专利名称:带有纤维胎的气凝胶复合材料的制作方法本发明的领域涉及气凝胶复合材料。更具体地说,本发明涉及气凝胶复合材料,其中与现有的气凝胶复合材料产品相比,得到的复合材料在一种或多种以下特性上显示出改善的性能减少的气凝胶烧结;较高的温度性能;改善的柔韧性和悬垂性;改善的耐久性;降低的气凝胶颗粒散落;增强的x-y平面导热性;增强的x-y平面导电性;增强的射频干扰(RFI)和/或电磁干扰(EMI)衰减;增强的红外辐射(IR)抑制;和/或增强的抗烧穿性。纤维增强材料优选是膨松纤维结构(纤维胎)、个体随机取向的短微纤维以及传导层的结合。更具体而言,两种纤维增强材料均基于有机(例如,热塑聚酯)或耐火(例如二氧化硅)纤维。已经改进保温材料,以解决大量物理问题。已知刚性聚合泡沫材料和玻璃纤维绝热板作为绝热体,在诸如制冷、土木建筑和供暖系统的领域中用于低温和高温应用。诸如那些由玻璃纤维制造的挠性纤维胎已经在需要柔韧性、低密度以及用以填充空隙的膨胀能力,诸如土木建筑应用中使用。人们改进气凝胶,更具体而言是气凝胶复合材料,以期结合两类材料的强度。气凝胶是一类基于其结构,即低密度、开孔结构、大表面积(通常是900m2/g或更高)和亚纳米级孔径的材料。超临界和亚临界流体萃取技术通常用于从材料的脆性孔中萃取流体。已知各种不同的气凝胶复合材料,其可以是无机或有机的。无机气凝胶通常基于金属醇盐,并且包括,诸如二氧化硅、碳化物和氧化铝的物质。有机气凝胶包括碳气凝胶和聚合气凝胶,例如聚酰亚胺。基于二氧化硅的低密度气凝胶(0.02-0.2g/cc)是优良的绝热体,优于100和大气压下导热率为10mW/m-K或更低的最佳硬质泡沫。气凝胶主要通过将传导(用于将热传递通过纳米结构的低密度、弯曲路径)、对流(非常小的孔径使对流最小化)和辐射(IR抑制掺合物可以容易地分散到整个气凝胶基质中)最小化而起绝热体的作用。根据配方,它们可以在550℃和更高的温度下很好地作用。但在整体状态下,它们趋于脆性并易碎,并因此不能很好地适用于实验室之外的大多数应用中。美国专利No.5306555(Ramamurthi等)公开了一种整体气凝胶与分散于整体气凝胶中的纤维形成的气凝胶基质复合材料,以及该气凝胶基质复合材料的制备方法。纤维可以是不同厚度的长或短纤维、单晶纤维、矿物棉、玻璃棉,甚至是颗粒。增强材料的组成是氧化物,例如SiO2和Al2O3(纤维、单晶纤维和棉)和碳、金属,以及各种氧化物(颗粒)。优选的纤维是玻璃棉和褐块石棉。纤维可以是随意分布或定向的。它们也可以是单独纤维、纤维束、垫状或片状、织造或非织造的形式。气凝胶基质复合材料基本上是无断裂和基本上无体积收缩的。复合材料是通过将凝胶前体浸入织造或非织造的预制纤维,随后在超临界条件下干燥湿凝胶而形成。产物可以在约3-7小时的范围内得到,但是主要缺点是弹性模量高,使产物同工业生产的一样非常僵硬。Ramamurthi等人的制品因其在气凝胶基质区域结构形成断裂而在使用时提高了柔韧性。第二个缺点是气凝胶基质复合材料的导热率还相对较高(与环境条件下本发明优选实施方案的8.6-14mW/m-K相比,为环境条件下18-21W/m-K)。美国专利No.5789075(Frank等)在Ramamurthi等人之后公开了与Ramamurthi等人相同的结构。除了所述结构从模塑中除去后,Frank等人的复合材料以受控方式有意断裂。据称受控断裂为所得复合材料赋予了额外的柔韧性。适合的纤维是随意的或有序的单个纤维,优选长度为至少1cm。可以使用网状或垫状纤维。多个网状或垫状纤维可以互相叠放。在纤维垫层状排列的情况下,在从一层到下一层方向上的变化被认为是有利的。虽然说明书和权利要求公开的生产方法包括步骤(b)“向溶胶中加入纤维”,但实施例只公开了将不含纤维的溶胶加入聚酯或玻璃纤维网中。单个随机分散的纤维未与纤维网结合使用。美国专利No.5972254(Sander)公开了超薄预压缩的纤维增强的气凝胶蜂巢结构催化剂整料。气凝胶、干凝胶、沸石和其它低密度材料的薄板或整料在三维的两个方向上用预压缩的纤维增强。金属醇盐、水和催化剂的混合物倾入含预先拉紧的增强纤维的气体可 透模型中,所述纤维在限定的间隔互相正交流动,随后聚合并超临界干燥。美国专利No.5973015和6087407(Coronado等)描述了用有机前体,例如,甲醛浸入预制纤维而制备的气凝胶复合材料。据称得到的复合材料具有机械稳定性。在附图中描述的增强纤维纵向排列并且在附图中显示呈平面结构。产物具有在空气中于高热负荷下热稳定性相对较低,以及对许多应用而言柔韧性不够的缺点。美国专利No.6068882(Ryu等)公开了由Aspen System公司在先制造和销售的气凝胶复合材料。产物的气凝胶成份是气凝胶粉末而非气凝胶整料。因此,产物的弯曲导致明显的大量粉末脱落。热性能与单独的气凝胶整料相比大大降低。现有的产物很硬,并且容易破裂或断裂。
