专利名称:共挤出的机械紧固件结构的制作方法发明的领域本发明涉及含杆卷材结构。更具体地说,本发明涉及由至少两种聚合物材料制成的含杆卷材结构。发明的背景圈-钩紧固件(如目前3M在市场上出售的ScotchmateTM紧固件)是普通的机械紧固件。钩扣的一种普通形状是蘑菇状,它还可通过与其它钩扣而非圈啮合而用作单一型机械紧固件。形成于卷材(web)上构成紧固件的这些钩扣结构是一种普通形状的含杆卷材。术语“杆”是指表面(如卷材)上的突起,与其外形、长度、长-宽比、几何形状或其它特征无关。美国专利4.056,593和4,959,265公开了一种早期挤出含竖杆的聚合物卷材(称为含杆卷材)的方法。该含杆卷材是由单种材料制成的。美国专利5,077,870的钩扣结构是将单组分热塑性树脂挤出至具有空腔阵列的模具中,再从该模具中分离,从而形成杆阵列。随后对这些杆进行压延,在杆的顶部形成较阔的头部。头部凸缘的形状、大小和曲率以及单位面积上杆的数量决定钩扣进入圈的难易程度以及啮合牢度。钩扣和杆的材料决定钩扣的挠性和杆的刚性,以及钩扣与圈的摩擦性。一些用于钩扣结构的树脂是高模量的热塑性树脂,它具有合适的强度来承载钩扣结构,但是在从圈上剥离时其弯曲强度不适于防止钩扣断裂或破裂。同时,在圈从钩扣的顶部移动至其底部时,该钩扣不具备低的摩擦性。美国专利5,393,475公开了一种使用两种不同材料制备在两面具有杆的含杆卷材的方法。该专利公开了将两种不同的材料挤出成两层基材,并使这两层基材通过两根夹辊,使所述材料填入这些夹辊的空腔中而形成钩扣。随后,使这两层基材通过两根夹辊,从而将其层压或粘合在一起。在一个实例中,使用与前两层具有化学亲和力的第三层。这种方法需要在层压前冷却这两股料流。还可如下制备钩扣通过型材挤出在卷材上形成长隆起,随后横向切开隆起,将卷材弯曲或拉伸以形成许多杆。可在切开前后在杆上形成头部。需要一种含杆卷材(如机械紧固件),它具有各种性能以满足不同用途。发明的概述本发明是一种卷材,在该卷材的至少一个表面上具有许多突出的杆。该卷材包括具有第一表面和第二表面的第一材料层和第二材料层。所述第二材料层具有朝第一材料层第一表面的第一表面和突出许多杆的第二表面。在两层材料的任何一层被冷却前,在其均处于熔融状态下将所述第一材料层和第二材料层复合在一起。第一材料层和第二材料层可由热塑性材料或可熔融加工的聚合物材料制成。第一层材料与第二材料不同,在一个实例中,形成第一层的材料突入并构成在第二层上形成的杆的至少一部分。在另一个实例中,材料层中的一层是不连续的,它包括多个与相同材料的其它部分不相连的相应材料部分。所述材料部分的形状选自柱状、棱柱、球状、平行六面体、不规则角度的形状和不规则曲线的形状。在另一个实例中,卷材的两个表面均带有杆,并且这些杆中的一个或多个具有顶盖。同时,卷材的至少一个表面可接受着色剂用于形成耐久的图象,从而能用于打印图案和图象用途,或者可具有摩擦性或剥离特性。还可形成附加的材料层,并在任何一层材料冷却前,在其均处于熔融状态时,将该附加的材料层与所述第一层和第二层复合在一起。
本发明还涉及具有许多杆的卷材的制造方法。它包括选择第一材料作为第一材料层,选择第二材料作为第二材料层。将第一材料层和第二材料层熔融成形,随后在这些材料层处于熔融状态下将第一材料层和第二材料层复合在一起,形成多层片材。接着,至少在第二材料层上形成许多杆。
所述杆可如下形成用至少一个含有孔阵列的温度受控表面压制所述多层片材,形成杆阵列。所述顶盖可通过用加热表面压制杆的顶端,在杆的顶端上形成顶盖而得到。
或者,可如下形成杆挤出多层热塑性或可熔融加工的材料通过定型模头,形成在至少一个表面上具有许多隆起的多层片材,使许多锐利刀刃垂直地通过该隆起,拉伸所述多层片材,将各条隆起分开,形成许多杆。形成的这些杆可具有钩扣状,或者随后用加热表面压制之,形成钩扣或带顶盖的杆。
熔融成形步骤可包括同时熔融成形第一材料层和第二材料层。复合步骤可包括在任何一层材料层冷却前将第一层和第二层复合在一起。可通过共挤出第一材料层和第二材料层来进行熔融成形。
附图简述
图1是含杆卷材的剖面图,其中杆形成于连续的下层材料上,杆的一部分和杆之间的卷材表面覆盖有上层材料;图2是含杆卷材的剖面图,其中杆顶部、杆的一部分和杆之间的卷材表面上覆盖有不连续的上层材料,并且杆的大部分是由连续的下层材料形成的;图3是含杆卷材的剖面图,其中卷材带有杆并且杆之间的卷材表面覆盖有连续的上层材料,所述杆具有主要由下层材料制成的内芯;图4是含杆卷材的剖面图,其中卷材带有杆并且杆之间的卷材表面覆盖有连续的上层材料,所述杆具有由很少下层材料制成的内芯;图5是含杆卷材的剖面图,其中卷材带有杆并且杆之间的卷材表面由连续的上层材料制成;图6是含杆卷材的剖面图,其中所述杆由许多基本连续的材料层制成;图7是含杆卷材的剖面图,其中所述杆全部由连续的外层材料制成,并且基底区含有不连续的弹性材料区;图8是在两个表面上均具有杆的卷材的剖面图,其中一个表面上的杆材料不同于另一个表面上的杆材料。
发明的详细描述机械紧固件的钩扣结构是含杆卷材的一种形式。这些机械紧固件在形成于卷材上的杆上形成某些类型的钩扣。在某些用途中,钩扣结构和其底部支承物由多种材料组成。在本发明中,将多种材料一起成形(如通过熔融成形(例如挤出))以提高机械紧固件的性能。这些性能(包括钩扣强度、钩扣和杆的挠性、耐久性、耐磨性、圈保持性、圈啮合性、柔软性、外观、剥离性和剪切强度)的提高取决于材料的选择。可选择材料和结构以改变机械紧固件的性能,从而用于不同用途。
