专利名称:一种用高酸值油脂制备生物柴油的方法众所周知,能源问题是经济发展的首要问题,是长期制约经济发展和社会发展的瓶颈,而我国石油资源贫乏,约有阳%的石油要依赖进口,2011年全国柴油年需求量约为 113880万桶,发展能替代石化柴油的生物柴油已成当务之急,以废弃动植物油脂、等为原料生产可再生的清洁能源,减少了环境污染,杜绝了垃圾油再次走向餐桌,保护了广大人民群众的身心健康;加工使用生物柴油,对推进能源替代,减少碳、硫、碳氢化合物、致癌芳香烃、 废微粒状物等有害物质的排放,保护大气环境,维护能源安全和生态环境治理具有十分重大的战略意义;随着世界范围内石油资源的日益枯竭以及人们环保意识的提高,提高了世界各国对生物柴油的研发热情,国外多以转基因植物油为原料,成本高,存在着与人和动物争抢油源的矛盾,不适合中国国情;国内生产企业多以地沟油、酸化油、潲水油、脂肪酸等废弃动植物油脂为原料生产生物柴油,由于其原料来源复杂,目前生产多采用高温高压工艺 (温度大于150°C),或超临界工艺(温度大300°C),工艺复杂,设备投资大、成本高,间歇生产、人工控制,生产效率低、生产中有废酸水排放,需后处理;产品质量不稳定,达不到产业化要求。
本发明的目的在与改进已有技术的不足而提供一种设备投资少、工艺简单、生产成本低、反应速度快、产品转化率高的用高酸值油脂制备生物柴油的方法。本发明的目的是这样实现的,一种用高酸值油脂制备生物柴油的方法,其特点是该方法包括以下步骤a、将脱水除渣的高酸值油脂与甲醇按质量比41的比例混合,升温至58-62C。,按原料油重的1-3%计量加入复合酸催化剂,经静态超微分散装置、多功能细化接触反应器,连续进入到酯化反应装置,油脂原料与甲醇在以上各装置和管线中进行了充分的反应,当物料达到酯化反应装置容量2/3时,停止进料,取样检测酯化反应进程,若反应未完成,则打开釜底循环泵和循环管线经第二静态超微分散器、多功能细化接触反应器、第三静态超微分散器进一步反应,直到反应完成,若循环过程中温度不足可采用换热器升温,保持反应温度在58-62°C。当物料酯化反应完成后,闪蒸脱去粗甲醇;b、在脱甲醇后的料液中,打入高酸值油脂原料量20-30%的浓度为2-3%氢氧化钾甲醇溶液,打开循环泵和循环管线经静态超微分散器组、多功能细化接触反应器进入到反应釜开始酯交换反应,若循环反应过程中温度不足可采用外置式换热器加热,保持反应温度在 58-62°C,反应过程中检测酯交换转化率,待反应结束后,再闪蒸脱粗甲醇;c、脱粗甲醇后的料液打入到带保温的锥形沉降罐,静置沉降4-5小时,分离除去甘油,得粗生物柴油;d、粗生物柴油根据其质量指标的差异,分别进行脱色或减压精馏处理,若产品酸值 ^ 0. 8mgK0H/g ;碘值彡80gI2 /IOOg则进行脱色处理,其终端产品为车船柴油机用生物柴油,产品技术指标应满足中华人民共和国BD100标准GB/T 20828-2007 ;若产品酸值 (1. 5mgK0H/g ;碘值> 80gI2 /IOOg则进行减压精馏处理,其终端产品为化工原料脂肪酸甲酯。为了进一步实现本发明的目的,可以是所述的复合酸催化剂由10-20%的乙酸、 10-20%的甲磺酸、15-30%的苯磺酸、15-30的乙二酸、0-50%的硫酸组成。本发明与已有技术相比具有以下显著特点和积极效果本发明方法总结了国内外现有工艺的优缺点,并进行了大量的小样实验,综合分析了各项实验数据,增添融进了静态超微分散技术和多功能细化接触反应器,本发明采用的静态超微分散装置是一种先进的单元设备,它的内部没有运动部件,主要运用流体流动和内部单元实现各种流体的混合,其特殊合理的结构设计与孔板柱、文氏管、搅拌器、均质器等其它设备相比较具有效率高、能耗低、体积小、投资省、易于连续化生产优点;采用静态超微分散器组能够能使料液在挤压,强冲击与失压膨胀的三重作用下超微细化,增加流体层流运动的速度梯度产生“分割-位置移动-重新汇合”或形成湍流,湍流时还会在断面方向产生剧烈的涡流,形成很强的剪切力作用于流体,使流体进一步分割混合,达到各物料间分子层面的充分接触;多功能细化接触反应器分上下两部分,内有填料,用作细化接触反应器时,从顶部进料,可提高非均相物料的接触面积和接触时间,降低能耗,提高反应速度和产品质量;另外多功能细化接触反应器从中部进料能兼作闪蒸釜用,生产中用其脱粗甲醇,不必重上闪蒸设备,可节省设备投资和维护成本;采用多功能细化接触反应器可进一步增加疏水相原料脂肪酸和甘油酯与亲水相甲醇的分子接触面积和接触时间,采用该发明工艺技术解决了反应物料的两相混合、反应传质和传热问题,有效的提高了反应速度和设备利用率,降低了反应温度,缩短了生产周期,反应时间由传统的5-8小时降低到1. 