因此,现有的气凝胶复合材料因以下一个或多个原因,对许多用途而言是不稳定的低柔韧性、低耐久性、当暴露于热量时过多的气凝胶烧结、低于理想导热率、x-y导热性和/或导电性不足、RFI-EMI衰减差,和/或抗烧穿性不足。
本发明针对解决这些问题而进行了研究。因此,本发明的目的在于制备显示以下一个或多个特性的改进气凝胶复合材料结构低烧结/高热温度性能;改进的柔韧性,特别是低导热率、悬垂性或顺服性;增强的x-y导热率和/或导电率;增强的RFI-EMI衰减;和/或增强的抗烧穿性。
发明概述本发明涉及在下列一个或多个方面比以前的气凝胶复合材料显示出改进性能的气凝胶复合材料柔韧性、耐久性、气凝胶烧结、x-y导热率和/或导电率、RFI和EMI衰减和抗烧穿性。
更特别地,本发明涉及有两个部分,即增强纤维和气凝胶基质的复合材料,其中增强纤维是膨松纤维结构形式(即,纤维胎),优选基于热塑聚酯或二氧化硅纤维,更优选与单个随机分散的短纤维(微纤维)结合。膨松纤维胎增强材料的使用使得未负载的气凝胶体积最小化,同时通常改善了气凝胶的热性能,不会象现有技术一样降解。而且,当气凝胶基质被膨松纤维胎材料,特别是由非常低纤度的纤维构成的连续非织造的纤维胎增强时,得到的复合材料至少保留了高柔韧性、悬垂性形式的整料气凝胶的热特性,使复合材料适于例如服装领域。
在非常高的热负荷下,例如那些通过气体/氧火炬火焰的直接表面接触产生的热负荷,整料气凝胶可以在数秒内迅速烧结并收缩。当气凝胶通过膨松纤维胎和微纤维结合增强时,如本发明的一个实施方案,绝热结构的收缩、烧结和最终破坏的速率可以延迟一个或多个数量级的时间,即烧穿时间从数秒增加至数小时。
更特别的是,已经发现还包括导热层的气凝胶复合材料有助于改进复合材料的热性能。例如,放置在复合材料中心的碳纤维布或单向性碳纤维的两个正交层在高热负荷下形成了热穿透阻隔层(thermalbreakthrough barrier),对IR高度不透过,以及形成在复合材料的x-y平面上将热量传播出去的热消耗层结构。更特别的是,可以选择在复合材料的中间,贯穿整个气凝胶复合材料厚度的导热层,以对复合材料的硬度具有最小影响。而且,如果需要,该层可以具有可塑性或内在的顺服性,以使得到的气凝胶顺服,例如,当复合材料弯曲时,放置在气凝胶复合材料制品内层的铜线网赋予其顺服性和可变形性。另外,导热网也提供了抗RFI和EMI性。
以下更详细地描述本发明的这些和其它实施方案。
附图简述
图1说明本发明的常规制备方法。
图2是本发明气凝胶复合材料的示意图。
图3是用作本发明增强材料的3层层压材料的分解图。
图4是用作本发明增强材料的另一备选3层层压材料的分解图。
图5是气凝胶复合材料的局部分解图,显示了使用长纤维胎在宏观上和微单丝在微观上增强的复合材料。
图6是用于本发明的另一备选5层层压材料的分解图。
图7是所制备的本发明的5种气凝胶复合材料在一定温度范围内的导热率图。
优选实施方案的描述气凝胶是一类在高于溶剂临界点的温度和压力下,通过从开孔聚合材料负载的凝胶结构的孔中除去流动的空隙间溶剂相而形成的材料。在全部溶剂的抽提过程中,通过将溶剂相保持在临界压力和温度以上,通过液体从非常小的孔蒸发产生的强毛细力引起收缩和孔破裂还未被认识。气凝胶通常具有低堆积密度(约0.15g/cc或更低,优选约0.03-0.3g/cc)、非常高的表面积(通常为约400-1,000m2/g和更高,优选约700-1000m2/g)、高孔隙率(约95%和更大,优选大于约97%),以及相对大的孔体积(大于约3.8mL/g,优选约3.9mL/g和更高)。在无定形结构中,这些特性的结合对任何粘结的固体材料产生最低的导热率值(在37℃和1个大气压下为9-16mW/m-K)。
