专利名称:非水溶性聚谷氨酸纤维及其制造方法一般常见的高吸水性材料主要有两种,一种以丙烯酸化合物为主,而另一种则以 碳水化合物为主。以丙烯酸化合物为主的高吸水性材料,虽然其价格便宜,且具有不错的吸 水性,但由于其不具生物可分解性,在环境中不易被微生物分解,因此将其弃置于环境中或 掩埋于土壤中均会对环境造成危害。而另一种以碳水化合物为主者,如淀粉、几丁聚醣、海 藻酸钠及羧基甲基纤维素(carboxymethyl cellulose ;CMC)等多醣类,虽然其价格便宜, 且有良好的生物兼容性,但其对于水的吸收倍率有限。故,开发具备良好的生物兼容性的新 型高吸水性材料是有必要的。习知聚谷氨酸具有高吸水性,且亦具有良好的生物兼容性。然而,聚谷氨酸由于其 具有高吸水性及易溶于水的特性,致使其一接触到水即产生溶解现象,即便是放置于空气 中,亦会因快速吸收空气中的湿气(水汽)而溶解。因此未经处理的聚谷氨酸并不适用于 作为高吸水性材料,亦无法被纺成纤维。为使聚谷氨酸于吸水后不会溶解并能保有其结构 与成型外观,习知可藉由将聚谷氨酸经由交联处理来达成。习知聚谷氨酸的交联的方法可区分为物理交联法以及化学交联法。在物理交联法 中,例如日本专利特开平第6-322358号中揭示藉由γ -放射线交联技术交联聚谷氨酸水溶 液,藉以制作高吸水性水胶。但Y-放射线的设备复杂且昂贵,且不利于工业上生产。另外,化学交联法方面,习知系藉由使用一交联剂使聚谷氨酸进行交联反应。习知 的化学交联剂包含具有双醛基(Dialdehyde)、双胺基(Diamine)或双环氧基(Di印oxide) 等官能团的交联剂。例如,日本专利特开平第11-343339号提出利用由培养液中分离精 制的聚谷氨酸与二环氧化合物进行交联反应,藉以得到生物可分解的高吸水性水胶。另 外美国专利第6998367号揭示利用双醛基、双胺基、双环氧基及金属离子进行交联反 应,藉以制得非水溶性的吸水性胶体。美国专利第7125960号中,亦揭示使用戊二醛 (Glutaraldehyde)、乙二醇二环氧丙基醚(Ethylene glycol diglycidyl ether)及碳二酰 亚胺(Carbodiimide)等交联剂制得吸水性胶体颗粒。虽然上述习知方法已揭示可藉由交联技术获得非水溶性的聚谷氨酸胶体,但其吸 水性会大幅下降,且此种胶体型态会使其在生医材料领域的应用上受到限制。有鉴于习知 技术存在着上述这些缺点,故若能将聚谷氨酸纺制成非水溶性的纤维,将可有效解决此些 问题。但熟习技艺者均知,未经改质或处理的聚谷氨酸易遇水而溶解,并无法藉由习知纺纱 技术纺成纤维。虽然前述习知技术可藉由交联技术获得非水溶性的聚谷氨酸,但此些技术 仅能制得胶体,并未揭示任何可制成非水溶性聚谷氨酸纤维的技术。再者,该些专利所揭示 的非水溶性的聚谷氨酸胶体,因不具流动性,故亦无法藉由习知纺纱技术纺成纤维。为此,开发出一种非水溶性聚谷氨酸纤维的制备方法,以符合工业化生产需求,是有其需要性。
因此,依据本发明的一目的,在于提供一种非水溶性聚谷氨酸纤维的制备方法及 由其所制得的纤维,藉以克服前述习知技术中尚存的缺陷。依据本发明一实施方式所揭示的非水溶性聚谷氨酸纤维的制备方法,其包含 下列步骤。首先,制备初始黏度为%的聚谷氨酸的水溶液。之后,加入一交联剂至该 聚谷氨酸水溶液之中,使聚谷氨酸进行交联反应。接着,当该聚谷氨酸水溶液于黏度为 [n0+i/500(nf-n0)]至< nf的部份交联状态下,让该聚谷氨酸水溶液通过纺嘴进行纺 丝,其中上述的、为该聚谷氨酸水溶液爬竿时的黏度。最后进行后交联处理,使未反应的 交联剂反应完全。藉此即可制得非水溶性的聚谷氨酸纤维。依据本发明另一实施方式,提供一种通过前述方法所制得的非水溶性聚谷氨酸纤 维,依据上述方法所制得的非水溶性聚谷氨酸纤维,在水洗后的失重率不高于15wt%。图1是依据本发明一实施方式的一种聚谷氨酸纤维的制造方法流程图。主要组件符号说明102、104、106、108、110 步骤为 6-30wt%,另一
