专利名称:一种薄膜晶体管液晶显示器及其机械切割制造方法 目前,商用薄膜晶体管液晶显示器面板尺寸的长宽比只有4∶3和16∶9两种标准规格,它也是我们目前市场上所销售的液晶显示器或电视的主要规格。它广泛地被绝大多数场合普遍采用,其屏幕尺寸的宽高比例,是根据人眼对观察图像的宽高比的视图习惯及电视图像扫描制式的规则而决定的,是一种历史形成的传统习惯,而一旦形成了习惯,其局面很难改变,故目前全球几乎所有的TFT-LCD显示器生产企业都只生产这两种长宽比规格的液晶屏。对一些特殊用途的显示领域来说,常常需要用一些特殊长宽比的电子显示器,甚至圆形显示器。如医疗仪器、航空航天导航、雷达指示、极坐标显示、高分辨率的电子地图及航空显示器等,就常需要用长宽比是1∶1的正方形或其它比例的TFT液晶显示器,然而由于上述的几种原因,这种正方形或其它比例的TFT液晶显示器在TFT-LCD面板工厂是无法制造的,耗巨资建造的TFT-LCD面板流水线是为4∶3显示器量身订做的,对1∶1或其它比例的生产工艺过程来说,是不兼容的,如果要进行制造,则必须再次投入巨资对工厂进行一定规模的技术改造,但是投资的规模与正方形TFT液晶显示器的市场容量在现阶段是不相匹配的,难有收回投资的可能,存在很大的投资风险。所以,迄今为止,除了特定的军事用途不考虑投资风险的政府行为外(国防投资),还鲜有TFT-LCD面板工厂愿意通过技术改造来生产这种长宽比为1∶1的正方形或其它比例的TFT液晶显示器,致使市场需求与生产的严重脱节。
本发明的目的针对上述问题,提供一种长宽比为1∶1的正方形或其它任意比例的薄膜晶体管液晶显示器及其机械切割制造方法。它无需投巨资即可直接生产正方形或其它非标比例的TFT液晶显示器,充分利用了目前市场上大量生产的、已商品化的矩形屏幕(4∶3或16∶9)的TFT-LCD,在原来的基础上,通过特有的切割方法来制造出正方形或是其它矩形的TFT-LCD。本发明的技术方案是一种薄膜晶体管液晶显示器,其特征是所述的显示器的长宽比或为N∶3、或为M∶9,其中N的取值范围为0.5~4,M的取值范围为1~16。当N等于3,M等于9,所得的显示器为正方形显示器。显示器的一边为切割边,切割边上封装有封口胶,封口胶中均布有7~9微米粒径的有机支撑隔珠。对上玻璃基板与下玻璃基板切口平齐的切割边(即上切割定位线与下切割定位线重合),其封口胶分别与组成显示器上偏振片、上玻璃基板、液晶材料、下玻璃基板、下偏振片相接触;对上玻璃基板与下玻璃基板切口错层的切割边(即上切割定位线与下切割定位线不重合),其封口胶或与上玻璃基板及液晶材料相接触、或与下玻璃基板及液晶材料相接触。上述的薄膜晶体管液晶显示器可采以以下方法制造一种薄膜晶体管液晶显示器的机械切割制造方法,以长宽比为4∶3或16∶9的、行扫描电极单边引出结构的成品有源矩阵液晶显示器模块为基材采用机械切割法沿宽度方向切割而成,其特征是包括以下步骤a、分解取成品有源矩阵液晶显示器模块进行分解取出其中的面板屏;b、定位将所述的面板屏采用真空负压法固定在有源矩阵液晶显示器专用金刚刀轮切割机的切割平台上,并将金刚刀轮切割机上的刀头对准根据最终成形产品所需的长宽比计算所得的沿宽度方向的切割线位置;
c、划线启动金刚刀轮切割机,使其刀头与工作台面以30~50厘米/秒的相对速度和2~3.5公斤接触压力沿上玻璃基板上的切割线移动,在上玻璃基板上形成上划线,将其翻转后重新定位,以相同的速度和压力使刀头在下玻璃基板上形成下划线;d、裂断将上述两面分别形成有上、下划线的面板屏置于有源液晶显示器专用裂片机上进行一次性折断;e、封堵对上述折断后的面板屏的断裂处用紫外光固化胶进行封口堵胶,并使堵胶后液晶盒的厚度维持在7~9微米之间,同时使胶液渗入液晶层之间的距离L控制在0.3~0.7mm之间,确保封口有效;f、连接成形将完成上述工艺过程的屏重新装入与其相配的模块中,即得本发明的薄膜晶体管液晶显示器。
上述的划线、封堵过程最好在1000级以上及有静电防护的洁净工作间内进行,其中切割裂断到封堵的间隔时间应小于10分钟。
所述的上划线与下划线重合时,折断后的上玻璃基板和下玻璃基板的断口呈平齐状;上划线与下划线不重合时,折断后的上玻璃基板和下玻璃基板的断口呈台阶状。
在所述的固化胶中均布有7~9微米粒径的有机支撑隔珠,以保证裂断、封堵后的液晶盒的厚度。
上述的分解过程必要时还应包括以下步骤a、分离将上述面板屏上的行、列驱动器与面板屏分离;b、揭片在50~100℃温度条件下揭去与面板屏相连接的上、下偏振片,即得所需的可供研磨的面板屏。