另一种类型的含杆卷材具有无顶盖的杆结构。当杆表面自粘附时,该杆表面会自啮合在一起。
影响提高性能的某些因素包括材料层的厚度,杆结构(杆是否由一种或多种材料组成,当杆由多于一种材料构成时材料的相对位置)、材料层的形状(连续的、不连续的或多层)、杆的密度、杆的几何形状(杆基本是直的、倾斜的还是具有形状的钩扣)以及结构的第二表面的特性。
多层紧固件包括至少两层热塑性(或可熔融加工的聚合物)层,其中至少一个表面带有杆阵列,制造时先将其成形,在熔融状态将其复合在一起,随后冷却。这些材料可各自具有不同的性能。例如,一种材料可以是可塑的,而另一种可以是刚性的。材料种类的一些例子有聚烯烃,如聚丙烯或聚乙烯;其它热塑性树脂,如聚苯乙烯、聚碳酸酯、聚甲基丙烯酸甲酯、乙烯-乙酸乙烯酯共聚物、丙烯酸酯改性的乙烯-乙酸乙烯酯共聚物和乙烯-丙烯酸共聚物;弹性体,如天然或合成橡胶、含异戊二烯、丁二烯或乙烯(丁烯)嵌段的苯乙烯嵌段共聚物、茂金属催化的聚烯烃、聚氨酯或聚二有机硅氧烷;压敏粘合剂,如丙烯酸类、天然或合成橡胶、增粘的苯乙烯嵌段共聚物、增粘的聚二有机硅氧烷脲共聚物和无定形聚(1-烯烃);热熔粘合剂,如乙烯-乙酸乙烯酯;可塑的热塑性塑料,如尼龙或聚氯乙烯;非粘性粘合剂;或它们的共混物。多层材料(如多于三层,并通常高达一百层)还可使带杆表面卷材结构的新复合物的性能不同于单层材料的性能。
还可利用材料使卷材的一个表面或两个表面具有所需的性能。这些材料的一些例子包括粘合剂表面、具有研磨性或高摩擦力的表面、能提供低摩擦力表面的剥离表面和能接受材料(如粘合剂、涂料或用于形成耐久图象的着色剂)的活性表面。着色剂包括各种材料,如溶解在水中的墨水、溶解在有机溶剂中的油墨、或由100%活性材料组成的印墨。这些墨水、油墨、印墨可通过例如紫外光照射或静电成象进行固化。涂料可包括各种材料,可以是100%的固体材料或者是溶解或分散在任何水和有机溶剂混合物中的涂料。涂料的一个例子是一种能使材料可用喷墨打印机进行打印的涂料。
材料层的相对厚度会影响具体材料所起的作用。由薄的粘合剂层构成的杆外层和由刚性聚合物形成的粗杆内芯所产生的杆阵列比厚的粘合剂层包裹细的刚性内芯上形成的杆阵列更硬。
通过控制厚度、粘度和加工条件,可制成各种结构的基底和杆。这些结构与选择的材料一起决定最终机械紧固件钩扣的性能。图1是含杆12的第一种片材或卷材10的结构。这种结构使用两层(上层14和下层16)共挤出的材料。在这种结构中,使用较厚的下层材料。下层材料16构成片材的基底、内芯和杆12的上部。上层材料14构成在片材基底上和杆下部周围的表面层。如图1和许多其它实例所示,使用同一种材料制成上层14和下层16。在另一类实例中,可使用多种材料和多层次层分别构成上层14和下层16。
图2所示的结构中,上层14所具有的材料多于图1结构的上层所具有的材料。下层16同样构成片材10的基底和杆12的内芯。此时,在由下层16构成的杆上上层14形成冠。上层14还在片材的基底上形成表面层,包括围绕杆底部的材料包层。
在图3中,下层16构成片材10的基底和杆12内芯材料的圆柱。上层14构成基底上和杆上的表面层。在图4中,下层16同样构成片材10的基底并构成一小部分杆12。上层14构成基底的表面层并构成大部分杆材料。下层在杆中的比例可达到这样的程度,即上层构成基底和杆而下层是连续光滑的片材,不形成任何杆部分。图5显示一个与图4相似的实例。在图5中,下层16构成片材10的基底,而上层14构成在基底上的表面层并构成整个杆材料。
图6显示使用许多材料层18形成的含杆片材结构。所述许多层可少至二层或多至数十层不同的层。这些层可以是在不同的层中任意地重复的两种或多种不同的材料。片材的基底和杆均是由多层材料层形成的。这种结构可使得到的产物仅用一种材料(最外层材料)构成在基底上的表面层并构成杆的外表面。或者,如图所示,沿杆的底部至顶部的长度方向杆可露出许多层。
在形成杆以前,含杆片材的各层可同时形成或依次形成,只要在任何一层冷却前,在其处于熔融状态时将其复合在一起即可。因此,各层不是同时相互层压并冷却的。在卷材的一面形成杆以后,在卷材的另一面不再添加其它材料层以制成卷材。根据卷材预定的用途,有时也可向卷材施加其它材料(如粘合剂)并进行打印。
可将来自不同挤出机的不同熔体料流导入一个多料道模头或一个多层供料头以及一个薄膜模头中进行共挤出。在所述供料头技术中,至少有两种来自不同挤出机的不同材料被导入供料头中的不同狭缝(通常是2个狭缝至超过200个狭缝)。各股料流在供料头中合并,并以层状堆叠物的形式进入模头,在材料离开模头时它流出成层状片材。离开模头的层状片材通过两个压辊形成的辊隙。所述两个压辊中至少有一个具有用模具加工过(tooled)的表面以形成杆。或者,可如下形成杆使卷材通过带图案的模唇,形成纵向带有隆起的卷材,切开所述隆起并拉伸卷材以分开杆。多料道模头在模唇将来自不同挤出机的不同熔融料流合并在一起。随后对各层进行上述操作以形成杆。这种方法通常限于2-3层薄膜,因为当层数增加时,复杂程度随之增加。
