一种基于基管外径维持与修正控制制造光纤预制芯棒的装置及其制造光纤预制芯棒方法[0002]光纤预制棒的制造方法主要有四种:外部气相沉积法(0VD)、轴向气相沉积法(VAD)、改进的化学气相沉积法(MCVD,FCVD),以及等离子体化学气相沉积法(PCVD)。它们可单独作为制作光纤预制棒的方法或者两者相互结合或与其它方法相结合制作光纤预制棒。[0003]光纤是将光纤预制棒置于熔炉中加热后拉成一定外径的细丝,再在细丝表面涂覆两层或多层涂料而制成的。[0004]改进的化学气相沉积法(MCVD,FCVD)工艺,又称作管内法,是一种将气相原料化学反应的生成物沉积在一个旋转的玻璃管内部的方法。在这种工艺中,一根玻璃管被装夹于玻璃车床上。气相原料混合物被通入玻璃管中,热源(氢氧火焰或熔炉)沿管子往返移动,使原料在高温下发生化学反应并使沉积在管内壁的反应生成物玻璃化。热源沿管子每往返移动,就生成一层玻璃。制造一根光纤预制棒芯棒需沉积10~250层。芯棒制作中,可以通过改变沉积过程中原料的成分实现渐变或阶跃折射率变化,从而得到设计的折射率剖面。沉积结束后在高温下将玻璃管熔缩成实心光纤预制芯棒。然后将实心芯棒与套管组成预制棒,或者在实心芯棒表面再沉积外包层形成预制棒,最后在拉丝塔上拉丝。[0005]在管内法制造光纤预制棒的工艺中,原料气体SiCl4、GeCl4、P0Cl3、气态氟化物,氧气、氦气、氯气等需要在1500~2050°C高温下才能反应形成化学生成物和玻璃化。由于使用的玻璃管通常壁厚较薄,长时间外部热源的高温加热很容易造成玻璃管径向的变形和塌陷,从而造成玻璃管不圆度以及轴向外径的不均匀性的增大。玻璃管几何特性的恶化将影响玻璃管内的温度分布的轴向和径向均匀性,改变原料气体的反应效率和生成物的沉积效率。最终导致光纤预制棒芯棒几何尺寸以及折射率剖面径向上的不对称性和与轴向上的不均匀性。进而影响预制棒拉制成光纤的光学参数与几何参数控制,例如:光纤模场直径,PMD,芯层不圆度,芯包同心度等。所以在运行中有必要保持玻璃管内有I~5Torr正压以减小和避免玻璃管的变形。[0006]为了保证玻璃管内压力高于外部压力,传统管内法沉积工艺通常在玻璃管末端废渣盒内通入恒定流量的稳定气体,如氮气,但不限于氮气。也有通过调整稳定气体的流量保持玻璃管内外有I~5T0rr正压。这两种方法虽然基本保证了沉积过程中玻璃管圆度,但是没有完全解决玻璃管外径轴向的不均匀性问题。[0007]因此,在改进的化学气相沉积法(MCVD,FCVD)制造光纤预制棒工艺中,如何维持与修正沉积的玻璃管外径,从而间接地使玻璃管径向的不对称性与轴向的不均匀性,以及玻璃管内的加热温度,原料气体的反应效率和生成物的沉积效率得到有效的控制。
[0008]本发明目的是所要解决的技术问题在于克服现有技术存在的不足,提供一种基于基管外径维持与修正外径均匀性控制制造光纤预制芯棒的装置及其制造光纤预制芯棒方法,它不仅基本消除了实心光纤预制棒芯棒不圆度与轴向外径的不均匀性,而且提高原材料的利用效率,降低了成本;还增加了拉制光纤用光纤预制芯棒的有效长度,改善光纤成品合格率。
为了以下叙述方便,将本发明所涉及到的术语解释如下:
预制棒:是由芯层和包层组成的径向折射率分布符合光纤设计要求可拉制成所设计光纤的玻璃棒或组合体;
基管:管状的基底管,符合一定几何要求的掺氟或者纯石英玻璃管;基管又称为石英基管。
[0009]沉积:光纤原材料在一定的环境下发生化学反应生成掺杂的石英玻璃的工艺过程;
熔缩:将沉积后的空心玻璃管在一定的热源下逐渐烧成实心玻璃棒的工艺过程; 芯棒:含有芯层和部分包层的预制件;
套管:满足一定截面积和尺寸均匀性的纯石英玻璃管;
