专利名称:一种精密喷射成型用电加热陶瓷模具的制备方法目前,一般的喷射成型对沉积坯底面的形貌和尺寸精度要求不高。沉积基板用铸 铁盘且不预热时,因沉积坯底面的初始沉积层温度太低且冷却速度太快,沉积坯边缘会翘 曲。而精密喷射成型要求沉积坯底面有尺寸精度较高的形貌,沉积坯边缘不能翘曲,并要求 沉积坯底面的疏松度低、致密度高。这就要求沉积基板采用热导率低的陶瓷模具,陶瓷模具 还要预热到合适的温度,通常要求达500°C以上。虽然也可以在气雾化罐的外面预加热陶瓷 模具后,再将其放入雾化罐内,抽真空后开始喷射成型。但这种方法难以较准确地控制陶瓷 模具所需的预热温度,使沉积坯底面的质量难以达到精密喷射成型的要求。
为了克服现有喷射成型用金属底模,或陶瓷底模在气雾化罐外预加热再放入罐 内,底模温度不宜控制的缺点,本发明解决了在气雾化罐内预热陶瓷模具的相关设计和制 造问题。本发明解决其技术问题所采用的技术方案是设计和制作一个有凹凸表面的原型一在原型上翻制硅橡胶模板一在硅橡胶模板 上翻制蜡模板一在蜡模板上翻制表面有凹凸形貌的陶瓷模板一陶瓷模板和电热丝炉组装 成可电加热的陶瓷模具。1. 一种精密喷射成型用电加热陶瓷模具的制备方法,所述方法步骤如下1. 1设计和制作一个直径200mm-400mm有凹凸表面的原型模板;1. 2在凹凸表面的原型模板上翻制硅橡胶模板;1. 3在硅橡胶模具上翻制蜡模板;1. 4在蜡模板上翻制表面有凹凸形貌的厚度8mm-35mm的陶瓷模板;1. 5陶瓷模板和电热丝炉等组装成可电加热的陶瓷模具。2.所述步骤1. 4中,所述陶瓷模板是锆英石陶瓷模板,或氧化铝陶瓷模板。3.所述锆英石陶瓷模板的制作包括陶瓷模板面层及陶瓷模板背层的制备;先制作陶瓷模板面层,方法如下3. 1陶瓷料浆制备(1)加入所需的硅溶胶;(2)开动机械搅拌器进行搅拌,转速60转/分钟以上;(3)按每升硅溶胶加入3. 5-4. 0克的表面活性剂的量,表面活性剂为十二烷基苯 磺酸钠;4(4)按粉液比4 1缓慢加入所需锆英石粉,避免锆英石粉粉料结块;(5)按每升硅溶胶加入1. 2-1. 3克的消泡剂,消泡剂为正辛醇;(6)混合均勻后,用流杯粘度杯测定涂料粘度,根据粘度加入锆英石粉料或硅溶胶 调整料浆;(7)搅拌8-24小时方可使用。3. 2压缩空气喷吹首先将蜡模用无水乙醇清洗干净,在压缩空气压力下,用喷枪喷吹料浆到蜡模表 面;每层厚度约1mm,每层喷涂完料浆后,进行撒砂,撒砂用耐火材料为200目锆英石粉;面 层型壳层数2 3层。3. 3锆英石模板面层干燥锆英石模板面层干燥工艺环境温度22 25°C,环境湿度50% 70%,最好在 60%以上,干燥时间6小时以上。再在锆英石模板面层上制作背层,方法如下3. 4料浆制备(1)加入所需的硅溶胶;(2)开动机械搅拌器进行搅拌,转速60转/分钟以上;(3)按粉液比4 1缓慢加入所需锆英石粉,防止粉料结块;(4)基本混合均勻后,用流杯粘度杯测定涂料粘度,根据粘度加入粉料或硅溶胶调 整料浆;(5)搅拌6小时以上方可使用。