专利名称:多硫化物在改进的蒸煮中的用途的制作方法多硫化物(PS)是商业上用来增加制浆得率的制浆添加剂。更高的制浆得率通过 减少木材消耗和/或增加纸浆生产能力来改善工艺经济性。多硫化物在商业上由包含在硫 酸盐法制浆碱溶液中的部分硫离子的催化氧化来生产,在硫酸盐法制浆领域中硫酸盐法制 浆碱溶液经常被称为“白液”。该氧化工艺是目前商业上最可行的将白液中的硫化物转换成 多硫化物的技术,其赋予得到的溶液橙色。因此,多硫化物碱液在本领域称为“橙液”。已经发现,多硫化物仅在应用于蒸煮开始时有效增加制浆得率,例如应用于温 度通常低于 140°C ( 284下)并且保持时间通常为15-45分钟的浸渍阶段。在 140°C ( 284下)或高于这个温度,多硫化物开始快速分解并失去其作为制浆得率增强剂 (enhancer)的效能。已经发现,源自多硫化物制浆的制浆得率增加随添加到蒸煮开始的多 硫化物的量成比例增加(多达约7%的多硫化物填充到木材上)。因此在多硫化物制浆中, 所有多硫化物溶液(橙液)最优选添加到蒸煮的开始,以使制浆得率增加最大化。该特征 适在传统的硫酸盐法制浆情况下运行良好。在二十世纪七十年代晚期前一直是仅有的商业 惯例的常规硫酸盐法制浆中,蒸煮所需的总用碱量添加到蒸煮的开始。在二十世纪七十年代晚期发展的改进的硫酸盐法制浆(改进的蒸煮)中,总用碱 量被分为至少两次添加,并且经常多于两次。通常,总碱中仅有约45-75%添加到改进的蒸 煮的开始。通过使总用碱量分为几次添加到不同的蒸煮阶段,改进的蒸煮中的碱浓度分布 在整个蒸煮中比传统硫酸盐法制浆更加平均。早期蒸煮阶段中的有效碱(EA)浓度具有特 殊的重要性,该阶段中蒸煮温度从通常彡135°C ( ^ 275 T )的浸渍温度增加到通常在150 到175°C (302到347 T )之间的充分蒸煮温度。在该早期蒸煮阶段中的有效碱浓度非常高 的时候,制浆得率和纸浆强度出现过多损失。因此,改进的蒸煮具有更平均的碱分布,特别 地在早期蒸煮阶段具有较低的有效碱浓度,这导致制浆得率和纸浆强度相比传统硫酸盐法 制浆显著更高,在传统硫酸盐法制浆中,总用碱量全部被添加到蒸煮的开始并且在早期阶 段有效碱浓度高。然而,在目前的商业多硫化物制浆技术应用于改进的蒸煮时,由于仅45-75%的含 有多硫化物的碱液添加到蒸煮的开始,因此全部可用多硫化物中仅有45-75%添加到蒸煮 的开始。结果,正如前面所讨论的,因为得率增加与添加到蒸煮开始的多硫化物的量成比 例,因此相比使用多硫化物的传统蒸煮,仅实现总制浆得率增加的一小部分。这意味着在现 有技术中,目前改进的蒸煮不能充分利用多硫化物制浆实现最大得率增加。换言之,目前改 进的蒸煮技术并不与目前的商业多硫化物制浆技术完全相容。本发明克服了改进的硫酸盐法制浆与目前商业上的多硫化物制浆技术的上述不相容性。本发明获得了与传统蒸煮相比的改进蒸煮的所有益处,并且获得了多硫化物制浆 的充分得率增加。
本发明包括涉及硫酸盐法制浆的方法,该方法采用在蒸煮容器中与多硫化物制浆 技术结合的改进的蒸煮过程,从而获得与现有技术中所教导的没有多硫化物的改进蒸煮、 具有多硫化物的传统蒸煮或应用于改进的蒸煮的多硫化物制浆所获得的得率相比更高的 得率。在本发明中,多硫化物溶液形式的所需的全部蒸煮碱剂量被添加到蒸煮的开始,通常 是浸渍阶段,正如传统蒸煮的情况。在浸渍阶段末端时,在所有多硫化物基本都与木素纤维 素材料(lignocellulosic material)在低于 135°C ( 275 °F )的温度——在该温度或 低于该温度不发生显著碳水化合物降解——下反应以增加制浆得率时,例如靠近浸渍阶段 末端时,有效碱(EA)浓度高的蒸煮液的一部分(第一量)从蒸煮过程中移走并被从另一工 艺点移走的有效碱浓度低的蒸煮液(第二量)代替,其中第二量可以等于、大于或小于第一 量。