专利名称:颗粒硫酸钾及其制造方法本发明涉及颗粒硫酸钾及粒化硫酸钾的方法。更具体地说,它涉及用氢氧化钙之类的中和剂,以一定的量加到已转化的含未反应硫酸的硫酸钾中,继之进行湿法粒化,从而得到颗粒硫酸钾,以及制造颗粒硫酸钾的方法。近年来,为了改进施肥操作,以及适应机械施肥,已普遍采用化肥造粒法。特别是机械施肥近年来已广泛盛行,而且,就硫酸钾来说,也已迫切要求一种具有良好流动性的球状产品。此外,近来已使用格外流行的散装掺和肥料和单一的颗粒肥料。再则,现在各种肥料都已根据适于各自的物理性质和适于市场供应的方法,进行颗粒化。对于例如钾肥之一的硫酸钾,也需要颗粒产品。然而,论及硫酸钾造粒法,在生产和质量方面都存在如下所述的各种问题。例如,在5%(重量)或更多的水分与原料硫酸钾混合的湿法造粒情况下,由于硫酸钾造粒性差,因此难以获得颗粒大小符合要求范围、肥效良好的颗粒产品。这样,在把硫酸钾与水的混合物经滚压机或类似机器加压粒化所得的颗粒硫酸钾用作散装掺和肥料的原料时,在肥料的装卸和运输过程中,散装掺和肥料中的颗粒硫酸钾就会部分粉化。结果产生散装掺和肥料发生分粒而引起肥料组分在各自颗粒大小方面出现偏差的问题。此外,6~12网目的颗粒硫酸钾一般已用作混合的复合肥料或散装掺和肥料的原料,用于此种情况时,由于根据上述加压粒化法得到的颗粒硫酸钾经压缩、研磨和筛分等步骤,所以在其表面有许多突出物(projection),而且压缩强度也较高。但是,容易从研磨过的表面产生损耗。此外,以流动为特征的颗粒产品在装卸和运输时,各个颗粒的易碎表面也会发生粉化。根据常规方法用滚压机加压粒化得到的硫酸钾已经用作掺和肥料的原料。但是,这种产品粉化百分数约10%,比平均粉化百分数为2~3%的其它颗粒肥料要高得多。从而,在散装掺和前,颗粒硫酸钾要先进行再筛分。因此要求得到不需要再筛分的硫酸钾颗粒产品。为了获得上述要求的硫酸钾颗粒产品,本发明的发明者作了广泛研究。结果,我们已发现,若把氢氧化钙一类的中和剂,以一定的量加到已转化的含未反应硫酸的硫酸钾中,继之以湿法粒化的话,就可以解决上述问题。从上所述很显然,本发明的目的是提供一种粉化百分数很低的粒化硫酸钾的方法,使制成的颗粒产品具有良好的流动性,以及提供由上述方法获得的颗粒硫酸钾。下文包括本发明的两个方面,即主要成分(1)和(2),以及作为本发明实施例的成分(3)至(17)(1)一种颗粒硫酸钾,是通过选自一组氢氧化钙、氧化钙、碳酸钙、氢氧化镁、氧化镁、碳酸镁和氨中至少一种组分,以相当于所述未反应硫酸的0.5~2倍当量的量,加到在无水状态下由氯化钾与硫酸反应得到的已转化硫酸钾,以及所含的未反应硫酸中,继之以湿法粒化,藉此得到颗粒硫酸钾。(2)一种粒化硫酸钾的方法,包括选自一组氢氧化钙、氧化钙、碳酸钙、氢氧化镁、氧化镁、碳酸镁和氨中至少一种组分,以相当于所述未反应硫酸的0.5~2倍当量的量,加到在无水状态中由氯化钾与硫酸反应得到的已转化硫酸钾及所含的未反应硫酸中,继之以湿法粒化。(3)一种颗粒状硫酸钾,是通过选自一组粉状的氢氧化钙、氧化钙、氢氧化镁、氧化镁和碳酸镁中至少一种粉状中和剂,以相当于所述未反应硫酸的0.5~2倍当量的量,加到在无水状态中由氯化钾与硫酸反应得到的已转化硫酸钾及所含的未反应硫酸中,继之对生成的混合物进行压模,对制成的模制产品进行研磨,并将形成的粉末进行湿法粒化,藉此得到颗粒硫酸钾。(4)一种制造颗粒硫酸钾的方法,包括选自一组粉状的氢氧化钙、氧化钙、氢氧化镁、氧化镁和碳酸镁中至少一种粉状中和剂,以相当于所述未反应硫酸的0.5~2倍当量的量,加到在无水状态中由氯化钾与硫酸反应得到的已转化硫酸钾及所含的未反应硫酸中,继之对生成的混合物进行压模。对制成的模制产品进行研磨,并将形成的粉末经湿法造粒使之湿法粒化。(5)根据(4)的方法,其中所述的压模是借助滚压机、压块机、压出机或压片机实施的。
