框架32前方,驱动装置30在移载机框架32下方,升降气缸34在移载机框架32中心,移载机直线导轨33固定设于移载机框架32前方侧面;移载机减速机31通过链传动机构与移载机从动轮35连接,所述取坯叉子29与移载机直线导轨33滑动配合,所述升降气缸34的活塞杆顶端与取坯叉子29下端铰接,移载机的作用在于能够将粘接完成的坐便器安全移动至下一工序,其主要包括行走系统和升降系统,升降是通过气缸实现,行走是通过电动机驱动。
[0024]在具体应用过程中:首先,坐便器本体高压成型机10、坐便器圈体高压成型机22同时工作,上型推进板11、下型推进板14通过上下型加压油缸48锁紧,侧型推进板12通过各侧型油缸13锁紧,圈体上型推进板23、圈体下型推进板24通过圈体加压油缸49锁紧,悬挂气缸25松开,圈体上型推进板23与上型油缸27分离,翻转气缸26推动圈体下型推进板23及坐便器圈体模具43旋转90°,倾斜油缸21推动主框架4以带座轴承20为中心旋转一定角度,注浆成型,旋转的目的是为了方便成型注浆,注浆成型以后复位,并由坐便器圈体行走小车和圈体上型将成型的坐便器圈体移动至坐便器本体上方对接。
[0025]坐便器本体高压成型机10的上型推进板11通过上型油缸19提升,翻转气缸26将坐便器圈体高压成型机22复位,悬挂气缸25将圈体上型推进板23与圈体上型油缸27固定,圈体上型油缸27将圈体上型推进板提升至上限高度。
[0026]本体行走小车减速机46带动同步带9运行,同步带9带动本体行走小车5向左侧行走(如图1所示),机械手38带动喷泥嘴40在坐便器本体高压成型机10内运动,将喷泥压力罐39内泥浆沿坐便器本体外延轨迹通过喷泥嘴40均匀喷涂在坐便器本体上;机械手38喷泥动作完成后回到初始位置,圈体行走小车减速机41带动同步带运行,同步带带动圈体行走小车28行走至坐便器本体高压成型机10正上方;圈体上型油缸27下降,圈体与坐便器本体粘结,之后圈体上型油缸27上升,圈体行走小车28复位,下型油缸15带动下型推进板14下降至下限位位置。
[0027]移载机3通过驱动装置30移动至坐便器本体高压成型机10正前方,升降气缸34将取坯叉子29送至下型推进板14正上方,坐便器本体下方;侧型加压油缸13泄压,侧型锁42打开,侧型气缸16分别将侧推进板12拉开至初始位置实现脱模,坐便器本体放置于移载机3的取坯叉子29上,移载机3通过驱动装置30回到初始位置,升降气缸34下降初始位置,完成一次成型和粘接,设备复位,进行下一循环,为了实现自动化控制,本发明还包括控制系统,控制系统包括PLC控制单元、触摸屏、中间继电器、气动电磁阀、液压电磁阀以及交流接触器,PLC控制单元通过中间继电器控制气动电磁阀、液压电磁阀和交流接触器,气动电磁阀控制系统中对应的气缸,液压电磁阀控制系统中对应的液压缸,交流接触器控制驱动电机,实现全自动化控制,提高生产效率。
[0028]总之,本发明通过在系统中同时设置坐便器本体高压成型机和坐便器圈体高压成型机,单独操作,通过使用模具注浆成型,摒弃现有的石膏模具成型方法,大大提高作业效率和成品率;通过自动化控制实现坐便器本体和坐便器圈体自动化粘接,在同一系统内集成成型和粘接工序,提高作业效率,避免在不同系统中成型和粘接过程中的搬运,降低劳动强度,还通过设置移载机实现粘接成型的坐便器自动搬运移位,提高系统自动化生产程度。
高压坐便器自动成型系统制作方法
- 专利详情
- 全文pdf
- 权力要求
- 说明书
- 法律状态
查看更多专利详情
下载专利文献
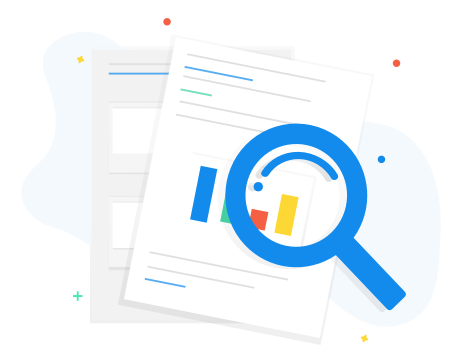
下载专利
同类推荐
-
杜伟建彭威周耀恩, 罗庆秦升益秦升益秦升益
您可能感兴趣的专利
-
丁伟丁伟孙克林王小锋周芸, 黄勇
专利相关信息
-
周芸, 黄勇李欢欢