对于被动绝缘体而言,气凝胶的一个最有吸引力的应用是以最低的能量消耗保持恒定温度或物体和其环境之间有效的δ温度。整料气凝胶结构在破裂之前通常具有最小的柔韧性(举例来说,二氧化硅气凝胶整料在0.1g/cc密度下具有0.5Mpa的挠曲模量)。
本发明的气凝胶复合材料包括两相。第一相是低密度气凝胶基质,而第二相是增强相。这个增强相主要由膨松纤维材料组成,优选膨松纤维胎与一种或多种厚度、长度和/或高径比明显不同的纤维物质组合。优选的两种纤维材料体系的组合是由短的、高径比高的微纤维(一种纤维材料)分散于整个气凝胶基质,所述气凝胶基质渗入连续的膨松纤维胎(第二种纤维物质)而产生的。
本发明可以通过图1-6理解。图1描述了本发明的制备方法,其中凝胶前体11加入在一些固定模型结构10中的增强纤维胎12中。图2显示了用无机或有机纤维胎21和气凝胶基质形成的本发明的气凝胶复合材料20。图3显示了用凝胶前体与成形为连续膨松的纤维胎材料的微纤维材料混合,以产生图4所示的复合材料。
本发明的气凝胶基质可以是有机的、无机的或其混合物。用于制备气凝胶的湿凝胶可以通过本领域技术人员公知的任何凝胶形成技术而制备例如将稀释的金属氧化物溶胶的pH和/或温度调节至产生胶凝的点(R.K.Iler,Colloid Chemistry of Silica andSilicates,1954,第6章;R.K.Iler,The Chemistry of Silica,1979,第5章,C.J.Brinker和G.W.Scherer,Sol-Gel Science,1990,第2和3章)。适用于形成无机气凝胶的材料是大部分能够形成氧化物的金属,例如硅、铝、钛、锆、铪、钇、钒等的氧化物。主要由水解的硅酸酯的醇溶液形成的凝胶因其容易得到并且成本低(醇凝胶)而特别优选。
本领域技术人员同样已知的是,有机气凝胶可以由聚丙烯酸酯、聚苯乙烯、聚丙烯腈、聚氨酯、聚酰亚胺、聚糠醇、苯酚糠醇、三聚氰胺甲醛、间苯二酚甲醛、甲酚甲醛、苯酚甲醛、聚乙烯醇二醛、聚氰脲酸酯、聚丙烯酰胺、各种环氧化物、琼脂、琼脂糖等形成(参见例如,C.S.Ashley,C.J.Brinker和D.M.Smith,Journal of Non-Crystalline Solids,卷285,2001)。但是,作为高温下在含氧气氛中的绝热制品,这些材料将会烧掉,因而不优选用于本发明。
为方便起见,下面用形成无机气凝胶的醇凝胶路线阐述本发明,但这并非为使本发明限制于任何特定类型的气凝胶和/或制备方法。本发明可用于其它的气凝胶和制备方法。
通常,用于形成无机气凝胶的常规合成路线是将适合的金属醇盐的水解和缩合。最适合的金属醇盐是在各烷基上具有约1-6个碳原子,优选1-4个碳原子的那些。所述化合物的具体例子包括四乙氧基硅烷(TEOS)、四甲氧基硅烷(TMOS)、四正丙氧基硅烷、异丙醇铝、仲丁醇铝、异丙醇铈、叔丁醇铪、异丙醇镁铝、异丙醇钇、异丙醇钛、异丙醇锆等。在二氧化硅前体的情况下,这些材料可以在低pH下部分水解和稳定,作为聚硅酸酯的聚合物,例如聚二乙氧基硅氧烷。这些材料可以醇溶液的形式从市场购买(例如,Silbond?40,40%二氧化硅含量,Silbond Corporation)。预聚合的二氧化硅前体特别优选用于本发明的气凝胶复合材料制品。
适合于形成低温下使用的气凝胶的材料是基于氧化物形成金属的非耐火金属醇盐。优选的所述金属是硅和镁及其混合物。对于高温应用而言,适合的醇盐通常是将形成氧化物的耐火金属醇盐,例如二氧化锆、氧化钇、氧化铪、氧化铝、二氧化钛、二氧化铈等,以及它们的混合物,例如二氧化锆和氧化钇。也可以使用耐火金属与非耐火金属混合物,例如铝与硅和/或镁。将多于一种金属氧化物基质材料用于气凝胶结构的优点在于IR不透性的增强,这是通过提供吸收更宽波长范围的辐射的化学官能团而实现的。
可以加入精细分散的掺杂剂,例如碳黑、二氧化钛、铁氧化物、碳化硅、硅化钼、镁氧化物、其中烷基含1-4个碳原子的聚二烷基硅氧烷等,以通过增加产品对IR传递的不透明度而改善高温下的热性能。所述掺杂剂的适合用量通常是最终复合材料的约1-20重量%,优选约2-10重量%。