(6)根据(4)的方法,其中所述湿法粒化是用盘式造粒机、鼓式造粒机或者压出机实施的。
(7)根据(4)的方法,其中,在所述湿法粒化中,加入水、硫酸钾的水溶液或硫酸钾的含水浆料,从而得到用于粒化的含水量(在未干燥的湿法粒化颗粒中的含水量),以颗粒的重量为基准计,为2~20%(重量)。
(8)根据(4)的方法,其中,通过所述湿法粒化得到的小颗粒,经干燥和分粒,将所得粒度过大的颗粒研磨,并返回所述湿法粒化的装置,而粒度不足的颗粒,无需研磨或者研磨后也返回所述装置,以得到颗粒硫酸钾。
(9)一种颗粒硫酸钾,通过选自一组氢氧化钙、氧化钙和碳酸钙中的至少一种中和剂,以相当于所述未反应硫酸的0.5~2倍当量的量,加到在无水状态中由氯化钾与硫酸反应得到的已转化硫酸钾及所含的未反应硫酸中,以实施湿法中和,继之将已中和的材料干燥,研磨已干燥的材料,使研磨的材料经湿法粒化,藉此得到颗粒硫酸钾。
(10)一种制造颗粒硫酸钾的方法,包括选自一组氢氧化钙、氧化钙和碳酸钙中至少一种中和剂,以相当于所述未反应硫酸的0.5~2倍当量的量,加到在无水状态中由氯化钾与硫酸反应得到的已转化硫酸钾及所含的未反应硫酸中,同时加水实施湿法中和,继之干燥此已转化的材料,研磨已干燥的材料,并且将研碎的材料湿法粒化。
(11)根据(10)的方法,其中,所加水量为所述已转化硫酸钾重量的2~20%(重量)。
(12)根据(10)的方法,其中,经过湿法中和、干燥和研磨过的材料与已湿法中和的材料,以2∶1的比例相混合,并研磨该混合物。
(13)一种颗粒硫酸钾,通过以相当于所述未反应硫酸的0.5~1.2倍当量的氨,加到在无水状态中由氯化钾与硫酸反应得到的已转化硫酸钾及所含的未反应硫酸中,继之以湿法粒化,由此得到颗粒硫酸钾。
(14)一种粒化硫酸钾的方法,包括以相当于所述未反应硫酸的0.5~1.2倍当量的氨,加到在无水状态中由氯化钾与硫酸反应得到的已转化硫酸钾及所含的未反应硫酸中,继之以湿法粒化。
(15)根据(14)的方法,其中加入水或氨水用作所述湿法粒化中粒化用水。
(16)根据(14)的方法,其中,所述湿法粒化是通过盘式干燥器、鼓式干燥器或者压出机实施的(17)根据(14)的方法,其中,由所述湿法粒化得到的材料经干燥后筛分而得到颗粒硫酸钾。其中粒度过大材料被研磨,粒度不足的材料经研磨或不经研磨,并返回至湿式造粒机。
图1至3各表示本发明方法所用设备的流程图。
作为硫酸钾,择优用本发明使用的粉末硫酸钾,较理想的是使用在无水状态中由氯化钾与硫酸反应获得的已转化硫酸钾。然而,当然可使用根据其它方法得到的硫酸钾。
这种原料硫酸钾对其粉状程度,即颗粒大小不作特别限定,如果原料属于通常可用作压片原料或可充分实现湿法中和的原料,那么这种原料可用于本发明。
换言之,就其形式而论,通过20网目的粉末是最佳的(本文的“网目”指的是泰勒标准筛号;这概念适用于以后提到的网目),但是粗颗粒,如大约5网目的颗粒是不合乎需要的。如果使用大约5网目的粗颗粒,则湿法中和便不完全,从而降低本发明的效率。换言之,有这样的趋势,即所制成的湿法中和产品的成粒性变差,所得颗粒产品的得率较低,并且颗粒产品的硬度(破碎时的压力)也较低。
