蒸压加气混凝土砖的制作方法[0002]加气混凝土砖因具有重量轻、保温性能和吸音效果好、以及有一定强度等诸多优点,已逐渐成替代传统实心黏土砖而得到了广泛运用。目前,建筑市场所采用的加气混凝土砖块的生产原料主要以粉煤灰为主,而粉煤灰原料供应量有限,导致现有加气混凝土砖块的产量有限,无法满足建筑市场的需求。若能开发一种以工业废弃物——磷渣为主要原料的加气混凝土砖,不仅能够降低成本、拓宽加气混凝土砖的原料来源,更为主要是可有效地消耗磷渣而减少堆放场地、节约土地资源和改善环境,无疑会具有较好的经济效益和社会效益。
[0003]针对现有技术中存在的上述缺陷,本发明旨在提供一种以磷渣为主要原料制成的蒸压加气混凝土砖。[0004]为了实现上述目的,本发明采用以下技术方案:它由以下质量百分比的原料制成:磷渣49~55%、硅砂21~26%、生石灰18~22%、水泥3~9%、石膏I~3%、铝粉膏0.04~0.06%,所述磷渣中Ca0、Si02的含量之和大于85%、所述生石灰的细度为0.08mm筛筛余量小于10%;其方法如下: 1)将生石灰和石膏混合,球磨机磨成胶结料备用,保证胶结料的比表面积达4000~6000 cm2/g ; 2)将磷渣、硅砂混合,球磨机湿磨成浆料备用; 3)将铝粉膏加水搅拌均匀,制成铝粉膏浆备用;
4)将所述浆料、水泥、所述胶结料与水混合,均匀搅拌3分钟、加入所述铝粉膏浆,通入蒸汽并搅拌30秒钟,得浇注料;
5)将浇注料入模,送入50°C的养护室养护I~1.5小时,得大砖坯;
6)将大砖坯按要求切块,得砖坯;
7)将砖坯送入压力为-0.04~0.06Mpa的蒸压釜内,通入蒸汽,保证在1.5~2小时内升温至175°C以上;恒温5~7小时,保持压力0.8~1.2Mpa ;然后在100分钟内将釜内温度降至45~50°C,取出砖坯。
[0005]在上述技术方案中,所述铝粉膏为GLY75≥75%、或GLY65≥65%的油剂型铝粉膏,其固体中活性铝≥90%,发气量为4min为50~80%、16min≥90%、30min≥99%。
[0006]所述铝粉膏还可以采用GLS70≥70%、GLS65≥65%的水剂型铝粉膏,其固体中活性铝≥90%,发气量为4min为40~60%、16min≥90%、30min≥99%。
[0007]与现有技术比较,本发明由于上述技术方案,以电炉法制取黄磷时产生水淬废渣(磷渣)为主要原料,将原来的工业废弃物变废为宝;不仅拓宽加气混凝土砖的原料来源、降低了成本,而且还能通过消耗磷渣而减少堆放场地,节约了土地资源、减少了环境污染。
[0008]检测表明,本发明砖块的强度可达到A3.5、A5.0、A7.5、A10四个级别,密度可达到B05、B06、B07、B08四个级别,符合国家相关标准。
[0009]
实施例1
1)将生石灰20.04千克、石膏I千克混合,球磨机磨成胶结料备用,保证胶结料的比表面积达 4000 ~6000 cm 2/g ;
2)将磷渣49千克、硅砂26千克混合,球磨机湿磨成浆料备用;
3)将铝粉膏0.06千克加水搅拌均匀,制成铝粉膏浆备用;
4)将所述浆料、水泥9千克、所述胶结料与水混合,均匀搅拌3分钟后加入所述铝粉膏浆,通入蒸汽并搅拌30秒钟,得浇注料;
5)将浇注料入模,送入50°C的养护室养护I小时,得大砖坯;
6)将大砖坯按要求切块,得砖坯;
