道路硅酸盐水泥及其生产方法【技术领域】[0001]本发明属于建筑材料【技术领域】,具体涉及一种道路硅酸盐水泥及其生产方法。[0002]道路硅酸盐水泥(即道路水泥)是由道路硅酸盐熟料,加适量的石膏和符合标准要求的混合材料,磨制而成的水硬性胶凝材料,其具有抗折强度高、耐磨性好、干缩性小、水化热低、抗硫酸盐侵蚀性强、抗冻性好等优点,用其配制混凝土具有良好的施工性能和优良的耐久性,技术性能优于普通水泥混凝土,能长期经受高速车辆的摩擦、循环不已的负荷、载重车辆的振荡冲击、温度变化产生的胀缩应力和冻融,主要应用于高等级公路、飞机跑道、交通道路、城市大面积路面建设以及军事等重点关键性工程。[0003]根据道路水泥生产标准要求,道路硅酸盐水泥中含SO3不得大于3.5%,烧失量不得大于3.0%, 28天磨耗量应小于3kg/m2,28天干缩率应小于0.1%,其熟料中含铝硅酸钙应不大于5.0%,含铁铝酸四钙应大于16%,等等。为达到道路水泥的技术标准要求,人们可以通过严格选料,采用科学配方,以及生产工艺改进等对道路水泥的各项指标进行控制,生产出符合国家或国际标准的道路水泥。随着道路建设的增多,对道路水泥研究的不断深入,已有较多相关道路硅酸盐水泥及其生产方法的文献报道,例如:[0004]1.中国专利,低碱抗硫型道路硅酸盐水泥及其生产方法,申请号:201210221127.7,申请日2012.06.29,【公开日】2012.09.12, 申请人::新疆天山水泥股份有限公司,法律状态:实质审查的生效。摘要:低碱抗硫型道路硅酸盐水泥及其生产方法,以低碱含量的优质石灰石、砂岩、钢铁粉为原料,按低碱钢铁粉4% -8%、低碱石灰石80% -82%、低碱砂岩12% -14%配料,生产出熟料;然后将熟料与低碱天然石膏按一定比例粉磨制成抗硫型低碱硅酸盐道路水泥。利用低碱含量的优质石灰石、砂岩、钢铁粉原料按低碱钢铁粉4% -8%、低碱石灰石80% -82%、低碱砂岩12% -14%的比例配料生产低碱、抗硫型道路硅酸盐水泥熟料。然后将低碱、抗硫型道路硅酸盐水泥熟料与低碱天然石膏按一定比例粉磨制成低碱、抗硫型道路硅酸盐水泥。干缩率小,耐磨性好,能够降低生产成本,显著提高道路硅酸盐水泥的性能。抗硫酸盐性能强。[0006]3.中国专利,钢渣道路水泥及其制备方法,申请号:201210017058.8,申请日2012.01.19,【公开日】2012.07.04, 申请人::攀枝花钢城集团有限公司,法律状态:实质审查的生效。摘要:本发明公开了一种用含钒钢渣制备的钢渣道路水泥和该水泥的制备方法,属于道路材料【技术领域】。钢渣道路水泥,原料包括20~50重量份的含钒钢渣、45~70重量份的水泥熟料和3~10重量份的石膏,其中所述含钒钢渣中游离氧化钙含量按重量百分比计<3% ;将上述原料混合即制得钢渣道路水泥。本发明通过控制含钒钢渣游离氧化钙的含量< 3%,从而消除含钒钢渣中游离氧化钙对水泥安定性造成的影响,通过控制含钒钢渣的比表面积≥400m2/kg,使其能够达到一定的细度、容易水化,解决C2S、C3S的含量低造成的水化性能低的问题,使得用含钒钢渣能够生产出合格的钢渣道路水泥。