然后,所移走的第一量的蒸煮液被加入制浆过程中有效碱浓度低的其它地方,例如靠近 第二量的蒸煮液被移走的地方。通过进行这种蒸煮液“交换”,实现了来自多硫化物制浆的 全部得率益处,而同时也实现了更均勻的有效碱浓度分布,从而从改进的蒸煮获得更高的 制浆得率和更高强度的益处。更具体地,本发明在实施方式中包括以下步骤(a)将全部用碱量以多硫化物溶 液的形式在蒸煮的第一阶段添加,该第一阶段在约15-45分钟内,100-140°C之间操作;(b) 在第一阶段末端时,从容器移走第一量的有效碱(EA)浓度相对高的蒸煮液,其在随后的阶 段中添加返回至容器;(c)在第一阶段末端添加第二量的蒸煮液,其从随后的蒸煮阶段中 移走,并且其有效碱浓度相对较低;(d)将蒸煮加热到充分蒸煮温度;(e)其中第二量的蒸 煮液在达到充分蒸煮温度后被移走约0-200分钟;(f)在蒸煮过程中比第一量的蒸煮液移 走点较晚的阶段,将该第一量的蒸煮液添加到容器中,或添加到另一蒸煮过程中;以及(g) 继续蒸煮直至完成。第一蒸煮液和第二蒸煮液的量,以及第一蒸煮液和第二蒸煮液的移走 点和添加点或次数受到控制,从而获得与目前改进的蒸煮相似并且比传统硫酸盐法制浆更 均勻的有效碱浓度分布。结合附图,本发明的上述和其它目的和优点可从下面详细说明中明显看出,其中 所有附图中相似的标号字符指示相似部分,其中图la和lb是根据本发明的优选实施方式的蒸煮过程的示意流程图;图2是比较下述方法的筛选过的纸浆得率增加的图表改进的蒸煮(MC-Ref)、具 有多硫化物的传统硫酸盐法(CK-PS)、具有多硫化物的改进的蒸煮(MC-PS)、和相对于传统 硫酸盐法(CK)伴随本发明增强的多硫化物工艺的改进的蒸煮(MC-EPS),其中卡伯值为15, 该卡伯值源自添加0.05% (在绝干木材(0D wood)上)蒽醌的混合的美国南方硬木的实验 ^^ ^^^、,图3是比较下述方法的筛选过的纸浆得率增加的图表改进的蒸煮(MC-Ref)、具 有多硫化物的传统硫酸盐法(CK-PS)、具有多硫化物的改进的蒸煮(MC-PS)、和相对于传统硫酸盐法(CK)伴随本发明增强的多硫化物工艺的改进的蒸煮(MC-EPS),其中卡伯值为15, 该卡伯值源自添加0. 05% (在绝干木材上)蒽醌的混合的南方松木的实验室蒸煮;图4是比较下述方法的筛选过的纸浆得率增加的图表具有多硫化物的传统硫酸 盐法(CK-PS)、具有多硫化物的改进的蒸煮(MC-PS)、和相对于传统硫酸盐法(CK)伴随本发 明增强的多硫化物工艺的改进的蒸煮(MC-EPS),其中卡伯值为30,该卡伯值源自不添加蒽 醌的另一南方松木配料的实验室蒸煮;图5示出在垂直单容器连续蒸煮器(continuous digester)中的本发明的示范性 实施方式,其中蒸煮区都是并流的(co-current);图6示出在连续蒸煮器中的本发明的另一实施方式,其中最后的蒸煮阶段以逆流 (counter-current)方式运行;图7a和7b示出在一连串间歇式蒸煮器中的本发明的示范性装置。
