专利名称:晶体活性成分颗粒的制备方法活性成分颗粒的エ艺性能,例如堆密度、润湿性、流动性、稳定性、溶解性特性等,取决于其颗粒大小,且尤其与颗粒大小的分布有夫。为了实现从剂型尽快释放的目的,弱水溶性的活性成分尽可能的被制备成精细的微粒形式。另ー方面,在经由颗粒大小控制释放行为的延迟型中,通常需要一更粗粒度来控制活性成分颗粒在所需时间内的溶解。为了实现优良的エ艺性能,该颗粒大小分布应被尽可能限制在一较窄范围且可重 复产生。又,为了活性成分的加工性或稳定性的缘故,需要制备更粗、但具有限定的且较窄范围颗粒大小分布的活性成分,其中理想的是,该颗粒大小分布通过结晶直接实现,如果可以的话无需如筛分和研磨的后续处理。研磨装置,例如转子/定子装置,可用于微粒晶体颗粒的制备及控制活性成分的颗粒大小的影响。在期刊“有机エ艺的研究与发展”于2007年11月,第699页至第703页刊登的“通过控制高剪切环境下的二次成核结晶过程中产生的精制药颗粒” 一文中,Kamahara等人描述了溶剤-杭溶剂系统中的沉淀结晶,通过分散単元的剪切区中的高度过饱和,用以实现多量的第二次成核以及尽可能细的粒度(平均粒度8-10 μ m)。随着该产物悬浮液经由结晶器及定子/转子循环,如果有恒定剂量的该活性成分溶液,可得到关于浓度和过饱和的非稳定状态。使用3-20kg的批量大小,其在活性成分制备上较为常见,通常需要更大的系统。第WO 03/033097 A2号专利文献还描述了与用于制备尽可能细粒度颗粒的沉淀反应有关的转子/定子研磨装置。溶液和沉淀物经由分离的供料线路被连续提供至该转子/定子单元,并在分散単元的剪切区内实现高成核速率以及因此所造成的晶体生长限制。上述方法适用于获得最细可能的粒度。然而,在大于10 μ m的平均粒径范围内,尤其是大于20 μ m的平均粒径范围内,更粗粒度的目标产物在分散剂的剪切区内具有沉淀反应的问题。此外,通过迭加成核及研磨作用,可制备出具有高比例细粒的双峰粒度。此外,第二次成核速率决定了最終的粒度,但其依赖于大量因素,因此存在有关エ艺监控及重现性的风险。在利用如转子/定子系统的湿磨装置的结晶期间,常见的问题为散热的大量输入,通常増加了热活性成分溶液的热量。由于溶解性通常与温度相关,因此必须再次从该系统有效地移除该热量。这需要相对较大的冷却表面。由于过饱和通常形成于这些表面之上,使此处被逐渐包裹(结垢)。由于外壳的粗颗粒,传输线的阻碍以及传热的逐步恶化,从而导致所需粒度的破坏。系统越小,排热及结垢的问题就越严重。利用所述方法及系统,在尽可能小且低成本系统中,连续于一延长时间周期下維持稳定状态以用于制备所限定的粒度操作是不可能的。第WO 03/091272 Al号专利文献中,描述了通过利用同步湿磨经由结晶而得到的精细初始颗粒的悬浮液的后续处理,凭借通过对应温度曲线重复部分溶解及重结晶,可实现定向且可重复的晶粒粗化。与第WO 03/033907 A2号专利文献所述的方法不同,这里所期望的颗粒大小分布主要不是通过第二次成核来实现的,而是通过一更好控制、逐步晶体生长过程。然而,缺点在于仅可经由额外エ艺步骤并用于エ业規模,以及仅当使用对应较大且成本密集型设备批量操作吋。此外,不利的是在随后回火阶段因为结块而于晶体生长时产生迭加的情形。