可通过例如先挤出一层,随后挤出另一层的依次挤出来进行依次成形。这可采用一个或多个模头来实现。或者,可在模具中或用其它已知的方法形成材料层。可通过例如共挤出进行同时成形。可使用一个多料道模头,或使用一个分成多个模腔以形成多层的供料头。或者,可在模具中或用其它已知的方法形成各材料层。
杆的密度取决于产品的用途。最适用的密度范围为12-465个杆/cm2(81-3000个杆/英尺2)。可使用各种不同形状的杆。杆可以是直的、倾斜的或带顶盖的。带顶盖的杆可具有蘑菇状、高尔夫球座状或钉尾状的形状。它们可具有挤出的外形。直的杆可自啮合、可具有压敏粘合剂(PSA)外层或者可随后涂覆PSA。
带杆卷材还可具有一个光滑的表面(与含杆表面相反的表面),在卷材光滑表面上具有一层共挤出层,从而在含杆表面的机械紧固功能上再复合其它功能。
如图7所示,含杆卷材10可由非连续层20和连续层22制成,所述非连续层20可包括多个与相同材料的其它部分不连接的材料部分,它的形状包括例如柱状、棱柱、球状、平行六面体、不规则角度的形状和不规则曲线的形状。在一个实例中,所述不连续部分可由弹性材料制成。它们可以是埋入连续外层中的不连续弹性区,形成可局部拉伸的区域。在本实例中,连续的非弹性材料的熔体粘度最好高于不连续的弹性材料的熔体粘度,以提高弹性区沿卷材纵向的拉伸性。
如图8所示,在一个实例中,可在卷材10的两个表面上形成许多带有或不带有顶盖的杆12。这种卷材可用作例如缠绕拉辊的包层,或者用于要求控制摩擦力的其它领域。
另外,可使用各种添加剂,如物理或化学发泡剂(较好使一层或多层材料中的部分或全部发泡或膨胀)或填料(以改变材料的牢度和流动性)。发泡剂的一种用途是将其置于杆顶端的材料中,经发泡后形成顶盖。还可使用微球、阻燃剂、内脱模剂、着色剂、导热颗粒和导电颗粒。
如美国专利5,077,870所述,还可将杆的顶盖制成蘑菇头来制成钩扣。也可通过型材挤出在卷材上形成长的隆起,随后横向切割该隆起并拉伸形成许多杆,从而制得钩扣。可在切割前或在切割后在杆上形成顶盖。这可参见美国专利4,894,060。
如其它含杆卷材一样,本发明含杆卷材实际上可用于各种用途。
实施例下面通过实施例进一步说明本发明,这些实施例不对本发明范围构成限制。除非另有说明,否则在实施例中所有份、比例和百分数均是以重量计算的。使用下列试验方法表征下列实施例中的含杆卷材复合物。
180°剥离粘合试验试验1.25cm宽和15cm长的含杆卷材试样对不锈钢和/或光滑的双轴取向的聚丙烯平挤薄膜的180°剥离粘合性。将试样粘合在受试表面上,用2.1kg(4.5磅)压辊对该试样碾压4次。在受控的温度和湿度(约22℃,50%相对湿度)下对其老化约1小时后,除非另有说明,否则使用购自Instrumentor,Inc.,的3M90型滑动/剥离试验机以180°和30.5cm/min(12英寸/分钟)的速度对该试样带进行试验。结果以N/dm表示。
撕裂强度试验将约75mm长以及正好宽63mm的试样的一端放置在一个垂直平面中并使其长度方向朝水平延伸,试样的端部夹在一对固定的夹具上,另一端夹在与固定夹具水平距离为2.5mm的另一对可移动的夹具中。在两对夹具之间的试样下部边缘切开一个20mm的切口。随后使一个带有圆周刻度标尺的摆锤自由下落,沿切口撕裂预先割开的试样。在标尺上的摩擦固定的指针指示以克为单位的撕裂试样的阻力。本试验通常被称为Elmendorf Tear Strength Test,结果以g/ply表示。
屈服负荷试验(ASTM D-882-81)将25.4mm(1.0英寸)宽、约150mm长的膜试条固定在拉伸试验机(InstronTM拉伸试验机,上夹具和下夹具相距25.4mm)上。随后以254mm/min(10英寸/min)的速度分开夹具直至达到屈服点。薄膜是在70-72℃和50%相对湿度下平衡约2星期后对该薄膜的纵向进行试验的。屈服点负荷以磅/英寸宽表示。
冲击强度试验进行冲击强度试验。进行两种试验(a)全片材和(b)2.5cm(1英寸)折痕。在全片材试验中,从在约23℃和50%相对湿度下经24小时调理的较大片材中切割数片尺寸各为10.2×15.2cm(4×6英寸)的试样,随后将其放置在试样架上。将该试样架放置在指示器设定为“p”的13-13 TMI型动态落球试验机中。松开预定重量的摆锤并冲击该试样。以cm-kg为单位记录指示器刻度。在2.5cm(1英寸)折痕试验中,从在约23℃和50%相对湿度下经24小时调理的较大片材中切割数片尺寸各为2.5×15.2cm(1×6英寸)的试样。握住试样的两端将其弯成圈,将圈的一部分放入12AS型Sentinel热密封机(购自Packaging Industries,Inc,已设定在0.62MPa(90psi)0.2秒,关闭加热)中。形成的试条沿2.5cm宽度在纵向约一半之处具有折痕,将其放入试样架的中央并用12.3mm宽的粘合带定位。随后将试样架放入13-13型TMI动态落球试验机中,对试样进行试验并记录对折痕的冲击。如上面全片材试验那样给出结果。
粘合带猛拉(snap)试验使用粘合带猛拉试验(ASTM#3359)评价油墨粘合性。粘合带猛拉试验包括用新的单面剃刀片在油墨层上割痕而不破坏下层打印面,形成割痕约1cm间距的方格图案。用PA1施加器将一片约10cm长的3M ScotchTM610粘合带施加在该方格区,使约8cm长度的粘合带与油墨粘结,留下一端未粘合以方便试验者抓住。试验者的一只手抓住粘合带,另一只手保持图象不动。以约180°的角度尽可能快地向后剥离粘合带。优良的结果是无油墨被粘合带除去;良好的结果是有少量(5%或更少)油墨被除去;差的结果是有显著部分(5-25%)油墨被除去;失败的结果是几乎所有的油墨被除去。