71和2)中实现相对均勻的有效碱浓度分布,该有效碱浓度分布可比得上从目前的改进的蒸 煮中获得的有效碱浓度分布。因此,本发明使人们能够实现全部的潜在益处,即来自PS制 浆的纸浆得率增加,以及来自如在改进蒸煮中获得的更平均有效碱浓度分布的更高制浆得 率和强度,因此克服了现有技术的改进蒸煮在使用商业上可得的多硫化物制浆工艺时的不 相容性。 本发明的另一实施方式是(a)将总所需用碱量以多硫化物蒸煮液(橙液)的形 式添加到蒸煮的第一阶段,该阶段通常为浸渍阶段,并且控制该阶段的条件,典型地为约 135°C (275 °F )或低于该温度,持续15-45分钟,以使基本上所有的多硫化物都与木素纤维 素材料反应,并且没有大的碳水化合物降解和多硫化物热解发生;以及(b)调节第一量和 第二量的溶液从某些工艺点移走并在其它工艺点被添加返回至蒸煮的数量,以及它们相关 的移走和添加工艺点,以使浸渍阶段后的整个蒸煮阶段中最大有效碱浓度保持等于或低于 18g/L 的 Na0H(0. 45M NaOH 或 14g/L 的 Na20)。 可选地,可以实践本发明,其中在浸渍阶段后的所有蒸煮阶段中,最大有效碱浓度 被控制为等于或低于24g/L的Na0H(0. 6M NaOH或18. 6g/L的Na20)的情况下实行。实践本发明的另一方式为,在浸渍阶段之后的所有蒸煮阶段中,将最大碱浓度控 制为等于或低于12g/L的Na0H(0. 3M NaOH或9. 3g/L的Na20)。实施例实例1 表1总结了来自在实验室蒸煮混合的美国南方硬木配料至卡伯值为15的制浆得 率。这些结果也在图2中描绘。CK-Ref表示传统硫酸盐法制浆的参考蒸煮,其包括(a)在配备外部循环和电热 器的实验室蒸煮容器中,在 100°c ( 212T)以低压蒸汽加热木片10分钟;(b)排出 全部游离蒸汽冷凝液;(c)添加所有蒸煮碱液(以基于活性碱(AA)具有 30%硫化度 (sulfidity)的白液的形式),该蒸煮碱液与蒸煮开始为20. 0% NaOH(15. 5%的Na20)的有 效碱/木材用量相当,并且通过向蒸煮添加适量的水,促使蒸煮液/木材比达到3. 5 ; (d) 15 分钟内将蒸煮从约60°C加热到120°C ;(e)将蒸煮在120°C保持30分钟,从而达到浸渍阶 段;(f)在30分钟内将蒸煮加热到约160°C (320 °F )的充分蒸煮温度,并使蒸煮在该温度 维持100分钟,从而达到目标卡伯值 15 ; (g)使蒸煮冷却到低于100°C ; (h)用自来水清 洗蒸煮的木片;(i)通过在稀释的水悬浮液中机械混合,将清洗的蒸煮木片加工成纤维(纸 浆);以及(j)使用具有0.25mm(0.01”)筛孔的实验室平筛来筛选纸浆,之后测定制浆得 率、不合格品、卡伯值和其它纸浆特性。MC-Ref表示利用改进的蒸煮过程完成的参考蒸煮,该蒸煮包括与上面关于 CK-Ref蒸煮概述的基本相同的步骤,除步骤(c)在蒸煮开始时仅添加总用碱量的65%,以 及除步骤(f)通过计量设备向蒸煮添加相当于总用碱量的20%的第二有效碱添加,之后 在30分钟内将蒸煮加热到157°C ( 315 T ),维持该温度45分钟,之后添加相当于总用 碱量的15%的第三有效碱添加,已经在该充分蒸煮温度下使蒸煮继续进行另外150分钟, 从而达到目标卡伯值 15。CK-PS和MC-PS分别代表使用上述CK-Ref和MC-Ref工序进行的多硫化物(PS) 蒸煮,其使用多硫化物溶液代替白液,多硫化物溶液通过白液的催化氧化生产,并且包含相