本发明的目的在于克服现有技术的所述缺陷并提供一种结晶方法,该结晶方法可产生大部分稳定、较窄范围的且低凝聚的颗粒大小分布,并且还可高效且较优成本地实现更多活性成分数量。此外,本发明的目的在于提供ー种实施该方法的装置。 该目的由用于制备晶体活性成分颗粒的方法达成,在该方法中,活性成分从过饱和溶液于该活性成分颗粒的表面上结晶出来,其中在一第一模块中,对该活性成分的过饱和溶液中的活性成分颗粒的悬浮液进行湿磨,至少部分活性成分颗粒的悬浮液于ー第二模块中被冷却并且同时暴露于超声波,将来自第一模块的活性成分颗粒悬浮液提供至该第二模块,并且在冷却并暴露于超声波之后,该活性成分颗粒悬浮液返回至该第一模块,其中将活性成分溶液及可选择性的抗溶剂提供至该悬浮液,并且移出活性成分颗粒以及液相,其中相对于总液相,该悬浮液的液相中活性成分的相对过饱和度为小于等于90%,并且被移出的活性成分颗粒具有10-500 μ m的平均粒径d50。根据本发明的方法提供具有非常窄范围的颗粒大小分布以及非常少凝聚颗粒的结晶微粒,其大部分与活性成分的理化性质无关,从而实现所得活性成分颗粒的显著エ艺性能。该目的进ー步由用于制备晶体活性成分颗粒的装置达成,该装置具有一第一模块、一第二模块、一供料线路以及一排出线路,该第一模块具有一湿磨装置,在该湿磨装置中,悬浮液中的活性成分颗粒被湿磨,该第二模块具有一冷却装置和一超声源,用于同时冷却并暴露该活性成分悬浮液于超声波,利用该供料线路活性成分溶液和可选择性的抗溶剂可提供至该第一模块或第二模块,利用该排出线路活性成分颗粒及液相可自该第一模块或第二模块移出,其中该第一模块和第二模块相互连接,使得至少部分活性成分颗粒悬浮液可自该第一模块移出,通过该第二模块引导并返回至该第一模块。在本发明的含义内,模块可理解为ー装置或一排列。在本发明的含义内,术语“活性成分”可理解为ー种制药活性成分,如当生物体的身体,特别是哺乳动物,尤其是人类,吸收足够量时可产生生理效应的物质。在根据本发明的方法中,对活性成分的过饱和溶液中活性成分颗粒的悬浮液进行湿磨,从而至少部分减小该等颗粒。该方法开始时发生该悬浮液的生成,例如藉由添加产物粉末或经由ー初始結晶。该方法开始时的颗粒大小对后续颗粒设计几乎没有任何影响。由于所提供的晶体表面处过饱和,该活性成分从该悬浮液中结晶出来,并且活性成分颗粒的研磨设定了颗粒大小的上限。一方面,活性成分溶液及可选择性的抗溶剂被提供至该悬浮液,并且另一方面,活性成分颗粒以及液相被移出。依据溶剂的结晶速率、选择性提供的抗溶剂以及过饱和溶液的浓度,选择供料及移出,从而该过饱和保持足够地低,进而几乎没有成核并且几乎仅在现存的活性成分颗粒的表面上結晶。为了实现较窄范围的颗粒大小分布,根据本发明的方法中的决定因素为过饱和。为了生成细颗粒,本发明特别避免了通过相应高过饱和来成核,如根据现有技术的方法中所寻求的。该过饱和可通过相对过饱和来描述,定义如下相对过饱和=(浓度活性成分-溶解浓度活性成分)/溶解浓度活性成分相对于总液相,以重量百分比计,浓度&!4^为悬浮液的液相中活性成分的浓度。相对于总液相,以重量百分比计,溶解浓度&|4^为饱和点时悬 浮液的液相中活性成分的浓度。饱和点(溶解度)表示液相内活性成分的热力学平衡中最大溶解量。例如,在悬浮液中,液相(过饱和溶液)中含有30Wt.-%溶解的活性成分且其溶解浓度为20被.-%,则具有50%的相对过饱和度。