实施例1-5实施例1-5的含杆表面的薄膜在薄膜的含杆表面一侧均具有一层PAS层,是自啮合紧固件。
在实施例1中,将组分A(上层14),(HL-2542-X,一种粒料状的橡胶基PSA,购自H.B.Fuller)加入单螺杆挤出机中,该挤出机的直径约为25mm(1.0英寸),L/D为24/1,螺杆速度为15.7rpm,并且升高的温度分布最高约为182℃。组分A通过挤出机,经过加热的颈管在至少约0.69MPa(100psi)的压力下连续出料,并进入安装在25.4cm(10英寸)宽的薄膜模头(UltraflexTM40模头,8811741型,购自Extrusion Dies,Inc.)上的三层可调叶片供料头(CloerenTM86-120-398型,购自Cloeren Co.,并设定用于两层)的一个入口。将组分B(下层16),ShellSRD 7-560(乙烯-聚丙烯抗冲击共聚物,购自Union Carbide)加入第二个单螺杆挤出机中,该挤出机的直径约32mm(1.25英寸),L/D为24/1、螺杆速度为30rpm,温度分布稳定地升温至约204℃,随后将组分B在至少约0.69MPa(100psi)的压力下通过加热的颈管连续地出料,并进入所述三层供料头的第二个入口。供料头和模头设定在约193℃。模头间隙为0.5-0.8mm(20-30mils)。两层熔融的物料(上层组分A和基层组分B)从模头中出料,并落入由辊隙压力为0.62KPa(90psi)的两个辊形成的辊隙中。第一个辊具有加热至59℃的用模具加工过的表面,所含空腔直径约为280微米(11mil)深度超过约2.5mm(100mil),间距约为813微米(32mil),形成的杆阵列的杆密度约为140个杆/cm2(900个杆/英寸2)。第二个辊具有镀铬表面,也加热至59℃。两层熔融的物料的上表面朝模具加工过的表面,下表面朝镀铬表面。形成的平挤薄膜以约1.5m/min(5fpm)的速度从模具加工过的表面上离去,形成带含杆表面的薄膜,其圆柱状杆从薄膜表面上突起,直径约300微米,高为587微米。这些与图3相似的杆结构被粘合剂层完全覆盖并具有组分B的内芯。
在实施例2-5中,具有杆表面的薄膜用与实施例1相似的方法制得,但是使用的模具加工过的表面具有不同的空腔密度、用于组分A的挤出机不同、并且使用不同的加工条件。模具加工过的表面的空腔密度使形成的具有杆表面的薄膜的杆密度约为390个杆/cm2(2500个杆/英寸2)。组分A加入的单螺杆挤出机的的直径约32mm(1.25英寸),L/D为30/1。对于实施例2-5,用于驱动组分A和组分B的挤出机螺杆速度之比分别为12.0/30.0、7.0/9.3、7.0/9.3和10.0/9.25,对于实施例2-5,挤出机加料组分A和B的最高温度分别为185℃/204℃、205℃/221℃、205℃/221℃和185℃/204℃。对于实施例2-5,卷材速度分别为2.1m/min(7fpm)、2.1m/min(7fpm)、3.0m/min(10fpm)和2.1m/min(7fpm)。各个实施例的辊隙压力为0.62MPa(90psi),实施例2-5各辊的表面分别加热至65℃、60℃、60℃和48℃。
对实施例1-5的具有杆表面的薄膜试验180°剥离粘合性(使用上述试验方法)。结果和组分A和组分B的挤出机螺杆速度比以及各实施例的杆密度一起列于表1。
表 1
>共挤出的具有杆表面的膜自啮合,无需带顶盖的顶端和圈状的配合物就能用机械方法紧固在一起。粘合性受组分A厚度的影响,该厚度由用于组分A和B的相对螺杆速度、膜卷材的速度和杆阵列密度所决定。在低杆阵列密度时,在杆顶部和杆之间的基底上的PSA(组分A)是主要的啮合表面,因为杆之间的距离远大于杆的直径。在高杆阵列密度时,杆的侧面和杆之间的凹谷是主要的啮合表面,因为PSA同时涂覆杆的侧面和杆之间的基底。当杆阵列的密度足以形成大量的杆侧面啮合时,粘合剂层的厚度具有更明显的影响。
实施例6-12和比较例1实施例6-12的具有杆表面的薄膜由至少两种不同聚合物的各种组合而制成,上述聚合物包括热塑性塑料、热塑性弹性体和弹性体。组分A作为表层,组分B作为芯层。
在各个实施例中,向一种组分中加入0.5-1.0重量%的蓝色颜料,向另一种组分中加入0.5-1.0重量%的红色颜料,从而能目测确定杆的外形以及随后成形的杆的顶部和杆身的形状。
实施例6的具有杆表面的薄膜用与实施例1相同方法制得,但是使用不同的材料和加工条件。组分A是PP7644(一种聚丙烯聚合物,熔体流动为23g/10sec,购自Amoco),组分B是PP5A95(一种聚丙烯聚合物,熔体流动为9.5g/10sec)。使组分A以102rpm通过加热至约246℃的单螺杆挤出机(32mm(1.25英寸),24/1L/D)。使组分B以60rpm的通过加热至约216℃的单螺杆挤出机(19mm(0.75英寸),38/1 L/D)。将供料头加热至约246℃。具有杆表面的薄膜的移动速率为1.5m/min(5fpm)。将具有模具加工过的表面的辊表面加热至约50℃,将具有镀铬表面的辊加热至约50℃。经目测检查,表面上的杆与图3所示的杆相似。这些杆兼有较软的热塑性组分A的较软手感和较硬的热塑性组分B的较硬的内芯支承。
