一种建筑用模块楼板组装结构及工艺方法【技术领域】[0001]本发明涉及模块化建筑【技术领域】,尤其涉及一种建筑用模块楼板组装结构及工艺方法。[0002]随着我国的社会进步和经济发展,能源和环境问题越来越多的被各行业所关注。对于住宅建筑而言,其基础造型、材质选择以及室内装修等方面,均需要严格执行环保、节能的标准。众所周知,在建设速度与住房需求增长的矛盾日益突出的情况下,大量挖山采石、取土烧砖制作建材,对土地资源和环境的破坏日趋严重;并且,相应技术的配套和完善、建筑设计和产品标准化等问题,导致住房质量并没有随着经济的发展而显著提高。[0003]受众多因素的影响,目前的住宅产业化水平还处于较低的水平,主要有以下两方面的原因。首先,建筑结构和建筑体系相对比较单一,基于钢筋混凝土结构的建筑体系比较成熟的现状,例如,钢筋混凝土剪力墙结构、框架结构、框架一剪力墙结构、筒体结构等,但是,与上述结构体系配套的技术以现场现浇工艺为主,与住宅产业化要求差距很大。其次,缺乏配套技术和系统化的产品,我国住宅技术仍以单项技术、产品为主,对提高住宅的整体性能和质量效果不明显。上述弊端严重制约了我国住宅产业化的健康发展,在转变经济增长方式、追求绿色发展的今天,加快住宅建设从粗放型向集约型转变,推进住宅产业现代化,加快住宅升级换代迫在眉睫。[0004]因此,针对以上不足,需要针对住宅建筑材料结构提供一种新材料、新技术和新工艺,在满足住宅建设质量的基础上,为住宅产业化提供可靠的保障。
[0005](一 )要解决的技术问题[0006]本发明要解决的技术问题是现有住宅建筑材料无法满足住宅产业化需求,影响住宅建设质量的问题。
[0007]( 二 )技术方案
[0008]为了解决上述技术问题,本发明提供了一种建筑用模块楼板组装结构,包括预制的模块楼板、钢楼柱和钢梁;其中,至少三根所述钢楼柱形成所述模块楼板的安装单元;与所述安装单元相应设置的钢梁,分别固定于所述安装单元的相邻两根所述钢楼柱之间;且每根所述钢梁的上表面均固定设置有竖向延伸的限位凸起,所述模块楼板的边缘相应开设有贯通孔;所述模块楼板的边缘搭抵于所述钢梁的上表面,且其上的所述贯通孔套装于所述限位凸起;所述限位凸起与所述贯通孔之间、所述模块楼板之间的缝隙处填充灌浆料,所述灌浆料固化后形成一体式楼板。
[0009]优选的,适配的所述限位凸起和所述贯通孔设置为多组,且沿相应的所述钢梁的长度方向间隔设置。
[0010]优选的,所述限位凸起为焊接在所述钢梁上的销钉。[0011 ] 优选的,所述销钉呈上大下小的台阶状。
[0012]优选的,所述模块楼板上的所述贯通孔与其预制用的加强筋相互错开。
[0013]优选的,四根所述钢楼柱形成所述模块楼板的安装单元。
[0014]优选的,所述钢楼柱采用方钢制成,与所述钢梁连接处的方钢外周表面固定设置有环状加强筋板;所述环状加强筋板为上下间隔设置的两个,且两个所述环状加强筋板之间设置有加强连接板;所述钢梁通过螺纹紧固件与所述加强连接板固定连接。
[0015]优选的,所述钢楼柱采用方钢制成,与所述钢梁连接处的方钢内腔固定设置有加强筋板;所述加强筋板为上下间隔设置的两个,所述钢梁通过螺纹紧固件与所述钢楼柱的外表面固定连接。
[0016]优选的,所述钢梁采用工字钢制成。
[0017]本发明还提供了一种实现如前所述建筑用模块楼板组装结构的工艺方法,包括以下步骤:
