专利名称:两级惯性分离的平面流动分离器的制作方法本发明涉及锅炉内使用的高温分离器,特别是涉及一种循环流化床锅炉使用高温分离器。所有的循环流化床锅炉都设置高温分离器,以捕捉区灰循环燃烧,提高燃烧效率。现有技术中的循环流化床锅炉一般都采用旋风分离器,但这种分离器结构复杂,阻力高达100-150mm水柱,因之引起的引风电耗大,且当容量增加时其性能变劣,不利于锅炉的大型化。为了解决传统技术中使用的旋风分离器的不足和缺陷,中国专利申请85109455提供了一种S型高温分离器,这种分离器是一种单元组合砌筑型惯性平面流动分离器,它具有低阻力,低能耗,分离效率高,放大性能良好等一系列优点。可应用于4-35T/h的循环流化床锅炉。但该分离器须与一沉降室配合使用,当锅炉容量进一步增大时,随S型分离器单元数增加,通往沉降室的浓灰气流量也相当增加,浓灰夹带气流增大,沉降室气速增大,因而引起沉降室内细灰粒的二次扬析,进入尾部烟气,降低了分离效率。这就限定了锅炉容量的进一步增加。其二,该分离器在保证额定流速为15~30m/s下,由于其结构参数的原因,对于大于35T/h的锅炉,其单元器组合高度将高于3米,因此这对于分离器的结构稳定性是不利的。本发明的目的是为流化床锅炉,特别是循环流化床锅炉提供一种具有两级惯性分离的平面流动分离器,该分离器既能保持原S型分离器的一系列优点,也能在锅炉容量进一步增大时其分离效率不随容量的增大而降低,同时结构稳定,对同种容量的锅炉,能进一步提高分离效率和锅炉的燃烧效率。附图1为本发明的水平断面图。附图2为本发明在流化床锅炉上的安装示意图。它是通过下底板〔3〕安装在沉降室〔6〕之上。本发明是这样实现的整个分离器由砌体〔1〕和砌体〔2〕组成。其分离器单元包括两级环形通道和两级净化气流通道,浓灰气流通道和集灰腔。且两级环形通道的旋转方向相反,第二级环形通道的基准截面宽度为第一级环形通道基准截面宽度的20%-40%,第二级净化通道与相邻单元的第一级净化通道相通构成主出气口〔17〕,同时保证每个分离器单元的进口通道的外缘宽度应与第一级环形通道的基准截面宽度成一比例。下面结合本发明的具体结构及实施。每个分离器单元的砌体〔1〕和砌体〔2〕之间组成一系列水平气体通道。即进口通道(一)第一级环形通道(二),第一级净化通道(三),第二级环形通道(四),第二级净化通道(五),和第二次浓缩气流通道(六)。原始含尘气流由炉膛进入由砌体〔1〕之间构成的进口通道(一)和第一级环形通道(二)。为提高分离器的稳定性,设计时,应保证进口通道(一)的外缘宽度为第一级环形通道其准截面宽度的1.5-2.5倍。气流在进口通道和第一级环形通道中作旋转流动,在惯性力作用下,灰粒向外侧浓缩。位于一级环形通道未部的砌体〔2〕的一个契形端点〔7〕将气流分为两部分。净化气流通过第一级净化通道流出;被浓缩的气流流入第二级环形通道。第二级环形通道是由砌体〔2〕与第一级环形通道外侧的砌体〔1〕组成,其基准截面宽度应为第一级环形通道基准截面宽度的20%-40%,它的旋转方向与一级环形通道的旋转方向相反,于是迫使气流逆向旋转。一次浓缩气流又依靠惯性再次被浓缩。砌体〔2〕的另一契形端点〔8〕将二级环形通道分为两部分,即位于旋转内侧的第第二级净化通道V和二次浓缩气流通道(三),第二级净化通道与相邻单元的第一级净化通道连通构成主出气口〔17〕。二次浓缩通道通向集灰腔〔9〕,灰和部分气流向下运动通过下底板〔3〕上的落灰口〔10〕进入沉降室〔6〕。本发明由于采用了二级惯性分离,因此明显降低了浓灰气流中的含气量和烟气中的含尘量,进一步提高了分离效率和沉降室的处理能力,因而当锅炉容量进一步增大时,其分离效率稳定。同时由于改变了一级环形通道截面宽度与进口通道外缘截面宽度的比例关系,因此在相同锅炉容量下,即相同烟气处理量时,分离器单元组合高度可以降低一倍以上,保证了分离器的结构稳定性,对于130T/h以下的锅炉,使用该分离器,其分离效率和分离器结构稳定性均有明显提高。