折射率差(Sn):光纤预制棒中某一部分的折射率与纯石英玻璃折射率的差;
正向移动:喷灯从玻璃管进气端向出气端运行。玻璃管抛光,腐蚀,和沉积总是发生在正向移动。
[0010]反向移动:喷灯从玻璃管出气端运行到进气端。在玻璃管抛光,腐蚀,和沉积过程中,玻璃管不需要加热,喷灯高速完成反向移动。
[0011]往返:完成一次正向移动和一次反向移动。
[0012]步骤:一个步骤可以包括一个或多个往返。在一个步骤中,各个往返的原料气体的流量可以不同但是阀门的状态是不变的。
[0013]一种基于基管外径维持与修正控制制造光纤预制芯棒的装置及其制造光纤预制芯棒方法是采取以下技术方案实现:
一种基于基管外径维持与修正控制制造光纤预制芯棒的装置包括原料供给管道、卡盘、旋转接头、石英基管、氢氧焰喷灯、外径测量仪、废渣收集盒和氮气管道。
[0014]原料供给管道与旋转接头相连接,安置于化学气相沉积(MCVD)车床卡盘上的石英基管中,各种所需气体通过原料供给管道输入。在氢氧焰喷灯中喷出的氢氧火焰高温作用下,石英基管中的原料发生反应并沉积在石英基管的内壁上。外径测量仪安装于氢氧焰喷灯的基座上,用于实时测量石英基管的外径。废渣收集盒安置于化学气相沉积(MCVD)车床卡盘上的末端,收集石英基管内未沉积的原料气体。氮气管道连接在废渣收集盒上。
[0015]所述石英基管作为沉积基底管,其长度为500~1500mm,外径为20~40mm,壁厚为I~4mm η[0016]一种基于基管外径维持与修正控制制造光纤预制芯棒的方法包括如下步骤:
I)石英基管装夹:将石英基管4安置于化学气相沉积(MCVD)车床卡盘上,再将石英基管一端与进气尾管对接,另一端与废渣尾管对接。装夹时进气尾管与旋转接头连接,废渣尾管与废渣盒连接。
[0017]2)抛光与内壁腐蚀:将氧气、含氟气体和氯气组成混合气体通入石英基管中,在氢氧焰作用下含氟气体分解并与石英基管内壁发生反应,温度为1700~200(TC,往返I~5次对石英基管进行火焰抛光,腐蚀,同时可以将石英基管外径修正到设定值。在正向移动中外径测量仪随着氢氧焰喷灯一起移动,移动速度为50~200mm/min,每隔3~5mm测量并记录下基管的实际外径数据。将石英基管设定外径值与实际外径数据相比较,计算出两者之间的偏差以及偏差随着往返次数增加的累积误差,根据偏差和记录积累误差计算出相应的实时控制氮气流量设定值为20~60L/min,来实现抛光和腐蚀过程中,实时不间断地减小基管外径测试值和设置值之间的偏差。再在反向移动中计算出正向移动的基管的平均外径。
[0018]3)沉积与玻璃化:根据光纤的设计将沉积过程分为一个或多个步骤。每一个步骤包含往返10~250个往返次数。将SiCl4、GeCl4, POCl3、氧气、氦气、氯气以及含氟气体组成混合气体通入基管,混合气体总量为2000~5000mL/min,在1600~2050°C温度下发生反应,生成物沉积在石英基管内壁上并玻璃化。每一个步骤按照其第一个往返的石英基管平均外径,并基于每次往返基管外径改变设定值为0.01~0.2mm,计算出每次往返需要控制的石英基管外径设定值。同时,在正向移动中外径测量仪随着氢氧焰喷灯一起移动,移动速度为50~200mm/min,每隔3~5mm测量并记录下石英基管实际外径数据。将石英基管设定外径值与实际外径数据相比较,计算出两者之间的偏差以及偏差随着往返次数增加的累积误差,根据偏差和记录积累误差计算出相应的实时控制氮气流量设定为20~60L/min,来实现石英基管沉积过程中,实时不间断地减小石英基管外径测试值和设置值之间的偏差。