[0007]以上文献均公开采用道路硅酸盐水泥熟料、石膏,以及粒化电炉磷渣、钢渣等混合材料制备水泥,所述熟料包括钙质原料、硅质原料及铁质原料等,所生产出的水泥达到国家技术标准要求。然而,现有道路硅酸盐水泥多单独采用“干法”或者“湿法”生产工艺,两种生产工艺各有优缺点:“干法”工艺产量高、生产率高,但生料组分均化效果差,容易影响产品品质;“湿法”工艺生产的水泥生料组分均化效果好、质量高,同时能耗也高。因此,面对道路建设需求的增多,道路建设质量要求的增高,急需一种产量高、耗能少、产品质量优的道路过酸盐水泥生产工艺。
[0008]针对现有技术的不足,本发明提供了一种道路硅酸盐水泥及其生产方法,其采用科学熟料配方,严格选用原料,运用“湿磨干烧”、“分别粉磨”的生产工艺,生产出具有强度高、磨耗量低及干缩性性等特性的道路硅酸盐水泥,填补了采用上述工艺技术生产出优于国家标准的水泥的技术空白。
[0009]本发明采用的技术方案是:
[0010]一种道路硅酸盐水泥,含原料道路硅酸盐熟料、脱硫石膏和粒化高炉矿渣粉;以重量份数计,是先按道路硅酸盐熟料:脱硫石膏=93-97: 3-7共同粉磨生产出水泥微粉,再按水泥微粉:粒化高炉矿渣粉=90-100: 0-10混合制备而得;其中,所述的道路硅酸盐熟料由以下重量百分比的原料组成生料:石灰石78-82%、高硅砂岩11-15%、硫酸渣5-8%,经生料粉磨、料浆脱水、滤饼烘干破碎、熟料烧成工序制备而得。
[0011]以上所述道路硅酸盐水泥,SiO3的重量百分比为2.0-3.5%,比表面积为300-450m2/kg,烧失量为 0.3-1.5%。
[0012]熟料质量的好坏直接影响着水泥产品的质量和可靠程度,本发明严格控制熟料各化学成分的比例及各矿物组成的含量,根据本公司生产工艺特性及道路硅酸盐水泥熟料的要求确定熟料率值为:LSF=96±1.5,SM=L 95 ±0.1,AM=0.80±0.1,f-CaO ( 1.0%,立升重^ 1200g/L。其中,LSF表示熟料中氧化硅被氧化钙饱和形成硅酸三钙的程度,SM表示熟料中SiO2的百分含量与Fe2O3及Al2O3百分含量之比,頂表示熟料中Al2O3的百分含量与Fe2O3百分含量之比。
[0013]本发明在配料方案的设计上,严格选用原料。以上所述石灰石中CaO的重量百分比≥53%,MgO的重量百分比≤1.2%,粒度≤25mm ;所述高硅砂岩中SiO2的重量百分比≥80% ;所述硫酸渣中Fe2O3的重量百分比≥40%。
[0014]作为本发明的进一步说明,所述粒化高炉矿渣粉中含氯离子的重量百分比(0.06%,比表面积≤350m2/kg, 28天活性指数≤75%。
[0015]作为本发明的进一步说明,所述脱硫石膏中SO3的重量百分比≤35%,结晶水的重量百分比> 5%。
[0016]一种如上所述道路硅酸盐水泥的生产方法,包括以下生产步骤:
[0017]1.生料制备:生料按以下重量百分比原料称取:石灰石78-82%、高硅砂岩11_15%、硫酸渣5-8%,加入水,进行粉磨,搅拌均匀,制成水分为33-37%的料浆;
[0018]2.料浆脱水:将料浆经真空吸滤机脱水后形成水分为17-20%的滤饼;
[0019]3.滤饼烘干破碎:将滤饼喂到烘干破碎机内,利用窑尾来的热废气将其烘干成水分为1-3%的生料粉;
[0020]4.熟料烧成:将生料粉预热分解后喂入回转窑,用窑头燃烧器将其煅烧成道路硅酸盐熟料;
[0021]5.水泥微粉制备:将道路硅酸盐熟料、脱硫石膏按93-97: 3_7的重量比配制,粉磨,得到水泥微粉;
[0022]6.水泥混合制备:将水泥微粉、粒化高炉矿渣粉按90-100: 0_10的重量比配制,
