晶须增韧补强氮化硅复相陶瓷刀具材料制作方法
- 专利详情
- 全文pdf
- 权力要求
- 说明书
- 法律状态
专利名称::晶须增韧补强氮化硅复相陶瓷刀具材料的制作方法::本发明涉及机械零部件新型材料的研制,属陶瓷材料领域。陶瓷材料具有耐高温高强度、耐磨及抗腐蚀性好等优点而受到军工、航天及高温工程领域的广泛注目。近年来,陶瓷发动机的设想,为陶瓷实现其价值开辟了新的途径。陶瓷材料在具有上述优点的同时,还存在一个本质性的弱点-即陶瓷很脆。陶瓷的过低的韧性满足不了工程可靠性的要求而严重地影响了对陶瓷的大胆使用。改善陶瓷的韧性已经成为高温陶瓷材料研究领域内亟待解决的重要课题。目前,陶瓷增韧的方法主要有相变增韧、弥散强化和纤维或晶须增韧等方法,对于诸如Si3N4、SiC等超高温材料来说,在维持陶瓷的杰出的耐高温及高强度的前提下,改善韧性的有效的方法是晶须或无机纤维的增韧法。晶须增韧氮化硅材料的研究,在国内外都在进行,如欧州EP0194811专利报导,晶须的加入和复合,提高了氮化硅的断裂韧性,但是降低了材料原有的抗弯强度,从而降低了氮化硅原有的特长。因此,在保持氮化硅材料的高强度的前提下增加氮化硅的韧性的研究显得十分必要。本发明的目的是在氮化硅陶瓷中加入一定量的碳化硅晶须,采用更新的工艺方案和材料配方,使晶须不仅能起到增韧的作用,而且能起到增加材料强度的作用。为了使这种高韧性高强度的复合材料同时具有高的耐磨性能,本发明采用多相复合的混合物为晶须的增韧基体,使这种新型材料更适合用作切削刀具及其它受力状态下的耐磨部件。本发明的内容是在氮化硅粉末中加入一定量的经过特殊处理的碳化硅晶须,氮化钛或碳化钛粉末和少量的氧化物添加物,经混合、成型、烧结使其成为致密化的材料。这种材料具有高强度、高韧性和高的耐磨性能,可以用作切削加工用的刀具以及轴承、拔丝模等受力耐磨部件。由于该陶瓷材料还具有较高的导电率,可满足普通电火花加工的要求,解决了高强高硬陶瓷材料后加工难的问题,同时还可以加工为各种形状复杂的零部件。这是陶瓷后加工的重大变革。本发明的内容有以下几点1)原料以氮化硅粉末为主,加入5~30wt%碳化硅晶须。为了提高晶须的增韧效果,需要加入适量的氧化镁(MgO)和氧化钇(Y2O3),同时为了提高材料的强度,尤其是高温强度,需要加入一定量的La2O3和Al2O3。为了增加材料的耐磨性能,在配方中还加入了部分碳化钛(TiC)或氮化钛。这些添加物的总重为5~30%,添加物的作用是各有所不同的。MgO和部分Y2O3主要渗透到晶须的周围,起到调节晶须与基体之间的结合力的作用;而La2O3、Al2O3和部分Y2O3则主要进入基体晶粒的晶界,一方面起促进烧结致密化的作用,另一方面起增加晶界结合力的作用。所以配方上表现为多种结晶相的复合,称为复相陶瓷的基体。2)晶须的分散处理为了使晶须能够均匀的分散在基体中,晶须的分散也是很重要的。本发明采用的分散工艺是,在极性溶剂(如水、乙醇、异丙醇、正丁醇等)中加入分散剂(正硅酸乙酯、钛酸四丁酯、异丙醇铝或高分子、聚合物等),将晶须放入,并用机械搅拌和超声波振荡,制成悬浮溶液,保证晶须的稳定分散;3)工艺为了使添加物起到所期望的作用,采用分头加入、二次混合的办法,即先分别将经分散处理的SiC晶须、MgO和Y2O3以及Si3N4粉体、La2O3、Al2O3和Y2O3、碳化钛分别制备成晶须混合体和基体混合体,将这两种混合体分别混合均匀,经过干燥、预烧后,再将这两种混合体混合到一起(二次混合)。