[0019]4)熔缩:沉积过程完成后,在石英基管中通入氧气与氯气组成的混合气体,混合气体的流量为1000~4000mL/min,在高温2200~2450°C下进行熔缩处理。为了避免石英基管的不圆度增大,熔缩过程通常需要3~8个往返,同时保证管内有-0.5Torr~0.5Torr压力。为了减小芯层中心由于锗的挥发而形成的中心凹陷,需要在芯棒中心孔径收缩到2~5_,通入氧气与含氟气体组成的混合气体,混合气体的流量为100~200mL/min,对中心孔壁进行腐蚀I~2次,最终在高温2200~2450°C下进行熔缩成实心的光纤预制芯棒。除了最后一次熔缩必须在反向移动中完成,其余的熔缩既可以在正向移动也可以在反向移动完成。
[0020]本发明光纤预制芯棒制作方法中基于基管外径维持与修正控制原理如下:
基于基管外径维持与修正控制,每次基管外表温度1600~2100°C正向移动过程中,实时不间断地根据基管外径实测值和设置值之间的偏差和积累误差给出相应的实时控制氮气流量设定值。控制最大的特点是运用向前反馈控制原理,计算和记录每一个位置的积累误差并用于下一个往返的同一位置,迅速地减小轴向的不均匀性。实时控制氮气流量设定值的计算公式如下:
制作一根芯棒共有步骤:Total_St印当前步骤:S=PHTotalStep 一个步骤共有往返次数(Pass): Total_pass 当前的往返次数是=P=PHTotalpass 当前的喷灯的位置是:Z 当前的外径测试值:OD (Z)
菜单预设值
外径测试点和玻璃管高温变形点之间的距离:L 氮气的预设值N2_set (S,P,Z)
每一个往返外径改变量:dD (S)
外径预设值0D_ recipe (S)
一个步骤中第一个正向移动实测外径平均值:0D_first 上个步骤中最后一个正向移动实测外径平均值:0D_last 外径设置值:根据不同的控制有3种不同方法计算设定值:
A: 0D_set (S, P) =0D_recipe (S).用于以下 2 种情况: i:菜单第一个步骤的第一个往返。
[0021]i1:需要在高温下将外径修正到一个确定的值。
[0022]B: 0D_set (S, P) =0D_last,用于一下 2 种情况 1:只有一个往返的步骤(除第一个步骤)
?:含有多个往返的步骤的第一个往返 C:对于含有多个往返的步骤,从第二个往返开始:
0D_set(P) = 0D_first - (P_l)*dD (S)
外径偏差:err (Z)= 0D_set (P)-OD (Z-L)
上个往返在该位置的积累偏差err_sum(P-l, Z)
比例常数B,积分常数J
总误差:dE(Z) = err (Z) + errsum(P-l, Z)/J
外径变化极限:MaxdD= B * D_set
氮气变化极限:dN2Max
氮气变化量:
如果 dE(Z) >MaxdD, dN2=dN2Max 如果 dE(Z)〈 -MaxdD, dN2=-dN2Max 否则 dN2 = (dE (Z) / MaxdD) * dN2Max 氮气使用值是:
N2_out (S, P, Z) = N2_set (S, P, Z) + dN2
积累误差值:err_Sum (P, Z) =err_Sum(P-l, Z) +err (Z)
本发明的优点在于:
I) 一种基于基管外径维持与修正控制制造光纤预制芯棒的装置与传统的化学气相沉积(MCVD)车床相比,本发明是一种改进化学气相沉积(MCVD)车床,新添加外径测量仪,用于记录喷灯正向移动中石英基管实际外径,为石英基管外径维持与修正控制提供基础数据;2)沉积开始前抛光与内壁腐蚀,降低或甚至消除石英基管内壁的羟基含量;