[0018]根据预制的模块楼板设立钢楼柱,形成所述模块楼板的安装单元;
[0019]将钢梁组装于相邻两根所述钢楼柱之间;
[0020]将所述模块楼板搭抵于相应安装单元外周的所述钢梁上,且所述模块楼板边缘处的贯通孔分别套装于相应所述钢梁上的限位凸起;
[0021]填充灌浆料于所述限位凸起与所述贯通孔之间、所述模块楼板之间的缝隙处,以便固化后形成一体式楼板。
[0022](三)有益效果
[0023]本发明的上述技术方案具有如下优点:
[0024]与现有技术相比,本发明采用装配式钢结构与预制的模块楼板有机结合。施工时,首先设立钢楼柱形成确定的模块楼板安装单元,并在每个安装单元的相邻钢楼柱之间组装固定钢梁,以承载预制的模块楼板。本方案中,每根钢梁的上表面均固定设置有竖向延伸的限位凸起,同时模块楼板的边缘开设有与限位凸起适配的贯通孔;当模块楼板的边缘搭抵于钢梁的上表面时,且其上的贯通孔套装于限位凸起;最后,在限位凸起与贯通孔之间、模块楼板之间的缝隙处填充灌浆料。
[0025]如此设置,一方面,主体构件的工厂化程度较高,整个施工工艺过程中可快速装配完成,构件缝隙处填充的灌浆料固化后即可形成一体式楼板为预制建材,大大提高了住宅建筑的施工进度,符合住宅产业化的发展趋势;另外,预制的模块楼板与钢梁之间设置有相适配的贯通孔和限位凸起,可实现模块楼板安装位置的预定位,从而无需调整模块楼板工作位置的相关操作,进一步提升了组装速度。由此,在有效降低施工人员作业强度的同时,获得了较高的整体组装精度,进而为住宅建设质量提供了可靠的保障。
[0026]图1是本发明实施例一所述建筑用模块楼板组装结构的整体结构示意图;
[0027]图2是图1中所示建筑用模块楼板组装结构的工序图;
[0028]图3是图2的I部放大图;
[0029]图4是图3的A-A局部剖视图;
[0030]图5示出了模块楼板上贯通孔与预制用加强筋之间的位置关系示意图;[0031]图6是本发明实施例一中所述钢梁与钢楼柱的连接方式示意图;
[0032]图7是本发明实施例二中所述钢梁与钢楼柱的连接方式示意图。
[0033]图中:钢楼柱1、环状加强筋板11、加强连接板12、加强筋板13、钢梁2、限位凸起21、固定连接板22、角连接板23、模块楼板3、贯通孔31、加强筋32、限位副4、螺纹紧固件5。
[0034]下面结合附图和实施例对本发明的作进一步详细描述。以下实施例用于说明本发明,但不用来限制本发明的范围。
[0035]实施例一
[0036]如图1所示,本发明实施例提供的建筑用模块楼板组装结构主体构成包括:钢楼柱1、钢梁2和预制的模块楼板3,整体设计构思采用了装配式钢结构与预制的模块楼板有机结合。
[0037]其中,四根钢楼柱I形成一块模块楼板3的安装单元,每个安装单元对应一块模块楼板3。应当理解,图1中所示的六个安装单元仅为示例性说明,根据实际设计施工需要及具体尺寸要求,可以进行相应的选择设置。与每个安装单元相应地,两根相邻钢楼柱I之间固定设置有用于承载模块楼板3的钢梁2。
[0038]其中,每根钢梁2的上表面均固定设置有竖向延伸的限位凸起21,且模块楼板3的边缘相应开设有贯通孔31 ;装配完成后的模块楼板3边缘搭抵于钢梁2的上表面,且其上的贯通孔31套装于限位凸起21 ;具体如图2所示,组装过程中,将模块楼板3上的贯通孔31分别与相应钢梁2上的限位凸起21对正,即可完成模块楼板3的预定位。为了清楚表达贯通孔31与限位凸起21之间的适配关系,请一并参见图3所示的局部放大示意图。