8当于0. 7%木材进料的总多硫化物量,其基于活性碱的硫化度为 14%。另外,相当于木材 0. 05%的蒽醌(AQ)进料在蒸煮开始与第一有效碱进料添加到这些PS蒸煮中。MC-EPS蒸煮使用本发明完成,并且以下列步骤执行(a)在配备外部循环和电热 器的实验室蒸煮容器中,用 100°C ( 212下)以低压蒸汽加热木片10分钟;(b)排出全 部游离蒸汽冷凝液;(c)在蒸煮开始时添加0. 05%的蒽醌和多硫化物溶液形式(包含相对 木材为0.7%多硫化物的当量,其基于活性碱的硫化度为14%)的总所需用碱量,其相当于 为20. 0% Na0H(15. 5%的Na20)的有效碱/木材进料,并且通过向蒸煮添加适量的水,使蒸 煮液/木材比达到3. 5 ; (d) 15分钟内将蒸煮从约60°C加热到120°C ; (e)将蒸煮在120°C 维持30分钟,从而达到浸渍阶段;(f)通过冷却设备,从蒸煮容器收集第一量的有效碱浓 度相对高的蒸煮液,其量按重量计约相当于全部木材进料的约1.2倍,以便用于接下来的 MC-EPS蒸煮;(g)通过计量设备,向蒸煮容器添加第二量的从先前MC-EPS蒸煮收集的有效 碱浓度相对低的蒸煮液;(h)在30分钟内将蒸煮加热到约157°C (315 °F )的充分蒸煮温 度,并将蒸煮在该温度维持45分钟;(i)通过冷却设备,从蒸煮容器收集第二量的蒸煮液, 其量按重量计相当于全部木材进料的约1. 2倍,并将该有效碱浓度相对低的第二量的蒸煮 液储存,以便用于接下来的MC-EPS蒸煮;(j)经计量设备,向蒸煮容器添加第一量的从前 面MC-EPS蒸煮收集的蒸煮液,并在该溶液交换期间维持充分蒸煮温度;(k)在该充分蒸煮 温度下继续蒸煮另外150分钟,从而达到目标卡伯值 15 ;(1)将蒸煮冷却到低于100°C ; (m)用自来水清洗蒸煮的木片;(n)通过在稀释的水悬浮液中机械混合,将清洗过的蒸煮木 片加工成纤维(纸浆);以及(n)使用具有0.25mm (0.01”)筛孔的实验室平筛来筛选纸浆, 之后测定制浆得率、不合格品、卡伯值和其它测试。表 1在卡伯值为15的情况下,美国南方混合硬木的纸浆得率。 所有多硫化物蒸煮和增强的多硫化物蒸煮添加0. 05%的AQ(蒽醌)。该结果显示,达到15卡伯值的美国南方混合硬木的改进的蒸煮(MC-Ref)导致木 材的纸浆得率相比传统的参考蒸煮(CK-Ref)增加约0.9%。在传统硫酸盐法制浆(CK-PS) 的开始添加多硫化物溶液形式的总所需用碱量——其中多硫化物溶液包含基于绝干木 材为0. 7%的多硫化物和0. 05%的蒽醌,相比传统参考蒸煮增加纸浆得率约2. 1%,相比 MC-Ref蒸煮增加纸浆得率约1. 2%个点。正如基于现有技术的教导所预期的,当全部多硫化物溶液的65%在开始添加,并且余量的多硫化物溶液添加至改进蒸煮(MC-PS)的随后蒸 煮阶段时,相比MC-Ref木材的总纸浆得率仅增加1. 4% (相比CK-Ref增加2. 1 % ),这明 显低于源自改进的蒸煮和多硫化物添加的得率增加的预期总和(0. 9% +2. 1%) =3.0%o 在应用本发明,即伴随改进蒸煮的增强多硫化物工艺(MC-EPS)时,发现木材的总纸浆得率 增加3. 3%,其接近改进的蒸煮相比传统硫酸盐法制浆所增加的0. 9%和源自多硫化物制 浆预期的2.1%的总和。实例2 在南方松木的实验室制浆中发现了相似的结果,该结果在表2中总结,并在图3中 描绘。每种类型蒸煮的蒸煮程序与实例1中所描述的那些相同。已经发现,达到约30卡伯值的改进的蒸煮(MC-Ref)的木材的制浆得率相比传统 硫酸盐法参考(CK-Ref)蒸煮提高 0. 5%。将0. 05%的蒽醌和0. 7%的多硫化物添加到传 统硫酸盐法制浆使木材的纸浆得率增加约1.7%。正如基于现有技术的教导所预期的,进行 多硫化物制浆和MC蒸煮,而不用本发明,即将总用碱量分为多次添加,并且在蒸煮的开始 仅添加总用碱量的约65 %,总纸浆得率相比CK-Ref仅增加 1.5%,并且相比MC-Ref仅增 加1. 0%,明显低于预期总和 2. 2% ( 0. 5%源自改进的蒸煮,以及1. 7%源自多硫化物 添加)。在使用增强的多硫化物工艺概念实施本发明时,MC-EPS蒸煮中总纸浆得率增加相 比CK-Ref为 2. 3%,并且相比MC-Ref蒸煮为 1. 8%0表 2在卡伯值为30的情况下,南方松木配料1的纸浆得率。