大于溶解浓度(溶解度)存在ー亚稳区,其延伸至过饱和极限,大于该极限在特定溶剂或溶剂混合物中且依据各个エ艺条件,如搅拌条件、冷却速率等每个物质成核。优选的是,溶解的活性成分的浓度保持在该悬浮液的液相中的亚稳区内。在根据本发明的方法中,相对于总液相,该悬浮液的液相中相对过饱和度小于等于90%。这样,活性成分颗粒的存在,尤其是具有新鮮断裂边缘的新鮮研磨的活性成分颗粒的存在可阻止核溶液形成,其将增加非常小的颗粒的部分,从而颗粒大小分布将变宽或变的不均匀。在根据本发明的方法中,相对于总液相,该悬浮液的液相中相对过饱和度优选在5-80%的范围内,特别优选在10-70%的范围内。此外,优选的是,选择该相对过饱和度,使得其位于亚稳区内。此外,优选的是,选择该相对过饱和度,使得无成核发生。用于湿磨的适合装置为分散装置及均质机,特别是转子/定子研磨装置,例如胶体磨或其它搅拌或辊式研磨机。优选使用转子/定子装置,藉由设定转子与定子之间的限定间隙宽度,可非常有效地避免非常小的颗粒的比例。通过暴露于超声波,可防止该过饱和溶液中颗粒的凝聚,并且该冷却面大部分且连续保持不成売。尤其,超声设备应尽可能均匀地发射声场。目的在于保持该冷却面不结晶活性成分。另ー方面,由于直接暴露于超声波,每面具体超声输出不必太高以导致超声材料的移出,并因此引发产物悬浮液的污染。令人惊讶的发现的是,已长久用于清洗槽超声管式谐振器可完全满足上述要求。该功率输入优选位于50至500W/L (每升悬浮液瓦)的范围内。每超声管式谐振器的表面単元的功率输出下降优选位于O. 5至5W/cm2的范围内。利用根据本发明的方法,可重复生产具有ΙΟμπι至500μπι范围内的平均粒径d5Q的颗粒。平均粒径d5Q优选为15-300 μ m,更优选在20-200 μ m且最优选在20-100 μ m。仅通过湿磨装置产生的研磨效果而无供料来初歩确定该下限。d1(l值优选为5-20 μ m,尤其是8-18 μ m0借助湿測量中常见激光衍射确定颗粒大小及颗粒大小分布(粒度分布),这提供了颗粒大小的分布曲线(Malvern System, Mastersizer E,比色皿中进行湿测量)。dx意思是X体积百分数(vol. % )的颗粒具有小于规定值的直径。I μ m的d5(l值为50vol. %的颗粒具有小于Iym(微米)的直径。d5(l值为平均(体积平均)粒径的测量值,且因此也称为平均粒径。15 μ m的d1Q以及50 μ m的d9(l为IOvol. %的颗粒具有小于15 μ m的直径以及90vol. %的颗粒具有小于50 μ m的直径。颗粒大小及颗粒大小分布的湿测量的样品制备凭借超声波发生器(Hielscher,d = 7mm,30%输出),将12. 5mg样品分散于25ml表面活性剂水溶液(O. 1% Tween 80于水中,活性成分饱和并通过0.2 μ m过滤器过滤)持续4分钟。搅拌同时将所得悬浮液逐滴添加至含有过滤的表面活性剂溶液的測量容器中,直至遮光率(浊点)达到10%,并且通过上述激光衍射确定颗粒大小分布。自五个測量值确定一平均值。·根据本发明的方法的优势为形成非常窄范围的颗粒大小分布。此外,获得了基本无凝聚的颗粒。这可一方面通过破坏性研磨及超声过程的同步反向旋转且另一方面通过建设性晶体生长而实现。