3. 5料浆涂挂采用直接涂覆和喷枪喷吹两种方法进行,每层厚度1 2mm ;每层喷涂完料浆后, 均勻撒砂;背层型壳的层数在4 10层;3. 6 干燥锆英石背层型壳干燥工艺参数为环境温度20 25°C,环境湿度40% 70%,干 燥时间6小时以上,充分干燥后再进行下一层操作。4.所述氧化铝型壳陶瓷模板制作包括面层及背层的制备,先制作面层,方法如 下4. 1料浆制备(1)加入所需的硅溶胶;(2)开动机械搅拌器进行搅拌,转速50转/分钟;(3)按每升硅溶胶加入3. 5-4. 0克的表面活性剂,表面活性剂为十二烷基苯磺酸 钠;(4)按粉液比4 1缓慢加入所需α -Al2O3粉,避免α -Al2O3粉粉料结块;(5)按每升硅溶胶应加入消泡剂的量1. 2-1. 3克,加入正辛醇;(6)基本混合均勻后,用流杯粘度杯测定涂料粘度,根据粘度加入α -Al2O3粉粉料 或硅溶胶调整料浆;(7)背层涂料搅拌时间少于面层涂料的搅拌时间,全部涂料新配时,搅拌时间应大 于10小时;部分涂料新配时,搅拌时间可缩短至5小时左右即可使用。背层料浆的粉液比可比面层锆英石料浆的粉液比略低,而且随着层数的增加,粉 液比可逐渐减小,但不低于3. 8g/ml。4. 2跟权利要求3中的步骤3. 2 —样。4. 3陶瓷模板干燥氧化铝模板面层干燥工艺参数为温度22 25 °C,湿度50% 80%,最好在60% 以上,干燥时间6小时以上,充分干燥后才能进行下一层操作;4. 4再在陶瓷模板面层上制作背层背层料浆涂挂工艺与面层相同,可采用直接涂覆和喷枪喷吹两种方法进行,每层 厚度1 2mm。每层喷涂完料浆后,均勻撒砂。背层的层数根据陶瓷模板尺寸的大小进行确 定,一般在4 10层左右。锆英石模板背层干燥工艺参数为环境温度最好在20 25°C,环境湿度一般为 40% 70%,干燥时间6小时以上。充分干燥后才能进行下一层操作。本发明在雾化罐内,从底部加热陶瓷模具,可更准确地控制陶瓷模具的温度,进而 提高精密喷射成型沉积坯的致密度。若用陶瓷浆料一次性浇注几厘米厚的陶瓷模板,干燥时易出现裂纹。本发明采用 精密铸造制作陶瓷型壳面层和背层的工艺。一般情况下,面层和背层浆料所用的耐火粉料 不同。因为面层会与金属液接触,不可与金属液发生反应,应使用纯度高的耐火粉料。制作 陶瓷模板采用多次喷涂或涂刷陶瓷浆料的方法,每层厚度不到1mm,干燥后再涂下一层,这 样做可以避免陶瓷模板的开裂。本发明优点是解决了在气雾化罐内预热陶瓷模具的相关设计和制造问题,可更准 确地控制陶瓷模具的温度,进而提高精密喷射成型沉积坯的致密度。锆英石面层料浆配制的加料顺序为硅溶胶一表面活性剂一锆英石粉一消泡剂。 其涂料配制流程如下。1)加入所需的硅溶胶;2)开动机械搅拌器进行搅拌,转速60转/分钟;3)按每升硅溶胶应加入表面活性剂的量3. 7克,加入十二烷基苯磺酸钠;4)按粉液比4 1缓慢加入所需锆英石粉,避免粉料结块;5)按每升硅溶胶应加入消泡剂的量1. 