所有多硫化物蒸煮和增强的多硫化物蒸煮添加0. 05%的蒽醌。实例3 在使用不同的南方松木配料,但没有向任何蒸煮添加蒽醌的另一实验室制浆研究 中,结果也明确显示出本发明的显著优点。每种类型蒸煮的蒸煮程序与实例1中所描述的 那些相同。如表3和图4中所示,已经发现,在蒸煮(CK-PS)开始将总所需用碱量以多硫化 物溶液(含有相对木材为0.7%的多硫化物)的形式添加,使相对木材的纸浆得率增加约 1.0%。正如基于现有技术的教导所预期的,进行多硫化物制浆和改进的蒸煮,而不用本发
10明,即将总多硫化物溶液分为多次进料,并且在蒸煮的开始(MC-PS)仅添加总多硫化物溶 液的约65%,总纸浆得率相比CK-Ref 仅增加 0. 6%。在使用伴随改进蒸煮的增强多硫化 物制浆概念(MC-EPS)实施本发明时,MC-EPS蒸煮中总纸浆得率增加相比CK-Ref蒸煮为 1. 0%。表3在卡伯值为30的情况下,南方松木配料2的纸浆得率。 任何蒸煮中都没有添加蒽醌。以上三个实施例明确说明本发明在使用伴随改进的蒸煮过程的多硫化物制浆方 面超过现有技术的优点。实例4 图5图解了本发明在垂直单容器连续蒸煮器20中的示例性实施方式,该连续蒸煮 器20包括一个在顶部的浸渍阶段21,以及在浸渍阶段下面的三个并流蒸煮阶段22、23和 24。第一循环回路25在浸渍阶段末端离开蒸煮器,并且在靠近蒸煮器上端处重新进入浸渍 阶段。第二循环回路26在第一蒸煮阶段22末端离开蒸煮器,并且在靠近第一蒸煮阶段上 端处重新进入第一蒸煮阶段。第三循环回路27在第二蒸煮阶段23末端离开蒸煮器,并且 在靠近第二蒸煮阶段上端处重新进入第二蒸煮阶段。木片28通常在蒸汽加工以便预热和 排除空气后,与多硫化物溶液29形式的100%总所需用碱量加入到蒸煮器顶部,即蒸煮开 始处。在该所谓浸渍阶段中,木片和蒸煮液从顶部向下移动到第一组筛子30,通常在30-45 分钟内,在 110°C到 135°C温度范围内进行。在该浸渍阶段的末端,基本上所有的多硫 化物都已经与木质成分反应,这使木片中的碳水化合物对碱催化降解更稳定,并且给予更 高制浆得率。第一量31的有效碱浓度相对高的蒸煮液紧接靠近蒸煮器顶部的浸渍阶段之 后经第一组筛子30被移走,如图5所示。第二量32的有效碱浓度相对低的蒸煮液从最后 的(最低的)筛子组33移走,如图5所示。可选地,但未示出,第二量的蒸煮液可以从倒数 第二组(中间的)筛子34移走。移走的第一量的蒸煮液31在第三循环回路27被添加返 回至蒸煮器,如图5所示,或可选地,但未示出,在第二循环回路26被添加返回至蒸煮器。 移走的第二量32的蒸煮液在第一循环回路25被添加返回至蒸煮器,如图5所示,或可选地 (未示出),在第二循环回路被添加返回至蒸煮器。从某些工艺点移走并添加返回至其它工艺点的第一量和第二量的蒸煮液的量应 进行调节,从而在浸渍阶段后的所有蒸煮阶段中实现最优选的有效碱浓度分布。也要考虑 到溶液移走和添加的位置与蒸煮器的液压平衡有关,并要考虑使木片列易于移动以便改进 蒸煮器的操作稳定性。通过实践本发明,在连续蒸煮器中,伴随改进的蒸煮的多硫化物制浆中的有效碱浓度分布比传统硫酸盐法制浆更均勻,其保留了来自改进的蒸煮的所有主要益处。同时,由 于所有多硫化物在蒸煮开始时投入使用,实现了来自PS制浆的最大纸浆得率增加。