为6-25wt%。
4
于前述聚谷氨酸的水溶液中加入交联剂(步骤104),使聚谷氨酸进行交联反应。 由于聚谷氨酸具有多个自由的羧基(-C00H)可进行交联反应,所以交联剂较佳为具有两个 或两个以上可与羧基反应的官能团的化合物。例如,具有两个或两个以上环氧基、胺基、醛 基或双键的化合物。可应用于本发明中的具有环氧基的交联剂,包含但不仅限于聚缩水甘油醚类 (polyglycidyl ether)的交联剂。可做为本发明中聚缩水甘油醚类的交联剂的具体实 例,包含但不仅限于,乙二醇缩水甘油醚(Ethylene glycol diglycidyl ether)、二甘油 聚缩水甘油醚(Diglycerol polyglycidyl ether)、聚甘油聚缩水甘油醚(Polyglycerol polyglycidyl ether) &胃 fl 乙; 山 _ 酉享胃 _ H _ 81 (Polyoxyethylene sorbitol polyglycidyl ether)。可应用于本发明中的具有胺基的交联剂,包含但不仅限于乙二胺(ethylene diamine),此可参阅美国专利第5,279,821号。可应用于本发明中的具有醛基的交联剂,包含但不仅限于戊二醛 (glutaraldehyde),此可参阅美国专利第 6,699,367 与 7,125,960 号。可应用于本发明中的具有双键的交联剂,包含但不仅限于N,N’ -(1,2_ 二氢氧基 乙烯)(N,N,- (1,2-dihydroxyethylene))。由于交联剂的加入量太少时,将使聚谷氨酸的交联程度不够,遇水气会容易崩解。 但是交联剂的加入量太多时,又会残留未反应的交联剂而造成浪费,且可能会造成交联程 度过高而不适合纺丝。因此,依据本发明的制造方法,添加的交联剂的当量数与聚谷氨酸可 交联官能团(即羧基)的总当量数比的
为1 45-1 1,另一
为 1 15-1 1。依据本发明实施方式所揭露的制造方法,熟习技艺者均可了解的是,当加入交联 剂之后,交联剂即会与聚谷氨酸开始进行交联反应(步骤106)。此一交联反应纵使在常 温下亦会发生进行,故于本发明中交联反应温度并无特别的限制。但若基于商业化生产考 量,可藉由加热器来进行加温,提高交联反应温度,以增加交联反应速率。但由于聚谷氨酸 系为一种多肽分子,过高的温度将导致其变性(denature)或分解。因此,依据本发明一实 施方式所提供的制造方法,交联反应温度的
为35-85°C,又一
为 45-75 0C ο为提高前述交联反应的反应速率,习知技艺者经由本说明书的说明还可理解,除 提高交联温度外,还可经由对含有交联剂的聚谷氨酸水溶液加以搅拌(例如,藉由一搅拌 棒进行搅拌),以提高交联反应的速率。为使水溶性的聚谷氨酸变成非水溶性的聚谷氨酸,进行交联是必要的,但交联过 度却会使聚谷氨酸因黏度过高,而不易通过纺嘴进行纺丝。发明人经过反复实验后发现,若 可让聚谷氨酸进行部份交联后即进行纺丝,可使所得纤维不至于因接触到空气中的水气而 立即溶化。随后,再进行后交联反应,除可使聚谷氨酸纤维更不易遇水溶解外,亦可进一步 增强其机械性质。