专利名称:步进梁式加热炉的滑动导轨的制作方法本发明涉及步进梁式加热炉的滑动导轨。步进梁式加热炉用于热轧工艺中,用来加热钢坯、钢板等钢材。为了支撑和输送要加热的钢坯、钢板或类似材料,在炉内设有多排滑动导轨,包括可动导轨和固定导轨。可动导轨周期地重复进行垂直和水平的往复运动以输送钢材,使钢材交替地在可动导轨和固定导轨之间传送。图1表示了一种步进梁式加热炉的导轨1。导轨1包括一个由耐热合金制成的空心滑道管10和许多轴向间隔地排列在管10上的滑道凸块12。安置在炉内的滑动导轨1,它的滑道管10的外周覆盖了一层耐火衬套14,而且滑道凸块的整个底部到以上部分也都覆盖了耐火衬套14。参照图6,传统的滑道凸块12是块状耐热合金(如耐热钴铸钢或耐热镍-铬铸钢),凸块通过焊接的方法固定地连接到滑道管10上。由于炉内通常保持在至少1000℃的高温状态,所以在滑道管的空心通道中通有冷却水,可避免滑道管由于温度升高而造成的弯曲、下垂或类似变形,并使管在承受材料的负荷时能保持抗弯强度。而且由覆盖在滑道管表面的可铸材料构成的耐火衬套14抑制了冷却水温度的提高,并使滑道管避免处于高温氧化气氛。滑道凸块由于冷却水从滑道管内流过而受到影响,因此,它比炉内温度低,结果使放在凸块顶上的钢材在与凸块接触的部位失去了热量。因而,材料与凸块接触部位造成了局部低温(即所谓的“滑道黑印”),这就引起加热不均匀的问题。如果这种不均匀加热较严重时,就会对以后的热轧工序产生严重影响。通过增加滑道凸块的高度似乎可以消除滑道黑印,这样就减小了冷却水对凸块顶部的影响。但是凸块高度的增加导致它的温度接近炉内温度,由于凸块通常由耐热钴或镍铬铸钢制成,于是降低了凸块的压缩强度并使它经受压缩变形。这样,滑道凸块在较短的使用周期后就必须要更换。靠增大凸块的横截面积,从而增大凸块与加热材料之间的接触面积和减少凸块单位面积上的压缩负荷似乎可以消除压缩变形。但是,接触面积的增加相应地减小了被加热材料暴露于炉内气氛的表面面积,造成加热效率降低,这就易引起加热不充分和温度分布不均匀,并且无法有效地排除这个缺陷。另外,也可能使用烧结的耐高温及在高温下有很高抗压强度的陶瓷材料制做滑道凸块。但是在运送要加热的材料时,凸块不仅要受到静负荷,而且还受较大的动负荷,以致使韧性较低的陶瓷材料易于破裂或击碎。而且陶瓷凸块不能直接焊接到滑道管上,因此,难以将凸块固定在滑道管上。例如,箱形滑凸块适合于用耐热合金作固定件,但如果凸块高度增加,它是不稳固的,并且易于滑脱,以致不能保证加热炉的稳定运行。已经解决了前述问题的本发明的主要目的是提供一种用于步进梁式加热炉的滑动导轨,它在高温下有较强的抗压缩变形的能力,并有较强的耐冲击性,而且它还使材料均匀地受热。更准确地说,本发明的目的是提供一种滑动导轨,它包括一根耐热合金制成的空心滑道管,滑道凸块竖直固定在滑道管上并以一定的间隔轴向地排列在滑道管上,每个滑道凸块都包括一个连接到滑道管上的第一部件和与要加热的材料相接触的第二部件,有一层衬套覆盖在滑道管的外周表面,并覆盖滑道凸块的整个底部和到朝上方的一部分,第一部件由耐热合金制成,第二部件由复合材料制成,该复合材料包括一种耐热合金基体和分散在其内的陶粒,陶粒的含量占复合材料总重量的30%到70%,滑道凸块的高度大于120mm。