7)将砖坯送入压力为0.06Mpa的蒸压釜内,通入蒸汽,保证在1.5小时内升温至175°C以上;恒温7小时,保持压力0.8Mpa ;然后在100分钟内将釜内温度降至45~50°C,取出砖坯得制品。
[0010]实施例2
各步骤同实施例1 ;其中,步骤I)中的生石灰为19千克、石膏为1.96千克;步骤2)中的磷渣为55千克、硅砂为21千克;步骤3)中的铝粉膏为0.04千克;步骤4)中的水泥为3千克;步骤5)中的养护时间为1.5小时;步骤7)中升温时的压力为-0.04Mpa,蒸汽通入时间为2小时,恒温时间为5小时、恒温时的压力为1.2Mpa。
[0011]实施例3
各步骤同实施例1 ;其中,步骤I)中的生石灰为22千克、石膏为3千克;步骤2)中的磷渣为50.96千克、硅砂为21千克;步骤3)中的铝粉膏为0.04千克;步骤4)中的水泥为3千克;步骤5)中的养护时间为1.2小时;步骤7)中升温时的压力为0.01Mpa,蒸汽通入时间为1.8小时,恒温时间为6小时、恒温时的压力为_a。
[0012]实施例4
各步骤同实施例1 ;其中,步骤I)中的生石灰为18千克、石膏为2千克;步骤2)中的磷渣为52千克、硅砂为21.95千克;步骤3)中的铝粉膏为0.05千克;步骤4)中的水泥为6千克;步骤5)中的养护时间为1.4小时;步骤7)中升温时的压力为0.04Mpa,蒸汽通入时间为1.7小时,恒温时间为6小时、恒温时的压力为0.9Mpa。
[0013]实施例5
各步骤同实施例1 ;其中,步骤I)中的生石灰为22千克、石膏为2千克;步骤2)中的磷渣为49.95千克、硅砂为21千克;步骤3)中的铝粉膏为0.05千克;步骤4)中的水泥为5千克;步骤5)中的养护时间为1.4小时,步骤7)中升温时的压力为0.04Mpa,蒸汽通入时间为1.7小时,恒温时间为6小时、恒温时的压力为0.9Mpa。
[0014]实施例6
各步骤同实施例1 ;其中,步骤I)中的生石灰为20千克、石膏为2千克;步骤2)中的磷渣为51千克、硅砂为21.05千克;步骤3)中的铝粉膏为0.05千克;步骤4)中的水泥为5千克;步骤5)中的养护时间为1.4小时;步骤7)中升温时的压力为0.04Mpa,蒸汽通入时间为1.7小时,恒温时间为6小时、恒温时的压力为0.9Mpa。
[0015]上述各实施例中,磷渣中CaO、SiO2的含量之和大于85%、所述生石灰的细度为0.08mm筛筛余量小于10% ;铝粉膏可为GLY75≥75%、或GLY65≥65%的油剂型铝粉膏,其固体中活性铝≥90%,发气量为4min为50~80%、16min≥90%、30min≥99% ;铝粉膏也可为GLS70≥70%、GLS65≥65%的水剂型铝粉膏,其固体中活性铝≥90%,发气量为4min为40 ~60%、16min ≥ 90%、30min ≥ 99%。
蒸压加气混凝土砖制作方法
- 专利详情
- 全文pdf
- 权力要求
- 说明书
- 法律状态
查看更多专利详情
下载专利文献
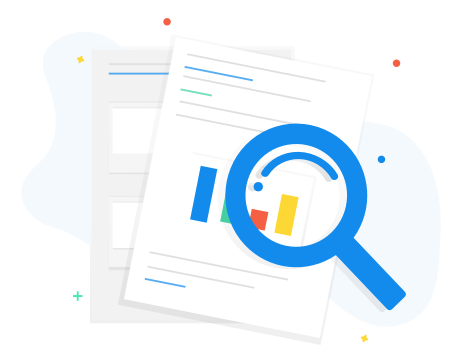
下载专利
同类推荐
-
于吉涛张鹏飞肖燎王卫东宋运来
您可能感兴趣的专利
-
吴金钻鱼智浩黄晓东, 张韬黄晓东, 张韬黄晓东, 张韬
专利相关信息
-
黄晓东, 张韬黄晓东, 张韬黄晓东, 张韬黄晓东, 张韬黄晓东, 张韬