混合均匀,即得。
[0023]作为本发明的进 一步说明,所述粒化高炉矿渣粉是将粒化高炉矿渣通过立磨粉磨制备而得的,所得粒化高炉矿渣粉比表面积高(比表面积> 350m2/kg),与水泥微粉按比例在均化机系统均化后得到本发明水泥,所得水泥的颗粒级混配更加合理,水泥质量稳定性好。
[0024]本发明的有益效果是:
[0025]1.本发明采用科学熟料配方,严格选用原料,运用“湿磨干烧”的熟料制备工艺,在生料粉磨方面较“干法”工艺能够更加快速的调节生料,避免生料波动,生料各组分均化效果好,进一步对窑烧阶段起到稳定熟料质量的作用,保证了熟料的质量稳定性,间接保证了产品的质量稳定性;同时,增加“分级粉磨”生产工艺,粒化高炉矿渣通过立磨粉磨得到比表面积较高(比表面积> 350m2/kg)的粒化高炉矿渣粉,进一步与水泥微粉混合制备水泥,水泥的颗粒级混配更加合理,水泥质量稳定性好,并增加了日产量(日产量可提高30%以上)。
[0026]2.本发明分别利用湿磨均化效果好和干法窑节能、高产,以及分级粉磨保质保量的优点,制备出的水泥3d抗折强度为5.6MPa,28d抗折强度为8.8MPa,3d抗压强度为27.2MPa,28d抗压强度为54.8MPa,28d干缩性为0.073%, 28d耐磨性为2.42kg/m2,等等,所有指标均优于国家标准,适用于各种道路建设。
[0027]3.本发明采用工业废渣硫酸渣为铁质校正原料,既解决固体废弃物对环境的污染,同时提高了道路硅酸盐水泥的性能。
[0028]图1是本发明道路硅酸盐水泥的生产工艺流程图。
[0029]以下结合实施例对本发明作进一步详细说明,本实施例仅是对本发明作更清楚的说明,而不是对本发明的限制。[0030]一、原料选取及预处理要求
[0031]1.石灰石:CaO ≥ 53%, MgO ( 1.2%,粒度≤ 25mm。
[0032]2.高硅砂岩:Si02 ≥ 80%ο
[0033]3.硫酸渣=Fe2O3 ≥ 40%。
[0034]4.脱硫石膏:S03≥ 35%,结晶水≥ 5%。
[0035]5.粒化高炉矿渣粉:粒化高炉矿渣通过立磨单独粉磨制备而得,氯离子< 0.06%,比表面积≥ 350m2/kg, 28天活性指数≥ 75%,备用。
[0036]6.煤:选用煤质较好,发热量较高,灰分较低的燃煤,碱含量要求< 0.6%。
[0037]二、道路硅酸盐水泥的生产方法
[0038]实施例1
[0039]1.生料制备:生料按以下重量百分比原料称取:石灰石80%,高硅砂岩12%、硫酸渣8%,采用湿法粉磨工艺,入磨原料配合一定比例的水分经过球磨机粉磨成合格料浆,将料浆泵入料浆泵系统8个料浆库,料浆经精确配料,放入料浆搅拌大池,经均匀配料泵进入料浆过滤系统,搅拌均匀,制成35%料浆。
[0040]2.料浆脱水:将上述浆料用真空吸滤机脱水,形成含水为18%的滤饼,滤饼落到带有BMP的输送皮带。
[0041]3.滤饼烘干破碎:通过箱式喂料机,滤饼被喂到烘干破碎机内,从窑尾来的废气(600°C)将其烘干成含水2%的生料粉,经烘干废气带入旋风分离器内进行料气分离,分离出来的生料粉进入烧成系统的旋风预热器、分解炉中,出旋风分离器的废气(约150°C)用窑尾风机送入电除尘器进行净化后,经烟?排入大气。