在实施例7中,具有杆表面的薄膜用与实施例6相同的方法制得,但是组分A是PP5A95,使之以45rpm通过19mm(0.75英寸)KillionTM单螺杆挤出机(L/D为32/1,加热至约216℃)。组分B是ENGAGETMEG8200(一种乙烯/聚α-烯烃共聚物,购自Dow Plastics Co.),使之以75rpm通过32mm(1.25英寸)KillonTM单螺杆挤出机(L/D为24/1,加热至约232℃)。具有杆表面的薄膜以2.4m/min(8fpm)的速度移动。将具有模具加工过的表面的辊和具有镀铬表面的辊加热至约70℃。经目测观察,在表面上的杆与图1所示的杆相似。杆的顶部兼有弹性组分B的较高摩擦性和较硬热塑性组分A的圆柱形较硬的支承。
在实施例8,具有杆表面的薄膜用与实施例7相似的方法制得,但是组分A是EngageTMEG8200,使之以50rpm通过挤出机,组分B是PP5A95,使之以70rpm通过挤出机。具有杆表面的薄膜以2.1m/min(7fpm)的速度移动。将具有模具加工过的表面的辊和具有镀铬表面的辊冷却至约7℃。经目测观察,在表面上的杆与图1所示的杆相似。杆的顶部兼有较硬热塑性组分A较低的摩擦性和弹性组分B的圆柱形较软的支承。
在实施例9中,具有杆表面的薄膜用与实施例7相似的方法制得,但是组分A是EngageTMEG8200,使之以60rpm通过挤出机,组分B是StyronTM666D(一种聚苯乙烯,购自Dow Chemical Co.),使之以60rpm通过挤出机。具有杆表面的薄膜以2.1m/min(7fpm)的速度移动。将具有模具加工过的表面的辊和具有镀铬表面的辊加热至约7℃。经目测观察,在表面上的杆与图3所示的杆相似。杆兼有弹性组分A的光滑手感和硬性热塑性组分B的硬性内芯支承。
在实施例10中,具有杆表面的薄膜用与实施例7相似的方法制得,但是组分A以60rpm通过挤出机,组分B是20重量%StyronTM666D和80重量%PP5A95的预混物,使之以50rpm通过挤出机。具有杆表面的薄膜以3.0m/min(10fpm)的速度移动。将具有模具加工过的表面的辊和具有镀铬表面的辊加热至约50℃。经目测观察,在表面上的杆与图3所示的杆相似。杆兼有刚性较小的热塑性组分A的较软手感和由内芯形成的增强性,这种内芯是由较刚性的热塑性塑料的细长的不连续区在作为表层的同样材料的连续区中形成的。
在实施例11中,具有杆表面的薄膜用与实施例7相似的方法制得,但是组分A是No.1057(聚丙烯均聚物,熔体流动指数为11g/10sec,购自UnionCarbide),使之以15rpm通过38mm(1.5英寸)Davis标准DS15S型单螺杆挤出机(L/D为24/1,温度分布由约190℃升至232℃),组分B是CarbideTM5A97(聚丙烯均聚物,熔体流动指数为5g/10sec,购自Union Carbide)和VectorTM4111(一种苯乙烯-异戊二烯嵌段共聚物,购自Dexco Polymers)的预混物。该混合物的重量比为40∶60,使之以15rpm通过64mm(2.5英寸)的Davis标准25IN25型单螺杆挤出机(L/D为24/1,温度分布由约204℃升至232℃)。三层CloerenTM供料头是J.O.90-802型,模头是635mm(25英寸)CloerenTMEpoch Extrusion J.O.90-802。组分A和组分B的相对进料速率导致薄膜具有ABA结构,其中ABA的重量比为10∶80∶10。具有杆表面的薄膜以12.2m/min(40fpm)的速度移动。将具有模具加工过的表面的辊和具有镀铬表面的辊加热至约38℃。经目测观察,在表面上的杆与图3所示的杆相似。热塑性弹性组分B形成弹性的杆内芯,增强了杆的挠性,组分A外壳使杆具有适当的刚性。同时,严重过量的组分B提供有较大弹性的基底薄膜,使具有杆表面的薄膜的弹性明显大于仅由组分A制成的薄膜的弹性。
在比较例1中,具有杆表面的薄膜仅由一层SRD 7-560制得,其厚度与杆阵列密度与实施例11的数据相同。
在实施例12中,具有杆表面的薄膜用与实施例11相似的方法制得,但是组分A是AttaneTM4802(一种超低密度聚乙烯,购自Dow Chemical Co.),使之以48rpm通过挤出机,组分B是SRD 7-560,使之以122rpm通过挤出机。将组分A导入供料头的外两层,将组分B导入中间一层。组分A和组分B的相对进料速率导致薄膜具有ABA结构,其中ABA的重量比为10∶80∶10。具有杆表面的薄膜以18.3m/min(60fpm)的速率移动。将具有模具加工过的表面的辊和具有镀铬表面的辊加热至约71℃。经目测观察,在表面上的杆与图3所示的杆相似。低分子量的热塑性组分B形成刚性较低的杆内芯,使杆摸上去较柔软。组分A外壳使杆具有适当的刚性。同时,严重过量的组分B提供挠性较大的基底薄膜,使具有杆表面的薄膜的硬度明显低于比较例1的试样。
由实施例6-12可见,根据用作表层或芯层材料的聚合物组分的种类和在带顶盖的杆的杆身、顶盖以及在基底薄膜中的聚合物构型,顶盖、杆和基底薄膜的性能可有很大的不同。同时,观察到多层杆比单一杆更充分地填入模具加工过的表面(实施例12对比较例1)。