二次混合的目的,是使MgO和Y2O3易粘附着在SiC晶须表面,而La2O3、Al2O3及其化合物相对集中在Si3N4颗粒周围。TiC加入到氮化硅粉体之中,使之均匀的分散在氮化硅相基体之中。混合后的粉料与乙醇混合成浆体,经过压虑,烘干后再成型成所需形状的坯体。4)材料的绕结致密化为了使材料致密化,采用热压烧结的方法。热压温度为1700~1900℃;压力为3~6吨;周围气氛为氮气气氛;保温时间为60~120分钟。5)加工方法由于加入了比较多的高导电率的SiC和TiC结晶相,所得的复合材料的导电率比较高,达到了一般的电火花切割加工的要求。所以这种材料能够采用电火花,线切割成各种复杂形状的零部件。用晶须增韧补强后的陶瓷基复合材料,韧性高、强度大,具有更高的机械强度、断裂韧性、耐高温、抗热震冲击,同时还具有很高的耐磨性能。这种材料不仅可以用于切削工具,也可使用于发动机部件和各种受力耐热耐磨部件。实施例分别将氮化硅、氧化镁、氧化钇、氧化镧、氧化铝、碳化钛粉末粉碎后,过80目的筛子,备用。在乙醇和乙丙醇铝混合溶液(混合比10∶1体积比)中,加入40克碳化硅晶须,用超声波振荡分散30分钟后,再加入5克MgO、10克Y2O3,再用超声波振荡30分钟后,压虑并且烘干,然后放入电炉中加热到800℃并且保温2小时,使MgO和Y2O3比较强地粘附在晶须的表面。再将所得块体粉碎并使之全部通过60目的筛孔。将过筛后的粉末加入到无水乙醇中进行球磨10小时。所得浆料为浆料1。另外将200克Si3N4、10克Y2O3、20克La2O3、2克Al2O3和40克TiC加入到400ml的无水乙醇中进行球磨10小时,所得浆料为浆料2。然后,把浆料1和浆料2倒入同一混合罐中,再进行第二次混合球磨,球磨时间为10小时,所得浆料为浆料3。将浆料3压虑、烘干后,过60目的筛子,再将所得粉体干压成型,做成直径为105mm的短圆柱坯体。将此圆柱放入石墨模具内,在1820℃、氮气气氛、4吨压力的条件下保温保压烧结90分钟,得到高度致密化的圆片材料。材料的相对致密度达到98%以上,材料的电阻率小于37欧姆·cm。完全达到电火法加工的要求。将该圆片上下表面磨平后,用电火花线切割成所需形状的零部件。对于该本发明来说,将圆片的一半切割成3×4×40mm的试条6根和3×6×40mm的试条6根,以供力学性能测试用。而另一半切割成13×13×8mm的四方刀片及φ13mm圆形刀片以供测试刀具切削性能。材料力学性能测试结果见表1表1刀具材料的性能及其测试方法</tables>与国外的类似产品的比较见表2表2刀具材料的性能及其刀具对护套(硬化毛坯Cr27HRC60-61)粗车切削性能的对比</tables>注*采用了瑞士Sandvik公布的指标。在切削试验中,本发明所制造的刀具特别适用于表面粗糙不平的工件和形状不规则的工件,最大切削涂度可达8mm。这主要是因为材质的韧性高,耐冲击。由于这个原因,在切削试验中,有时突然停电而刀具却完好无损。对切削合金钢、不锈钢等材料本发明刀具更具优越性。刀具的切削性能测试方面,最佳切削速度为40~70m/min。