专利名称:用含沉积物湿法磷酸生产高养分磷铵的系统及方法湿法磷酸是生产磷酸一铵和磷酸二铵的主要原料。由于湿法磷酸是用浓硫酸分解磷矿石得到的,其中含有大量的不溶物及沉积物,如果不及时分离就会对产品质量产生较大影响,同时生产系统中的酸储槽会产生“坐槽”现象,在酸储槽内产生沉积物,对生产影响较大。现有的生产系统中没有处理该沉积物的系统,通常是直接用泵将该沉积物输送到反应过滤机对五氧化二磷进行洗涤回收,将洗涤后的酸渣输送至渣场堆放,但由于洗涤不够彻底使磷损过高造成效益流失,同时还造成浓酸供量不足影响下工序产能发挥。目前,国内也有些企业将酸储槽内的沉积物分离后,用来生产低养份磷酸二铵或磷酸一铵。但是,对于没有生产磷酸一铵系统的企业来说,用酸储槽内的沉积物生产64%养分磷酸二铵困难极大
为了克服上述现有技术中存在的问题,本发明的目的在于提供一种用含沉积物湿法磷酸生产高养分磷铵的系统,能用酸渣生产64%养分的磷铵,在磷酸达不到要求的情况下,保证了磷铵的养分。本发明的另一目的是提供一种利用上述生产系统生产合格养份磷铵的方法,解决了大型湿法磷酸系统磷酸澄清槽中沉积物处理问题,同时不影响64%养分磷铵产品的生产。为实现上述目的,本发明所采用的技术方案是一种用含沉积物湿法磷酸生产高养分磷铵的系统,包括依次相连接的酸储槽、第一离心泵、澄清槽和第一渣浆泵,澄清槽通过第二离心泵与供酸槽相连接,供酸槽还分别与输酸泵和第二渣浆泵相连接,输酸泵与磷铵装置相连接;第二渣浆泵与储酸槽相连接。所述的酸储槽为带有搅拌桨的储酸槽。本发明所采用的另一技术方案是一种利用上述生产系统生产64%养分磷铵的方法,具体按以下步骤进行步骤I :将新产浓磷酸送入供酸槽,例行取样分析,若该新产浓磷酸的指标合格,则将供酸槽内的浓磷酸送去磷铵系统生产64%养份磷铵;若送入供酸槽的新产浓磷酸的指标不合格,则将供酸槽内的新产浓磷酸和供酸槽底部含沉积物的浓磷酸连续送入酸储槽中持续搅拌,并送至澄清槽内;步骤2 :含沉积物的磷酸在澄清槽内澄清24小时以上,形成上层澄清磷酸和酸渣; 将酸渣送往反应过滤系统;对上层澄清磷酸进行取样分析;若该上层澄清磷酸的指标合格,则备用;若该上层澄清磷酸的指标不合格,采取继续沉降并连续排浆的方法,直至上层澄清磷酸的指标合格; 步骤3 :对送入供酸槽的新产浓磷酸进行取样分析,根据新产浓磷酸的分析数据确定从澄清槽送入供酸槽的上层澄清磷酸的用量,然后将相应用量的指标合格的上层澄清磷酸送入供酸槽,与新产浓磷酸进行配酸,形成浓度符合要求的浓磷酸;将供酸槽液位50%以上的符合要求的浓磷酸送去磷铵系统生成64%养分磷铵;再将供酸槽底部含沉积物的磷酸送入带酸储槽。本发明生产系统,合理利用含沉积物磷酸生产64%养分磷铵,为湿法磷酸生产过程中处理磷酸沉积物提供了一条途径,每年创造的经济效益可观,同时回收了部分P2O5,减少了企业效益流失。图I是本发明生产系统的结构示意图。图中1.酸储槽,2.第一离心泵,3.澄清槽,4.第一渣浆泵,5.第二离心泵,6.磷铵装置,7.输酸泵,8.供酸槽,9.第二渣浆泵。
下面结合附图和
对本发明进行详细说明。如图I所示,本发明生产系统的结构,包括依次相连接的酸储槽I、第一离心泵2、 澄清槽3和第一渣浆泵4,澄清槽3通过第二离心泵5与供酸槽8相连接,供酸槽8还分别与输酸泵7和第二渣浆泵9相连接,输酸泵7与磷铵装置6相连接;第二渣浆泵9与酸储槽 I相连接。酸储槽I为带有搅拌桨的储酸槽。本发明还提供了一种利用上述生产系统生产高养分磷铵的方法,该方法具体按以下步骤进行