25克,加入正辛醇;6)基本混合均勻后,用流杯粘度杯测定涂料粘度,根据粘度加入粉料或硅溶胶调 整料浆;7)搅拌12小时以上再使用。由于锆英石比重较大,很容易在搅拌过程中沉淀。为了尽量避免锆英石沉淀,可以 提高搅拌速度的方法加以改善。当面层涂料全部为新料时,搅拌时间应大于24小时才能使 用,部分为新配的料,搅拌时间可缩短为12小时。涂料搅拌过程中,应根据蒸发情况适当补 充一定量的去离子水进去,以保证涂料粘度基本不变。(2)压缩空气喷吹法由于直接涂覆法不宜涂挂均勻,所以实验中还采用压缩空气进行喷吹涂挂料浆。 首先将蜡模用无水乙醇清洗干净,在压缩空气压力下,用喷枪喷吹料浆到蜡模板表面。喷涂 法比直接涂敷法能使料浆更好地涂挂到蜡模板表面,涂层均勻,且无气泡。每层厚度约1mm, 每层喷涂完料浆后,进行撒砂,撒砂用耐火材料为200目锆英石粉。(3)锆英石面层干燥工艺参数 锆英石面层干燥工艺参数为环境温度最好在22 25 °C,环境湿度一般为50 % 70%,最好在60%以上,干燥时间6小时以上。一定要充分干燥后才能进行下一层操作。采用喷吹法所制得锆英石面层的体积密度为3. 24g/cm3,致密度为75. 9%,弯曲强 度为30. 74MPa。制得直径达400mm以上,表面有精细结构的锆英石陶瓷模板。在锆英石模板面层上制备背层背层制备与锆英石模板面层的工艺大致相同,只是不再添加表面活性剂和消泡 剂。用200目锆英石粉作为背层耐火材料和撒砂材料,硅溶胶作粘结剂。(1)背层料浆制备背层料浆配制基本流程为1)加入所需的硅溶胶;2)开动机械搅拌器进行搅拌,转速60转/分钟或更高;3)按粉液比4 1缓慢加入所需锆英石粉,防止粉料结块;4)基本混合均勻后,用流杯粘度杯测定涂料粘度,根据粘度添加锆英石粉或硅溶 胶调整料浆;5)搅拌大于10小时方可使用。背层涂料搅拌时间少于面层涂料的搅拌时间,全部涂料新配时,搅拌时间应大于 10小时;部分涂料新配时,搅拌时间可缩短至5小时左右即可使用。背层料浆的粉液比为 4 1 3.8 1,而且随着层数的增加,粉液比逐渐减小。(2)料浆涂挂及干燥
背层料浆涂挂工艺与锆英石模板面层相同,可采用直接涂覆和喷枪喷吹两种方法 进行,每层厚度1 2mm。每层喷涂完料浆后,均勻撒砂。背层的层数根据模板尺寸的大小 进行确定,一般在4 10层左右。锆英石背层干燥工艺参数为环境温度最好在20 25°C,环境湿度一般为40 % 70%,干燥时间6小时以上。充分干燥后才能进行下一层操作。粉液比对料浆以及陶瓷模板的性能起着关键的作用。锆英石料浆的最佳粉液比是 4. 0g/mlo陶瓷模板在无风条件下干燥时主要影响因素是环境温度及环境湿度。无风条件下 干燥陶瓷模板,最合适的干燥条件是环境温度22士2°C,环境湿度50% 70%。随着烧结温度的提高,陶瓷模板的收缩率提高,致密度增大,抗弯强度及抗压强度 均增大。锆英石陶瓷模板经1350°C烧结后,收缩率为1.7%,致密度达75.9%,抗弯强度 30. 74MPa,抗压强度 73MPa。