关于用于本发明的中和剂,凡是在0~200℃温度下,能与已转化硫酸钾中所含的未反应硫酸进行反应,且反应后生成的产品(硫酸盐),作为肥料组分对于硫酸钾无不利影响的任何一种中和剂都可使用。这种中和剂的最佳实例,是选自一组钙化合物或镁化合物,如氢氧化钙、氧化钙、碳酸钙、氢氧化镁、氧化镁、碳酸镁和氨中至少一种粉状化合物。
这种粉状化合物所用的量,相当于上述已转化硫酸钾中未反应硫酸含量的0.5~2倍当量,以0.8~1.5倍当量为最佳。
如果上述用量少于0.5倍当量,则中和后,硫酸钾具有高酸性(即低pH值),从而不适用于散装掺和肥料。而假若该量超过两倍当量,则中和后,硫酸钾中肥料组分(K2O)容易低于一定的浓度。
本发明中用作中和剂的氨量,相当于在未中和硫酸钾中所含未反应硫酸量的0.5~1.2倍当量,最好为0.8~1.0倍当量。若该量少于0.5倍当量,则中和后,硫酸钾具有高酸性(即低pH值),从而不适用于散装掺和肥料。而假若该量超过1.2倍当量,则未反应的氨量之大,会造成干燥时的挥发,因此,为要回收它,就使工艺过程复杂化。通常以水溶液或气体形式使用氨。
在上述(4)作为本发明的实施例中,在中和时不使用水。中和剂与已转化硫酸钾的混合工艺过程,以及中和工艺过程都没有特别限制。换言之,例如,已转化的硫酸钾颗粒,用已知的旋转式或搅拌式混合机进行滚动和拌合时,将一定量的粉状中和剂一次全量加入或分次加入,以使这些组分在短时间内(例如30分钟内)能均匀混合。为避免中和剂粘附于混合机器壁上或粘附在一部分已转化的硫酸钾上,可以预先混合全部中和剂和一部分已转化的硫酸钾,由此稀释的中和剂,可以用于上述混合过程中。
此外,关于中和,由于包含在已转化硫酸钾及中和剂内的水分通常是很微量的[例如0.1%(重量)],故在混合同时,并不发生中和作用。但是,可在本发明随后接着进行的一系列步骤,例如压模、研磨和湿法粒化时进行中和,换言之,随着时间的推移,在粒化完成的同时,也基本上完成了中和。
压模法借助于如滚压机、压块机、压出机、压片机之类的压模机实施。压模法的条件不作特别限制,但是,最好选择能使压缩材料被充分压模的条件。
同时,如此获得的压模产品随所采用压模机的不同种类而有以下的不同形状压片板形、碎片形、条形、小片形等。任一种类压模产品都是用研磨机研磨,以得到如下所述的颗粒大小。对所采用研磨机的种类和研磨的条件没有特别加以限制,只要靠它能尽可能达到所述的颗粒大小即可。例如,可采用球磨机、轧制机等。在室温至50℃下连续进行研磨或在室温至50℃下分批研磨5分钟至5小时,最好为10分钟至3小时。
研磨后,压模产品的粉状程度即颗粒大小没有特别限制。一般来说,最好如用于湿法粒化的原料那样的细粒程度。例如,该产品被研磨至约100网目或更小的粒度。
这样得到的已中和的粉状材料,下一步用造粒机进行湿法粒化。在本发明的上述实施例(4)中,由于原料已经实施混合、加压粒化和粉化等步骤,因此可有效地实施直接的湿法粒化步骤。
虽然用于实施例(10)或(15)的湿法中和的水量没有特殊限定,但是足以发生中和这种程度的水量可能是足够的。该量通常为2~20%(重量),最好为4~15%(重量),根据已转化硫酸钾的湿产品重量为基准计算(这种基准也适用于以后水量的计算)。如果该量少于2%(重量),中和就不能充分进行,以致降低本发明的效率。假若水量超过20%(重量)时,需增加用于干燥的能量。结果很不经济。