[0039]实际施工时,每层楼板的各块模块楼板3均装配到位后,在限位凸起21与贯通孔31之间以及模块楼板3之间的缝隙处均填充灌浆料,待灌浆料固化后形成一体式楼板。
[0040]为了更好地实现模块楼板3的预定位,确保其工作位置的精准程度。如图所示,适配的限位凸起21和贯通孔31可以设置为多组,且沿相应的钢梁3的长度方向间隔设置,通过多重限制建立较高的操作可靠性。也就是说,针对每个安装单元的四个钢梁2及相应模块楼板3的边缘,均设置为多组适配的限位凸起21和贯通孔31 ;这里,优选沿钢梁3的长度方向均布设置,具有较好的工艺性。
[0041]需要说明的是,限位凸起21的结构可以采用不同的形式实现,例如,可以与钢梁2本体浇铸成型,也可以作为独立构件与钢梁2本体焊接固定。本方案中,该限位凸起21为焊接在钢梁2上的销钉,显然,与一体浇铸成型的方式相比,选用销钉焊接固定在钢梁2上的方式制造成本较低。
[0042]另外,作为限位凸起21的销钉可以呈上大下小的台阶状。请一并参见图4所示的销钉装配关系局部剖视图。如此设置,填充于销钉与贯通孔31之间的灌浆料固化后,可形成限制其与销钉脱离的限位副4,由此可进一步确保模块楼板3与钢梁2相关位置关系的稳定性。
[0043]本方案中,模块楼板3的本体结构可以根据实际设计进行选定,只要具有与限位凸起21适配的贯通孔31均要本申请请求保护的范围内。当然,该预制的模块楼板3具有保温、防火及隔音功能为最优配置。为了不影响模块楼板3的自身强度要求,模块楼板3上的贯通孔31与其预制用的加强筋32相互错开,请一并参见图5。显然,在获得与限位凸起21适配结构的同时,不影响预制用加强筋32的布置,填充于销钉与贯通孔31之间的灌浆料固化后,使得贯通孔31的开设对楼板强度不会产生影响;特别是,模块楼板3之间的缝隙处均填充灌浆料,可形成一体的满足更高强度要求的楼板。
[0044]可以理解的是,本实施例所述的建筑用模块楼板组装结构由四根钢楼柱I形成安装单元,实际上,该安装单元也可以由三根或者四根以上的钢楼柱I围合形成,从而适应不同建筑设计风格,只要能够搭抵固定所预制的模块楼板3均可。
[0045]为了有效兼顾钢梁2与钢楼柱I之间的装配便利性及连接强度,可以采用图6所示的连接结构。
[0046]如图6所示,采用方钢制成的钢楼柱1,其与钢梁2连接处的方钢外周表面固定设置有环状加强筋板11 ;该环状加强筋板11为上下间隔设置的两个,且与工字钢制成的钢梁2上下板面大致齐平,以确保整体强度。这里,环状加强筋板11的形状为与钢楼柱I的截面形状适配的矩形,同时便于与钢梁2连接固定。两个环状加强筋板11之间设置有加强连接板12,钢梁2通过螺纹紧固件5与加强连接板12固定连接。
[0047]对于采用工字钢制成的钢梁2来说,其端部需要焊接固定连接板22,由此固定连接板22与加强连接板12相抵且穿装孔对正后,采用螺纹紧固件5实现钢梁2与钢楼柱I的固定连接。如此设置,可靠连接的同时最大限度地保证了钢楼柱I连接处的承载强度。
[0048]前述“方钢”及“工字钢”为以其截面形状定义的型材,在本方案的应用中,“方钢”及“工字钢”可以选用标准外购型材,也可以采用非标准自制设计。
[0049]实施例二