在无机气凝胶形成方法中,主要变量包括醇盐的类型、溶液pH、以及醇盐/醇/水之比。控制变量就可以控制在从“溶胶”状态向“凝胶”状态整个转变过程中基质种类的生长和聚集。尽管前体溶液的pH和反应物的摩尔比对所得气凝胶的特性影响很大,但在本发明中可以使用能够形成凝胶的任何pH和摩尔比。
溶剂通常是低级醇,即具有1-6个,优选2-4个碳原子的醇,尽管也可使用其它液体,如本领域已知的。其它可用的液体的例子包括但不限于,乙酸乙酯、乙酰乙酸乙酯、丙酮、二氯甲烷等。
另一选择,也可以使用以下方法中的任一种以制备本发明的气凝胶复合材料制品,但优选能够得到最低密度和/或最佳绝热制品的方法。例如,在制备凝胶的第一可选方案中,通过在水中进行酸化,使水溶性的碱金属氧化物前体凝胶化,以制备水凝胶。硅酸钠已经被广泛用于这一目的。可以通过离子交换和/或通过随后用水洗涤形成的凝胶而从硅酸前体中除去盐副产物。可以使用极性有机溶剂,例如乙醇、甲醇或丙酮,通过交换从凝胶的孔中除去水。得到的干凝胶具有的结构与在相似溶剂中,通过凝胶的超临界萃取而直接形成的结构相似。第二可选方法是通过化学改性处于其湿凝胶态的基质材料,将表面羟基转化为三甲基甲硅烷基醚,降低溶剂/孔内界面上的破坏性毛细管压力(例如参见US5877100),使气凝胶材料在低于溶剂临界点的温度和压力下干燥。
对于含低温绝热体的二氧化硅气凝胶而言,目前优选的配料是四乙氧基硅烷(TEOS)、水和乙醇(EtOH)。TEOS与水的优选比例是约0.2-0.5∶1,TEOS与EtOH的优选比例是约0.02-0.5∶1,以及优选的pH是约2-9。配料溶液本身的pH是约5。可以使用任何酸以得到较低pH的溶液,HCl、H2SO4或HF是目前优选的酸。为了产生较高的pH,NH4OH是优选的碱。
对本发明的目的而言,膨松纤维胎定义为这样的纤维材料,其显示出堆积性能和某些弹性(有或无充分的体积恢复(full bulkrecovery))。优选形式是该材料的软网。膨松纤维胎增强材料的使用使得无支撑气凝胶的体积最小化,同时避免了气凝胶热性能的大幅退化。纤维胎优选是指纤维材料的薄层或薄片,通常用于填絮被,或用于填充物或包装的材料,或作为绝热的毛毡。
用于本发明的增强纤维材料是一层或多层膨松纤维胎。膨松纤维胎增强的使用使得无支撑气凝胶的体积最小化,同时避免了气凝胶热性能的大幅退化。尽管“纤维胎”通常是梳毛或回丝纤维以形成薄片状的纤维软网得到的产物,例如Albany International的产品Primaloft?,前提是它们充分疏松而“膨松”。纤维胎通常是指通常用于填絮被,或用于填充物或包装的材料,或作为绝热毛毡的纤维材料。适用于生产纤维胎的纤维相对精细,通常为15旦或更细,优选10旦或更细。网的柔软度是用于生产纤维网的相对精细、多方向取向纤维的副产物。
如果纤维胎充分含有很少的个体单丝(或纤维),因而与相同材料的未增强气凝胶体相比,不会明显改变增强的复合材料的热特性,那么对于本发明的目的而言,就是“膨松”的。通常这意味着当检查最终的气凝胶复合材料的横截面时,纤维的横截面面积低于横截面的总横截面积的10%,优选低于8%,最优选低于5%。室温和压力下,优选纤维胎的导热率为50mW/m-K或更低,以促进低导热率的气凝胶复合材料形成。
检测纤维胎是否在本发明范围内充分膨松的另一途径是评价其压缩率和回弹性。此时,膨松纤维胎是一种(i)其固有厚度的至少50%,优选至少65%,最优选至少80%被压缩,以及(ii)在压缩数秒后充分回弹,恢复为初始厚度的至少70%,优选至少75%,最优选至少80%。根据这一定义,膨松纤维胎是一种可以被压缩除去空气(胀量)而充分反弹至其原有尺寸和形状的纤维胎。例如,HolofilTM纤维胎可以由其最初的1.5”厚度被压缩至最小约0.2”,并且一旦除去负重就可以回弹至最初的厚度。该纤维胎可以视为含有1.3”空气(胀量)和0.2”纤维。其被压缩87%并基本上回弹至其初始厚度的100%。用于内部绝热(homeinsulation)的玻璃纤维胎可以被压缩至类似程度并回弹至初始厚度的约80%,但回弹相当慢。