混合已转化硫酸钾、中和剂和水的方法不作特别限定。例如,以上三种待混合的原料可同时或依次进入敞开式混合器或封闭式混合器,在0~100℃,最好20~80℃下,混合1分钟至1小时,最好5~30分钟。然而,只要不影响本发明的效率,就可以预先只混合已转化的硫酸钾和中和剂,继之将生成的混合物和水一起送入湿法造粒机,以促进中和作用。所加水量对进入湿法造粒机的已中和硫酸钾的重量比可在0.5范围内,或少于0.5。通过采用这种方法,有可能在从原料得出产品的全过程中,由两次干燥步骤中部分省略中和材料的干燥步骤。
对以上混合器无特殊限制,只要能在短时间内使如粉末那样的原料混合即可。例如槽式掺和器,螺条混合器等都可用。
通常用如盘式造粒机、鼓式造粒机等类的滚动造粒机,或压出机实施湿法粒化,但是造粒机并不限于这些。
湿法粒化中进料硫酸钾的加水量无特殊限制,刚刚粒化后的颗粒产品内的含水量(即为小颗粒中的含水量;同样适用于以后的情况)随造粒机种类和所加的硫酸钾颗粒大小而变化,但是,通常为2~20%(重量),最好为4~15%(重量),根据湿产品的重量计(同样适用于以后的情况)。
作为造粒用水,可以用水、硫酸钾水溶液或硫酸钾浆料。只要对硫酸钾粒化作用无损害,则造粒用水中也可含有其它化合物。
用湿式造粒机成粒的硫酸钾借助于干燥器干燥,干燥器种类和干燥方法不作特别规定,但为了减少干燥期间的粉化作用,最好选择温和的条件。
只要本发明的效率不受损害,就可用同样的干燥器对湿法中和的产品和湿法成粒产品进行干燥。必须选择以上的粒化条件,使湿颗粒产品在干燥前可充分发生中和作用。因为根据本发明的方法,在许多情况下,仅靠开头的湿法中和作用,往往不能使中和反应进行到需要和充分的程度,但是,湿法中和后,在使湿法中和产品通过研磨,经受湿法粒化阶段时,就能首次继续进行充分的中和。
如上得到的颗粒产品,用筛选机进行处理,并按颗粒直径筛分为粒度过大产品,产品和粒度不足的产品。粒度过大的产品用研磨机研磨后,返回至湿式造粒机,而粒度不够的产品不经研磨或用研磨机研磨后,返回湿式造粒机。粒度不够的产品是否被研磨,取决于供给湿式造粒机的硫酸钾所有颗粒大小的平衡。
当相同的干燥器用于使用一台干燥器的两步干燥法时,在上述粒度不足的产品中就存在有湿法中和过并已干燥的产品。粒度过大产品的中和通常很充分,因此,有可能代替研磨该产品的步骤,并且将生成的研碎产品送入湿式造粒机,用于研磨湿法中和过并已干燥的产品,以及将所得已研碎产品送入湿式造粒机。
参照图1至3阐述上述方法。
在针对上述实施例(4)的图1中,从管1和管2分别进料的已转化硫酸钾和中和剂,被混合(图中未图示混合器),通过管3储存在料斗A,再送至加压造粒机B,在此,混合物被压模成压片,通过管4输送到研磨机C,压片经研磨后,通过斗式提升机5送到湿式造粒机D,与返回的产品混合在一起(在下文叙述)。
在D中,由管6散射造粒用水,使粉状和细颗粒的硫酸钾转化成为湿颗粒的产品,通过管7将它输入干燥器E。在E内干燥的颗粒产品由斗式提升机8送到筛选机F,颗粒产品在此按颗粒直径筛分成粒度过大产品、产品和粒度不足的产品。
粒度过大的产品经由管9输送到研磨机G进行研磨。
产品从管11取出系统外,粒度过大的产品和粒度不够的产品,各自从管10和12取出,通过流动输送机13返至D。
在针对以上实施例(10)的图2中,由管1和管2分别输入已转化硫酸钾和中和剂,通过管3将它们加入混合器A,通过管16在此散射水,三种原料被混合,结果发生中和反应。已发生中和作用的混合物经由管5与独自由管7输送的湿颗粒产品一起输送到干燥器E(采用上述相同的干燥器)。在E内干燥的硫酸钾通过斗式提升机8输送到筛选机F,硫酸钾颗粒在此按颗粒直径被筛分成粒度过大产品、产品和粒度不够的产品。