图1是步进梁式加热炉滑动导轨的透视图;
图2到图5为体现本发明的不同的滑道凸块,其中每个图的剖面(Ⅰ)是横剖视图,剖面(Ⅱ)是沿导轨轴的纵剖视图;
图6表示传统的滑动凸块,它的剖面(Ⅰ)和(Ⅱ)分别为横剖视图和沿导轨轴向的纵剖视图;
图7a是使用不同陶粒含量的滑道凸块试验所获得的结果的示意图;
图7b是说明滑道凸块压缩变形的横剖视图;
图8是表示陶粒含量和冲击能之间关系的曲线图;
图9是表示温度和不同材料的抗压强度之间关系的曲线图;
图10是表示滑道凸块的高度和滑道凸块顶部与炉内的温差之间关系的曲线图;
图11是表示衬套厚度和滑道凸块顶部与炉内的温差之间关系的曲线图;
图12是表示复合陶瓷材料的厚度和发生在将陶瓷材料写耐热合金连接在一起的工序期间产生的断裂之间关系的示意图;
图13是表示滑道凸块压缩变形的比率和凸块第二部件的横截面面积比值之间关系的曲线图;
图14是表示滑道凸块的热应力和凸块水平截面的长宽比之间关系的曲线图。
体现本发明的滑动导轨将参照附图作详细的描述。然而,应该理解,下面的实施例只是为了要说明本发明,而本发明不仅仅局限于此。图2到图5显示了本发明的滑动导轨1。每个导轨1都包括一根滑道管10和一些滑道凸块12,每个滑道凸块都包括一个连接在滑道管10上并作为一个底部的第一部件12a,以及一个连接在第一部件上部并适合于与要加热的材料相接触的第二部件。在滑道管的整个外周表面和滑道凸块12的整个底部到顶部都覆盖一层耐火衬套14。第一部件12a是由耐热合金制成的,第二部件12b是由耐热合金和陶瓷材料的复合材料制成的。更准确地说,复合材料包含作为基体的耐热合金和占复合材料总重量30%到70%的陶粒。适用的耐热合金包括有耐热钴铸钢和耐热镍-铬铸钢。比如,可铸材料可用于制造耐火衬套14。
为了制备第二部件用的复合材料,将耐热合金和陶瓷材料在融熔状态下混合在一起,然后迅速冷却,这样,大小在0.01到0.1μm的细陶粒被均匀地分散在合金基体内。分散的粒子和耐热合金基体产生的复合作用,使形成的材料在高温下具有较高的抗压强度和韧性。复合材料可以说是介于易碎的细陶粒和有韧性的合金材料之间的材料。复合材料的特性可通过改变陶粒的含量而改变。
预定形状的滑道凸块可以靠熔化复合材料,例如用钨极隋性气体保护电弧源来熔化复合材料并将该材料与耐热合金的第一部件连接在一起来制备。
我们已对不同陶粒含量(重量百分比)的、已实际应用于加热炉的复合材料进行了测试。并发现当陶粒的重量百分比含量在30%到70%之间时,该复合材料适合于长期使用而不会发生断裂或压缩变形。测试结果是在如下条件下产生的,图7a显示了这一结果。
炉内温度1280℃,滑道凸块宽500mm,长130mm,高200mm,被加热材料(钢板)厚220-260mm,步进梁移动大约100,000次。
制作的滑道凸块的陶粒重量百分比含量为10、15、25、35、50、65、75、85或90%,每种含量有两块被连接在滑道管上。扁钢坯随意地放入炉内。图7a中的符号代表下列结果X显著的压缩变形(3-10mm)△较小的压缩变形(0.5-3mm)○正常(包括不影响使用的微小变形)●凸块的上缘部破碎或断裂在上述变形中,数值指的是滑道凸块从原来的高度降低了一段高度△h(见图7b),降低的这段高度是由于压缩变形引起的。
