专利名称:一种熔制镧系光学玻璃的石英坩埚及熔制镧系光学玻璃玻碴熟料的方法镧系光学玻璃一般也称高折射率低色散光学玻璃,包括了国际中的LaK、LaF和ZLaF等玻璃品种。Hoya以折射率高低和引入的氧化物进一步分为LaC、TaC、LaF、TaF、NbFD、TaFD0镧系光学玻璃是一种高档的无色光学玻璃,为了保证镧系光学玻璃的各种光学性能,要求在熔制过程中严禁引入铁、镍、锰等着色粒子,所以镧系光学玻璃的原料、熔制设备以及工装器具的选择都要求较高。由于镧系光学玻璃的熔制温度普通在1200-1400°C的高温,业内普遍采用钼金作为埚体材料,但是由于钼金坩埚的钼粒子的微量引入,会影响光学玻璃的透过率,而且设备成本昂贵;也有一些厂家使用特定结构、厚度的特制石英坩埚为埚体材料,其设备制造成本同样十分昂贵。昂贵的设备成本已严重制约了高档镧系光学玻璃的发展。虽然专利申请号:200920082682.X,发明名称:一种熔制镧系光学玻璃的石英坩埚,公开了一种熔制镧系光学玻璃的石英坩埚,包括坩埚体,耐火材料套筒,耐火材料填充层,坩埚体为电熔石英坩埚。其结构简单,可使用次品电熔石英坩埚作坩埚体,成本只需几百元,而钼金坩埚或特制石英坩埚成本需上万元,使成本大为降低,还消除了钼金坩埚对产品质量的影响,提高了镧系光学玻璃的产品性能,但是,该埚体外部的耐火材料套筒减少石英坩埚受热辐射量,使生产周期增长;该坩埚使用在投料前的升温阶段花费时间较长;在熔制阶段,加料时间长,约22小时。整个生产周期较长,约39小时。因此对石英坩埚埚体侵蚀较严重,且能源成本较高,而且套筒的使用也增加了生产成本。
本发明的技术方案是提供了一种熔制镧系光学玻璃的石英坩埚。本发明的另一技术方案是提供了熔制镧系光学玻璃玻碴熟料的方法。本发明提供了一种熔制镧系光学玻璃用坩埚,包括石英坩埚和位于石英坩埚底部的耐火材料底座。优选的,所述耐火材料底座上表面开有与石英坩埚底部形状相适配的凹槽,石英坩埚底部嵌入耐火材料底座内,且耐火材料底座顶部的高度低于石英坩埚高度的四分之 一 。优选的,所述石英坩埚底部开有出料孔,耐火材料底座内部连接出料孔的流通通道。进一步的,所述石英坩埚底面与侧面之间为圆角过渡。本发明还提供了一种熔制镧系光学玻璃玻碴熟料的方法,它是采用所述的石英坩埚进行熔制。具体包括下述步骤:a、升温:权利要求1或2所述的石英坩埚从室温升至750°C 900°C,升温时间4.0-5.0小时,再从750°C 900°C升温至1200±50°C,升温时间2.0-3.0小时,保温1200±50°C I小时后开始投入粉料;b、熔制:加料后,保持1200±50°C恒温加料,加料时间12-18小时,粉料加完后保温,然后放入鼓泡器开始鼓泡,完成鼓泡后将溶制完成的玻璃液放出,完成一批次熟料生产。进一步优选地,它包括下述步骤:a、升温:石英坩埚从室温升至800°C,升温时间4.5小时,再从800°C升温至1200°C,升温时间2.5小时,保温1200°C I小时后开始投入粉料;升温时间共8小时;b、溶制:加料后,保持1200 C恒温加料,加料时间15小时,粉料加完后保温半小时,然后放入鼓泡器开始鼓泡,鼓泡时间半小时,完成鼓泡后将熔制完成的玻璃液放出,完成一批次熟料生产。本发明通过对坩埚结构的改进,同时改变升温工艺、熔炼工艺,在不影响产品品质的情况下大幅缩短升温及熔制时间,提高生产效率,减少熔制过程中对石英埚的侵蚀,并降低能源成本。图1本发明石英坩 埚的结构示意图,图中:1_石英坩埚,2-耐火材料底座,3-通道。图2本发明工艺与旧工艺升温对比图3本发明工艺与旧工艺熔制数据对比图4本发明工艺与旧工艺数据对比图5本发明坩埚和专利申请号:200920082682.X所述的石英坩埚在本发明工艺条件下的相关数据对比