另外,由于在进行交联反应的过程中,聚谷氨酸水溶液的黏度会随着聚谷氨酸 交联程度的增加而增加,终至黏度过高而流动性不佳,致使无法进行纺丝,此时聚谷氨酸 水溶液中经部份交联的聚谷氨酸会顺着搅拌棒爬升,即产生所谓的「爬竿」现象。假设,配制好所需浓度的聚谷氨酸水溶液的初始黏度为%,而此聚谷氨酸水溶液经部份交联 后,在产生「爬竿」时的浓度为nf。因此,为制得本发明所述的非水溶性聚谷氨酸纤维, 具体的实施方式为交联反应至聚谷氨酸水溶液的黏度达到可纺丝黏度时,亦即其黏度为 [n0+i/500(nf-n0)]至< nf时,进行纺丝(步骤108)。另一
为当聚谷氨酸 水溶液的可纺丝黏度为[n0+i/4(nf-n0)] M [ n0+3/4( nf-n0)]时,进行纺丝。在此所述的纺丝技术系为纺织业界习用的纺织方法,可应用的纺丝技术包含干 纺、湿纺、电纺...等。习熟技艺者均知当利用湿纺技术进行纺丝时,需使用一凝固液使纺 出来的纤维定型,而利用干纺及电纺时则无须使用凝固液。故当利用湿纺技术进行纺丝时, 为配合本发明所使用的纺丝原料-聚谷氨酸,凝固液较佳为C1-C5的醇类、醚类或酮类。可 被应用于此的醇类,包含但不仅限于甲醇、乙醇、异丙醇或其组合。可被应用于本发明中的 醚类,包含但不仅限于乙醚、二甲醚(dimethylether ;DME)或其组合。可被应用于本发明中 的酮类,包含但不仅限于丙酮。由于熟悉本发明技术领域且具有通常知识者皆了解湿纺的 相关技术,且经由本发明说明书的教示当能自行决定如何组合运用的,故在此不再赘述湿 纺的其它相关细节。另外,由于当聚谷氨酸水溶液中加入交联剂后,交联反应会持续进行至反应完全 为止,加上湿式纺丝时需费时一段时间,才能使所有纺丝原料(经部份交联的聚谷氨酸)完 成纺丝步骤。故为避免部份已交联达到可纺丝黏度的聚谷氨酸在通过纺嘴纺丝前已交联至 无法纺丝的黏度,较佳为当聚谷氨酸水溶液为上述可纺丝黏度时,减缓交联反应的速率,以 利聚谷氨酸于通过纺嘴纺丝前均能处于半交联的状态以利湿纺步骤的进行。熟习技艺者经 由本发明说明书的教示可轻易了解到的是,若将前述交联、纺丝的动作以一连续化生产设 备进行操作,亦可于无须减缓交联反应速率的状况下执行。前述减缓交联反应速率的方式,只要是任何习知可用于减缓交联反应的手段均可 被应用于上述方法中而并无特别的限制。例如,可将已达纺丝黏度的聚谷氨酸的温度降低, 藉以降低其交联反应的速率。温度可降低至约4-10°C或约6°C以有效地减缓交联反应的速 率,又不会让聚谷氨酸水溶液凝固。降温的方法例如可为让聚谷氨酸水溶液置于冰浴中,或 是在后续的湿纺步骤中提供循环的冷凝水。依据另一实施方式,也可以加入阻滞剂来减缓交联反应的速率。上述的阻滞剂包 含但不限于具有胺基的化合物,例如D-谷氨酸(D-glutamic acid)。在获得聚谷氨酸纤维之后,进行烘干步骤(步骤110),以利处于部分交联状态的 聚谷氨酸纤维可以继续进行后面的交联反应(即后交联反应),并去除多余水份,以让聚谷 氨酸纤维结构更为坚固。由于烘干温度太高时,容易产生副反应,例如聚谷氨酸的分解反 应;而烘干温度太低时,交联反应速率又会太慢。因此,依据本发明一实施方式,烘干温度的
为25-90°C,另一
为35-85°C,又一
为45_75°C。而 烘干所需时间,依据本发明一实施方式为至少约20小时。以下实施例将对本发明聚谷氨酸纤维的制备方法及以其所进行的测试加以说明, 但非用以限制本发明的申请专利范围,任何熟悉于此项技艺中具有通常知识的人士可轻易 达成的修饰及改变,均涵盖于本发明的申请专利范围内。聚谷氨酸纤维的制备实施例1