粒度过大产品经由管9输送到研磨机G进行研磨。
产品从管11取出系统外。
粒度不够的产品由管15输送到研磨机H进行研磨,或者按照原样,即不经研磨通过管14输送。
与上述产品不同的硫酸钾产品(即粒度过大产品或研磨后粒度不够的产品,以及未研磨的粒度不够的产品)通过流动输送机13和管13′返回至湿式造粒机D,在此,根据硫酸钾的重量为基准计,水以约50%(重量)或更少的量,通过管6散射在硫酸钾上,以实施粒化作用。
经受如上所述的湿法粒化的未干燥颗粒硫酸钾,由管7输送到上述鼓式干燥器E,在此,它与由混合器A输送来的已中和的硫酸钾(注意湿法中和过的产品)一起被干燥。
在针对上述实施例(14)的图3中,预先研磨的已转化硫酸钾,经由管1输送到湿式造粒机D,而返回的产品通过管13′也送到D。另一方面,氨水由管2输送到D。在湿式造粒机D实施粒化。湿颗粒产品通过管7送到干燥器E,生成的干燥颗粒产品经斗式提升器8输送到筛选机F,在此,按颗粒直径筛分成粒度过大产品、产品和粒度不够的产品。粒度过大产品由管9输送到研磨机G,进行研磨。
产品从管11取出系统外。
粒度不够的产品按照原样,通过管14、流动输送机13和管13′,被输送到湿式造粒机D,或者通过管15,一次输送到研磨机H进行研磨。研碎产品通过管12取出,并经过流动输送机13和管13′返回D。
本发明的首要效果是如此获得的颗粒产品,具有高硬度和低百分数的粉化程度,即,从下文所述的实例1和2以及比较实例1至4很显然,根据本发明得到的颗粒产品的硬度(在破碎时的压力),在产品具有颗粒大小6~7网目(泰勒筛)的情况下,等于4~6公斤,粉化百分数为3~5%(重量),就是说,很显然产品在硬度和粉化百分数方面比常规产品优越得多。
本发明的第二效果是生成的颗粒产品具有良好的形状(球形)和良好的流动性,因此,相当适用于机械施肥。
本发明的第三效果是,在湿法粒化中,粉状产品具有良好的成粒性,以及很高的产品得率。即,由于产品的得率高,材料的循环量相对于产品量被减少到使设备的规模较小。
此外,关于本发明的上述实施例(4),从下文所述实例1至3及比较实例1至3可清楚地观察到的现象为通过实施压模,在湿法粒化中粒化用水量并非少量。
虽然机理尚未弄清楚,但是足以推断通过实施压缩,颗粒密度增加而减少了每单位重量的颗粒的表面积(比表面积)。
粒化用水量的减少连同上述设备规模的减小,提供了节能效率。
由实例和比较实例,更详细地阐述本发明。
实例1
将消石灰(纯度氢氧化钙含量为95%(重量))作中和剂,以相应的量加到含2.8%(重量)未反应硫酸的已转化硫酸钾中,继之将这些组分压模,得到压片,用研钵将压片碾碎成通过10网目的粒度,依次将碾碎材料(500克)放入带有直径20厘米研钵的混合研磨机,将碾碎材料研磨30分钟,制备成样品。
用带有盘径45厘米、25转/分的转数及夹角45°的盘式造粒机,使该样品粒化,同时用喷射器将水散射在其上面,继之用调整到110℃温度的电加热干燥器干燥该成粒材料4小时,得到颗粒产品。
粒化用水量和测得的物理参数值如下粒化用水的含量9.0%(重量)。
颗粒产品的硬度4.3公斤。
颗粒产品的粉化百分数4.1%(重量)。
(测量方法)(这种测量方法适用于以下的测量方法)。
硬度用Kiya型硬度计测量。取20粒6~7网目粒度的测量值的平均值。