步骤I :将酸质相对稳定的新产浓磷酸送入供酸槽8,并对该新产浓磷酸进行例行取样分析,若该新产浓磷酸的指标合格,则通过输酸泵7将供酸槽8内的浓磷酸送去磷铵系统6 生产64%养份磷铵;
若送入供酸槽8的新产浓磷酸的指标不符合指标要求,则通过第二渣浆泵9将供酸槽 8内的新产浓磷酸和供酸槽8底部含沉积物的浓磷酸连续送入带搅拌桨的酸储槽I中持续搅拌,并通过第一离心泵2将搅拌后的含沉积物的磷酸送至澄清槽3内;
新产浓磷酸要求的指标为
P2O5 44 46% ;
SO3 5. 0% ;
含固量彡I. 5% (正常为O. 8 I. 2%)
Fe2O3 含量 O. 8 I. 0% ;Al2O3 含量 O. 9 I. 3% ;MgO 含量 I. 7 2. 0% ;
步骤3 :含沉积物的磷酸在澄清槽3内澄清至少24小时,形成上层澄清磷酸和酸渣; 通过第一渣浆泵4将酸渣送往反应过滤系统;
对上层澄清磷酸进行取样分析;若该上层澄清磷酸的指标符合以下要求酸比重 I. 5 I. 54g/cm3、浓度为40 43%(计算时取41. 5%)、含固量彡I. 5% ;则备用;若该上层澄清磷酸的指标不符合要求,则采取继续沉降以降低含固量并继续澄清,直至上层澄清磷酸的指标符合要求;
步骤3 :对送入供酸槽8的新产浓磷酸进行取样分析,根据新产浓磷酸的分析数据确定从澄清槽3送入供酸槽8的上层澄清磷酸的用量,然后通过第二离心泵5将相应用量的澄清槽3液位50%以上沉降后的上层澄清磷酸送入供酸槽8,与新产浓磷酸进行配酸,形成浓度符合要求的浓磷酸;再通过输酸泵7,将供酸槽8液位50%以上的符合要求的浓磷酸送去磷铵系统生成64%养分磷铵;再将供酸槽8底部含沉积物的磷酸送入带搅拌桨的酸储槽I。酸储槽I必须带搅拌桨,以使送入酸储槽I的含沉积物的磷酸得到持续搅拌,避免发生沉积物“坐槽”现象。通过控制新产浓磷酸输送泵出口的浓磷酸的分析数据确定配酸量。每班都要取样分析主要是对新产浓磷酸中的各项指标进行掌握,便于前后工序更好地控制各自的指标。 在配酸过程中不需要单独取样分析,只要保证澄清槽3中上层澄清磷酸的指标合格即可, 况且配酸过程不是连续的过程,待上层澄清磷酸取样分析合格后才进行配算。配酸是通过分析控制供生产用酸的内在质量来满足生产需求。配酸过程要求用于生产磷铵的浓磷酸中的五氧化二磷(P2O5)的质量分数为44 46%,且新生产浓磷酸质量稳定。混合酸的具体要求数据为
1)P2O5 44 46% ;
2)SO3 ·.≤ 5. 0% ;
3)含固量≤I.5% (正常为O. 8 I. 2%)
4)Fe2O3 含量 O. 8 I. 0% ;A1203 含量 O. 9 I. 3% ;MgO 含量 I. 7 2. 0%。配酸时可配上层澄清磷酸用量的计算方法
上层澄清磷酸的密度为I. 5 I. 54g/cm3 (计算时取I. 52g/cm3)、浓度为40 43% (计算时取41. 5%)、含固量彡I. 5% ;要求配酸后混合酸的含固量彡I. 5% (正常O. 8 I. 5%)为计算基准。如正常情况下供酸槽8每小时送入磷铵系统6的混合酸的量为40m3,该混合酸的比重为I. 58 I. 60 g/cm3,计算时取I. 59g/cm3 ;为减少效益流失该混合酸的浓度取44% ; 上工段进入供酸槽8的新生产浓磷酸的比重为I. 60 I. 62g/cm3 (计算时取I. 61 g/cm3), 该新生产浓磷酸的浓度取为45. 5%,设每小时可配上层澄清的磷酸的量为Xm3