组装电加热锆英石陶瓷模板的精密喷射成型底模把IOmm厚的锆英石陶瓷模板放在3kW电炉上,之间的空隙用耐火材料颗粒填充, 加热30分钟后陶瓷模板表面温度可达600°C以上。实施例2直接涂覆法制备电加热锆英石陶瓷模板基本步骤如实例1。锆英石面层采用首先直接涂敷的方式进行。先将蜡模板用无 水乙醇清洗干净,晾干后就可将涂料施挂到水平放置的蜡模板上表面,料浆在自身的流动 性下铺展覆盖蜡模板表面,用毛刷修补没有覆盖的地方。每层厚度1 2mm左右,第一层可 略薄。每层涂挂完料浆后,需进行撒砂,锆英石面层可以直接用为200目锆英石粉撒砂,撒 砂要均勻。面层层数2 3层。采用直接涂覆法经1350°C烧结所制得的陶瓷模板体积密度为3. 22g/cm3,致密度 为75.6%,弯曲强度为26. 28MPa;制得直径达400mm以上,表面有精细结构的锆英石陶瓷模 板。实施例3制备氧化铝陶瓷模板氧化铝陶瓷模板面层所用耐火粉料为α -Al2O3电熔刚玉,以硅溶胶作粘结剂,添 加表面活性剂和消泡剂。撒砂用耐火粉料是200目的α-Al2O3粉。氧化铝面层料浆配制的加料顺序为硅溶胶一表面活性剂一α -Al2O3粉一消泡 剂。详细配制流程如下。1)加入所需的硅溶胶;2)开动机械搅拌器进行搅拌,转速50转/分钟;3)按每千克硅溶胶应加入表面活性剂的量,加入十二烷基苯磺酸钠;4)按粉液比缓慢加入所需α -Al2O3粉,避免粉料结块;5)按每千克硅溶胶应加入的消泡剂的量,加入正辛醇;6)基本混合均勻后,用流杯粘度杯测定涂料粘度,根据粘度调整料浆;7)搅拌至工艺规定时间方可使用。氧化铝陶瓷模板面层干燥工艺参数为温度22 25°C,湿度一般为50% 80%,最好在60%以上,干燥时间6小时以上,充分干燥后才能进行下一层操作。其它步骤如实例1。实施例4制备厚锆英石陶瓷模板基本步骤如实例1。在35毫米厚的锆英石陶瓷模板的底部用3kW电炉加热,50分 钟后表面温度可达500°C以上。
本发明属于材料喷射成型领域,涉及一种精密喷射成型用电加热陶瓷模具的制备方法,其特征是设计和制作一个有凹凸表面的原型→在原型上翻制硅橡胶模板→在硅橡胶模板上翻制蜡模板→在蜡模板上翻制表面有凹凸形貌的陶瓷模板→陶瓷模板和电热丝炉组装成可电加热的陶瓷模具。在喷射成型的气雾化罐内从底部对陶瓷模板进行预热,以提高精密喷射成型沉积坯的致密度和表面质量。本发明优点是解决了在气雾化罐内预热陶瓷模具的相关设计和制造问题,可更准确地控制陶瓷模具的温度,进而提高精密喷射成型沉积坯的致密度。
一种精密喷射成型用电加热陶瓷模具的制备方法
- 专利详情
- 全文pdf
- 权力要求
- 说明书
- 法律状态
查看更多专利详情
下载专利文献
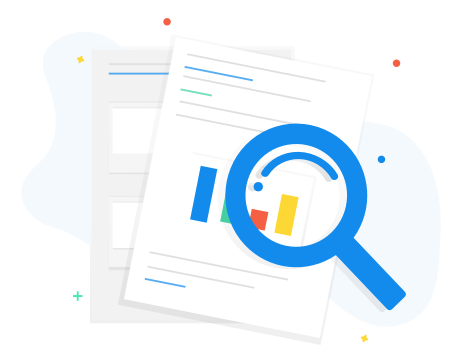
下载专利
同类推荐
-
刘璐瑶名取荣治彭威汤玉斐秦升益
您可能感兴趣的专利
-
秦升益秦升益秦升益罗兰·尼德刘强刘强
专利相关信息
-
刘强安焕涛安焕涛陈秀丽王小锋