此处使用的纤维胎基本上不同于纤维垫。纤维垫是“密集织造或稠密缠结的块状物”,即在相邻纤维之间具有最小开放空间的密实并相对较硬的纤维结构(如果有的话)。同时纤维垫通常具有大于25lbs/ft3(0.41g/cc)的密度,此处使用的膨松纤维胎具有更低的密度,即约0.1-16lbs/ft3(0.001-0.26g/cc),优选2.4-6.1lbs/ft3(0.04-0.1g/cc)。通常纤维垫的可被压缩度低于约20%,并显示出很少至没有回弹性。在用纤维垫增强制备的气凝胶复合材料中,垫纤维的横截面积最多是总横截面积的30-50%。
在凝胶形成液倾入后,优选纤维胎至少保留其50%的厚度。
此处使用的纤维增强材料需要敞开,是因为纤维增强趋于沿z轴进行(按照热流的方向),通过起热导管的作用而明显增加了所得复合材料的导热率。纤维胎具有高度校整(直)纤维,特别是在x-y水平面上,其比具有沿全部三个方向伸展的弯曲或卷曲纤维的相同密度的常规膨松纤维胎更硬。为了将z方向上的热流最小化(如同大多数绝热材料所需的),纤维胎应当沿z轴(热流的方向)具有低热流。因此,适合的纤维胎具有足量的沿z轴定向的纤维,以保持膨松,但所述量不应大到所得复合材料的绝热特性被这些纤维影响的程度。沿z轴的纤维可以是不同于x和y轴的材料(优选一种导热率较低的)。可以将z轴纤维制得更为迂回,使其比x-y方向的纤维提供更加曲折的导热路径。相同的纤维材料和方法可用于整个纤维胎,以使所有轴上的导热最小化,但在很多绝热应用中,只涉及特定方向上的热流,并且使用所述材料和方法会影响所得复合材料的柔性。理想的膨松纤维胎是一种带有均匀分散于整个复合材料中的精细,卷曲纤维的纤维胎。
用膨松纤维胎生产的复合材料是柔性耐用的,具有低导热率和良好的抗烧结性,气凝胶复合材料的性能通过将随机分布的微纤维混入复合材料而得以大幅增强,特别是微纤维在增加耐久性和减少粉尘的同时有助于耐烧结。短纤维增强材料(微纤维)对于复合材料性能的影响取决于很多变量,例如纤维排列、直径、长度、高径比(纤维长度/纤维直径)、强度、模量、拉断力(strain to failure)、热膨胀系数以及纤维和基质介面间的强度。微纤维是通过将其分散至凝胶前体液体并随后使用该液体渗入膨松纤维而混入复合材料中的。
此处使用的微纤维的直径通常在0.1-100μm范围内,具有高高径比(L/d>5,优选L/d>100),并且相对均匀地分布于整个复合材料。因为较高的高径比改善了复合材料性能,那么需要尽可能长的微纤维。但是,此处使用的纤维长度应当有所限制,以避免(至少是最小化)当含微纤维的凝胶前体注入纤维胎时所选纤维胎起到的任何过滤作用。微纤维应当足够短,以使膨松纤维胎的过滤作用最小化,但又足够长,以便最大可能地影响所得复合材料的热和机械性能。微纤维优选具有200mW/m-K或更低的导热率,以促进低导热率的气凝胶复合材料形成。
当微纤维分散于溶胶中时,它们通常快速沉降。为了克服上述问题,可以向溶胶中加入不会对形成凝胶产生负面影响的悬浮剂或分散剂。适合的悬浮剂/分散剂包括带有颜料亲合基团的大分子量嵌段共聚物(BYK-Chemie生产的Disperbyk184和192)的溶液等。试剂需要在至少微纤维分散于凝胶前体和溶胶凝胶化之间的时间段内产生作用。
在特定的气凝胶复合材料中使用的微纤维的用量、类型和/或尺寸,以及高径比可以变化,以符合特定需求。例如,一种应用可以涉及使用连续气凝胶复合材料的不同温度的绝热区;可以制造这样的复合材料,即多种微纤维存在于将与更高温度区域接触的复合材料的区域内。类似地,不同微纤维(例如不同材质、不同高径比,尺寸)可以混入上述区域,以取得最佳绝热性能。所述微纤维的改变可以通过使用不同悬浮剂和/或微纤维进行,使微纤维以不同速度沉降于复合材料中并因此分布于不同位置。
适合形成膨松纤维胎和微纤维的纤维材料包括任何纤维形成材料。特别适合的材料包括玻璃纤维、石英、聚酯(PET)、聚乙烯、聚丙烯、聚苯并咪唑(PBI)、聚亚苯基苯并二噁唑(PBO)、聚醚醚酮(PEEK)、多芳基化合物、聚丙烯酸酯、聚四氟乙烯(PTFE)、聚间亚苯基二胺(Nomex)、聚对亚苯基对苯二甲酰胺(Kevlar)、超高分子量聚乙烯(UHMWPE),例如SpectraTM、novoloid树脂(Kynol)、聚丙烯腈(PAN)、PAN/碳和碳纤维。
虽然相同的纤维材料可用于纤维胎和微纤维,但也可以使用不同材料的组合。一种所述组合是膨松玻璃纤维胎和和分布于其中的碳微纤维的组合。