在粗粒径及凝聚物区域中,上述所有破碎效果(研磨过程及超声)在减小方向上起主要作用,以及在细颗粒区域中,晶体生长在颗粒大小增长方向上起作用。因此,实现了非常窄范围的颗粒大小分布。该颗粒大小分布的宽度(跨距)定义如下跨距=(d90-d10)/d50利用根据本发明的方法,可实现小于等于2. O的跨距值,优选小于等于I. 5的跨距值,且更优选小于等于I. 3的跨距值。在根据本发明的方法中,尤其是通过超声可主要防止凝聚的形成,并且还通过湿磨装置的能量输入使其处于粗粒径范围内。结晶的活性成分颗粒的凝聚度通过凝聚因子(AGF)来描述。其定义为凝聚颗粒的直径与非凝聚颗粒的直径之商。当对比d9(l值时,该方法最能提供凝聚信息。因此,在本发明含义内凝聚因子定义如下凝聚因子=d90 (凝聚颗粒)/d90 (非凝聚颗粒)通过将不同的能量输入至欲测量的样品来确定两个d9(l值。使用高输入能量,现有凝聚物分解,并且下述颗粒大小測量提供非凝聚的颗粒的d9Q。根据上述湿测量的样品制备(利用Hielscher超声波发生器)获得了 d9(l(非凝聚颗粒)。所有凝聚物基本上分解为其初始颗粒。另ー方面,使用低能量输入则凝聚物大部分存在,并且下述颗粒大小測量提供了d9。(凝聚颗粒)。利用Ultra Turrax搅拌器(d = 8mm, from Ika)以最低速度(IOOOOrpm)将12. 5mg样品分散于25ml表面活性剂水溶液(O. I % Tween 80于水中,活性成分饱和并通过0.2 μ m过滤器过滤)持续30秒。搅拌同时将所得悬浮液逐滴添加至含有过滤的表面活性剂溶液的測量容器中,直至遮光率达到10 %,然后通过上述激光衍射确定颗粒大小分布。自五个测量值确定一平均值。该d9CI(Ultra Turrax搅拌器)/d9(l (超声波发生器)的商为凝聚因子的測量值。值接近I表示低凝聚。利用根据本发明的方法,可得到小于等于1.6的颗粒的凝聚因子,优选小于等于I. 3,特别优选I. O至I. 3。另ー方面,利用传统沉淀的产物,该凝聚因子通常在2和3之间。通过根据本发明的方法,特别优选获得具有d5Q = 20-200 μ m, d10 = 8-18 μ m,跨距< I. 3以及AGF ( I. 3的活性成分颗粒。根据本发明的方法的另ー优点为所得产物颗粒的高结晶度。在本发明的含义中,高度结晶或结晶颗粒意思是不含或只含有较少非晶部分而因此为主要结晶的的颗粒。结晶度,如结晶部分,优选大于等于98wt.-%。根据本方法得到的活性成分颗粒的结晶度特别优选为大于等于99. 5wt.-%以及最优选为大于等于99. 9wt.-%。结晶度是通过X射线粉末衍射(XRPD)(装置Siemens D8, fixed sampleposition)来決定。在背景校正之后,对比X射线衍射图形中的整体強度和參考材料的整体強度。该參考材料能为如传统微粒化物或使用已知结晶度和可比粒度根据不同制备方法所得到的产物。因此该结晶度为相对量,其表征对比參考样品的有序度。因此颗粒样品和參考样品的整体反射強度的比例为它们结晶度差的定量表示。根据本发明的方法能被不连续及连续实施。在不连续操作中,不连续地添加活性成分和可选择性的抗溶剂(非溶剤)的溶液,如分批,并且分批移出产物颗粒,尤其是以产物颗粒的悬浮液的形式。优选为连续步骤,其中连续地添加活性成分的溶液和可选择性的抗溶剂并且连续地移出活性成分颗粒以及液相,优选以活性成分颗粒的悬浮液的形式。