实施例3本发明熔制镧系光学玻璃玻碴熟料的方法与旧工艺对比旧的升温及熔炼工艺:采用专利申请号:200920082682.X所述的石英坩埚,从室温升至850°C,升温时间约6小时,保温850°C 2小时后再次升温至1200°C,升温时间约3小时,保温1200°C 2小时后降温至起始加料温度1050°C,降温时间约I小时,在1050°C保温I小时后开始投入粉料进行熔制。升温时间共约15小时。开始加料后,在加料过程中逐渐升温,加料时间约22小时,粉料加完后保温I小时,然后放入鼓泡器开始鼓泡,鼓泡时间I小时,熔制阶段总时间约24小时,完成鼓泡后将熔制完成的玻璃液放出,完成生产。单个炉期投入两批次粉料熔炼,即升温一次熔炼两次,单个炉期总时间约63小时。新工艺相比旧工艺单个炉期生产时间缩短约23小时,其中升温时间缩短约7小时,熔制阶段时间缩短约16小时。石英坩埚可在1450度以下使用,目前镧系光学玻璃熔制温度均低于1450°C。具体对比如下:1、在旧的技术方案基础上,根据石英坩埚、生产设备情况,改进升温工艺。新的升温工艺(以熔炼温度曲线图体现)比旧的升温工艺缩短约7 8小时升温时间。对生产设备、石英坩埚无不利影响,石英坩埚物化性能与旧技术方案下表现一致。通过图2可以看出,旧的工艺升温速率慢(以电流控制,15A/小时增加),升温阶段不必要的保温时间长,使得整个升温周期较长,约15个小时。在分析以往统计数据及对生产设备的实际使用情况进行分析后,去除掉不必要的保温时间,在不损害设备前提下,大幅度提高升温速度(以电流控制,40A/小时增加)。使总升温时间得到缩短,相比旧升温工艺缩短约7至8小时。2、熔制阶段,在旧熔炼工艺基础上进行改进。根据不同牌号玻璃的性质,改变加料方式、熔炼温度制定出新的熔炼工艺。新的熔炼工艺下,熔炼时间大幅缩短。因玻璃牌号不同缩短的时间长短不一,每批次熔炼时间缩短7 10小时。时间缩短减少了熔制过程中玻璃液对石英坩埚的侵蚀,提高了石英坩埚使用寿命,并且生产效率提高约80%。(见图3、图4)3、采用本发明石英坩埚直接接触炉膛内的辐射热量,受热更加均匀,系统升温时间及玻璃熔制时间均较有套筒坩埚系统明显缩短。并且玻璃熔制的工艺温度也相应降低,同一牌号玻璃新工艺熔炼温度比旧工艺降低约80 100°C。使得石英坩埚使用寿命得到提高,能耗降低,生产总成本降低;生产效率得到提高。本发明坩埚和专利申请号:200920082682.X所述的石英坩埚在本发明工艺条件下的相关数据对比,对比结果见图5 ;试验结果表明,本发明工艺熔炼时间短、熔炼温度低、每小时产量高31%,每公斤熟料耗材成本降低21.9%。综上所述,本发明生产工艺大幅缩短生产周期,提高了生产效率,降低生产成本。无套筒石英坩埚系统生产周期短,能耗低,生产效率高且生产成本低于有套筒石英坩埚系统。
本发明提供了一种熔制镧系光学玻璃的石英坩埚,包括石英坩埚和位于石英坩埚底部的耐火材料底座。本发明还提供了一种熔制镧系光学玻璃玻碴熟料的方法。本发明通过对坩埚结构的改进,同时改变升温工艺、熔炼工艺,在不影响产品品质的情况下大幅缩短升温及熔制时间,提高生产效率,减少熔制过程中对石英埚的侵蚀,并降低能源成本。
一种熔制镧系光学玻璃的石英坩埚及熔制镧系光学玻璃玻碴熟料的方法
- 专利详情
- 全文pdf
- 权力要求
- 说明书
- 法律状态
查看更多专利详情
下载专利文献
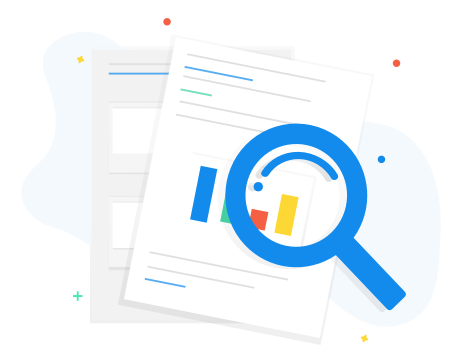
下载专利
同类推荐
-
王自力, 周兵王自力, 周兵金凤山托尔斯滕·德林, 伊纳·米特拉
您可能感兴趣的专利
-
高惠民高惠民高惠民山口康介, 蜂谷洋一山口康介, 蜂谷洋一吴立龙
专利相关信息
-
李宗辉罗尔夫·马丁廖寄乔彭明营彭明营戎俊华