如所指出,已经发现,纤维胎和微纤维增强的组合增强了抗烧结性。这可以通过在将凝胶前体倾入纤维胎之前,将适合材料的微纤维,例如碳单丝混入凝胶前体(通常与适合的非反应性分散剂结合)中而完成。图5是所述凝胶复合材料的分解图,其中复合材料用纤维胎51在粗纤维水平和碳纤维单丝52在细纤维水平上进行增强。当分散于二氧化硅基质中时,碳微纤维提供了IR不透明化和微观增强的结合,使得不耐火金属氧化物,例如二氧化硅在更高温度下的热和机械性能相对于未增强和不透明二氧化硅大大提高。
在本发明的另一实施方案中,膨松增强纤维胎以图3、4和6所示的多层层压材料形式使用。除了含有纤维材料胎之外,层压材料还可以含有有助于为最终产品提供特定特征的材料层。例如,在x-y平面中含有金属层,例如网能够改善x-y的导热性和/或导电性、RFI-EMI衰减、复合材料固定于载体结构的能力,和/或提供额外的物理强度。尽管任何金属均可用于制备金属网,但铜和不锈钢是目前优选的。适合的网可以由直径约0.001-0.1英寸、优选约0.01-0.05英寸的金属丝制成,并且金属丝间距可以从象纱窗一样紧密至0.3英寸。
当额外的层是高(>1W/m-K)导热率的材料,例如碳纤维、碳化硅或金属时,已经发现得到的复合材料显示出明显增强的将热量快速分散出多层复合材料的x-y平面的能力,进一步提高了高热量负载下复合材料的耐久性。
图3显示了一种3层层压材料,由一层膨松纤维胎32、精细的铜网31和第二层膨松纤维胎32组成。图4显示了另一种3层层压材料,由一层膨松纤维胎42、碳纤维织造织物41以及第二层纤维胎42组成。虽然图示的这些层压材料是对称的,但这是优选方案且并不构成限制。
当金属网用作一个或多个中间层时,其也为制得的气凝胶复合材料提供了这样的优点不仅具有悬垂性或柔韧性,而且还是顺服的,即弯曲之后仍保持其形状。
将传导率高的层引入复合材料的其它方法包括金属薄片,其中将薄片部分切割并弯出平面之外。这些弯曲的部分作为传导层和复合材料其余部分之间的固定物。类似地,也可以使用金属箔条,或所述材料的组合。
传导层具有大量的次要益处。可以将含金属传导层的气凝胶复合材料变形为某个形状并保持这一形状。图3的复合材料可以变形为简单和复杂的曲率。其仅能回弹至有限的程度,但可以有效地塑性变形,从而保持某个形状。传导层的其它益处在于其通常由结构纤维(坚固和连续)构成。该传导层可作为连接件材料,通过它可以驱动机械结合件。结合件可以紧扣于复合材料或传导层本身中。
复合材料负担的机械性负重可以通过金属传导层传递至结合件并传入其它结构中。一个例子是将气凝胶复合材料结合至汽车底盘,起隔热层的作用。如果增强材料被适当磁化,那么可以将其与含铁或磁性结构连接,而无需机械结合件。通过传导层传递的热量可以排入环境和/或冷源中(辐射、对流),或者用于驱动次级过程。例如,过量的热量可直接使用(加热水等),或通过Pelier元件等转化为电能。可以如此设计气凝胶复合材料,使壳层的较热一侧在表面附近具有传导层,仅在安装了Peltier元件的点上将热流流向壳层的较冷一侧。高导热率纤维的例子包括石墨、碳化硅、铜、不锈钢、铝等。
图6是层压材料的分解图,该层压材料由纤维胎层61、碳化硅毡层62、细铜网63、碳化硅毡层62和纤维胎层61组成。
在确定待制备的气凝胶后,制备合适的金属醇盐的醇溶液。气凝胶形成溶液的制备是本领域公知的。参见,例如S.J.Teichner等,Inorgabic Oxide Aerogel,Advances in Colloid and InterfaceSciennce,卷5,1976,245-273页,以及L.D.LeMay等,Low-DensityMicrocellular Material,MRS Bulletin,卷15,1990,19页。
尽管通常使用单一的醇盐-醇溶液,但也可以将两种或更多的醇盐-醇溶液用于配制混合的氧化物气凝胶。在醇盐-醇溶液形成后,加入水以进行水解,使得金属氢氧化物以“溶胶”态出现。使用四乙氧基硅烷作为例子的水解反应如下(1)为了形成气凝胶整料,该溶胶态醇盐溶液随后老化充分长的一段时间(通常过夜),使得发生缩合反应(如式2所示),并形成前体,之后超临界干燥为气凝胶。