该悬浮液可返回至第一模块,为此可提供泵或可使用湿磨装置的泵作用,尤其是转子/定子研磨装置的泵作用。第一模块中的体积流量与第二模块中的体积流量的比率优 选大于等于10,特别优选为10至100。利用根据本发明的结晶方法的不连续操作和连续操作,优选的是结晶悬浮液的体积保持实质上恒定,由此能达成特别均匀的粒度分布。“实质上恒定”在本发明中意思是悬浮液的体积变化不大于20vol. %。悬浮液的体积,相对于体积的平均值(100%值),优选为90vol. % -110vol. %,特别优选为 95vol. % -105vol. V0o活性成分的溶液及悬浮液包括ー种或ー种以上活性成分溶剂。合适的溶剂特别为醇、酮和醚,例如甲醇、こ醇、异丙醇、丙酮和こ醚。优选将水用作抗溶剂。抗溶剂在本发明的含义内为ー种液体,在该液体中活性成分是难溶的。溶解度应每公升非溶剂中小于O. 5g活性物质。利用本发明的方法,优选的是该悬浮液由活性成分颗粒和ー种或ー种以上的溶剂以及可选择性的ー种或ー种以上的抗溶剂组成。尤其该悬浮液不应包含额外形成的物质。在根据本发明的用于制备晶体活性成分颗粒的方法的优选实施例中,活性成分从过饱和溶液于该活性成分颗粒的表面上结晶出来,其中在一第一装置中,对该活性成分的过饱和溶液中活性成分颗粒的悬浮液进行湿磨,尤其使用ー转子/定子研磨装置,在活性成分的过饱和溶液中,部分悬浮液从第一装置通过第二装置,于ー第二装置中被冷却并且同时暴露于超声波,尤其使用一超声管式谐振器,然后,该悬浮液部分返回(循环)至该第一装置,以及将活性成分溶液和可选择性的抗溶剂连续地提供至该悬浮液,并且移出活性成分悬浮液,结果相对于总液相,该悬浮液的液相中活性成分的相对过饱和度为小于等于90%,并且被移出的活性成分颗粒具有10-50(^!11的平均粒径(15(|。优选移出的活性成分颗粒(产物颗粒)的跨距小于等于2并且凝聚因子小于等于I. 6。根据本发明方法得到的结晶活性成分颗粒具有10-500 μ m的平均粒径d5(l和非常窄范围的颗粒大小分布以及低凝聚因子,特别是跨距小于等于2. O且凝聚因子小于等于I. 6,其中,如上所述,该跨距定义为(d9CI-d1(l)/d5CI,以及该凝聚因子定义为d9(l(凝聚颗粒)/d90 (非凝聚颗粒)。本发明也涉及的结晶活性成分颗粒作为药剂或治疗的使用。此外,本发明涉及包含根据本发明结晶活性成分颗粒的制药组成物。从设备方面来说,根据本发明的结晶方法可在相对简单且低成本的装置中进行。根据本发明用于制备结晶活性成分颗粒的装置包含第一模块以及第ニ模块,该第一模块具有一湿磨装置,在该湿磨装置中悬浮液中活性成分颗粒被湿磨,该第二模块具有一冷却装置和一超声源,用于同时冷却并暴露该活性成分悬浮液的至少一部分于超声波。该第一模块可为一容器,以下也称为结晶器。该湿磨装置优选为ー转子/定子研磨装置。该湿磨装置可位于该结晶器内,如Ultra Turrax搅拌棒,或优选排列在该结晶器的外部。此外,该湿磨装置可产生ー循环流,使得第一模块形成为循环装置。特别优选的实施例为具有可调间隙宽度的胶体磨用作转子/定子装置。该悬浮液的颗粒大小分布寻求ー目标值,其主要通过胶体磨的转子和定子之间的设定间隙宽度且其次通过旋转速度而确定。