实施例13制备中间层不连续的三层具有杆表面的薄膜。用与实施例12相同的方法制得薄膜,但是使用不同的材料和加工条件。组分A是SRD 7-560,它以50.1和41.3rpm通过两个64mm(2.5英寸)单螺杆挤出机(L/D各自为24∶1,温度分布由约218℃升至274℃),并进入三层CloerenTM型可调节叶片供料头的外两层。组分B是KratonTMG1657(一种线型苯乙烯-(乙烯-丁烯)嵌段共聚物,购自ShellChemical Co.),将其以45rpm通过38mm(1.5英寸)单螺杆挤出机(L/D为24∶1,温度分布由约160℃升至204℃)并进入所述供料头的中层。一根钢插件用螺栓固定在下叶片上,移动上叶片使之与插件接触,以便将组分B的流动限制在以83mm(3-1/4英寸)间距加工在插件上的6mm(1/4英寸)宽的狭缝中。组分B从插件槽中出料后,刚好在进入457mm(18英寸)CloerenTM模头的成型区前它被组分A上层和下层包封。将具有模具加工过的表面的辊和具有镀铬表面的辊分别保持在约26℃和6℃。具有杆表面的薄膜以15.2m/min(50fpm)的速率移动,杆的高度约为760微米(30mil),杆的密度约为140个杆/cm2(900个杆/英寸2),总重量约为170g/m2。随后使具有杆表面的薄膜通过一个加热至约137℃的辊,使杆的顶部软化,形成蘑菇状头部或顶盖。当对该膜进行横向拉伸时,在埋有不连续的组分B的区域该膜表现出弹性伸长性能。
实施例14、15和比较例2实施例14和实施例15具有杆表面的薄膜包括两种不同的聚合物(组分A和组分B),如图6所示它们交替排列,即ABA…BA。
在实施例14中,具有杆表面的薄膜用与实施例6相似的方法制得,但是使用不同的材料和不同的加工条件,包括多层排列,形成具有29层的聚合物卷材。组分A是CarbideTM7-587(一种丙烯共聚物,购自Union Carbide),使之以122rpm通过64mm(2.5英寸)Davis标准25IN25型单螺杆挤出机(L/D为24/1,温度分布由约204℃升至232℃),组分B是ExactTM4041(乙烯-丁烯共聚物,购自Exxon),使之以48rpm通过38mm(1.5英寸)的Davis标准DS15S型单螺杆挤出机(L/D为24/1,温度分布由约190℃升至232℃)。随后使两种熔融材料进入位于70mm(97.5英寸)的71型Extrusion Die(购自Johnson Plastic Machinery)的预定的狭缝中。供料头含有一个插件,该插件具有一直排相邻的狭缝,对于组分A的所有层(即从里层至外层),各条狭缝具有的X(宽度)尺寸为12.5mm。所有其它狭缝的X尺寸为9.4mm。转移管将各个挤出机与第一和第二分流料道相连,该料道将材料送至插件中预定的狭缝位置。总共有29个狭缝,15个用于组分A,14个用于组分B。从插件中流出的产物具有大致矩形的截面并具有组分A和组分B交替的层。从插件上流出后,沿产物的Y轴(高度)较平稳地对其进行压制,同时较平稳地沿X轴(宽度)使其进行膨胀。使得到的宽的并且较薄的薄膜通过模头可调节的模唇,形成平的薄膜。调节加料速率,使得到的薄膜中组分A和组分B的重量比为80∶20。薄膜以16.5m/min(54fpm)的速率移动。分别将具有模具加工过的表面的辊和具有镀铬表面的辊加热至约71℃和93℃。
实施例15的具有杆表面的薄膜用与实施例14相同的方法制得,但是使用121个狭缝,形成的薄膜具有61层交替的组分A和60层交替的组分B。薄膜的移动速度为12.2m/min(40fpm)。
在比较例2中,具有杆表面的薄膜仅由单层CarbideTM7-587制成,它与实施例14的薄膜具有相同的厚度和杆阵列密度。
对各种具有杆表面的薄膜进行抗撕裂性、屈服点负荷和冲击强度试验。结果列于下表。
表 2<
>由表2可见,多层具有杆表面的薄膜的抗撕裂性和冲击强度要好于比较例试样。在剖面SEM下,惊奇地观察到在杆中多层材料保持完整无缺。
实施例16和比较例3实施例16说明将本发明用于制造能容易接受印刷或其它标记的具有杆表面的片材。用聚丙烯(Shell“SRD 7-560”)和BynelTM3101共聚物(一种丙烯酸酯改性的乙烯-乙酸乙烯酯共聚物,购自E.I.Dupont de Nemours,Wilmington,Delaware)制得双组分具有杆表面的薄膜。聚丙烯是在约55rpm由38mm单螺杆挤出机(Johnson公司制,L/D为30∶1,温度分布由150℃升至205℃)挤出的。共聚物单独地以约20rpm由25mm Killion单螺杆挤出机(Killion Company,Ann Arbor,Michigan制,L/D为30∶1,温度分布由约150℃升至约205℃)挤出。将两种挤出物在203mm宽的分路集料管薄膜模头(Extrusion Dies,Incorporated,Chippewa Falls,Wisconsin)中合并在一起。将挤出的双组分薄膜导入带有冷却装置并以2.68m/min(8.8英尺/min)旋转的三辊组件的上辊和中间辊之间的辊隙中。上辊和下辊由镀铬钢制成,中辊包覆有橡皮,橡皮表面上具有均匀的0.508mm(0.020英寸)直径、2.03mm(0.080英寸)深的空腔阵列。该空腔阵列以与辊的旋转轴平行的方式等距离间隔交错排列放置。各排中的空腔之间的间距为2.79mm(0.110英寸),排与排相隔1.40mm(0.055英寸)。从上辊和中间辊之间的辊隙出来后,使薄膜保持与中间辊接触而旋转180°(直至进入中间辊和下辊之间的辊隙并从该辊隙出来),使之转移至下辊。与下辊表面接触并运转约180°以后,将形成的具有杆表面的双组分薄膜导向一个收卷机。该薄膜产品具有聚丙烯含杆表面和由25-50mm厚的Bynel共聚物层组成的光滑表面。