(2)通过以下具体实施例进一步详细描述和解释本发明,其中描述了根据本发明制备气凝胶复合材料,以及由此得到的实验结果。除非另有说明,所有的份和百分比均按重量计。
实施例1将一段(2’×3’×1/4”)购自3M Company的聚酯Thinusulate?LiteLoft绝热材料置于有壁容器中。将1300ml市售预水解的二氧化硅前体(Silbond H-5)与1700ml 95%工业酒精混合。搅拌溶液15分钟。随后通过缓慢加入HF(溶液总体积的2%)并搅拌,使溶液凝胶化。将得到的溶液倾入预先置于容器中的壳层中。在几分钟内发生凝胶化。新鲜“壳凝胶”在密封的乙醇浴中于50℃老化过夜。通过亚临界和超临界CO2萃取超过四天,除去被凝胶吸收的醇。
得到的气凝胶复合材料所具有的密度为约0.1g/cc。通过ThinHeater Thermal Conductivity Test(ASTM C1114-98)测定的气凝胶复合材料的导热率为16.6mW/m°K。采用相同原料和制造方法制备的纯气凝胶整料的导热率为17.4mW/m°K。
气凝胶复合材料非常柔韧。可以将其悬垂绕过一个人的手臂而无外观损坏。该“悬垂测试”相当于半径约2”的曲率,180°弯曲。
当将壳层经受丙烷、液化石油气和甲基乙炔-丙二烯(MAPP)气的混合物,以及氧乙炔火炬火焰时,其表现出显著的抗传热和抗热降解/烧结性。如果用火焰将壳层从一侧加热,另一侧可以用裸露的皮肤接触而没有损伤。当直接暴露于火焰时,单独的聚酯纤维胎快速降解。而聚酯纤维胎增强的气凝胶复合材料在很大程度上抵御了聚酯的热降解(对于经受丙烷火炬火焰的1/4”厚的样品,瞬时烧穿约40秒烧穿)。只要聚酯保留于气凝胶基质中,复合材料就能够保持柔韧性并具有较低的导热率。如果火焰过于接近于气凝胶复合材料,将会发生烧穿。
实施例2重复实施例1的步骤,除了用带有聚乙烯醇粘结剂的密度为65g/m2的膨松二氧化硅纤维结构(Quartzel,来自Saint-Gobain Quartz)代替聚酯纤维胎。
在防护加热板(guarded hotplate)(ASTM C-177)上进行测试,得到的二氧化硅纤维胎/二氧化硅气凝胶复合材料的导热率为15.0mW/m-K。复合材料的柔韧性低于实施例1的气凝胶-聚酯壳层,但仍然显著。非常柔韧但不能悬垂相同的程度。气凝胶复合材料的密度为0.113g/cc。复合材料的厚度约3mm。当暴露于明火时,该复合材料的抗热降解性优于实施例1的产物。
由于纤维的存在,使得气凝胶的烧结显示最小。将氧乙炔火焰置于样品下5-6”,使得火焰的顶部与壳层的底部接触。在向火焰暴露5小时后,样品的底表面可见轻微烧结。样品的上表面在实验过程中可以用裸手接触。根据壳层和火焰源之间的距离,气凝胶复合材料的顶部温度在150-230℃之间变化。壳层的底部发出桔黄色-黄色的光。用高温计单次读取壳层底部黄色部分的温度,为1100℃。
实施例3重复实施例1和2的步骤,除了用聚酯/碳化硅/-16铜网/碳化硅/聚酯的5层纤维层压材料代替增强纤维胎。
导热率(通过ASTM C-177测试)为12.5mW/m-K(平均)。复合材料不是很柔韧性。层压材料的厚度为10.3mm。铜网通过将点负载(pointload)扩展到更大的面积而改善了x-y导热率。铜网也可以提供EMI-RFI屏蔽。由于增强聚酯和碳化硅纤维的存在,气凝胶的烧结显示最小。
实施例4重复实施例3的步骤,除了由聚酯纤维胎、带有聚合粘结剂的单向碳纤维、轻质铜网和膨松聚酯纤维胎的4层纤维层压材料组成增强材料。
导热率(通过ASTM C-177测试)为14.1mW/m-K(平均)。复合材料几乎没有柔韧性。层压材料的厚度为8.0mm。由于增强纤维的存在,气凝胶的烧结最小。
实施例5重复实施例3的步骤,除了增强材料的一侧由二氧化硅毡、不锈钢网和二氧化硅毡的约6”的3层纤维层压材料组成。还制备第二块增强气凝胶复合材料,其中铜网代替了不锈钢。
导热率(通过ASTM C-177测试)为12.4mW/m-K(平均)。复合材料一定程度上柔韧,并且是顺服的,能够保持为其弯曲的形状。层压材料的厚度为5.3mm。在火焰实验中,使用放置于距复合材料底部6”的氧乙炔火炬,并且接触面积为约2英寸直径(发红色-桔红色光),由于增强纤维的存在,气凝胶的烧结显示最小。复合材料边缘的温度为120℃(热电偶接触穿过顶部的钢网),而接触中心两英寸之外(尽管仍然在火焰正上方)的温度为60℃,处于稳态条件。
