专利名称:一种改性氧化铝气凝胶复合材料及其制备方法传统的保温隔热材料密度高,质量大,极大地限制了在飞行器上的使用。与传统绝 热材料相比,纳米多孔气凝胶绝热材料以更轻的质量、更小的体积达到等效的绝热效果,而 受到各国宇航领域材料研究者的青睐。气凝胶具有独特的三维纳米网络结构(骨架2 5nm),高比表面积(500 1200m2/g),纳米尺寸的孔(约20nm),孔洞率高达95%以上,能 够有效抑制固态热传导和气体对流传热,是目前热导率最低的固态材料(常温为0.015W/ m · K),因此在国际上也被称为超级绝热材料。但是常规的氧化硅气凝胶作为绝热材料时, 其高温遮挡红外辐射能力差而导致隔热效果差,耐温较低,长期使用温度不高于650°C。另 外,常规的氧化硅气凝胶强度差,纳米级孔隙结构在外部压力下很容易被破坏,难以形成具 有一定面积或体积的型材,这是限制其在航空、航天飞行器的推广应用另一个原因。长期以来,人们对本身具有更高耐温特性的氧化铝材料进行了深入研究,发现这 类材料的气凝胶在高温下同样具有优异的保温隔热特性。如氧化铝气凝胶除了密度低,比 表面积大,而且高温下的热导率也能够保持着很低(30°C、1大气压时热导率仅为0. 029W/ m ·Κ ;800°CU大气压时热导率仅为0. 098W/m ·Κ),但氧化铝气凝胶存在高温下发生晶形转 变而导致结构坍塌,高温下结构容易收缩而导致其耐温性有限。为了解决现有技术中的上述问题,本发明采用通过增加第二相硅来实现可控相的 转变,使转变相稳定下来。在更优选的实施方案中,本发明还采用的硅相为硅溶胶的水体 系,其中主要通过硅溶胶中的水作为铝溶胶的水解反应物,让硅溶胶参与铝溶胶价键形成 过程,得到Al-O-Si键,凝胶干燥后即得到改性氧化铝气凝胶(本文有时称为硅铝复合气 凝胶)。硅溶胶水溶液体系的溶胶颗粒较大,通常为20nm 30nm,远大于硅醇盐所形成的 Inm IOnm溶胶颗粒。据研究发现,溶胶颗粒大小决定了气凝胶高温下的颗粒聚集速度和 骨架结构粗细,颗粒越大,表面能越小,颗粒之间聚集速度越慢,高温结构越趋于稳定,同时 颗粒大的胶体粒子组成具有较粗骨架的网络结构,高温受热后不易坍塌,因此通过硅铝复 合气凝胶提高氧化铝气凝胶的耐温性。另外,本发明将采用无机纤维材料来增强本发明方 法制得的鬼铝气凝胶的强度,以改善所述气凝胶的力学性能,从而制备出耐高温的纤维增 强型硅铝气凝胶复合材料。
为了克服现有技术存在的一个或多个甚至是全部上述问题,尤其是单一的纯氧化 铝气凝胶由于高温下晶形转变导致的高温结构不稳定因而影响其高温隔热性能的问题,并 且利用硅溶胶水溶液体系的溶胶颗粒较大的特定,进一步解决了改善了硅铝气凝胶复合材 料的高温稳定性。本发明通过如下方案来解决上述问题1、一种硅铝气凝胶复合材料,其中,所述硅铝气凝胶复合材料包含(1)硅铝复合3气凝胶;和(2)无机纤维材料;其中所述硅铝复合气凝胶是利用硅溶胶水溶液来制得。2、根据技术方案1所述的硅铝气凝胶复合材料,其中,所述硅溶胶水溶液中的溶 胶颗粒直径为IOnm 20nm。3、根据技术方案1或2所述的硅铝气凝胶复合材料,其中,所述硅溶胶水溶液为低 钠型硅溶胶水溶液。4、根据技术方案1 3中任一项所述的硅铝气凝胶复合材料,其中,所述硅溶胶水 溶液中的SiO2在水体系中的质量比例为1 % 25 %。5、根据技术方案1 4中任一项所述的硅铝气凝胶复合材料,其中,所述硅铝复合 气凝胶中的SiO2的比例以所述硅铝复合气凝胶的摩尔计为0. 01% 20%。