[0042]4.熟料烧成:将生料粉预热分解后喂入窑进料端,借助窑的斜度和旋转、慢慢地向窑头运动,在烧成带用窑头煤粉所提供的燃烧器将其烧结成水泥熟料。烧结后的高温熟料出窑落入篦式冷却机,通过推杆的往复运动,进入冷却机尾部的锤式破碎机,经打碎后卸落到链斗输送机上,再由链斗输送机输送至联合库的熟料堆场。通过熟料层后的气体作为二次风直接入窑,也作为三次风抽往窑尾分解炉燃烧用风及供煤磨烘干原煤用热风,多余的废气(约220~280°C)将通过窑头电收尘器净化后,由离心锅炉引风机排入大气,熟料电收尘器收集的粉尘由链式输送机送至链斗输送机。熟料的率值范围详见表1。
[0043]5.水泥微粉制备:熟料进入联合储存库后,经水泥磨磨头电子皮带秤配料,按照道路硅酸盐熟料:脱硫石膏球重量比=95: 5入磨进行粉磨,出磨水泥微粉合格即经水泥输送系统运入均化机水泥仓储存。
[0044]6.水泥混合制备:将水泥微粉、粒化高炉矿渣粉按95: 5的重量比配制,混合均匀,所得水泥经过水泥输送系统运入水泥库。成品的主要性能参数详见表2。
[0045]实施例2
[0046]1.生料制备:生料按以下重量百分比原料称取:石灰石78%,高硅砂岩15%、硫酸渣7%,采用湿法粉磨工艺,入磨原料配合一定比例的水分经过球磨机粉磨成合格料浆,将料浆泵入料浆泵系统8个料浆库,料浆经精确配料,放入料浆搅拌大池,经均匀配料泵进入料浆过滤系统,搅拌均匀,制成33%料浆。
[0047]2.料浆脱水:将上述浆料用真空吸滤机脱水,形成含水为17%的滤饼,滤饼落到带有BMP的输送皮带。[0048]3.滤饼烘干破碎:通过箱式喂料机,滤饼被喂到烘干破碎机内,从窑尾来的废气(600°C)将其烘干成含水1%的生料粉,经烘干废气带入旋风分离器内进行料气分离,分离出来的生料粉进入烧成系统的旋风预热器、分解炉中,出旋风分离器的废气(约150°C)用窑尾风机送入电除尘器进行净化后,经烟?排入大气。
[0049]4.熟料烧成:将生料粉预热分解后喂入窑进料端,借助窑的斜度和旋转、慢慢地向窑头运动,在烧成带用窑头煤粉所提供的燃烧器将其烧结成水泥熟料。烧结后的高温熟料出窑落入篦式冷却机,通过推杆的往复运动,进入冷却机尾部的锤式破碎机,经打碎后卸落到链斗输送机上,再由链斗输送机输送至联合库的熟料堆场。通过熟料层后的气体作为二次风直接入窑,也作为三次风抽往窑尾分解炉燃烧用风及供煤磨烘干原煤用热风,多余的废气(约220~280°C)将通过窑头电收尘器净化后,由离心锅炉引风机排入大气,熟料电收尘器收集的粉尘由链式输送机送至链斗输送机。熟料的率值范围详见表1。
[0050]5.水泥微粉制备:熟料进入联合储存库后,经水泥磨磨头电子皮带秤配料,按照道路硅酸盐熟料:脱硫石膏球重量比=93: 7入磨进行粉磨,出磨水泥微粉合格即经水泥输送系统运入均化机水泥仓储存。
[0051]6.水泥混合制备:将水泥微粉、粒化高炉矿渣粉按92: 8的重量比配制,混合均匀,所得水泥经过水泥输送系统运入水泥库。成品的主要性能参数详见表2。
[0052]实施例3
[0053]1.生料制备:生料按以下重量百分比原料称取:石灰石80%,高硅砂岩15%、硫酸渣5%,采用湿法粉磨工艺,入磨原料配合一定比例的水分经过球磨机粉磨成合格料浆,将料浆泵入料浆泵系统8个料浆库,料浆经精确配料,放入料浆搅拌 大池,经均匀配料泵进入料浆过滤系统,搅拌均匀,制成37%料浆。
[0054]2.料浆脱水:将上述浆料用真空吸滤机脱水,形成含水为20%的滤饼,滤饼落到带有BMP的输送皮带。