在比较例3,随后对具有杆表面的薄膜(由Shell聚丙烯SRD-560制成,杆大小和杆阵列密度与比较例2相似,但是膜的移动速度为12.2m/min(40fpm))进行加工以形成杆顶盖。接着使用44mm(1.35英寸)Prodex 13524型单螺杆挤出机(L/D为14∶1,温度分布升至约227℃)和单层模头(宽度约305mm(12英寸))在具有杆表面的薄膜上涂覆一层厚度为25微米的BynelTM3101。卷材的移动速度为9.1m/min(20英尺/min)。该挤出涂覆是在加热的辊隙中进行的,其中铬辊被加热至121℃,与杆表面接触的橡胶垫辊被加热至10℃,以便使界面粘合增至最大,而不损害带顶盖的杆结构。
随后对实施例16和比较例3的试样进行电晕处理,并使用Pamarco HandProofer(购自Pamarco Inc.,Roselle,New Jersey)涂覆SSKP-4000黑色胶印印墨(购自Werneke Inks,Plymouth,Minnesota)。在环境温度使印墨干燥10分钟。各个试样均得到良好的印刷质量,对各个试样进行粘合带猛拉试验。对于实施例16,观察到具有良好的印墨粘合性并且未观察到组分B与组分A脱层。对于比较例3,观察到具有良好的印墨粘合性,但是组分B和组分A有些脱层。
实施例17用不同的方法共挤出与实施例16相似的具有杆表面的材料。由设定仅有二层的Cloeren三层供料头向约70cm宽的单层Cloeren模头供料。组分A是96%Union Carbide SRD 7-587和4%Reed光谱颜料母料(11000409244)的掺混物,它以15.9rpm通过64mm Davis标准单螺杆挤出机(L/D为24∶1,温度分布由215℃升至260℃)。组分B是96%Bynel 3101和4%Reed光谱颜料母料的掺混物,它以27rpm通过38mm Davis标准单螺杆挤出机(L/D为24∶1,温度分布由150℃升至205℃)。调节相对加料速率,使组分A的膜厚(包括杆的高度)约为130-150微米,组分B约25-50微米厚。具有杆表面的薄膜的移动速度为16.8m/min。将带有各种模具加工过的表面的辊加热至约52℃,将镀铬辊加热至约15℃。平均辊隙压力均为23psi。经边缘修整后形成的卷材宽50cm。产品的杆密度为50和140个杆/cm2。
随后使含杆卷材以12m/min的速度通过两个加热的辊隙,朝杆表面的热辊被加热至约140℃,朝B层的冷铬辊被冷却至约7℃。在不影响组分B层的同时在杆上形成蘑菇状的顶盖。对B层进行空气电晕处理以改进其着墨性。
用ScotchprintTM静电法印刷杆密度为140个杆/cm2的第一试样。使用OrcaIII层压机(上辊温度为92℃,下辊温度为56℃)以50psi的压力和0.76m/min的层压速度将印刷的转印纸8603热层压在光滑的B层上。得到完全转移的图象。目测观察表明经历了无缺陷的转印,得到良好的色彩密度。
使用390T丝网将Scotchcal 9705黑色丝网印墨印刷在杆密度为50个杆/cm2和140个杆/cm2的第二试样上,并使用中压汞蒸气聚焦的UV灯以168mT/cm2(American Ultraviolet Co.,Murrary Hill,NJ)固化之。使用粘合带猛拉试验测试印刷试样的印墨粘合性。两份试样均得到优良的印墨粘合性。
使用225目丝网在这些试样上丝网印刷SCOTCHCAL 3972溶剂基丝网印墨,并在66℃干燥30分钟。得到优良的印刷质量。两种试样均以优良的结果通过粘合带猛拉试验。在粘合带猛拉试验中,在两种情况下,均未观察到Bynel 3101和SRD 7-587层之间有脱层现象。
实施例18如实施例17制得的批料9701-3具有喷墨接受涂层(3M 8502URC),它是用3M 9540层压机在82℃,0.3m/min和64psi热层压在9701-3材料的光滑一面上的。随后使得到的结构通过Novajet III喷墨打印机(Encad Inc.6059Cornerstone Ct.W.,San Diego,California),用美国喷墨印墨(AmericanInkjet,13 Alexander Rd,Billeria,Massachusetts)打印之。粘合带猛拉试验表明具有良好的印墨锚固性,无印墨从卷材表明上被剥落。
比较例4用相同的方法对与比较例3相同的杆表面进行电晕处理。将喷墨接受涂层层压在光滑的表面,并用与实施例18相同的方法对涂层进行打印。粘合带猛拉试验表明印墨和喷墨接受涂层被从卷材表面上完全除去。
实施例19实施例19的具有杆表面的薄膜由两种不同的聚合物(组分A和组分B)组成,它们用图8所示的两层结构排列,薄膜的每一面具有从其表面上突出的杆阵列。