6、根据技术方案1 5中任一项所述的硅铝气凝胶复合材料,其中,所述无机纤维 材料为选自由石英纤维、高硅氧纤维、硅酸铝纤维、玻璃纤维、氧化铝纤维、氧化锆纤维、氮 化硼纤维、玄武岩纤维和莫来石纤维组成的组中的一种或者两种以上的组合;优选的是,所 述无机纤维材料的形式为选自由纤维毡、纤维棉、纤维毯、纤维板、纤维折叠块、纤维预制件 和预制件复合体组成的组中的一种或两种以上的组合。7、如技术方案1 6中任一项所述的硅铝气凝胶复合材料,其中,所述无机纤维材 料的体积密度为0. 01g/cm3 0. 90g/cm3,单根纤维直径为0. 1 μ m 10 μ m。8、一种制备硅铝气凝胶复合材料的方法,其特征在于,该方法包括如下步骤(1)铝溶胶预制液的制备将铝盐、螯合剂、铝溶胶用溶剂混合均勻,制得铝溶胶 预制液;(2)硅铝复合溶胶的制备将硅溶胶水溶液加入所述铝溶胶预制液并混和,再加 入碱性催化剂,水解得到硅铝复合溶胶;(3)浸胶通过浸渗工艺使所述硅铝复合溶胶浸入无机纤维材料中,得到硅铝复 合溶胶与无机纤维材料的混合物;(4)胶凝将所述混合物置于60°C 80°C的环境中,使所述混合物中的所述硅铝 复合溶胶发生胶凝,得到硅铝复合凝胶;(5)老化通过加入老化用醇溶剂进行24小时 48小时的老化;和(6)超临界干燥对经老化的硅铝复合凝胶进行超临界干燥处理,得到所述硅铝 气凝胶复合材料。9、如技术方案8所述的方法,其中,在步骤(2)中,所述硅溶胶水溶液按照使所述 硅铝复合气凝胶中的SiO2以所述硅铝复合气凝胶的摩尔计为0. 01% 20%的比例与步骤 (1)中制得的所述铝溶胶预制液混合。10、根据技术方案8或9所述的方法,其中,所述铝溶胶用溶剂为醇溶剂或酮溶剂,11、根据技术方案8 10中任一项所述的方法,其中,所述老化用醇溶剂为选自由 乙醇、异丙醇和仲丁醇组成的组中的一种或两种以上的组合。12、如技术方案8 11中任一项所述的方法,其中,所述硅铝复合溶胶的制备采用 如下方式进行(1)以所述铝盐为先驱体,加入所述螯合剂并混合均勻,再加入所述溶胶用 溶剂并混合均勻;(2)然后滴加所述硅溶胶水溶液,最后滴加所述碱性催化剂并混合均勻, 得到所述硅铝复合溶胶。13、如技术方案8 12中任一项所述的方法,其中,所述铝盐、螯合剂、硅溶胶4水溶液中的纯二氧化硅和碱性催化剂的摩尔比为1 0.001 0.6 4 32 0. 6 4 0. 0001 1。14、如技术方案8 13中任一项所述的方法,其中,所述浸胶通过如下方式(1)或 ⑵进行(1)直接将所述硅铝复合溶胶加入放置有所述无机纤维材料的模具中,依靠重力 进行浸胶;(2)使用所述硅铝复合溶胶浸渍所述无机纤维材料,并将经浸渍的所述无机纤维 材料装入模具中,再使用所述硅铝复合溶胶进行浸渗。15、如技术方案14所述的方法,其中,所述无机纤维材料为大而厚的无机纤维材 料,并且所述浸胶采用方式(2)进行。16、如技术方案8 15中任一项所述的方法,其中,所述超临界流体干燥按照如下 方式进行将浸渍有所述硅铝复合溶胶的所述无机纤维材料放入超临界流体干燥设备中, 打入2兆帕斯卡 10兆帕斯卡的干燥介质,在0 50°C保温1小时 30小时;再升温至 20°C 80°C,并利用干燥介质以10升/小时 400升/小时的流量将辅助介质带入分离釜 进行分离;在辅助介质分离完全后,再以1兆帕斯卡/小时 6兆帕斯卡/小时的速度将压 力释放至与外界大气压平衡,得到所述硅铝气凝胶复合材料。17、如技术方案13所述的方法,其中,所述干燥介质为二氧化碳或乙醇,所述辅助 介质为醇溶剂或酮溶剂,所述醇溶剂为乙醇和/或异丙醇,所述酮溶剂为丙酮。