实施例进口通道包括一个契形分割墙〔15〕,它位于第一级环行通道的外侧,其作用是增加气流的旋转角度和增加通过环形通道内侧的气体流量以尽快实现自由涡流动。在进口通道的砌体〔1〕上还设有一个集灰槽〔11〕,其作用在于使撞入基中的灰颗粒下滑返回炉膛,同时增加进口内侧气流湍动程度,有利于颗粒加速。第一级环形通道在与分离器轴线垂直的断面S的宽度α是整个分离器单元设计的基准。(S=α×nh为分离器总高度),α为200-400毫米,以250-300毫米为佳。第一级环形通道内侧为砌体〔1〕的一个凸园弧,它的半径r1为(40-50%)α,该园弧的终点切线与轴线成70°-90°夹角。一级环形通道外侧为砌体〔1〕的一个凹面,它可以由园弧面及其切面组成也可以由近似的折平面组成。平面〔12〕为与轴线平行的平面,折转30°成为平面〔13〕,再折转30°成为平面〔14〕,它们分别与以点O1为园心,以r1+α为半径的园相切。在平面〔14〕上设置集灰槽〔4〕,它的宽度为40-60毫米,以50毫米为佳,深度为100-150毫米,灰粒通过下底板〔3〕上的落灰口〔5〕流入沉降室〔6〕落灰孔〔5〕为与槽宽相同的正方孔。砌体〔2〕的契形端点〔7〕的顶点与园心O1的距离为r1+(0.6-0.8)α,它与O1的联级与轴线成0-15夹角,契形端点〔7〕是由两个与轴线成30°和75°的平面组成。30°的平面过渡为与轴线平行的平面,再与以O2为园心的园弧相切,构成第二级环形通道的外侧。以O2为园心,与平面〔14〕相切的园弧面构成第二级环形通道的内侧,环形内园半径为50-100毫米,以75毫米为佳,(其基准截面宽度为b)。内侧园弧旋转到与轴线垂直,然后沿切线延伸,外侧园弧旋转到与轴线成30°夹角,然后沿切线延伸。砌体〔2〕的另一楔形端点〔8〕与园心O2的距离为r2+0.8b,它与O2的连线与轴线成0°-15°夹角,契形端点〔8〕也是由两个与轴线成30°和75°夹角的平面组成。环形外侧面与契形面均过渡到与轴线平行进入集灰腔〔9〕,进入集灰腔的宽度C为(0.6-0.7)b,集灰腔水平截面积为(0.1-0.4)S。两单元轴线间的距离1.5-2.5α,以2α为好,按炉膛宽度布置单元数,其分离器总高度h应能保证与分离器轴线垂直的断面S处的气速为15-30米/秒,以25米/秒为佳。两级净化气体进口处,即过契形端点与内侧园的切线,通道下底板分别有一台阶,〔16〕,〔18〕,高度为50毫米,以阻档底部物料进入净化气体通道。
砌体〔1〕和〔2〕可选用碳化硅,钢玉或高强度耐火混凝土等耐火材料。
申请号87103655 申请日87.5.22发明创造名称 两级惯性分离的平面流动分离器
一种具有两级惯性分离的平面流动分离器,用于流化床锅炉,特别是循环流化床锅炉使用的高温分离器,该分离器是在原S型高温分离器的基础上,采用两级惯性分离,第二级环形通道的基准截面宽度为第一级环形通道基准截面宽度的20%—40%,并改变一级环形通道的基准截面宽度与进口通道外缘截面宽度的比例关系,即改变气体通道的流通量,因此当锅炉容量增大时,该分离器不仅能明显降低出口烟气中的含尘量及浓灰气流中的含气量,进一步提高分离效率,而且当锅炉容量增大时,其结构稳定性也有明显提高。
两级惯性分离的平面流动分离器制作方法
- 专利详情
- 全文pdf
- 权力要求
- 说明书
- 法律状态
查看更多专利详情
下载专利文献
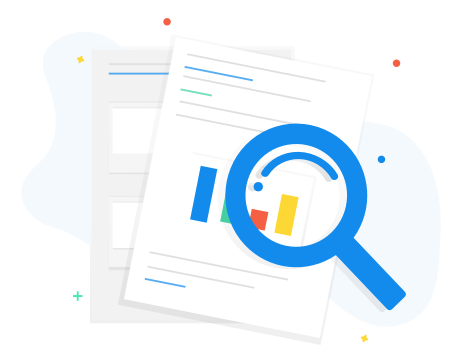
下载专利
同类推荐
-
张绪祎张绪祎张绪祎
您可能感兴趣的专利
-
韩成美刘顺兴刘顺兴刘顺兴刘顺兴刘顺兴
专利相关信息
-
杨顺才, 蔡军杨顺才, 蔡军杨顺才, 蔡军杨顺才, 蔡军刘怀军, 梁莹刘怀军, 梁莹刘怀军, 梁莹