5-2小时,可提高反应速度2. 0倍,省去了搅拌装置,降低设备投资和生产成本;针对生产工艺中对设备的高温耐酸、碱防腐要求,本装置中采用了外置式耐酸、碱换热器,外置式装置方便维修、维护,同时也降低了其他设备的参数要求,除了换热器,其他装置采用了钢衬塑复合料,可适应工艺参数要求,并节省了设备投资;另外本发明工艺在生产控制上设计采用了 DCS自动化控制系统代替手工控制,提高了控制的精度和生产效率,增加了设备运行的稳定性和安全性,且降低了能耗和人工费用;本发明工艺技术科学先进,布局合理,生产过程稳定,控制系统可靠,符合环保要求,实现了生产的连续化与规模化,各种资源得到了最大化利用,与传统工艺体系相比可提高反应速度2 倍、产品收率率10%以上,节能降耗35%以上,达到了产业化技术要求,该工艺技术的推广应用,可产生巨大的经济效益、社会效益和环境效益。
a、将6吨脱水除渣的高酸值油脂与1. 5吨甲醇互相混合,升温至58-62C。,计量加入 120公斤复合酸催化剂,经静态超微分散装置、多功能细化接触反应器,连续进入到酯化反应装置进行酯化反应,当物料达到酯化反应装置容量2/3时,进料完毕,取样检测反应进程,若反应未完成,则打开循环泵和循环管线进行内循环,当物料酯化反应完成后,反应液酸值彡2. 0mgK0H/g时,闪蒸脱去粗甲醇;
b、在脱甲醇后的料液中,打入原料量1.2吨的浓度为2. 5%氢氧化钾甲醇溶液,打开循环泵和循环管线经静态超微分散器组、多功能细化接触反应器进行酯交换反应,若循环反应过程中温度不足可采用外置式换热器加热,保持反应温度在58-62°C,反应过程中检测酯交换转化率,待反应结束后,再闪蒸脱粗甲醇;
c、脱粗甲醇后的料液打入到带保温的锥形沉降罐,静置沉降4-5小时,分离除去甘油, 得粗生物柴油;
d、粗生物柴油根据其质量指标的差异,分别进行脱色或减压精馏处理,若产品酸值 ^ 0. 8mgK0H/g ;碘值彡80gI2 /IOOg则进行脱色处理,其终端产品为车船柴油机用生物柴油,产品技术指标应满足中华人民共和国BD100标准(GB/T 20828-2007);若产品酸值 (1. 5mgK0H/g ;碘值> 80gI2 /IOOg则进行减压精馏处理,其终端产品为化工原料脂肪酸甲酯;
所述的复合酸催化剂由10-20%的乙酸、10-20%的甲磺酸、15-30%的苯磺酸、15-30的乙二酸、0-50%的硫酸组成,是采用以下方法生产
a、在1#反应釜中加入重量为A的甲醇,打开搅拌,搅拌速度为60-70r/m ;
b、向反应釜中加入甲醇重量A的6%的苯磺酸和甲醇重量A的6%的乙二酸,维持釜内温度在20°C -30°C,温度不足打开加热系统加热;
c、取甲醇重量A的4%的甲磺酸和甲醇重量A的4%的乙酸,保温25°C左右,甲磺酸与乙酸在此温度下呈液态状态,将其加入到反应釜中搅拌均勻,得到1号催化剂料液;
d、在2#反应釜中加入重量为B的甲醇,打开搅拌,搅拌速度为70-80r/m,缓慢加入甲醇重量B的20%的纯硫酸搅拌均勻,得到辅配催化剂料液F ;
e、将1号催化剂料液与辅配催化剂料液F按1:0,2:1,1:1的比例分别调配混勻即得1 号、2号和3号催化剂料液;
f、将1号、2号、3号催化剂料液分别用甲醇稀释2-5倍,与油脂原料按1:3的比例配料生产生物柴油,以上三种催化剂料液可分别用于不同的生产原料,其中低酸值、低水杂的油脂原料用1号催化剂料液;中酸值、中水杂的油脂原料采用2号催化剂料液;高酸值、高水杂的油脂原料采用3号催化剂料液;高、中、低酸值的划分范围为低酸值油脂原料< 30 mgK0H/g,中酸值油脂原料30-80 mgK0H/g,高酸值油脂原料> 80 mgK0H/g ;
本发明中所使用的静态超微分散装置、多功能细化接触反应器以及酯化反应装置均为常规装置。
本发明公开了一种用高酸值油脂制备生物柴油的方法,是将高酸值油脂与甲醇按混合,加入复合酸催化剂,进行酯化反应,闪蒸脱去粗甲醇,打入氢氧化钾甲醇溶液,进行酯交换反应,再闪蒸脱粗甲醇,脱粗甲醇后的料液静置沉降4-5小时,分离除去甘油,得粗生物柴油,本发明具有设备投资少、工艺简单、生产成本低、反应速度快、产品转化率高的特点。
一种用高酸值油脂制备生物柴油的方法
- 专利详情
- 全文pdf
- 权力要求
- 说明书
- 法律状态
查看更多专利详情
下载专利文献
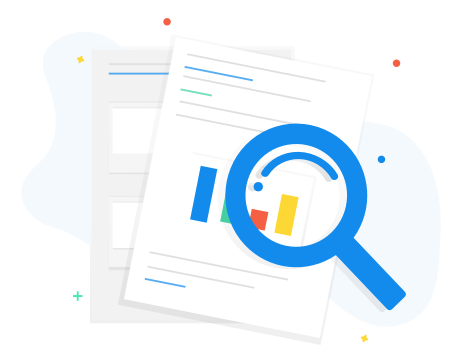
下载专利
同类推荐
-
余愚马丁·哈德, 格哈德·森格山下秀人, 饭岛好隆李鹏程
您可能感兴趣的专利
-
吴超, 李百健川崎成辉, 野田龙治川崎成辉, 野田龙治彭雅莉, 胡飞彭雅莉, 胡飞
专利相关信息
-
中西惠, 棚桥一裕后藤直宏后藤直宏崔正忠, 韩芳吴海燕