18.根据技术方案8 17中任一项所述的方法,其中,所述铝盐为选自由异丙醇 铝、仲丁醇铝和硝酸铝组成的组中的一种或两种以上的组合;所述铝溶胶用醇溶剂为选自由乙醇、异丙醇和正丁醇组成的组中的一种或两种以 上的组合;所述螯合剂为乙酰丙酮和/或乙酰乙酸乙酯;和/或所述碱性催化剂为选自由氨水、氢氧化钠或氟化铵组成的组中的一种或两种以上 的组合,优选为氨水。19、根据技术方案8 18中任一项所述的方法,其中,所述无机纤维材料为选自由石英纤维材料、高硅氧纤维、硅酸铝纤维、玻璃纤维、 氧化铝纤维、氮化硼纤维、玄武岩纤维和莫来石纤维组成的组中的一种或者两种以上的组 合;优选的是;所述纤维的纤维形式为连续纤维形式和/或短纤维形式;优选的是,所述无机纤维材料的制品形式为纤维棉、纤维毯、纤维板、纤维折叠块、 纤维预制件或纤维预制件复合体形式。20、如技术方案8 19中任一项所述的方法,其中,所述无机纤维材料的体积密度 为0. 01 0. 90g/cm3,单根纤维直径为0. 1 10 μ m。21、由技术方案8 20中任一项所述的方法制得的硅铝气凝胶复合材料。本发明的有益效果(1)采用硅溶胶与铝溶胶形成复合气凝胶,避免了铝气凝胶 高温下晶型容易转变而导致气凝胶结构坍塌造成的负面影响,不仅提高了其耐温性,同时 也使其在高温下具有较低的热导率;与经过纤维增强的单一的硅气凝胶材料或氧化铝气凝 胶材料相比,本发明的耐高温隔热复合材料在相同条件下,可具有更好的耐温性和更低的高温热导率。(2)通过对一种或者多种无机纤维与硅铝气凝胶的复合使用,显著降低了增强 纤维本身的固体传热;(3)采用纤维增强的气凝胶复合材料,除具有优异的隔热以及力学 性能外,还可根据产品的外观和形貌进行包覆;(4)所制备的硅铝气凝胶复合材料,除具有 优异的隔热性能外,还具有优异的力学性能,例如通过纤维的铺层设计,可以使其拉伸强度 高于2MPa ; (5)制备工艺简单,只需制备纤维增强凝胶材料,通过超临界流体干燥,即可得 到纤维增强的硅铝气凝胶复合材料。如果采用硅醇盐,则所得到的硅溶胶颗粒的颗粒级别 为Inm 10nm,与铝溶胶复合后,会因为颗粒太小,表面能太大,高温下容易发生聚集,导致 气凝胶纳米结构容易坍塌。相反,本发明采用硅溶胶水溶液来制备硅铝气凝胶复合材料,所 得到的硅溶胶颗粒较大,一般为20nm 30nm,与铝溶胶复合后,颗粒较大而不易聚集,从而 保证在高温下气凝胶结构的稳定性。6无机纤维材料。但是优选的是,所述无机纤维材料为选自由石英纤维、高硅氧纤维、硅酸铝 纤维、玻璃纤维、氧化铝纤维、氧化锆纤维、氮化硼纤维、玄武岩纤维和莫来石纤维组成的组 中的一种或者两种以上的组合。在制备过程中所使用的无机纤维材料的形式可以为选自由 纤维毡、纤维棉、纤维毯、纤维板、纤维折叠块、纤维预制件和预制件复合体组成的组中的一 种或两种以上的组合,本领域技术人员可以根据所要制备的具体材料的具体要求选择使用 适当形式的无机纤维材料。另外优选的是,无机纤维材料的体积密度为0. 01 g/cm3 0. 90g/cm3,例如为 0. 01g/cm3、0. 05g/cm3、0. 10g/cm3、0. 20g/cm3、0. 30g/cm3、0. 40g/cm3、0. 50g/cm3、0. 60g/cm3、 0. 70g/cm3、0. 80g/cm3或0. 90g/cm3。。另外还优选的是,无机纤维材料的单根纤维直径为 0. 1 μ m ~ 10 μ m,例如为 0. 1 μ m、0. 5 μ m、1· 0 μ m、2. 