3)沉积过程中,通过石英基管外径设定值与实际外径数据比较,计算出两者之间的偏差以及偏差随着往返次数增加的累积误差,根据偏差和记录积累误差计算出相应的实时控制氮气流量设定为20~60L/min,来实现石英基管沉积过程中,实时不间断地减小基管外径测试值和设置值之间的偏差;
4)通过基于基管外径维持与修正控制,消除光纤预制芯棒不圆度同时大大改进了光纤预制芯棒轴向几何特性与折射率剖面的特性;
5)芯棒熔缩过程中,当芯棒中心孔径收缩到2~5_时,通入氧气与含氟气体组成的混合气体,混合气体的流量为50~200mL/min,对中心孔壁进行腐蚀I~2次,保证了芯棒最中间部分的质量。
[0023]以下将结合附图对本发明作进一步说明:
图1是传统方法所采用的化学气相沉积(MCVD)设备的示意图。
[0024]图2是本发明方法所采用的改进化学气相沉积(MCVD)设备的示意图。 [0025]图3是本发明基管外径不均性随着沉积次数增加逐次被修正后的对比图。
[0026]图4是本发明基管外径基于氮气控制与外径控制对比图。
[0027]图中:1、原料供给管道,2、旋转接头,3、卡盘,4、石英基管,5、氢氧焰喷灯,6、外径测量仪,7、废渣收集盒,8、氮气管道。
[0028]参照附图1~4,一种基于基管外径维持与修正控制制造光纤预制芯棒的装置包括原料供给管道1、卡盘3、旋转接头2、石英基管4、氢氧焰喷灯5、外径测量仪6、废渣收集盒7和氮气管道8。
[0029]原料供给管道I与旋转接头2相连接,安置于化学气相沉积(MCVD)车床卡盘上的石英基管4中,各种所需气体通过原料供给管道输入。在氢氧焰喷灯5中喷出的氢氧火焰高温作用下,石英基管4中的原料发生反应并沉积在石英基管4的内壁上。外径测量仪6安装于氢氧焰喷灯5的基座上,用于实时测量石英基管4的外径。废渣收集盒7安置于MCVD车床卡盘3上的末端,收集石英基管4内未沉积的原料气体。氮气管道8连接在废渣收集盒7上。
[0030]所述石英基管4作为沉积基底管,其长度为500~1500mm,外径为20~40mm,壁厚为I~4mm。
[0031]下面结合附图详细地描述本发明的基于基管外径维持与修正控制制造光纤预制芯棒的装置及其制造光纤预制芯棒方法:
本发明所涉及的MCVD光纤预制芯棒制造设备示意图如图2所示,其中原料供给管道I与旋转接头2相连接,安置于化学气相沉积(MCVD)车床卡盘3上的石英基管4中,各种所需气体通过原料供给管道I输入。在氢氧焰喷灯5高温作用下,石英基管4中的原料发生反应并沉积在石英基管4前方的内壁上。外径测量仪6安装于氢氧焰喷灯5的基座上,用于实时测量石英基管4的外径。废渣收集盒7安置于化学气相沉积(MCVD)车床卡盘3上的末端,收集石英基管4内未沉积的原料气体和粉末。氮气管道8连接在废渣收集盒7上。
[0032]一种基于基管外径维持与修正控制制造光纤预制芯棒方法包括如下步骤:
I)石英基管装夹:将石英基管4安置于化学气相沉积(MCVD)车床卡盘3上,再将石英基管4 一端与进气尾管对接,另一端与废渣尾管对接。装夹时进气尾管与旋转接头2连接,废渣尾管与废渣盒7连接。
[0033]2)抛光与内壁腐蚀:将氧气、含氟气体和氯气组成混合气体通入管中,在氢氧焰作用下含氟气体分解并与基管4内壁发生反应,温度为1700~200(TC,往返I~5次对石英基管4进行火焰抛光,腐蚀,同时可以将石英基管4外径修正到设定值。在正向移动中外径测量仪6随着氢氧焰喷灯5 —起移动,移动速度为50~200mL/min,每隔3~5mm测量并记录下石英基管4的实际外径数据。将石英基管4设定外径值与实际外径数据相比较,计算出两者之间的偏差以及偏差随着往返次数增加的累积误差,根据偏差和记录积累误差计算出相应的实时控制氮气流量设定值为20~60L/min,来实现抛光和腐蚀过程中,实时不间断地减小石英基管4外径测试值和设置值之间的偏差。在反向移动中计算出正向移动的石英基管4的平均外径。