[0055]3.滤饼烘干破碎:通过箱式喂料机,滤饼被喂到烘干破碎机内,从窑尾来的废气(600°C)将其烘干成含水2%的生料粉,经烘干废气带入旋风分离器内进行料气分离,分离出来的生料粉进入烧成系统的旋风预热器、分解炉中,出旋风分离器的废气(约150°C)用窑尾风机送入电除尘器进行净化后,经烟?排入大气。
[0056]4.熟料烧成:将生料粉预热分解后喂入窑进料端,借助窑的斜度和旋转、慢慢地向窑头运动,在烧成带用窑头煤粉所提供的燃烧器将其烧结成水泥熟料。烧结后的高温熟料出窑落入篦式冷却机,通过推杆的往复运动,进入冷却机尾部的锤式破碎机,经打碎后卸落到链斗输送机上,再由链斗输送机输送至联合库的熟料堆场。通过熟料层后的气体作为二次风直接入窑,也作为三次风抽往窑尾分解炉燃烧用风及供煤磨烘干原煤用热风,多余的废气(约220~280°C)将通过窑头电收尘器净化后,由离心锅炉引风机排入大气,熟料电收尘器收集的粉尘由链式输送机送至链斗输送机。熟料的率值范围详见表1。
[0057]5.水泥微粉制备:熟料进入联合储存库后,经水泥磨磨头电子皮带秤配料,按照道路硅酸盐熟料:脱硫石膏球重量比=97: 3入磨进行粉磨,出磨水泥微粉合格即经水泥输送系统运入均化机水泥仓储存。
[0058]6.水泥混合制备:将水泥微粉、粒化高炉矿渣粉按95: 5的重量比配制,混合均匀,所得水泥经过水泥输送系统运入水泥库。成品的主要性能参数详见表2。[0059]实施例4
[0060]1.生料制备:生料按以下重量百分比原料称取:石灰石82%,高硅砂岩12%、硫酸渣6%,采用湿法粉磨工艺,入磨原料配合一定比例的水分经过球磨机粉磨成合格料浆,将料浆泵入料浆泵系统8个料浆库,料浆经精确配料,放入料浆搅拌大池,经均匀配料泵进入料浆过滤系统,搅拌均匀,制成36%料浆。
[0061]2.料浆脱水:将上述浆料用真空吸滤机脱水,形成含水为18%的滤饼,滤饼落到带有BMP的输送皮带。
[0062]3.滤饼烘干破碎:通过箱式喂料机,滤饼被喂到烘干破碎机内,从窑尾来的废气(600°C)将其烘干成含水2.5%的生料粉,经烘干废气带入旋风分离器内进行料气分离,分离出来的生料粉进入烧成系统的旋风预热器、分解炉中,出旋风分离器的废气(约150°C)用窑尾风机送入电除尘器进行净化后,经烟?排入大气。
[0063]4.熟料烧成:将生料粉预热分解后喂入窑进料端,借助窑的斜度和旋转、慢慢地向窑头运动,在烧成带用窑头煤粉所提供的燃烧器将其烧结成水泥熟料。烧结后的高温熟料出窑落入篦式冷却机,通过推杆的往复运动,进入冷却机尾部的锤式破碎机,经打碎后卸落到链斗输送机上,再由链斗输送机输送至联合库的熟料堆场。通过熟料层后的气体作为二次风直接入窑,也作为三次风抽往窑尾分解炉燃烧用风及供煤磨烘干原煤用热风,多余的废气(约220~280°C)将通过窑头电收尘器净化后,由离心锅炉引风机排入大气,熟料电收尘器收集的粉尘由链式输送机送至链斗输送机。熟料的率值范围详见表1。
[0064]5.水泥微粉制备:熟料进入联合储存库后,经水泥磨磨头电子皮带秤配料,按照道路硅酸盐熟料:脱硫石膏球重量比=96: 4入磨进行粉磨,出磨水泥微粉合格即经水泥输送系统运入均化机水泥仓储存。
[0065]6.水泥混合制备:将水泥微粉、粒化高炉矿渣粉按99: I的重量比配制,混合均匀,所得水泥经过水泥输送系统运入水泥库。成品的主要性能参数详见表2。
[0066]实施例5