取聚谷氨酸钠盐(取自味丹企业股份有限公司)加水配制成6衬%的浓度。之后, 于配制好的聚谷氨酸水溶液中加入作为交联剂用的乙二醇缩水甘油醚(Ethylene glycol diglycidyl ether,取自TOKYO YASEI)。相对于每IOOg的聚谷氨酸水溶液,交联剂的添加 量为7 μ L交联剂/g聚谷氨酸水溶液(交联剂/聚谷氨酸的当量数比为1/4)。前述聚谷氨 酸水溶液中加入交联剂后,以50rpm的搅拌速率于60°C下进行交联反应。聚谷氨酸水溶液 中加入交联剂后未进行交联反应的初始黏度为56. 4cp。于此条件下若不中止交联反应使其 持续交联至爬竿时(约5. 5小时),可测得此时的黏度为997. 2cp。为进行抽丝测试,将前述添加有交联剂的聚谷氨酸水溶液于前述条件下进行交联 反应,待黏度上升至82cp时(约240分钟),使其通过纺嘴进行抽丝。为避免尚未通过纺嘴 的聚谷氨酸水溶液持续进行交联,可将聚谷氨酸水溶液降温至6°C以减缓交联反应。将前述通过纺嘴抽丝所得的纤维,通入作为凝固液的异丙醇(取自景明化工,型 号为TG-078-000000-75NL)中,使其定型。之后,将所制得的聚谷氨酸纤维收集后,移至 60°C烘箱中烘干(约20小时)。藉此,即可顺利地制得聚谷氨酸纤维。实施例2操作条件大致上与实施例1相同,但聚谷氨酸水溶液浓度变更为10wt%,交联剂 添加量变更为5 μ L交联剂/IOOg聚谷氨酸水溶液(交联剂/聚谷氨酸的当量数比为1/9)。 于此条件下初始黏度为60. 2cp,爬竿黏度为1247. 4cp(约交联2. 3小时)。于本实施例中, 系交联至黏度达92. 3cp时(约40分钟)开始进行抽丝,即可顺利地制得聚谷氨酸纤维。实施例3操作条件大致上与实施例1相同,但聚谷氨酸水溶液浓度变更为15wt%,交联剂 添加量变更为5 μ L交联剂/IOOg聚谷氨酸水溶液(交联剂/聚谷氨酸的当量数比为1/14)。 于此条件下初始黏度为74. 6cp,爬竿黏度为964. 8cp(约交联2. 2小时)。于本实施例中, 系交联至黏度达152. Icp时(约90分钟)开始进行抽丝,即可顺利地制得聚谷氨酸纤维。实施例4操作条件大致上与实施例1相同,但聚谷氨酸水溶液浓度变更为20wt%,交联剂 添加量变更为6 μ L交联剂/IOOg聚谷氨酸水溶液(交联剂/聚谷氨酸的当量数比为1/15)。 于此条件下初始黏度为87. 8cp,爬竿黏度为1124cp(约交联1. 9小时)。于本实施例中,系 交联至黏度达185. 3cp时(约60分钟)开始进行抽丝,即可顺利地制得聚谷氨酸纤维。实施例5操作条件大致上与实施例1相同,但聚谷氨酸水溶液浓度变更为20wt%,交联剂 添加量变更为2 μ L交联剂/IOOg聚谷氨酸水溶液(交联剂/聚谷氨酸的当量数比为1/45)。 于此条件下初始黏度为83. 7cp,爬竿黏度为1012. 5cp(约交联2. 6小时)。于本实施例中, 系交联至黏度达133. 5cp时(约60分钟)开始进行抽丝,即可顺利地制得聚谷氨酸纤维。实施例6操作条件大致上与实施例1相同,但聚谷氨酸水溶液浓度变更为25wt%,交联剂 添加量变更为3 μ L交联剂/IOOg聚谷氨酸水溶液(交联剂/聚谷氨酸的当量数比为1/40)。 于此条件下初始黏度为96. 3cp,爬竿黏度为1221. 9cp(约交联1. 6小时)。于本实施例中, 系交联至黏度达225. 6cp时(约60分钟)开始进行抽丝,即可顺利地制得聚谷氨酸纤维。比较例1