0 μ m、3. 0 μ m、4. 0 μ m、5. 0 μ m、6. 0 μ m、 7.0 μ m、8. 0 μ m、9. 0 μ m或10. 0 μ m。若单根纤维较粗,则固体热导率会显著上升,因此一 般纤维越细越好;但是从目前工业生产水平的角度来看(即易得性),优选为0. 1 μ m 10 μ m。第二方面,本发明提供了一种制备硅铝气凝胶复合材料的方法,所述方法包括如 下步骤(1)铝溶胶预制液的制备将铝盐、螯合剂、铝溶胶用溶剂混合均勻,制得铝溶胶 预制液;(2)硅铝复合溶胶的制备将硅溶胶水溶液加入所述铝溶胶预制液并混和,再加 入碱性催化剂,水解得到硅铝复合溶胶;(3)浸胶通过浸渗工艺使所述硅铝复合溶胶浸入无机纤维材料中,得到硅铝复 合溶胶与无机纤维材料的混合物;(4)胶凝将所述混合物置于60°C 80°C的环境中,使所述混合物中的所述硅铝 复合溶胶发生胶凝,得到硅铝复合凝胶;(5)老化通过加入老化用醇溶剂进行24小时 48小时的老化;和(6)超临界干燥对经老化的硅铝复合凝胶进行超临界干燥处理,得到所述硅铝 气凝胶复合材料。优选的是,在步骤(2)中,所述硅溶胶水溶液按照使所述硅铝复合气凝胶中的SiO2 以所述硅铝复合气凝胶的摩尔计为0.01% 20%的比例与步骤(1)中制得的所述铝溶胶 预制液混合。本发明方法对步骤(2)中的碱性催化剂没有特别的限制,优选所述碱性碱性催化 剂为选自由氨水、氢氧化钠、四甲基氢氧化铵、乌洛托品和氟化铵组成的组中的一种或两种 以上的组合,进一步优选氨水或者氨水与一种或多种其他所述碱性催化剂的组合,最优选 的是氨水;另外优选的是,所述乌洛托品以其水溶液的形式使用,浓度例如可以为20%。本发明对铝溶胶用溶剂没有特别的限制,只要铝溶胶用溶剂能够用以制备铝溶胶 并且总体看来在制备过程中以及材料使用过程中对材料体系不造成不良影响即可,例如可 以为醇溶剂;更优选的是,所述醇溶剂选自由乙醇、异丙醇和正丁醇组成的组中的一种或两 种以上的组合;但是从例如易得性、易用性或成本等角度来看,更优选的是乙醇。本发明对铝盐也没有特别的限制,本发明方法中所用的铝盐可以为选自由异丙醇 铝、仲丁醇铝和硝酸铝组成的组中的一种或两种以上的组合。7
本发明方法对螯合剂也没有特别的限制,不过所述螯合剂优选为乙酰丙酮和/或
乙酰乙酸乙酯。本发明方法所用的无机纤维材料如本发明的第一方面所述。在配制铝溶胶预制液时,可以例如采用如下方式进行以铝盐为先驱体,加入螯合 剂并混合均勻,再加入铝溶胶用溶剂并混合均勻,然后滴加硅溶胶水溶液,接着添加所述碱 性催化剂并混合均勻,得到硅铝复合溶胶。优选的是,所述铝盐、螯合剂、铝溶胶用溶剂、硅 溶胶水溶液和碱性催化剂的摩尔比为1 0.001 0.6 4 32 0. 6 4 0. 0001 1,例如可以为 1 (0. 001、0. 01、0. 1、0. 2、0. 3、0. 4、0. 5 或 0. 6) (4、8、12、16、20、24、28 或 32) (0. 6、1. 2、1. 8、2. 4、3. 2、3. 5、3. 8 或 4) (0. 0001、0· 0002、0· 0005、0· 001、0· 01、 0. 1 或 1)。在浸胶时,通过如下方式(1)或(2)进行(1)直接将硅铝复合溶胶加入放置有无 机纤维材料的模具中,依靠重力进行浸胶;(2)使用硅铝复合溶胶浸渍无机纤维材料,并将 经浸渍的无机纤维材料装入模具中,再使用硅铝复合溶胶进行浸渗。当无机纤维材料为大 而厚(例如尺寸超过300*300、厚度超过20nm)的无机纤维材料形式时,优选采用方式(2) 进行浸胶。