[0034]3)沉积与玻璃化:根据光纤的设计将沉积过程分为一个或多个步骤。每一个步骤包含往返10~250个往返次数。将SiCl4、GeCl4, POCl3、氧气、氦气、氯气以及含氟气体组成混合气体通入石英基管4,混合气体总量为2000~5000mL/min,在1600~2050°C温度下发生反应,生成物沉积在石英基管4内壁上并玻璃化。每一个步骤按照其第一个往返的石英基管4平均外径,并基于每次往返石英基管4外径改变设定值为0.01~0.2mm,计算出每次往返需要控制的石英基管4外径设定值。同时,在正向移动中外径测量仪6随着氢氧焰喷灯5 —起移动,移动速度为50~200mm/min,每隔3~5mm测量并记录下石英基管4实际外径数据。将石英基管 4设定外径值与实际外径数据相比较,计算出两者之间的偏差以及偏差随着往返次数增加的累积误差,根据偏差和记录积累误差计算出相应的实时控制氮气流量设定为20~60L/min,来实现石英基管4沉积过程中,实时不间断地减小石英基管4外径测试值和设置值之间的偏差。
[0035]4)熔缩:沉积过程完成后,在石英基管4中通入氧气与氯气组成的混合气体,混合气体的流量为1000~4000mL/min,在高温2200~2450°C下进行熔缩处理。为了避免石英基管4的不圆度增大,熔缩过程通常需要3~8个往返,同时保证管内有-0.5Torr~0.5Torr压力。为了减小芯层中心由于锗的挥发而形成的中心凹陷,需要在芯棒中心孔径收缩到2~5_,通入氧气与含氟气体组成的混合气体,混合气体的流量为100~200mL/min,对中心孔壁进行腐蚀I~2次,最终在高温2200~2450°C下进行熔缩成实心的光纤预制芯棒。除了最后一次熔缩必须在反向移动中完成,其余的熔缩既可以在正向移动也可以在反向移动完成。
[0036]实施例:
选用Heraeus F320-08石英基管4作为沉积基底管,外径31.7mm,内径26.3mm,长度1200mm,并将石英基管安置于化学气相沉积(MCVD)车床卡盘3上。
[0037]将氧气、SF6、氯气组成混合气体通入石英基管4中。在正向移动中,在氢氧焰作用下与石英基管4内壁发生反应,温度为1850°C,进行火焰抛光及腐蚀,氢氧焰喷灯5往返I次。同时,外径测量仪6随着氢氧焰喷灯5 —起移动,正向移动速度为145mm/min,外径测量仪6的测量点距尚氢氧焰喷灯5中心45mm。外径设置值31.7mm。每隔3mm测量并记录下石英基管4的实际外径数据,在氢氧焰喷灯5反向移动计算出石英基管4的平均外径31.7mm。
[0038]将SiCl4、GeCl4、P0Cl3、氧气、氦气、氯气与SF6组成混合气体通入石英基管4,混合气体总量为4500mL/min。正向移动中,在1885°C温度下发生反应,石英基管4内壁上沉积并玻璃化形成折射率凹陷层,氢氧焰喷灯5往返10次。在第一个往返中采用上一步骤中计算出的石英基管4平均外径作为外径设置值,在其余的往返中基于第一个往返外径的平均值每次往返石英基管4外径减少0.02mm,计算出每次往返需要控制的石英基管4外径设定值。同时,外径测量仪6随着氢氧焰喷灯5 —起移动,正向移动速度为145mm/min,每隔3mm测量并记录下石英基管4实际外径数据。将石英基管4设定外径值与实际外径数据相比较,计算出两者之差与两者之差随着往返次数增加累积误差,从而给出相应的氮气控制管道8中实时控制氮气流量设定为40~50L/min,来实现在石英基管4折射率凹陷层沉积过程中,通过调节氮气流量实时地修正石英基管4外径使得外径的测量值和设置值之间的差趋近于零。