操作条件大致上同实施例4,但仅使聚谷氨酸水溶液进行交联反应至黏度值比初 始黏度高一点(约为87. 9cp,交联反应时间约为10分钟),即进行抽丝。结果显示,由于交 联程度不足,虽可于凝固液中形成纤维,但当此纤维离开凝固液后,仅暴露于空气中30秒, 即会因吸收空气中水汽而溶解,而无法持续呈现纤维型态。比较例2操作条件大致上同实施例4,但使聚谷氨酸水溶液进行交联反应至黏度值比爬竿 黏度高一点(约为1130cp,交联反应的时间约为2小时),后进行抽丝。但此时聚谷氨酸水 溶液黏度已超过爬竿黏度(已爬竿),并成为具有弹性的固体,故难以通过纺嘴进行抽丝。聚谷氨酸纤维的特性测试实施例7将实施例1-6中所制得的聚谷氨酸纤维分别进行纤维吸水率,及水洗后失重率的 测试,以检测其是否能既维持其高吸水率,又能稳定地维持其构形。上述两种测试所得数据 皆列在下面的表一的中。表一聚谷氨酸纤维的测试 在上述纤维吸水率的测试中,系先让聚谷氨酸纤维于过量的去离子水中充分吸水 之后,再移除多余水分。接着,量测聚谷氨酸纤维吸水前后的重量差,藉此即可量测出聚谷 氨酸纤维可吸收多少倍本身重量的水分。纤维吸水率的计算方法如下式(I)所示(吸水后重-吸水前重)/吸水前重(I)而在上述水洗后失重率的测试中,会先让聚谷氨酸纤维于过量的去离子水中充分 吸水再静置1小时后,再移除多余水分。接着让吸水后的聚谷氨酸纤维于烘箱中干燥至恒 重为止,再进行秤重以测量其失重百分比。纤维水洗后的失重百分比的计算方法如下式 (II)所示(水洗前重-水洗后重)/水洗前重X100% (II)由上表一的纤维吸水率结果可知,由前述实施例1-6的聚谷氨酸纤维的制造方法 所制得的聚谷氨酸纤维仍能保有相当高的吸水率,可吸收高达本身重量150倍以上的水 分。而且更惊人的是,在吸收150倍重量的水分之后,还能维持其构形至少一个月而仍不崩解。另外,由表二的水洗失重的测试结果可知,聚谷氨酸纤维在静置吸水1小时再烘 干后,其失重率均可小于15wt%。此结果显示,根据本发明聚谷氨酸纤维的制造方法所制得 的聚谷氨酸纤维确实可克服习知技术无法将聚谷氨酸制成纤维的问题,亦可同时获致吸水 后失重率小于15衬%的「非水溶性纤维」。上述的测试结果,显示前述的聚谷氨酸纤维的制造方法及其所得的聚谷氨酸纤维 已经彻底解决习知聚谷氨酸纤维的难以成型及难以长时间维持其构形的两大难题。
虽然本发明已以实施方式揭露如上,然其并非用以限定本发明,任何熟习此技艺 者,在不脱离本发明的精神和范围内,当可作各种的更动与润饰,因此本发明的保护范围当 视后附的权利要求所界定者为准。
本发明提供一种非水溶性聚谷氨酸纤维及其制造方法。在其制造方法中,使聚谷氨酸以交联剂进行交联,并于部份交联状态下通过纺嘴进行抽丝,以形成聚谷氨酸纤维。藉此,即可使习知无法纺丝的高吸水性聚谷氨酸得以被纺成纤维并仍保有良好的吸水性。
非水溶性聚谷氨酸纤维及其制造方法
- 专利详情
- 全文pdf
- 权力要求
- 说明书
- 法律状态
查看更多专利详情
下载专利文献
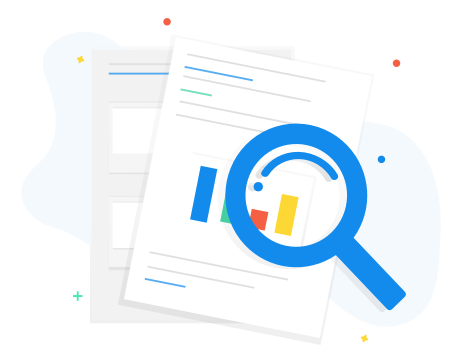
下载专利
同类推荐
-
代淑梅, 李秋园代淑梅, 李秋园代淑梅, 李秋园代淑梅, 李秋园代淑梅, 李秋园
您可能感兴趣的专利
-
马延和马延和马延和F-J·明特, J·博斯曼F-J·明特, J·博斯曼迈克尔·H·埃利, 迈克尔 H 埃利
专利相关信息
-
吕伟民吕伟民张根源D·索默, U·斯图茨李晓杰, 车景超林育忠