在进行老化时,本发明对老化温度没有特别的限制,可以在例如室温 60°C的温 度范围内进行老化。老化所用的溶剂优选为醇溶剂,例如为乙醇、异丙醇和/或仲丁醇。在进行超临界流体干燥时,可以例如采用按照以下方式进行将浸渍有所述硅铝 复合溶胶的无机纤维材料放入超临界流体干燥设备中,打入2兆帕斯卡 10兆帕斯卡的干 燥介质,在0 50°C保温1小时 30小时;再升温至20°C 80°C,并利用干燥介质以10升 /小时 400升/小时的流量将辅助介质带入分离釜进行分离;在辅助介质分离完全后,再 以1兆帕斯卡/小时 6兆帕斯卡/小时的速度将压力释放至与外界大气压平衡,得到硅 铝气凝胶复合材料。在超临界干燥过程中,可以使用二氧化碳或乙醇作为干燥介质,使用醇 溶剂或者酮溶剂作为辅助介质,所述醇溶剂为乙醇和/或异丙醇,所述酮溶剂为丙酮。第三方面,本发明还提供了以上所述的本发明方法制得的硅铝气凝胶复合材料。在本文中,除非另有说明,否则本说明书中所述的“高温”是指650°C以上的温度。除非另有说明,否则本文所述的“硅铝复合溶胶”是指含有硅和铝的溶胶。除非另有说明,否则本文所述的“硅铝复合气凝胶”是指由通过硅溶胶水溶液掺杂 铝醇盐水解制得的硅铝复合溶胶。本发明的硅铝复合气凝胶是在硅溶胶与铝溶胶预制液复 合后形成了 Al-O-Si键而制得的。本发明的硅铝复合气凝胶可以克服单一气凝胶在高温下 的性能不稳定性,而且还达到两种单一气凝胶(即硅气凝胶和铝气凝胶)组合的最佳效果。 特别是由于采用硅溶胶水溶液来制备硅铝复合溶胶,进一步改善了硅铝复合气凝胶材料在 高温时的结构稳定性。除非另有说明,则否则本文所述的“硅铝气凝胶复合材料”的“复合”指起到增强 等作用的无机纤维材料与由浸渍到无机纤维材料中的硅铝复合溶胶制得的硅铝复合气凝 胶的结合。除非另有说明,否则术语“选自由......组中的一种或两种以上的组合”是指选
自所述组的任意一种,或者是所述组中任意两种以上的任意组合。除非另有说明,否则本文所用的术语“两种以上”中的“以上”包括本数在内,即包括两种的情形和多于两种的情形。除非另有说明,否则本文所述及的数值范围包括端值以及两端值(即上限和下 限)之间的任意值。
实施例下文将以实施例的形式对本发明作进一步说明。然而,这些实施例只是就本发明 的优选实施方式进行举例说明,本发明的保护范围不应解释为仅限于这些实施例。以下实 施例所采用的化学试剂购自北京市化学试剂公司,无机纤维材料购自山东鲁阳股份有限公
司ο对于作为配制硅溶胶或铝溶胶的原料的水,在所有下述实施例中,使用的均为用 于举例说明的去离子水。20-30实施例1本实施例所制备的硅铝气凝胶复合材料为硅酸铝纤维增强硅铝气凝胶复合材料, 硅铝复合气凝胶中的SiO2相对于所述硅铝复合气凝胶的摩尔比为1%。所用的硅溶胶 水溶液为硅溶胶低钠型水溶液(硅含量为25 %,钠含量为< 0. 25 %,溶胶颗粒为20nm 30nm,购自北京市化学试剂公司,下同);。所用材料还包括作为铝盐的仲丁醇铝、作为 螯合剂的乙酰乙酸乙酯、作为铝溶胶用溶剂的乙醇和作为碱性催化剂的氨水(摩尔比为 1 0.001 16 3 0.002),所述硅溶胶水溶液的加入量根据使硅铝复合气凝胶中的 SiO2相对于所述硅铝复合气凝胶的摩尔比为来算得。将铝盐、螯合剂和铝溶胶用溶剂 配成混合溶液后,加入所述硅溶胶水溶液,再加入作为碱性催化剂的氨水,制得硅铝复合溶 胶。然后,直接将硅铝复合溶胶加入装有体积密度为0. 2g/cm3、单根纤维直径为1 μ m的硅酸 铝纤维材料的模具中,依靠重力进行浸渍。