[0067]1.生料制备:生料按以下重量百分比原料称取:石灰石82%,高硅砂岩13%、硫酸渣5%,采用湿法粉磨工艺,入磨原料配合一定比例的水分经过球磨机粉磨成合格料浆,将料浆泵入料浆泵系统8个料浆库,料浆经精确配料,放入料浆搅拌大池,经均匀配料泵进入料浆过滤系统,搅拌均匀,制成35%料浆。
[0068]2.料浆脱水:将上述浆料用真空吸滤机脱水,形成含水为18%的滤饼,滤饼落到带有BMP的输送皮带。
[0069]3.滤饼烘干破碎:通过箱式喂料机,滤饼被喂到烘干破碎机内,从窑尾来的废气(600°C)将其烘干成含水1.8%的生料粉,经烘干废气带入旋风分离器内进行料气分离,分离出来的生料粉进入烧成系统的旋风预热器、分解炉中,出旋风分离器的废气(约150°C)用窑尾风机送入电除尘器进行净化后,经烟?排入大气。
[0070]4.熟料烧成:将生料粉预热分解后喂入窑进料端,借助窑的斜度和旋转、慢慢地向窑头运动,在烧成带用窑头煤粉所提供的燃烧器将其烧结成水泥熟料。烧结后的高温熟料出窑落入篦式冷却机,通过推杆的往复运动,进入冷却机尾部的锤式破碎机,经打碎后卸落到链斗输送机上,再由链斗输送机输送至联合库的熟料堆场。通过熟料层后的气体作为二次风直接入窑,也作为三次风抽往窑尾分解炉燃烧用风及供煤磨烘干原煤用热风,多余的废气(约220~280°C)将通过窑头电收尘器净化后,由离心锅炉引风机排入大气,熟料电收尘器收集的粉尘由链式输送机送至链斗输送机。熟料的率值范围详见表1。
[0071]5.水泥微粉制备:熟料进入联合储存库后,经水泥磨磨头电子皮带秤配料,按照道路硅酸盐熟料:脱硫石膏球重量比=97: 3入磨进行粉磨,出磨水泥微粉合格即经水泥输送系统运入均化机水泥仓储存。
[0072]6.水泥混合制备:将水泥微粉、粒化高炉矿渣粉按96: 4的重量比配制,混合均匀,所得水泥经过水泥输送系统运入水泥库。成品的主要性能参数详见表2。
[0073]实施例6
[0074]1.生料制备:生料按以下重量百分比原料称取:石灰石80%,高硅砂岩13%、硫酸渣7%,采用湿法粉磨工艺,入磨原料配合一定比例的水分经过球磨机粉磨成合格料浆,将料浆泵入料浆泵系统8个料浆库,料浆经精确配料,放入料浆搅拌大池,经均匀配料泵进入料浆过滤系统,搅拌均匀,制成35%料浆。
[0075]2.料浆脱水:将上述浆料用真空吸滤机脱水,形成含水为19%的滤饼,滤饼落到带有BMP的输送皮带。
[0076]3.滤饼烘干破碎:通过箱式喂料机,滤饼被喂到烘干破碎机内,从窑尾来的废气(600°C)将其烘干成含水2.2%的生料粉,经烘干废气带入旋风分离器内进行料气分离,分离出来的生料粉进入烧成系统的旋风预热器、分解炉中,出旋风分离器的废气(约150°C)用窑尾风机送入电除尘器进行净化后,经烟?排入大气。
[0077]4.熟料烧成:将生料粉预热分解后喂入窑进料端,借助窑的斜度和旋转、慢慢地向窑头运动,在烧成带用窑头煤粉所提供的燃烧器将其烧结成水泥熟料。烧结后的高温熟料出窑落入篦式冷却机,通过推杆的往复运动,进入冷却机尾部的锤式破碎机,经打碎后卸落到链斗输送机上,再由链斗输送机输送至联合库的熟料堆场。通过熟料层后的气体作为二次风直接入窑,也作为三次风抽往窑尾分解炉燃烧用风及供煤磨烘干原煤用热风,多余的废气(约220~280°C)将通过窑头电收尘器净化后,由离心锅炉引风机排入大气,熟料电收尘器收集的粉尘由链式输送机送至链斗输送机。熟料的率值范围详见表1。