图7a的结果表明,当陶粒的重量百分比含量在30%到70%时,滑道凸块显示出了卓越的性能。
测试结果的分析如下图8表示复合材料的高温韧性值和陶粒含量之间的关系,图9表示复合材料的高温抗压强度和耐热合金的高温抗压强度的比较。参见图9,陶粒的重量百分比含量为70%,50%和30%的复合材料分别由线(a)、(b)和(c)来表示,钴合金由线(d)表示,镍-铬合金由线(e)表示。图8显示出,陶粒的重量百分比含量为30%时,冲击能为100Kg·Cm,而且韧性随陶粒含量的增加而降低。但是可以看出,当陶粒的重量百分比含量为70%时,冲击能仍有30Kg·Cm。此外,当冲击能的值小于30Kg·Cm时,断裂问题便能克服了。参见图9,比如钴合金线(d)在温度超过1210℃时,其抗压强度小于0.10Kg/mm2,而陶粒的重量百分比至少有30%的复合材料线(a)、(b)和(c),在温度高达1280℃的情况下,还保持至少0.10Kg/mm2的较高的抗压强度。
为了有效地防止由于放在滑道凸块顶部运送的材料上产生滑道黑印,我们发现,滑道凸块与炉内的温度差必须不大于40℃。形成的炉子内部与炉内气氛温度区内的滑道凸块之间的温度差,可归因于流过滑道管内的冷却水对滑道凸块的影响。此外,滑道凸块越高,流过滑道管内的冷却水的影响就越小,从而温差也就越小。而当衬套的厚度增加时,相应地提高了绝热作用,这有利于抑制冷却水温度的上升,结果,由于较低温度的冷却水对滑道凸块的影响,使得温差变大。
另外,在衬套的厚度保持定值,而使滑道凸块的高度变化的情况下,来测量滑道凸块的温度与炉内的温度之间的温差△T。图10表示了这个结果。参见图2(Ⅰ),术语“滑道凸块”的高度,指的是从滑道管的顶表面到滑道凸块的顶之间的距离H,术语“衬套的厚度”指的是从覆盖衬套的滑道凸块的底部到衬套的上部的尺寸t。把这一尺寸作为衬套的厚度,是由于冷却水对滑道凸块的影响取决于这覆盖部分的尺寸。图10的测试结果是在厚度t为110mm时获得的。该结果表明,当滑道凸块高于120mm时,滑道凸块和炉子内部之间的温差△T不大于40℃。如果衬套的厚度低于110mm,冷却水产生的影响就较小,使得滑道凸块的温度接近于炉内温度。
图11进一步显示出在滑道凸块的高度为200mm和150mm时衬套厚度t与温差△T之间的关系。参见图11,线(a)代表高度为200mm时获得的结果,线(b)代表高度为150mm时获得的结果。图11揭示了衬套厚度t与温差△T之间存在着确定的对应关系。因此,就可以先确定滑道凸块的高度,然后为使温差不超过40℃再根据所需的高度来确定衬套的厚度t。
假如滑道凸块暴露于1000℃以上的温度,而凸块高度超过120mm时,我们发现滑道凸块高于衬套的部分(即尺寸H-t见图2(Ⅰ))应至少有30mm,以便控制温度不超过40℃。
图2到图5表示体现本发明的各种滑道凸块,每一种凸块都包括耐热合金的第一部件和由耐热合金与陶粒的复合材料制成的第二部件。
图2的实施例包括第一部件12a和第二部件12b,第二部件是层状的,并且连接到第一部件的顶部。为了削弱流经滑道管内的冷却水的影响,滑道凸块的总高度应该增加,使得滑道凸块的顶部温度接近炉内温度,因而,由于上面已描述的陶瓷复合材料在高温下抗压缩变形的优良特性,就防止了凸块顶部的高温变形。