则有40X1. 61X45. 5%+ΧΧ1. 52X41. 5% = (40+X) XL 59X44% ;解之得出每小时配入供酸槽8的上层澄清的磷酸的用量。
实施例甘肃瓮福有限责任公司采用本发明系统用含沉积物的磷酸生产64%养分磷铵。该系统中供酸槽8的容积为1100m3、酸储槽I的容积为500m3、澄清槽3的容积为800m3 ;各泵的进口均采用阀门控制。将澄清槽2中液位50%以上的上层澄清磷酸送入供酸槽8与新生产浓磷酸进行配酸,形成混合酸,将供酸槽8液位50%以上的混合酸送入磷铵系统6生产 64%养分磷铵。配酸时的计算方法为上层澄清磷酸含固量彡1.5%、比重取I. 52g/cm3、酸浓取 41. 5% ;要求配酸后混合酸的含固量彡I. 5%为计算基准;正常情况下供酸槽8每小时送入磷铵系统8的混合酸的量为40m3,该混合酸的比重为I. 59、浓度为44% ;送入供酸槽8的新生产浓磷酸的比重为I. 61 g/cm3、浓度为45. 5%,设每小时可配入供酸槽8的上层澄清磷酸的量为Xm3,
则有40X1. 61X45. 5%+ΧΧ1. 52X41. 5% = (40+X) XL 59X44%,
解之得出每小时可配含沉积物的磷酸量为19. 2 m3。而使用的澄清槽的每个液位为8m3, 19. 2 m3为2. 4个液位与实际配算量相符。采用本发明方法后,40万吨/年磷酸二铵生产系统中,每天排往反应过滤系统的酸渣减少了 50m3 (比重为I. 8g/cm3),按实际磷损I. 5%、排浆天数340天计算,每年可回收 P2O5 为
340X50X1. 8X1. 5%=459 (吨)
每吨浓磷酸按3260元计算,则每年可挽回损失
459X1000X3260 / 450=330. 48 万元。本发明方法合理利用含沉积物磷酸生产64%养分磷铵,为湿法磷酸生产过程中处理磷酸沉积物提供了 一条途径,每年创造的经济效益可观,同时回收了部分P2O5,减少了二次污染。
本发明提供了一种用含沉积物湿法磷酸生产合格养分磷铵的系统及方法,包括依次相连接的酸储槽、第一离心泵、澄清槽和第一渣浆泵,澄清槽通过第二离心泵与供酸槽相连接,供酸槽分别与输酸泵和第二渣浆泵相连接,输酸泵与磷铵装置相连接;第二渣浆泵与储酸槽相连接。将供酸槽中含沉积物的磷酸送入酸储槽,在送入澄清槽澄清,将上层澄清磷酸再送入供酸槽与送入供酸槽的新生产浓磷酸配成混合酸,将符合要求的混合酸送入磷铵系统生产高养分磷铵。本发明生产系统合理利用含沉积物磷酸生产64%养分磷铵,为湿法磷酸生产过程中处理磷酸沉积物提供了一条途径,每年创造的经济效益可观,同时回收了部分P2O5,减少了二次污染。
用含沉积物湿法磷酸生产高养分磷铵的系统及方法
- 专利详情
- 全文pdf
- 权力要求
- 说明书
- 法律状态
查看更多专利详情
下载专利文献
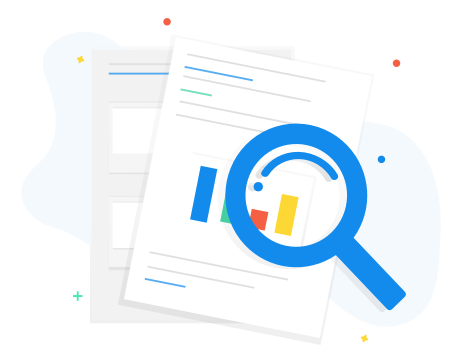
下载专利
同类推荐
-
宁聪琴, 鲁文豪张亚锋, 胡长坤刘永彪
您可能感兴趣的专利
-
乔治·哈尔西·比尔崔桂玲
专利相关信息
-
席真