[0078]5.水泥微粉制备:熟料进入联合储存库后,经水泥磨磨头电子皮带秤配料,按照道路硅酸盐熟料:脱硫石膏球重量比=94: 6入磨进行粉磨,出磨水泥微粉合格即经水泥输送系统运入均化机水泥仓储存。
[0079]6.水泥混合制备:将水泥微粉、粒化高炉矿渣粉按90: 10的重量比配制,混合均匀,所得水泥经过水泥输送系统运入水泥库。成品的主要性能参数详见表2。
[0080]实施例7
[0081]1.生料制备:生料按以下重量百分比原料称取:石灰石82%,高硅砂岩11%、硫酸渣7%,采用湿法粉磨工艺,入磨原料配合一定比例的水分经过球磨机粉磨成合格料浆,将料浆泵入料浆泵系统8个料浆库,料浆经精确配料,放入料浆搅拌大池,经均匀配料泵进入料浆过滤系统,搅拌均匀,制成33%料浆。
[0082]2.料浆脱水:将上述浆料用真空吸滤机脱水,形成含水为18%的滤饼,滤饼落到带有BMP的输送皮带。
[0083]3.滤饼烘干破碎:通过箱式喂料机,滤饼被喂到烘干破碎机内,从窑尾来的废气(600°C)将其烘干成含水2.5%的生料粉,经烘干废气带入旋风分离器内进行料气分离,分离出来的生料粉进入烧成系统的旋风预热器、分解炉中,出旋风分离器的废气(约150°C)用窑尾风机送入电除尘器进行净化后,经烟?排入大气。
[0084]4.熟料烧成:将生料粉预热分解后喂入窑进料端,借助窑的斜度和旋转、慢慢地向窑头运动,在烧成带用窑头煤粉所提供的燃烧器将其烧结成水泥熟料。烧结后的高温熟料出窑落入篦式冷却机,通过推杆的往复运动,进入冷却机尾部的锤式破碎机,经打碎后卸落到链斗输送机上,再由链斗输送机输送至联合库的熟料堆场。通过熟料层后的气体作为二次风直接入窑,也作为三次风抽往窑尾分解炉燃烧用风及供煤磨烘干原煤用热风,多余的废气(约220~280°C)将通过窑头电收尘器净化后,由离心锅炉引风机排入大气,熟料电收尘器收集的粉尘由链式输送机送至链斗输送机。熟料的率值范围详见表1。
[0085]5.水泥微粉制备:熟料进入联合储存库后,经水泥磨磨头电子皮带秤配料,按照道路硅酸盐熟料:脱硫石膏球重量比=93: 7入磨进行粉磨,出磨水泥微粉合格即经水泥输送系统运入均化机水泥仓储存。
[0086]6.水泥混合制备:水泥微粉通过均化机混合均匀,所得水泥经过水泥输送系统运入水泥库。成品的主要性能参数详见表2。
[0087]三、道路硅酸盐水泥相关试验参数
[0088]1.熟料质量控制参数
[0089]熟料质量是确保水泥质量的基础,上述实施例1-7的熟料质量控制参数结果表明,采用“湿法干烧”的方法生产熟料,使水泥具有低C3A (铝酸三钙)、高C3S (硅酸三钙)等特点,有效保证了水泥强度,降低水泥干缩率及耐磨耗,另具有生料均化性好、熟料质量高、转产便利、热耗低等优点,详见表1。
[0090]表1道路硅酸盐水泥熟料主要化学成分、率值及矿物组成
[0091]
【公开日】2014年6月18日 申请日期:2014年3月19日 优先权日:2014年3月19日
道路硅酸盐水泥及其生产方法
- 专利详情
- 全文pdf
- 权力要求
- 说明书
- 法律状态
查看更多专利详情
下载专利文献
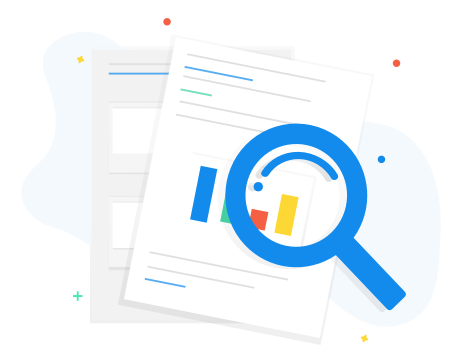
下载专利
同类推荐
-
张声军张亚锋, 胡长坤M·J·德内卡, S·戈麦斯M·J·德内卡, S·戈麦斯M·J·德内卡, S·戈麦斯
您可能感兴趣的专利
-
王善祝, 王明刘杰, 吕春叶强叶强崔桂玲
专利相关信息
-
刘书杰张雷