根据本发明用于制备结晶活性成分颗粒的装置还包含一供料以及ー出料,其中该供料如一流体线,利用该供料活性成分溶液和可选择性的抗溶剂可提供至该第一模块或第ニ模块,该出料同样可为一流体线,利用该出料活性成分颗粒及液相可自该第一模块或第ニ模块移出。该第一模块和第二模块相互连接,优选通过流体线,使得至少部分活性成分颗粒悬浮液可自该第一模块移出,通过该第二模块并返回至该第一模块。ー泵可提供于此,尤其是在第一和第二模块之间的流体线中。 在优选实施例中,活性成分溶液(供料)经由供料可连续地提供至结晶器,并且产物如活性成分颗粒悬浮液可经由出料被连续地移出。当研磨过程吋,该供料的连续供给对颗粒大小具有负面影响。通过供料与第一模块特别是ー结晶器之间的温度差以及供料率来设定过饱和,从而晶体生长几乎只发生悬浮液的颗粒上。关于颗粒大小的动态平衡,通过研磨过程或超声波,该颗粒合成的静操作点建立在晶体生长与破坏之间。该过饱和还可通过混合抗溶剂来设定。供料的水平特别依赖于所谓的溶解极限与过饱和极限之间无成核形成的亚稳区中晶体生长的最大速率。晶体生长的表面相关速率(kg/m2*h),依赖于相对过饱和以及亚稳区的宽度,依赖于エ艺条件,表现为材料特异方式并可通过熟悉本领域的人员已知的方法来实验性确定。因此,通过转子和定子之间的间隙宽度、颗粒和液相的供料及移出,尤其是以活性成分颗粒悬浮液的形式,可基本上控制该颗粒大小分布。因此,不同于现有技术方法中初始及第二次成核的非常复杂的过程,可更好地控制该过程,并且可以定向及重复方式产生较窄范围的颗粒大小分布。在本发明范围内的研究显示,即使以最大旋转速度并使用最小可能间隙,也几乎不可能利用转子/定子装置研磨粗颗粒悬浮液至小于10 μ m的d5(l值。当使用ー转子/定子研磨装置作为湿磨装置时,通过转子/定子单元的最大可能间隙宽度,对大颗粒超声的分解效应以及过饱和溶液中晶体生长,初步确定500 μ m的活性成分颗粒所获上限。在一优选实施例中,根据本发明的装置还具有ー控制模块,该控制模块控制该活性成分溶液及可选择性的抗溶剂的供给以及该活性成分颗粒及液相的移出,使得相对于总液相,该悬浮液的液相中活性成分的相对过饱和度小于等于90%。该控制模块可设计为硬件及/或软件或传统计算机。尤其优选该控制模块控制该活性成分溶液及可选择性的抗溶剂的供给以及该活性成分颗粒及液相的移出,使得相对于总液相,该悬浮液的液相中活性成分的相对过饱和度在5-80%的范围内,尤其优选在10-70%的范围内。在优选实施例中,活性成分颗粒及液相以活性成分颗粒悬浮液的形式被移出,如自装置移出。在根据本发明的优选实施例中,第一和第二模块为循环装置及/或该超声源为ー超声管式谐振器。还优选的是,第一和第二模块的结合能力不超过20升,特别为10升。第二模块中的悬浮液的冷却以及暴露于超声可以各种方式发生,其包含一循环周期,以下通过图2和图3更为详细地描述。可以理解的是,在不超过本发明的范围内,上述特征以及下述解释可不仅用于给定组合,还可以其它组合或単独使用。
借助所附图式通过实例更详细解释本发明,其中所附图式公开了本发明的基本特征。图I显示了根据本发明的活性成分颗粒的光显微照片。图2和图3显示了根据本发明用于制备结晶活性成分颗粒的装置 的实施例的示意图。