用此切削速度,用材质为1Cr18Ni9Ti合金及CrWMn为切削对象,切削路程为500米后,磨损量(mm)及磨损量为0.3mm时的切削总路程与其他同类型刀具的对比结果列于表3、表4表3刀具的性能的比较-对1Cr18Ni9Ti合金切削总长度为500米时刀具的磨损量表4刀具的性能的比较-磨损量为0.3mm时刀具的切削总长度(切削CrWMn淬硬钢HRC60-63的寿命对比)注例2的刀片的制备工艺和配方基本与例1相同,只是TiC相的加入量较少(12W%)。权利要求1.一种晶须增韧补强的氮化硅复相陶瓷刀具材料,其特征在于这种材料以氮化硅粉末为主,加入一定量的碳化硅晶须,又加入一定量的氧化镁和氧化钇以提高材料的韧性,加入一定量的氧化镧和氧化铝以提高材料的高温强度,加入一定量的碳化钛或氧化钛以提高材料的耐磨性。2.一种如权利要求1所述的刀具材料,其特征在于其中所述的氮化硅粉末的重量百分比为60~90%,碳化硅晶须的重量百分比为5~40%,所述的氧化镁、氧化钇、氧化镧、氧化铝和碳化钛等添加物的总重量百分比为5~40%。3.一种以氮化硅为主要原料制备复相陶瓷刀具材料的方法,其特征在于在原料中加入碳化硅晶须,碳化钛粉末和少量的氧化物添加剂,其具体制备方法包括以下各步骤1)晶须的分散处理将晶须放入极性溶剂和分散介质经机械搅拌和超声波振荡制成悬浮溶液,保证晶须稳定分散;2)在经分散处理后的碳化硅晶须中加入氧化镁和氧化钇制成晶须混合体,混合均匀后干燥预烧;3)在主要原料氮化硅中加入氧化镧、氧化铝、氧化钇和碳化钛或氮化钛用湿法制成基体混合体,混合均匀后干燥预烧;4)将预烧后的上述二种混合体混合均匀,再与乙醇混合成浆体,经过压虑、烘干,再成型成所需形状的坯体;5)用热压烧结法使材料致密化,即将坯体放在保护气氛中,在高温高压下保温一段时间。4.如权利要求3所述的制备方法,其特征在于其中所述的热压温度为1700~1900℃,压力为3~6吨,保温时间为60~120分钟,保护气氛为氮气。5.一种以氮化硅粉末为主要原料,加入一定量的经过特殊处理的碳化硅晶须、碳化钛粉末和少量氧化物添物后,经混合均匀、成型热压后制成的晶须增韧补强氮化硅复相陶瓷,其特征在于所述的复相陶瓷材料用来制作切削刀具和发动机零部件及其它受力的耐热、耐磨损的零部件。全文摘要本发明涉及机械零部件材料的研制,属陶瓷材料领域。本发明以氮化硅粉末为主要原料,加入一定量的经过特殊处理的碳化硅晶须、碳化钛粉末和少量的氧化物添加剂,混合均匀后成型,烧结使其致密化。这种材料具有高强度、高韧性和高的耐磨性,可以用作切削加工刀具的材料以及轴承、拨丝模等受力耐磨部件。由于该陶瓷材料还具有较高的导电率,可用电火花进行加工,所以可以制形状复杂的各种机械零部件。文档编号C04B35/76GK1051900SQ9011001公开日1991年6月5日申请日期1990年12月29日优先权日1990年12月29日发明者黄勇,李建保,郑隆烈,胡晓清,衷待群,吴建光申请人:清华大学
查看更多专利详情
下载专利文献
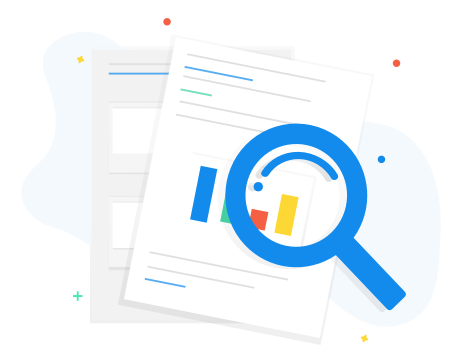
下载专利
同类推荐
-
名取荣治汤玉斐郭伟明
您可能感兴趣的专利
-
鲁中良鲁中良陈秀丽陈秀丽
专利相关信息
-
陈秀丽王红云王红云