实施例19的具有杆表面的薄膜证明了本发明在制造不同组成的两主表面均具有突出物的工业辊覆盖材料方面的功效。这种制品提供一个改进的摩擦表面和一个完整的附着体系。具有两个主表面的熔融的双组分聚合物膜是如下制得的通过两个在204℃运行的单螺杆挤出机向分路集料管双组分薄膜模头供料,对材料进行挤出。双组分薄膜的第一主表面是组分A(Shell聚丙烯SRD 7-560,目前购自Union Carbide Corporation,Danbury,CT)。第二主表面是组分B(RecflexTMFP-D1720增韧的聚丙烯,购自Rexene Corporation,Dallas,Texas)。将挤出的双组分薄膜引入一组垂直放置的辊(三个温控共旋转的5英寸(12.70cm)直径的圆柱形辊铝套筒)的上辊和中辊之间的辊隙中。中辊和上辊的铝套筒具有圆柱形空腔(分别深0.66mm(0.026英寸),直径0.46mm(0.018英寸)和1.32mm(0.052英寸)深以及0.46mm(0.018英寸)直径),各空腔排与绕各辊圆周的旋转轴平行,空腔间和各排间间隔1.41mm(0.0556英寸)。空腔的交错排之间偏移0.71mm(0.0278英寸)以形成交错排列。将连续的熔融双组分薄膜放置在上辊和中辊之间的辊隙中,辊旋转约180°转至中辊和下辊的辊隙,此时部分冷却的双组分薄膜与第三辊(镀铬钢辊)接触并传输至第三辊的表面上,该第三辊再旋转180°,此时通过控制张力的收卷机将模塑的双组分制品从第二辊表面上取出。在第一主表面上形成的杆在与热表面接触后容易变形成蘑菇状顶盖,形成适合于与具有纤维圈的表面或与其同类钩扣啮合的机械紧固表面。在第二主表面上这样形成的突起具有韧性和挠性,当作为工业辊的接触表面时,在与通过的卷材或片材啮合时,它提供受控的摩擦力。
实施例20实施例20的具有杆表面的薄膜由两种不同的聚合物(组分A和组分B)组成,它们以三层ABA的结构排列,其杆如图1所示,由组分B组成的中间层具有弹性,它能降低随后的加工操作中产生的应力。该薄膜是通过挤出制得的。
将组分A(SRD 7-560)加入单螺杆挤出机(直径64mm,L/D为24∶1,速度为122rpm,温度分布由185℃升至232℃)。将组分B(ExactTMULDPE,一种线型低密度聚乙烯,购自Exxon)加入单螺杆挤出机(直径38mm,L/D为24∶1,速度为41rpm,温度分布由185℃升至232℃)。随后将组分A通入一个46mm(18英寸)宽的三层模头的上层和下层,并将组分B通入中层,形成熔融的三层薄膜。将熔融的三层薄膜输入由具有凹凸的表面和具有光滑的表面的两个辊形成的辊隙中,并用高达0.41MPa(60psi)的压力压制。凹凸的表面带有直径约430微米(17mil),深超过约1.52mm(60mil)的空腔,这些空腔的间距使得形成的杆阵列的杆密度约为50个杆/cm2(324个杆/英寸2)。两个表面的温度保持在约90℃。形成的平挤薄膜以约16.5m/min(55fpm)的速率从模具加工过的表面上离去,形成如图4所示的具有杆表面的薄膜。该薄膜的基底厚度约为127微米(5mil),从薄膜表面上突起的柱状杆的直径约为430微米,杆的高度约为760微米(30mil)。127微米基底膜包括三层,两层厚度约51微米(2mil)的组分A外层和一层厚度约25微米(1mil)的组分B中间层。随后以7.6m/min(25fpm)的速率将该具有杆表面的薄膜以杆表面向上的方式通过一组三辊两辊隙的加热辊,在直径为760微米(30mil),高度约510微米(20mil)的杆顶端形成顶盖。两个外辊加热至约149℃,中间辊加热至约16℃,两个辊隙均为280-635微米(15-25mil)。
将具有带顶盖的杆的所述三层具有杆表面的薄膜用作涂覆研磨制品的背衬,该制品用与美国专利5,551,961相似的方法制得。使用的磨料是180级经热处理的氧化铝,并且构造涂层(make coat)和上胶涂层(size coat)均为酚醛和脲醛粘合剂的共混物。
中间层使用弹性低分子量热塑性塑料的结果,由构造涂层和固化方法在具有机械紧固表面的均聚物研磨薄膜上原来形成的大多数应力减小,形成的研磨薄膜具有更好的性能(如卷曲)。
一种在至少一个表面上具有许多突出的杆(12)的卷材(10)。它包括具有第一和第二表面的第一材料层(14)和具有朝第一材料层第一表面的第一表面和突出许多杆的第二表面的第二材料层(16),在两层材料被冷却前,在其均处于熔融状态下将所述第一和第二材料层复合在一起。第一和第二材料层可由热塑性材料或可熔融加工的聚合物材料制成。一种卷材的制造方法,它包括选择第一材料作为第一材料层;选择第二材料作为第二材料层;熔融成形第一材料层和第二材料层;在这些材料层均处于熔融状态下将第一材料层和第二材料层复合在一起,形成多层片材;随后至少在第二材料层上形成许多杆。熔融成形包括例如通过共挤出同时熔融成形第一和第二材料层。
共挤出的机械紧固件结构制作方法
- 专利详情
- 全文pdf
- 权力要求
- 说明书
- 法律状态
查看更多专利详情
下载专利文献
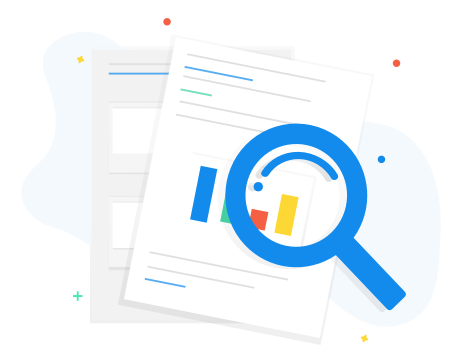
下载专利
同类推荐
-
R.J.V.艾弗里A·韦恩迪杰克欧希舜, S·S·拉姆博兹黄运贤黄运贤黄运贤利·博尔达克, 胡安·帕罗蒂
您可能感兴趣的专利
-
利·博尔达克, 胡安·帕罗蒂杨雪平许艾莎, 颜伟桂辉辉, 祝仲凯刘兵
专利相关信息
-
赵亮O·米尔盖, R·L·M·戈斯米尼O·米尔盖, R·L·M·戈斯米尼O·米尔盖, R·L·M·戈斯米尼