9、超声源10以及流体线11形成本实施例中的第二模块(M2)。活性成分溶液经由供料线路12被连续供至结晶器2,并且以活性成分悬浮液形式的产物经由排出线路13被移出。所示实施例具有ー控制模块SI,该控制模块SI控制活性成分溶液及可选择性的抗溶剂的供给以及活性成分颗粒及液相的移出,使得相对于总液相,悬浮液的液相中该活性成分的相对过饱和度小于等于90%。为此,控制模块SI可连接至供料线路12以及排出线路13,如图2虚线所示。阀门及/或泵可经由该控制模块SI控制。在图2所示的实施例中间接暴露于超声波。从而排除悬浮液与超声材料的污染。利用线圈原理传热是非常有效的且系统延迟较小。然而,随着处理时间变长,包覆层将形成于该线圈内部的部分区域中,可使用少量热溶剂通过定期清洗过程来溶解该等包覆层。图3所示的实施例为根据图2的装置的变型。相同的參考数字代表相同的系统部分。与根据图2的装置不同,该装置不包含螺旋线圈8,但是包含具有水套冷却15的搅拌槽14,用以使用超声源10直接暴露于超声波。将该悬浮液提供至搅拌槽14,接近上填充水平。使用一搅拌器16在底部附近强烈搅拌该悬浮液。另ー方面,在超声源10的区域中该悬浮液缓慢循环。该超声撞击并冷却的悬浮液返回至流体线11底部附近,从而在超声放射槽中填充水平尽可能保持恒定。该悬浮液经由线11传回至结晶器2中。流体线7、超声源
10、流体线11、搅拌槽14、水套冷却15以及搅拌器16形成本实施例的第二模块(M2)。
在该实施例中,除了冷却面之外,接触该系统的所有其它系统部分应具有至少相同于结晶器内温度。因此,为了避免复杂的回火,建议接近室温进行結晶。结晶器壁本身的温度应大致控制在2至8°C,高于结晶温度,从而用以避免由于长期高度过饱和下所导致的成壳现象。为了当连续操作时,尽可能快地建立颗粒大小分布不再变化的过程的固定操作点,可更好地控制该方法,使得颗粒在离开产物流系统之前应尽可能多地通过湿磨装置以及用于冷却和超声搅拌的装置。藉由设定循环流实现结晶器外部具有转子/定子线路,从而相对于整个系统内的滞留时间,该结晶器内颗粒的滞留时间尽可能短。因此,该结晶器内滞留时间应小于5分钟,更好小于I分钟或尤其特别小于20秒。有利地选择该第二模块内的循环,从而热量的 适当移出是可能的,使得该结晶器内与第二模块内的悬浮液温度之间的温度差尽可能小。所述供料以及产品移出流为让整个系统内颗粒的滞留时间足以适当地降低周围母液内的过饱和。利用多种有机活性成分,这可在10至60分钟内发生。因此,在根据本发明的方法中,供料及产物移出流比循环流小10至100倍。当使用根据图3的装置时,因为相对于图2支持了更大的系统,更好的降低了过饱和,从而更多供料的操作是合理可能的。随着产物流移出的悬浮液主要包含结晶期间通过生长而形成的颗粒。过大颗粒及凝聚物主要由研磨和超声波所阻止。因此,除了颗粒大小的损坏之外,也可阻止导致纯度及干燥问题的母液的内含物。为了防止产物颗粒的干燥及后续过滤期间再凝聚,当冲洗滤饼时,一溶解性梯度可形成于该清洗介质中。使用一接近母液溶解度的清洗介质开始并且使用一清洗介质结束的操作是可能的,其中即使在更高温度时该活性成分几乎不溶。“更高温度”指的是任何后续干燥过程高于室温之上。可连续或逐步产生该溶解性梯度。由于在冲洗过程期间溶解度下降太快,必须不惜一切代价避免活性成分分离于母液的沉淀。然后,利用熟悉本领域的人员公知方法干燥该产物。以下示例解释本发明。实例I在根据图2的系统中,将IOOOg黄体酮置于结晶器Rl中并将4000g具有33wt.