在60°C进行6小时的胶凝,而后于室温在乙醇中 老化48小时,再放入高压釜中,打入2兆帕斯卡的二氧化碳,在30°C保温15小时。再升温 至50°C,并将二氧化碳以200升/小时的流量将乙醇带入分离釜进行分离。在乙醇分离完 全后,再以3兆帕斯卡/小时的速度缓慢释放压力,直至与外界大气压平衡,最后取出纤维 增强气凝胶复合材料。经测定,该硅铝气凝胶复合材料在800°C高温下的热导率为0. 078瓦 /米·开尔文(测试标准YB/T 4130-2005,下同,标准为公开标准),线性收缩率小于3%。实施例2本实施例所制备的硅铝气凝胶复合材料为莫来石纤维增强硅铝复合气凝胶,硅铝 复合气凝胶中的SiO2相对于所述硅铝复合气凝胶的摩尔比为5%。所用的硅溶胶水溶液为 硅溶胶低钠型水溶液,硅含量为25%。所用材料还包括仲丁醇铝、乙酰乙酸乙酯、乙醇和氨 水(摩尔比为1 0.001 16 3 0.002),硅溶胶水溶液的添加量根据使硅铝复合气凝 胶中的SiO2相对于所述硅铝复合气凝胶的摩尔比为5%来算得。按与实施例1类似的相同 的方法制得硅铝复合溶胶。然后,直接将硅铝复合溶胶加入装有体积密度为0. 2g/cm3、单根 纤维直径为0. 1 μ m的莫来石纤维的模具中,依靠重力浸渍,在60°C下凝胶6小时,后于室 温在乙醇中老化48小时,放入高压釜中,打入2兆帕斯卡的二氧化碳,在30°C下保温15小 时。再升温至50°C,并将二氧化碳以200升/小时的流量将乙醇带入分离釜进行分离。在 乙醇分离完全后,再以3兆帕斯卡/小时的速度缓慢释放压力,直至与外界大气压平衡,最 后取出纤维增强气凝胶复合材料。经测定,该硅铝气凝胶复合材料在800°C高温下的热导率为0. 078瓦/米 开尔文,线性收缩率小于3%。实施例3本实施例所制备的硅铝气凝胶复合材料为高硅氧纤维增强硅铝复合气凝胶,硅铝 复合气凝胶中的SiO2相对于所述硅铝复合气凝胶的摩尔比为10%。硅溶胶低钠铵型水溶 液,硅含量为20%。所用的材料还包括仲丁醇铝、乙酰乙酸乙酯、乙醇和氨水(摩尔比为 1 0.001 16 3 0.002),硅溶胶水溶液的添加量根据使硅铝复合气凝胶中的SiO2相 对于所述硅铝复合气凝胶的摩尔比为10%来算得。按与实施例1类似的相同的方法制得硅 铝复合溶胶。然后,直接将硅铝复合溶胶加入装有体积密度为0. 22g/cm3、单根纤维直径为 0. 5 μ m的高硅氧纤维的模具中,依靠重力浸渍,在60°C下凝胶8小时,后于室温在乙醇中老 化48小时,放入高压釜中,打入2兆帕斯卡的二氧化碳,在30°C下保温15小时。再升温至 50°C,并将二氧化碳以200升/小时的流量将乙醇带入分离釜进行分离。在乙醇分离完全 后,再以3兆帕斯卡/小时的速度缓慢释放压力,直至与外界大气压平衡,最后取出纤维增 强气凝胶复合材料。经测定,该硅铝气凝胶复合材料在800°C高温下的热导率为0. 081瓦/ 米·开尔文,线性收缩率小于3%。实施例4本实施例所制备的硅铝气凝胶复合材料为石英棉纤维增强硅铝复合气凝胶,硅 铝复合气凝胶中的SiO2相对于所述硅铝复合气凝胶的摩尔比为8%。硅溶胶低钠铵型 水溶液,硅含量为25%。所用的材料还包括仲丁醇铝、乙酰乙酸乙酯、乙醇(摩尔比为 1 0.001 16 3 0.002),硅溶胶水溶胶的添加量根据使硅铝复合气凝胶中的SiO2 相对于所述硅铝复合气凝胶的摩尔比为8%来算得。按与实施例1类似的相同的方法制得 硅铝复合溶胶。然后,直接将硅铝复合溶胶加入装有体积密度为0. 