当陶瓷复合材料具有相当的厚度时,如果要将该材料与耐热合金的第一部件连接在一起,那么在熔接的过程中,材料可能发生断裂。图12表示出当陶瓷复合材料连接到耐热合金上时发生断裂的可能性,以便确定使用哪种厚度的复合材料。在该示意图中,空心圆(记号为○)代表正常样品(无断裂),实心圆(记号为●)代表会发生断裂的样品。断裂的程度按坐标来标出,位置较高的记号表示断裂的程度也较大。图12表明,当复合材料的厚度超过35mm时就会发生断裂,所以,陶瓷复合材料的厚度应该小于约35mm。因此,本申请建议采用图3到图5中的实施例。
图3的实施例包括一个具有大致位于中央位置的凸起部分16的第一部件,和帽形的并覆盖住整个凸起部分16的第二部件。第一部件设置凸起部分是为了减小构成第二部件12b的陶瓷复合材料的厚度。第二部件12b在凸起部分16的顶面和滑道凸块的顶面之间的厚度,以及凸起部分16的外周面和滑道凸块的外周面之间的厚度最好小于35mm,但厚度最好要大于8mm,更佳的是大于12mm,因为厚度过薄会使陶瓷复合材料的第二部件变得毫无意义。在制造第一部件的凸起部分16时,使凸起部分的横截面积从底部向顶部逐渐减小,使得第二部件有一缩小的顶面面积(如图3(Ⅰ)的虚线所示),这样可使第二部件的顶部在高温下的抗压强度提高。
图4的实施例包括具有大致位于中央部分的凸起部分16的第一部件12a和环状的、覆盖住凸起部分16的外周面的第二部件12b。对于该实施例,滑道凸块的顶部还部分地包括有耐热合金的第一部件,所以该实施例不能较大地提供抗压缩变形的能力,它只能用于顶部温度稍低的场合。
图5的实施例包括一柱状的第一部件12a和覆盖第一部件顶部和侧部的第二部件12b。该实施例是图3实施例的改进,改进在于增加了滑道凸块沿其高度上使用陶瓷复合材料的量。
无论上面的哪一种实施例,可铸的耐火衬套14覆盖住滑道管10的外周面以及滑道凸块的底部到朝上方向的一部分。
考虑到第二部件在高温下的变形率和两部件的膨胀系数等因素,图3到图5的实施例中关于包括有第一部件和第二部件的凸块部的水平截面的面积比最好具有如下特点。
首先,将安全系数考虑进去,滑道凸块在压缩负荷下其变形率达到0.025%/hr。变形率取决于第二部件相对于滑道凸块横截面的面积之比。图13表示出滑道凸块的变形率(%/hr)与第二部件对凸块的横截面积之比(S1/S2×100)之间的关系,其中S2是滑道凸块的总横截面积,包括第一部件和第二部件;S1是第二部件的横截面积,这些面积值是在单位面积压力为0.25Kg/mm2,温度为1250℃的情况下测得的。曲线图显示出,当横截面积之比大于50%时,变形率可以不大于0.025%/hr。
图14表示构成第一部件的耐热合金和构成第二部件的陶瓷复合材料的热应力关系,图中宽度对长度的比是(W/L),其中(W)代表横截面的宽度,(L)代表滑道凸块纵截面的长度(参见图2(Ⅰ)(Ⅱ))。用于测试的样品,它的第二部件在第一部件顶部以上的厚度是15mm。第二部件在第一部件侧部的厚度在(L+W-L2+W2]]>)/4的范围内,这是由于上述的横截面积之比的下限为50%。测试是在1200℃的温度下进行的。在曲线图中,曲线(ⅰ)代表当滑道凸块在炉内整个温度均匀一致时测得的结果,曲线(ⅱ)代表当凸块在低于实际运行时的相同条件下被冷却时测得的结果。曲线图揭示出,W/L比越大,则热应力越小。可以看出,不会导致断裂的允许的热应力上限是7.2kg/mm2,对应的W/L值至少为0.34。