[0050]本实施例所述建筑用模块楼板组装结构的主体构成与实施例一相同,区别在于钢梁2与钢楼柱I之间连接方式的不同。如图7所示,相同构件采用了同样的标记进行标示,以清楚示出两方案之间的区别和联系。
[0051]本方案中,采用方钢制成的钢楼柱1,其与钢梁2连接处的内腔固定设置有加强筋板13 ;图7中未示出一侧钢梁2及相应钢材楼柱I的侧壁,以明确加强筋板13的安装位置。该加强筋板13同样为上下间隔设置的两个,且与工字钢制成的钢梁2上下板面大致齐平,钢梁2通过螺纹紧固件5与钢楼柱I的外表面实现固定连接。
[0052]同样地,对于采用工字钢制成的钢梁2来说,其端部需要焊接固定连接板22,由此固定连接板22与钢楼柱I外表面相抵且穿装孔对正后,采用螺纹紧固件5实现钢梁2与钢楼柱I的固定连接。当然,必要时可以在钢梁2上下板面与固定连接板22之间设置角连接板23,可靠连接的同时最大限度地保证了钢楼柱I连接处的承载强度。
[0053]需要说明的是,实施例一中的环状加强筋板11及实施例二中的加强筋板13的设置数量,不局限于图中所示的上下间隔设置的两个,可根据实际情况进行设定。
[0054]除前述建筑用模块楼板组装结构外,本实施方式还提供一种实现前述建筑用模块楼板组装结构的工艺方法,该方法主要包括以下步骤:
[0055]SI,根据预制的模块楼板3设立钢楼柱1,形成模块楼板3的安装单元。当然,除模块楼板3外,钢楼柱I及钢梁2均可以预先完成构件加工。
[0056]S2,将钢梁2组装于相邻两根钢楼柱I之间;组装方式可以采用螺纹紧固件或者直接焊接连接,相比较而言,采用螺纹紧固件的方式能够更加快速的完成装配。[0057]S3,将模块楼板3搭抵于相应安装单元外周的钢梁2上,且模块楼板3边缘处的贯通孔31分别套装于相应钢梁2上的限位凸起21 ;由此完成模块楼板3的预定位。
[0058]S4,填充灌浆料于限位凸起21与贯通孔31之间、模块楼板3之间的缝隙处,固化后即可形成一体式楼板。
[0059]显然,对于多层住宅建筑而言,逐层依次施工组装即可。
[0060]综上所述,由于本发明所述建筑用模块楼板组装结构的构件工厂化程度较高,整个施工工艺过程中可快速装配完成,构件缝隙处填充的灌浆料固化后即可形成一体式楼板为预制建材,符合住宅产业化的发展趋势;另外,预制的模块楼板与钢梁之间设置有相适配的贯通孔和限位凸起,可实现模块楼板安装位置的预定位,从而无需调整模块楼板工作位置的相关操作,在有效降低施工人员作业强度的同时,获得了较高的整体组装精度,进而为住宅建设质量提供了可靠的保障。
[0061]最后应说明的是:以上实施例仅用以说明本发明的技术方案,而非对其限制;尽管参照前述实施例对本发明进行了详细的说明,本领域的普通技术人员应当理解:其依然可以对前述各实施例所记载的技术方案进行修改,或者对其中部分技术特征进行等同替换;而这些修改或者替换,并不使相应技术方案的本质脱离本发明各实施例技术方案的精神和范围。
一种建筑用模块楼板组装结构及工艺方法
- 专利详情
- 全文pdf
- 权力要求
- 说明书
- 法律状态
查看更多专利详情
下载专利文献
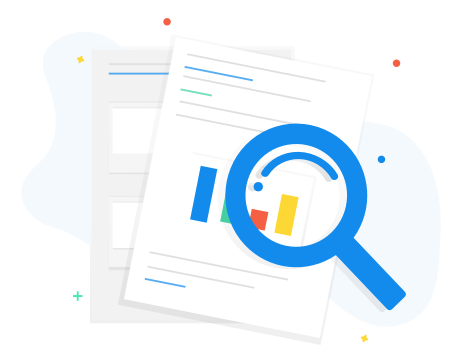
下载专利
同类推荐
-
张宏亮张宏亮张宏亮张宏亮吴立军吴立军吴立军
您可能感兴趣的专利
-
吴立军C·S·马德拉里R·希戴拉, 拉里R 希戴拉杨雪平佘志清佘志清佘志清
专利相关信息
-
佘志清夏莹陈国亮陈国亮陈国亮