实例5 图6图解了本发明在连续蒸煮器20’中的另一实施方式,该连续蒸煮器20’以逆 流模式运行最后的蒸煮阶段24’。该实施方式中第三个并且是最后的循环回路27’在第三 蒸煮阶段24’的末端离开蒸煮器,然后重新进入第三蒸煮阶段中的较早点。第一量31’的 有效碱浓度相对高的蒸煮液在浸渍阶段21的末端从第一组筛子30移走,并且添加到最后 循环回路27’。第二量32’的有效碱浓度相对低的蒸煮液从中间抽取口 35中移走(在倒数 第二组筛子34处从蒸煮器移走),并添加到第一循环回路25,该循环回路25的入口设置在 第一量的溶液移走点的下游。如前所讨论,从某些工艺点移走并添加返回至其它工艺点的第一量和第二量的蒸 煮液的量应进行调节,从而在浸渍阶段后的所有蒸煮阶段中实现最优选的有效碱浓度分 布。也要考虑到溶液移走和添加的位置与蒸煮器的液压平衡有关,并要考虑使木片列易于 移动以便改进蒸煮器的操作稳定性。实例6
图7a和7b图解了本发明在一连串能够运行改进的间歇蒸煮的间歇蒸煮器410、 420、430和440中的应用。对于每个蒸煮器,100%所需的碱剂量以多硫化物(橙色)溶液 的形式在蒸煮开始添加,或与木片一起添加,或在所有所需木片添加后添加。每个间歇蒸煮 器,例如蒸煮器#1,配备有由一组洗浆池(drainer)(提取筛)412、循环泵413和加热器414 组成的蒸煮循环回路411。第一量的高有效碱的蒸煮液44从正好位于浸渍阶段末端的蒸煮 容器#1移走,并添加到另一蒸煮器(容器#4),其完成浸渍阶段并经历相当的蒸煮,例如在 蒸煮温度下蒸煮至少30分钟并且在第二量的低有效碱的蒸煮液从该容器移走后。在蒸煮 的第一量移走后,从蒸煮器#3移走的第二量的低有效碱浓度的蒸煮液46添加到蒸煮容器 #2。可选地,在泵入不同蒸煮阶段的另一蒸煮器之前,移走的第一量和第二量的溶液 可以储存在单独的溶液槽中,从而实现优选的碱浓度分布。可以看出,根据本发明,有效碱浓度相对高的蒸煮液与有效碱浓度相对低的蒸煮 液进行“交换”,其中浓度相对较高的蒸煮液和浓度相对较低的蒸煮液分别在不同工艺点或 不同时间从蒸煮过程提取,并且分别在其它的点或时间重新加入或再循环到蒸煮过程中。虽然本发明的
在本文中详细说明和描述,但应该理解,可以在不背 离所附权利要求定义的本发明的精神和意图的情况下,对本发明做出多种变化和修改。
本发明涉及一种硫酸盐法制浆方法,该方法采用与多硫化物制浆技术结合的改进的蒸煮方法,从而使获得比现有技术下所获得的制浆得率更高的制浆得率。总的所需用碱量(多硫化物溶液)在蒸煮的开始添加,并且在基本上所有多硫化物都与木素纤维素材料在低于没有明显的碳水化合物降解发生的温度下反应后,有效碱(EA)浓度高的第一量的蒸煮液从制浆工艺中的第一点移走,并用从另一工艺点移走的有效碱浓度低的蒸煮液代替。然后该第一量被添加到制浆工艺中有效碱浓度低的其它地方。该蒸煮液“交换”获得了源自多硫化物制浆的全部得率益处和更均匀的有效碱浓度分布,从而保留了改进的蒸煮的主要益处。
多硫化物在改进的蒸煮中的用途制作方法
- 专利详情
- 全文pdf
- 权力要求
- 说明书
- 法律状态
查看更多专利详情
下载专利文献
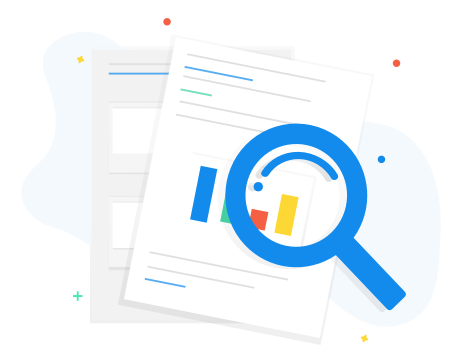
下载专利
同类推荐
-
江健儿乔瓦尼·曼布里尼, 索尼娅·塞拉菲尼乔瓦尼·曼布里尼, 索尼娅·塞拉菲尼乔瓦尼·曼布里尼, 索尼娅·塞拉菲尼梁锁页, 赵松源梁锁页, 赵松源任明
您可能感兴趣的专利
-
罗殷, 蔡愈杭罗殷, 蔡愈杭罗殷, 蔡愈杭陈松涛
专利相关信息
-
陈松涛R·卡瓦R·卡瓦R·卡瓦R·卡瓦希尔雅斯·布安达里希尔雅斯·布安达里