2g/cm3、单根纤维直径为 5 μ m的的石英棉纤维的模具中,依靠重力浸渍,在60°C下凝胶4小时,后于室温在醇溶剂中 老化48小时,放入高压釜中,打入2兆帕斯卡的二氧化碳,在30°C下保温15小时。再升温 至50°C,并将二氧化碳以200升/小时的流量将乙醇带入分离釜进行分离。在乙醇分离完 全后,再以3兆帕斯卡/小时的速度缓慢释放压力,直至与外界大气压平衡,最后取出纤维 增强气凝胶复合材料。经测定,该硅铝气凝胶复合材料在800°C高温下的热导率为0. 081瓦 /米·开尔文,线性收缩率小于3%。实施例5本实施例所制备的硅铝气凝胶复合材料为玄武岩纤维增强硅铝复合气凝胶,硅 铝复合气凝胶中的SiO2相对于所述硅铝复合气凝胶的摩尔比为20%。硅溶胶低钠型 水溶液,硅含量为30%。所用的材料还包括仲丁醇铝、乙酰乙酸乙酯、乙醇(摩尔比为 1 0.001 16 3 0.002),硅溶胶和铝溶胶的混合比例根据使硅铝复合气凝胶中的 SiO2相对于所述硅铝复合气凝胶的摩尔比为20%来算得。按与实施例1类似的相同的方 法制得硅铝复合溶胶。然后,直接将硅铝复合溶胶加入装有体积密度为0. 21g/cm3、单根纤 维直径为10 μ m的玄武岩纤维的模具中,依靠重力浸渍,在60°C下凝胶6小时,后于室温在 乙醇中老化48小时,放入高压釜中,打入2兆帕斯卡的二氧化碳,在30°C下保温15小时。 再升温至50°C,并将二氧化碳以200升/小时的流量将乙醇带入分离釜进行分离。在乙醇 分离完全后,再以3兆帕斯卡/小时的速度缓慢释放压力,直至与外界大气压平衡,最后取 出纤维增强气凝胶复合材料。经测定,该硅铝气凝胶复合材料在800°C高温下的热导率为0.081瓦/米·开尔文,线性收缩率小于3%。实施例6本实施例所制备的硅铝气凝胶复合材料为玻璃纤维增强硅铝复合气凝胶,硅 铝复合气凝胶中的SiO2相对于所述硅铝复合气凝胶的摩尔比为5%。硅溶胶低钠铵型 水溶液,硅含量为25%。所用的材料还包括仲丁醇铝、乙酰乙酸乙酯、乙醇(摩尔比为 1 0.001 16 3 0.002),硅溶胶和铝溶胶的混合比例根据使硅铝复合气凝胶中的 SiO2相对于所述硅铝复合气凝胶的摩尔比为5%来算得。按与实施例1类似的相同的方法 制得硅铝复合溶胶。然后,直接将硅铝复合溶胶加入装有体积密度为0. 23g/cm3、单根纤维 直径为1 μ m的玻璃纤维的模具中,依靠重力浸渍,在60°C下凝胶6小时,后于室温在乙醇 中老化48小时,放入高压釜中,打入2兆帕斯卡的二氧化碳,在30°C下保温15小时。再升 温至50°C,并将二氧化碳以200升/小时的流量将乙醇带入分离釜进行分离。在乙醇分离 完全后,再以3兆帕斯卡/小时的速度缓慢释放压力,直至与外界大气压平衡,最后取出纤 维增强气凝胶复合材料。经测定,该硅铝气凝胶复合材料在800°C高温下的热导率为0. 081 瓦/米 开尔文,线性收缩率小于3%。实施例7本实施例所制备的硅气凝胶复合材料为玻璃纤维增强硅气凝胶,所用的材料包括 正硅酸乙酯、异丙醇、去离子水和氨水(摩尔比为1 1 1 0.0008),以其中的氨水作 为碱性催化剂配成硅溶胶后,直接将硅溶胶加入装有体积密度为0. 23g/cm3、单根纤维直径 为的Iym玻璃纤维的模具中,依靠重力浸渍,在60°C下凝胶6小时,后于室温在乙醇中老 化48小时,放入高压釜中,打入2兆帕斯卡的二氧化碳,在30°C下保温15小时。再升温至 50°C,并将二氧化碳以200升/小时的流量将乙醇带入分离釜进行分离。在乙醇分离完全 后,再以3兆帕斯卡/小时的速度缓慢释放压力,直至与外界大气压平衡,最后取出纤维增 强硅气凝胶材料。