用铜网代替了不锈钢网的气凝胶复合材料显示出相同的效果。
实施例6重复实施例2的步骤,除了向二氧化硅溶胶中加入量中其它两种成分。第一种是低纤度碳纤维(Pyrograf III,来自Pyrograf产品的Grade PR-11-AG,Zenia,OH。)第二种是分散剂(来自BYK-Chemie的Disperbyk 184)。将2g碳纤维和6g分散剂加入1000ml烧杯中的750ml乙醇中。将烧杯置于冰浴并使用Misonix 2020声波破碎器以全功率进行声波破碎1小时,打碎纤维团块并形成目测稳定至少一小时的悬浮液。当将悬浮液滴置于玻璃片上并使其成片时,不会很快形成纤维团块。
得到的二氧化硅纤维胎/碳纤维/二氧化硅气凝胶复合材料的导热率为14.8mW/m-K(ASTM C-177)。复合材料的柔韧性略低于实施例2气凝胶的壳层(壳层#2),但仍然很明显。气凝胶基质在弯曲时宏观上趋于开裂。气凝胶复合材料的密度约为0.12g/cc。复合材料的厚度为约3mm。
当暴露于明火时,该复合材料的抗热降解性优于实施例2的气凝胶壳层。
将MAPP气体火炬用作火源。当施用于单独的石英纤维胎时,火炬将会使纤维胎缩拢并最终熔化。MAPP气体火炬与用于壳层#2的效果类似。如果将火炬喷嘴接近壳层#2,最后出现降解/烧结和烧穿。仅仅除底表面之外,该实施例的短碳纤维增强的气凝胶纤维胎显示未降解。使用MAPP气体火炬不会烧穿。在实验过程中,样品的顶部可以用裸手接触。根据火炬放置的距离,壳层的底部发桔黄-黄色-白色光。气凝胶烧结显示最小。长纤维和微纤维的结合增强远胜于单独的长纤维增强。
实施例7为了评价各种增强体系对于本发明的一种或多种实施方案的气凝胶复合材料的效果,根据实施例1的方法制备一系列复合材料,但改变增强材料。使用适合的溶胶渗入膨松增强材料并随后进行超临界干燥以制备气凝胶复合材料。图7显示了以下样品的热性能与温度关系的结果。
样品A使用低于2旦的膨松聚酯纤维胎,其中纤维的横截面积低于气凝胶复合材料的总横截面积的15%,并且在压缩后,膨松纤维胎恢复至其初始厚度的75%。
样品B使用由9μm纤维制备的石英棉,纤维胎密度为0.005g/cc,并且在压缩后,膨松纤维胎恢复至其初始厚度的75%。
样品C使用样品B的纤维胎,并结合了基于干燥复合材料总重量的5重量%碳黑掺杂剂,和3%(相同基准)碳微纤维。碳黑是CabotVulcan碳黑。碳微纤维直径为0.1-100μm,且长度为约1-2mm。使用了Disperbyk 184分散剂。
样品D使用样品B的纤维胎,并结合了基于干燥复合材料总重量的6重量%碳黑掺杂剂,和4%(相同基准)碳微纤维。碳黑是CabotVulcan碳黑。碳微纤维直径为0.1-100μm,且长度为约1-2mm。使用了Disperbyk 184分散剂。
样品E使用样品B的纤维胎,并结合了基于干燥复合材料总重量的6重量%碳黑掺杂剂,4%(相同基准)碳微纤维以及10重量%聚二甲基硅氧烷掺杂剂。碳黑是Cabot Vulcan碳黑。碳微纤维直径为0.1-100μm,且长度为约1-2mm。使用了Disperbyk 184分散剂。
样品E可以经受超过100,000次弯曲循环,其中的材料本身折叠,而热性能不损失。
具有膨松纤维胎增强材料的气凝胶复合材料,优选结合各自随机定向的短微纤维和传导层的一种或两种,其显示出一种或全部改善的以下特性柔韧性、悬垂性、耐久性、抗烧结性、x-y导热率、x-y电导率、RFI-EMI衰减和/或抗烧穿性。
带有纤维胎的气凝胶复合材料制作方法
- 专利详情
- 全文pdf
- 权力要求
- 说明书
- 法律状态
查看更多专利详情
下载专利文献
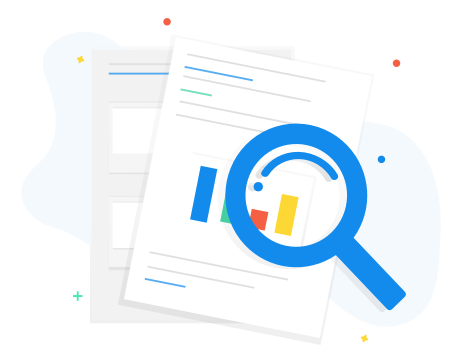
下载专利
同类推荐
-
希琳·巴赛斯, 布鲁斯·西布里代淑梅, 李秋园代淑梅, 李秋园代淑梅, 李秋园代淑梅, 李秋园
您可能感兴趣的专利
-
官培龙马延和马延和马延和马延和
专利相关信息
-
F-J·明特, J·博斯曼李章雨迈克尔·H·埃利, 迈克尔 H 埃利吕伟民