粉化百分数根据Kumiai研究会的方法测量颗粒大小6~9网目混合的粒状复合肥料。
比较实例1用研钵将含2.8%(重量)未反应硫酸的已转化硫酸钾碾碎成通过10网目的颗粒,继之用实例1同样方法再进一步研磨已碾碎材料,用相应量的消石灰粉末加入研磨材料,充分地摇动装入袋内的混合物,以制备样品。
用实例1的同样方法实施粒化和干燥,得到颗粒产品。
测量值如下粒化用水的含量13.6%(重量)颗粒产品的硬度0.8公斤颗粒产品的粉化百分数65.8%(重量)。
实例2除采用由研磨实例1制得的颗粒产品而获得的样品外,还用实例1的同样方法进行样品的粒化和干燥。
测量值如下粒化用水的含量8.2%(重量)颗粒产品的硬度5.4公斤颗粒产品的粉化百分数3.3%(重量)。
比较实例2除采用由研磨比较实例1得到的颗粒产品而获得的样品外,还用实例1的同样方法进行样品的粒化和干燥。
测量值如下粒化用水的含量10.6%(重量)颗粒产品的硬度2.8公斤颗粒产品的粉化百分数8.1%(重量)实例3将消石灰作中和剂,以相应的量加到含2.7%(重量)未反应硫酸的已转化硫酸钾中,接着,该混合物经加压成粒,用冲击式研磨机研磨所得压片,以制备原料。用带有盘径3.6米、10转/分的转数和夹角50°,并装有一干燥器和一筛选机的盘式造粒机连续进行粒化,得到5~9网目小颗粒产品。
原料量和供给造粒机的返回产品量分别为3.0吨/小时和6.0吨/小时。
筛选机中的量如下粒度过大产品0.6吨/小时(被研磨和返回)产品3.0吨/小时粒度不足产品5.4吨/小时(未经研磨直接返回)粒化用水的含量和产品物理参数的测量值如下粒化用水的含量5.4%(重量)产品硬度(6~7网目)5.9公斤粉化百分数4.7%(重量)。
比较实例3除用冲击式研磨机研磨含2.7%(重量)未反应硫酸的已转化硫酸钾,接着加入相应量的消石灰用作中和剂以得到原料,并用于本实例以外,还用实例2的同样方法进行连续粒化。
原料量和供给造粒机的返回产品量各为2.5吨/小时和8.5吨/小时。
此外,筛选机中的量如下粒度过大的产品0.6吨/小时(已被研磨和返回)产品2.5吨/小时粒度不足的产品7.9%吨/小时(本身直接返回)粒化用水的含量和产品的物理参数测量值如下粒化用水的含量5.8%(重量)产品硬度2.3公斤产品的粉化百分数9.2%(重量)实例4将含2.8%(重量)未反应硫酸的已转化硫酸钾碾碎成通过10网目(泰勒筛)的颗粒,随后把这些颗粒(500克)放入带有直径20厘米研钵的混合研磨机,研磨30分钟,添加相应量的粉状消石灰(氢氧化钙纯度95%(重量)),充分摇动装入袋内的混合物,得到样品(称为样品A)。
将样品放入2升容积的捏合机,接着用喷射器在其上散射水,同时搅拌总计10分钟,再用温度调整到110℃的电热干燥器干燥所得材料4小时,得到中和的产品。
由散射而加入的水量,为样品重量的7%(重量)。
用混合研磨机研磨以上得到的中和产品15分钟,得到粉末(称为样品B)。
将样品B放入带有盘径45厘米、转数25转/分钟和夹角45°的盘式造粒机,继之用喷射器在其上散射水,然后,用调整到110℃的电热干燥器,干燥所得材料4小时。生成颗粒产品的物理参数如下颗粒产品的硬度2.5公斤颗粒产品的粉化百分数8.3%(重量)粒化用水的含量(参考)10.3%(重量)比较实例4除不实施中和外,重复实例4,得到颗粒产品。