[0039]将SiCl4、GeCl4、氧气、氦气、氯气与SF6组成混合气体通入石英基管4,混合气体总量为4500mL/min。正向移动中,在1990°C温度下发生反应,石英基管4内壁上沉积并玻璃化形成包层,氢氧焰喷灯5往返13次。在第一个往返中采用上一步骤中氢氧焰喷灯5最后一次往返计算出的石英基管4平均外径作为外径设置值,在其余的往返中基于第一个往返外径的平均值并基于每次往返石英基管4外径减少0.1mm,计算出每次往返需要控制的石英基管4外径设定值。同时,外径测量仪6随着氢氧焰喷灯5 —起移动,正向移动速度为145mm/min,每隔3_测量并记录下石英基管4实际外径数据。将石英基管4设定外径值与实际外径数据相比较,计算出两者之差与两者之差随着往返次数增加累积误差,调节相应的比例与积分参数,从而给出相应的氮气控制管道8中实时控制氮气流量设定为50~60L/min,来实现在石英基管4包层沉积过程中,通过调节氮气流量实时地修正石英基管4外径使得外径的测量值和设置值之间的差趋近于零。
[0040]将SiCl4、GeCl4、氧气、氦气、氯气组成混合气体通入石英基管4,混合气体总量为4500mL/min,在2040°C温度下发生反应,石英基管4内壁上沉积并玻璃化形成芯层,氢氧焰喷灯5往返14次。在第一个往返中采用上一步骤中氢氧焰喷灯5最后一次往返计算出的石英基管4平均外径作为外径设置值,在其余的往返中基于第一个往返外径的平均值,并基于每次往返石英基管4外径减少0.1_,计算出每次往返需要控制的石英基管4外径设定值。同时,外径测量仪6随着氢氧焰喷灯5 —起移动,正向移动速度为145mm/min,每隔3mm测量并记录下石英基管4实际外径数据。将石英基管4设定外径值与实际外径数据相比较,计算出两者之差与两者之差随着往返次数增加累积误差,调节相应的比例与积分参数,从而给出相应的氮气控制管道8中实时控制氮气流量设定为50~60L/min,通过调节氮气流量实时地修正石英基管4外径使得外径的测量值和设置值之间的差趋近于零。
[0041]沉积过程完成后,在石英基管4中通入氧气与氯气组成的混合气体,混合气体流量为2500mL/min,在高温2200~2450°C下进行熔缩处理。为了避免石英基管的不圆度变大,熔缩过程分5次往返,同时控制氮气流量保证管内有O~0.2Torr压力。为了减小芯层中心由于锗的挥发而形成的中心凹陷,需要在预制芯棒中心孔径收缩到2_,通入氧气与SF6组成的混合气体,混合气体流量为150mL/min,对中心孔壁进行腐蚀2次,最终在高温2450 V下进行熔缩成实心的光纤预制芯棒
选用羟基含量小于或等于Ippm的合适尺寸的石英套管与实心的光纤预制芯棒组合成预定要求的光纤预制棒。将光纤预制棒安置在拉丝设备上,在2050°C左右的高温下,将其拉丝成玻璃包层直径为125 μ m,内涂层直径为190 μ m,外涂层直径为245 μ m的光纤。该光纤的部分技术指标如表1所示:
一种基于基管外径维持与修正控制制造光纤预制芯棒的装置及其制造光纤预制芯棒方法
- 专利详情
- 全文pdf
- 权力要求
- 说明书
- 法律状态
查看更多专利详情
下载专利文献
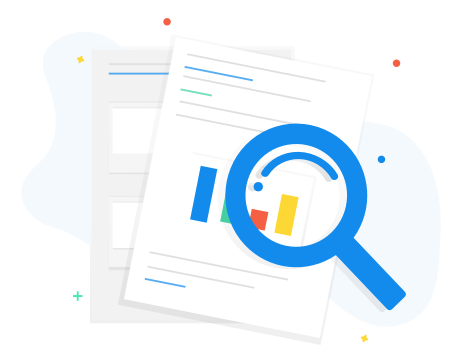
下载专利
同类推荐
-
埃米利奥·鲁伊斯莫拉莱斯埃米利奥·鲁伊斯莫拉莱斯田皓日李金积李金积
您可能感兴趣的专利
-
陈华曲晓青曲晓青李健祥, 王晓光李健祥, 王晓光
专利相关信息
-
刘健康陈国栋, 赵文辉陈国栋, 赵文辉M.卡普蒂孔令学侯银萍侯银萍