经测定,线性收缩率为40%。实施例8本实施例所制备的铝气凝胶复合材料为硅酸铝纤维增强铝气凝胶,所用材料包括 仲丁醇铝、乙酰乙酸乙酯、乙醇、水和氨水(摩尔比为1 0.6 16 3 0.002),以其中 的氨水作为碱性催化剂配成铝溶胶后,直接将铝溶胶加入装有体积密度为0. 23g/cm3、单根 纤维直径为1 μ m的硅酸铝纤维的模具中,依靠重力浸渍,在60°C下凝胶6小时,后于室温在 乙醇中老化48小时,放入高压釜中,打入2兆帕斯卡的二氧化碳,在30°C下保温15小时。 再升温至50°C,并将二氧化碳以200升/小时的流量将乙醇带入分离釜进行分离。在乙醇 分离完全后,再以3兆帕斯卡/小时的速度缓慢释放压力,直至与外界大气压平衡,最后取 出纤维增强铝气凝胶材料。经测定,线性收缩率为20%。实施例9本实施例所制备的硅铝气凝胶复合材料为氮化硼纤维增强硅铝复合气凝胶,其中 硅铝复合气凝胶中的SiO2的比例以所述硅铝复合气凝胶的摩尔比计为80 %,硅溶胶制备条 件为将正硅酸甲酯、乙醇、去离子水和氨水按摩尔比为1 1 1 0.0008,以碱性催化剂 配成硅溶胶。铝溶胶的制备条件为将仲丁醇铝、乙酰乙酸乙酯、乙醇、水和氨水按摩尔比为 1 0.2 16 4 0.005,以碱性催化剂配成铝溶胶,后将所制得的硅溶胶和铝溶胶混合 均勻制得硅铝复合溶胶。直接将硅铝复合溶胶加入装有体积密度为0. 24g/cm3、单根纤维直径为1 μ m的氮化硼纤维的模具中,依靠重力浸渍,在60°C下凝胶6小时,后于室温在乙醇中 老化48小时,放入高压釜中,打入2兆帕斯卡的二氧化碳,在30°C下保温15小时。再升温 至50°C,并将二氧化碳以200升/小时的流量将乙醇带入分离釜进行分离。在乙醇分离完 全后,再以3兆帕斯卡/小时的速度缓慢释放压力,直至与外界大气压平衡,最后取出纤维 增强气凝胶复合材料。经测定,该硅铝气凝胶复合材料在800°C高温下的热导率为0. 08瓦 /米·开尔文,线性收缩率大于4%,达4.8%。由于实施例7中的硅气凝胶和实施例8中的铝气凝胶在800°C的时候均容易收缩, 因此无法测试热导率。实施例9中所制得的材料的收缩率4. 8%。本文中所描述的实施例仅仅是对本发明的优选实施例所作的举例说明。本发明所 属技术领域的技术人员可以根据本发明所公开的内容对所描述的实施例进行各种修改,但 是由此修改而得到的没有偏离本发明的实质的技术方案仍然落在所附权利要求书所限定 的范围之内。
1
本发明提供了一种硅铝气凝胶复合材料,其中,所述硅铝气凝胶复合材料包含(1)硅铝复合气凝胶;和(2)无机纤维材料;其中所述硅铝复合气凝胶是利用硅溶胶水溶液来制得;本发明还提供另一种制备所述硅铝气凝胶复合材料的方法,所述方法包括硅铝复合溶胶的制备、浸胶、胶凝、老化和超临界干燥等步骤。所述硅铝气凝胶复合材料具有优异的耐高温性能和力学性能,并且在高温条件下具有低热导率,可以满足航空、航天、军事方面苛刻热防护的要求,也能用于民用的隔热领域。
一种改性氧化铝气凝胶复合材料及其制备方法
- 专利详情
- 全文pdf
- 权力要求
- 说明书
- 法律状态
查看更多专利详情
下载专利文献
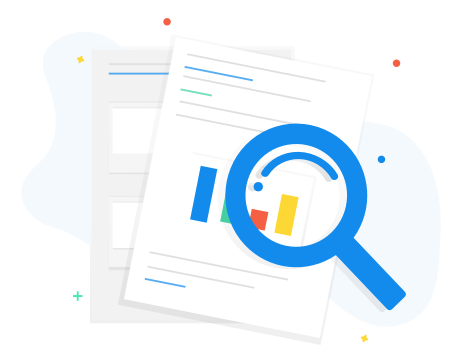
下载专利
同类推荐
-
希琳·巴赛斯, 布鲁斯·西布里希琳·巴赛斯, 布鲁斯·西布里希琳·巴赛斯, 布鲁斯·西布里
您可能感兴趣的专利
-
李贺军
专利相关信息
-
陈丹C·J·斯捷潘尼扬凌一心, 孙国庆凌沛学