颗粒产品的物理参数如下颗粒产品的硬度0.8公斤颗粒产品的粉化百分数65.8%(重量)粒化用水的含量(参考)13.6%(重量)实例5除使用实例4的样品A(150克)和样品B(350克)的混合样品外,重复实例4,得到颗粒产品。
颗粒产品的物理参数如下颗粒产品的硬度2.1公斤颗粒产品的粉化百分数9.8%(重量)粒化用水的含量(参考)11.1%(重量)比较实例5除使用样品A(350克)和样品B(150克)的混合样品外,重复实例4,得到颗粒产品。
颗粒产品的物理参数如下颗粒产品的硬度1.2公斤颗粒产品的粉化百分数49.3%(重量)粒化用水的含量(参考)11.2%(重量)比较实例6除使用氢氧化镁(MgO∶67%(重量))作为中和剂外,重复比较实例5,得到颗粒产品。
颗粒产品的物理参数如下颗粒产品的硬度1.0公斤颗粒产品的粉化百分数13.8%(重量)粒化用水的含量(参考)12.3%(重量)。
比较实例7除使用氢氧化镁作为中和剂外,重复实例4,得到颗粒产品。
颗粒产品的物理参数如下颗粒产品的硬度2.0公斤颗粒产品的粉化百分数13.1%(重量)粒化用水的含量(参考)10.4%(重量)。
实例6用研钵把含2.8%(重量)未反应硫酸的已转化硫酸钾,研磨成通过10网目(泰勒筛)的颗粒,继之把这些颗粒(500克)放入带有直径20厘米研钵的混合研磨机,研磨30分钟,以制备样品。
在带有盘径45厘米,转速25转/分和夹角45°的盘式造粒机中粒化所生成的颗粒,同时用喷射器在颗粒上散射氨水,并且用调整到110℃的电热干燥器干燥所生成的小颗粒4小时,得到颗粒产品。观测和计算颗粒产品中游离硫酸和氨型氮的含量。结果,加入的氨量相当于未反应硫酸量的0.96倍当量。
颗粒产品的物理参数如下颗粒产品的硬度2.1公斤颗粒产品的粉化百分数6.8%(重量)粒化用水的含量(参考)10.1%(重量)。
比较实例8将与实例6相同的已转化硫酸钾颗粒产品,及作为中和剂的消石灰(氢氧化钙纯度∶95%(重量))或氢氧化镁[MgO67%(重量)],各以相应的量混合,接着用与实例6中相同的盘式造粒机粒化该混合物,同时用喷射器在其上散射水。
用实例6的同样方法干燥颗粒产品,其物理参数如下
实例7除使用对实例6制备的颗粒产品进行研磨而得到的样品外,用比较实例8的同样方法实施粒化和干燥。
颗粒产品的物理参数如下颗粒产品的硬度2.8公斤颗粒产品的粉化百分数4.4%(重量)粒化用水的含量(参考)8.9%(重量)。
比较实例9除使用实例6制备的颗粒产品经研磨而得到的样品外,用比较实例8的同样方法实施粒化和干燥。
本发明提供一种粉化百分数很低的硫酸钾造粒法和生产出具有良好流动性的颗粒硫酸钾的方法,以及按上述方法获得的颗粒硫酸钾。本发明方法包括选自一组氢氧化钙、氧化钙、氢氧化镁、氧化镁、碳酸镁和氨中至少一种组分,以相对于所述未反应硫酸量的0.5~2倍当量的量,加到由氯化钾与硫酸在无水状态中反应得到的已转化硫酸钾及所含的未反应硫酸中,继之进行湿法粒化。
颗粒硫酸钾及其制造方法
- 专利详情
- 全文pdf
- 权力要求
- 说明书
- 法律状态
查看更多专利详情
下载专利文献
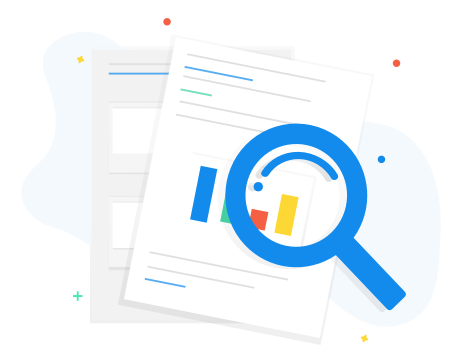
下载专利
同类推荐
-
孙锡德, 张西森孙锡德, 张西森郭洲奖郭洲奖郭洲奖
您可能感兴趣的专利
-
何佩华王新, 王桂英德特勒夫·格拉韦, 莎宾·格利辛德特勒夫·格拉韦, 莎宾·格利辛A·基菲J·H·阿伦斯
专利相关信息
-
J·H·阿伦斯J·H·阿伦斯J·H·阿伦斯J·H·阿伦斯孙瑞艳郭中信, 陈树华蒂莫·皮沃斯基, 贝恩德·威尔维斯