水的丙酮/水混合物置于双壁容器R2中。随后,使用ー胶体磨(MK-Modul,MagicLab,IKA)以160001/min且近似4001/h的通过量启动Z2,以及通过双壁容器R2使用每个具有近似601/h的泵P3和P4启动循环周期Zl。将R2于夹套内冷却至_20°C,以及将Rl于夹套内加热至28°C。通过ー冷却套于顶部额外地冷却该谐振器。将容器Rl中的IOOOg黄体酮加至丙酮/水混合物中。使用近似300W驱动浸入容器R2的管式谐振器。30分钟循环之后,于52°C下提供包含具有33%水及16wt. 黄体酮的丙酮/水混合物的料液,并且以61/h经由Pl泵至结晶器Rl。于该结晶器内构建22-25°C的温度,并且于容器R2中构建17-20 V的温度。在供料同吋,使用P2移出产物悬浮液,使Rl和R2的填充水平保持恒定。稳定状态中该结晶器内相对过饱和度为15%。该产物悬浮液通过ー玻璃料被吸入,使用丙酮/水混合物(33%水;50%水)冲洗并且空气干燥。如上所述确定干燥的产物的颗粒大小分布、凝聚因子以及结晶度。确定下述參数
dlO = 12ymd50 = 34 μ md90 = 64 μ m跨距=1.5AGF = I. 3结晶度=100%显微照片见图I·
实例2在根据图I的系统中,使用内部Ultra Turrax搅拌器代替具有循环周期Z2的外部转子/定子装置,以及使用传统US槽代替管式谐振器。将500g具有33wt. 水的丙酮/水混合物置于结晶器Rl中,藉由搅拌补充添加95g黄体酮至容器Rl中的丙酮/水混合物中。然后在Rl中以HOOOrpm启动该Ultra Turrax(25G,lka),使用泵P3启动循环周期Z1,其中该泵P3通过具有3mm内径及IOm总长的PTEE管的冷凝旋管以10L/h泵出悬浮液,该PTEE管的冷凝旋管浸入超声放射容器R2。填充有近似5L、利用额外提供的冷水控制温度在近似5-10°C的超声波浴用作超声放射容器。然后开启该US浴。Rl的温度控制在夹套内28で。30分钟操作之后,于52°C下提供包含具有33%水及16wt. 黄体酮的丙酮/水混合物的料液,并且以I. 21/h经由Pl泵至结晶器R1。于该结晶器内构建24°C至26°C的温度。在供料同时,使用P2移出产物悬浮液,使Rl的填充水平保持恒定。60分钟后自产物流移出悬浮液样品。稳定状态中相对过饱和度为23%。该产物悬浮液通过ー玻璃料被吸入,使用丙酮/水混合物(33%水;50%水)冲洗并且空气干燥。如上所述确定干燥的产物的颗粒大小分布、凝聚因子以及结晶度。确定下述參数dlO =IOymd50 = 26 μ md90 = 45 μ m跨距=1.3AGF = I. I结晶度=100%
本发明涉及一种晶体活性成分颗粒的制备方法,其中活性成分从过饱和溶液于该活性成分颗粒的表面上结晶出来,其中在一第一模块中,在该活性成分的过饱和溶液中对活性成分颗粒的悬浮液进行湿磨,至少部分活性成分颗粒的悬浮液于一第二模块中被冷却并且同时经过超声波处理,在该第二模块内提供有来自该第一模块的该活性成分颗粒悬浮液,并且在冷却并经超声波处理之后,该活性成分颗粒悬浮液再提供回该第一模块内,其中将活性成分溶液及可选择性的抗溶剂添加至该悬浮液,并且提取活性成分颗粒以及液相,其中相对于总液相,该悬浮液的液相中活性成分的相对过饱和度为小于等于90%,并且被提取的活性成分颗粒包括10-500μm的平均粒径d50。
晶体活性成分颗粒的制备方法
- 专利详情
- 全文pdf
- 权力要求
- 说明书
- 法律状态
查看更多专利详情
下载专利文献
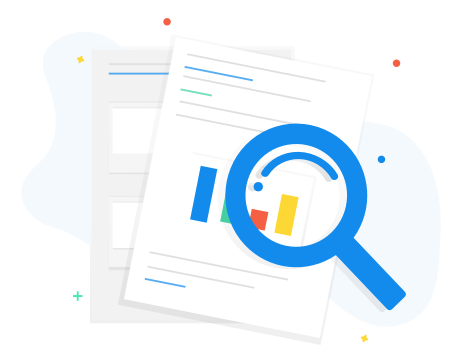
下载专利
同类推荐
-
德特勒夫·格拉韦, 莎宾·格利辛T.B.霍尔贝切宋伟, 许金裕宋伟, 许金裕宋伟, 许金裕
您可能感兴趣的专利
-
孙锡德, 张西森郭洲奖郭洲奖郭洲奖郭洲奖何佩华
专利相关信息
-
亓培实顾喆栋德特勒夫·格拉韦, 莎宾·格利辛德特勒夫·格拉韦, 莎宾·格利辛