如上详细描述的,装有本发明的滑动导轨的步进梁式加热炉适合于均匀地加热材料,并能有效地防止滑道黑印的产生。均匀加热的效果使随后的热轧工艺能生产出性能极稳定的高质量产品。另外,这种滑道凸块在高温下有着极好的抗冲击和抗压缩变形的特性,不易因热应力而断裂,因此可用于长期稳定的生产。
应该理解到,本发明并不局限于前述特定的实施例,而是可以根据
权利要求
1.一种适用于工作温度超过1000℃的步进梁式加热炉的滑动导轨,该滑动导轨包括一根空心的耐热合金的滑道管,滑道凸块竖直设置在滑道管的顶部并且以预定的间隔沿管的轴向排列,耐火衬套覆盖在滑道管的外周表面及滑道凸块的由底部向上的部分,每个滑道凸块包括一连接在滑道管上的第一部件和与被加热材料接触的第二部件,第一部件由耐热合金制成,第二部件由复合材料制成,该复合材料以耐热合金作底基,占复合材料重量的30%到70%的陶粒散布在底基内,滑道凸块的高度超过120mm。
2.根据权利要求
1所述的滑动导轨,其特征是覆盖滑道凸块底部及以上部分的衬套的厚度尺寸是这样确定的,即应使滑道凸块的顶部与炉子内部之间的温差不大于40℃。
3.根据权利要求
1所述的滑动导轨,其特征是滑道凸块的高度约为200mm。
4.根据权利要求
1所述的滑动导轨,其特征是第一部件顶部为平面,第二部件设置在第一部件之上。
5.根据权利要求
1所述的滑动导轨,其特征是第一部件在其顶部接近中央的部位有一凸起部分,第二部件是环状的,并覆盖在凸起部分的外周。
6.根据权利要求
1所述的滑动导轨,其特征是第一部件在其顶部接近中央的部位有一凸起部分,第二部件是帽状的,并覆盖住整个凸起部分。
7.根据权利要求
1所述的滑动导轨,其特征是第一部件是从滑道管的外周表面延伸的柱状体,第二部件覆盖住整个柱状的第一部件。
8.根据权利要求
1所述的滑动导轨,其特征是滑道凸块横截面的宽长比至少为0.34,第二部件所占据的滑道凸块的横截面积至少为50%。
用于工作温度超过1000℃的步进梁式加热炉的滑动导轨,包括一根空心的耐热合金的滑道管,滑道凸块竖直设置滑道管的顶部并且以预定的间隔沿管的轴向排列,耐火衬套盖在滑道管的外周表面及滑道凸块底部向上的部分。每个滑道凸块包括一连接在滑道管上的第一部件并由耐热合金制成,以及与被加热材料接触的第二部件。第二部件由陶瓷与耐热合金的复合材料制成,滑道凸块的高度超过120mm。
步进梁式加热炉的滑动导轨制作方法
- 专利详情
- 全文pdf
- 权力要求
- 说明书
- 法律状态
查看更多专利详情
下载专利文献
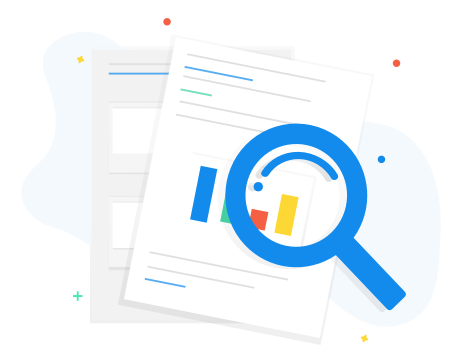
下载专利
同类推荐
-
高木清曾维芳曾维芳于海滨, 蔡海宁于海滨, 蔡海宁于海滨, 蔡海宁
您可能感兴趣的专利
-
于海滨, 蔡海宁于海滨, 蔡海宁薛黎明, 杨耀华薛黎明, 杨耀华薛黎明, 杨耀华薛黎明, 杨耀华薛黎明, 杨耀华
专利相关信息
-
薛黎明, 杨耀华薛黎明, 杨耀华薛黎明, 杨耀华薛黎明, 杨耀华