必要时,裂断后应对断口处进行清理,去除断裂过程中产生的玻璃粉尘及外溢的液晶,必要时还应在清理结束后采用加压灌晶工艺重新补充液晶。
在上述的连接成形工艺中,必要时还包括上、下偏振片的连接及行、列驱动器的连接。
上、下偏振片的连接也就是常规的贴片过程即待固化胶固化后,重新将上、下偏振片与相应的上、下玻璃基板相贴合;必要时还需进行补线操作,在面板屏的外部通过柔性连接电极将面板屏两端被切断的电极重新压接;在上述裂断结束后,必要时还必须对折断后的双面或单面电路板采用直接焊接补线的方式来恢复电路板的功能,此时元器件容易修复及更换,若电路密度很高而且排列均匀规则,则可用各向异性导电膜热压工艺(ACF)作柔性连接,恢复原来功能。如果TAB封装上连接的是多层电路板,必须通过多种方式才能恢复板的功能,在大多数情况下,比较好的方式是重新制板。
上述步骤中的补线操作可采用各向异性导电膜热压工艺进行;所述的行、列驱动器重新与面板屏相连时也采用各向异性导电膜热压工艺(以下简称ACF)进行。
目前,在有源矩阵液晶显示器(TFT-LCD)制造工艺中,其开关阵列器件主要采用非晶硅薄膜晶体管(a-Si TFT.)和多晶硅薄膜晶体管(poLy-Si TFT)的制造工艺。在多晶硅薄膜晶体管的制造工艺中,又分为低温poLy-Si TFT和高温poLy-Si TFT两种,高温工艺是指整个加工过程中温度高于620℃,a-SiTFT采用的是高温工艺,低温工艺是指整个加工过程中温度低于620℃,对于不同的工艺,采用了不同材料特性的TFT玻璃基板。低温工艺可用普通的平板玻璃做衬底,高温工艺则必须采用石英玻璃为TFT的衬底,而滤色器屏面一般采用由碱石灰或硼硅酸盐成份组成的平板玻璃,这几种玻璃的热膨胀系数、硬度、工作温度和材料组成等理化特性都不一样,对同样的切割方法会造成不同的结果,所以在切割工艺操作中,应根据不同的TFT面板情况区别对待。本发明的制造方式尤其适合于低温多晶硅薄膜晶体管(poLy-Si TFT)制造的有源矩阵液晶显示器的非标规格的再造。
此外,本发明必须首先根据实际应用要求来选择被切割的TFT屏,如屏的有效显示面积、视角范围、对比度、最高分辨率、响应速度等。一般均采用普通商业等级的TFT屏,但是并非所有的屏都能用来切割,必须注意两点一是尽可能采用光电和环境性能指标高的TFT屏,否则即使切割成产品,其实用意义也会大打折扣;二是TFT屏的行扫描电极必须为单边引出结构。
目前TFT-LCD屏内部薄膜晶体管阵列的驱动采用两种方式,一是将驱动集成芯片做在专用的软带上,通过外部柔性连接将屏内的有源矩阵阵列与驱动芯片的输出端相连接,驱动芯片的输入端再通过柔性电路与驱动电路板相连接,电路板上焊装有各类供驱动控制用的元器件,最终在这块板上形成了该TFT屏的接口电路。这称为TAB封装的驱动方式。另外一种是直接将驱动芯片做在TFT玻璃面板内,此时有源矩阵阵列的被驱动端与驱动芯片的输出端已在屏内相连接,然后就可将数量大大减少的驱动输入端通过柔性带的方式从屏上引出,这种直接将驱动芯片做在TFT玻璃屏内的驱动方式称为COG封装的驱动方式。从上可见,无论哪种驱动方式,都必须通过软带进行柔性电路连接。针对屏的切割工艺过程,一般情况下,为了确保屏及电路板的切割、封口、光固化、揭贴偏振片、补线、修复驱动电路板等众多复杂工艺过程的顺利进行,在切割前的准备工序中,应当将TAB或COG封装的柔性带从屏及电路板两边分别剥离去除,剥离时可通过热压机在高温下进行。
当LCD屏、电路板的裂断、补线等工艺完成后,即可再用被揭下的TAB或COG封装的柔性带将屏与驱动电路板重新连接起来。连接方法采用常规TFT-LCD制造中的ACF膜热压工艺,在整个热压工艺过程中,TFT屏、TAB或COG封装的柔性带及电路板三者之间必须精确定位,这可通过常规定位设备来进行。
具体使用时可通过对采用的TFT-LCD现有工艺过程中使用的切割机进行进行适当的改进,在切割刀头上配备专门用于切割TFT面板的刀头,考虑到液晶屏面板的硬度,在选择刀头的切割倾角时应尽量小些,以保证切割强度。
被切割的液晶屏可使用真空负压法固定在切割平台上,为了保证吸气平整度,切割前要去除屏侧面的柔性电路板及屏上、下面的上、下偏振片。
可使用切割设备上的CCD对位装置和TFT屏上原有的定位标记,对TFT玻屏进行精确对位和划线。
由于金刚刀轮机械切割法的合格率与许多因素有关,所以工艺要求就更严些,在工艺过程中要重点掌握以下几点a)切割速度既不能太快也不能太慢,太快会影响划线的均匀性,造成切割异常,太慢会产生切口的微裂纹和局部横向应力,造成裂片过程的困难(显微镜、应力仪可观察、测量到)。具体速度的数值可根据切割压力的大小,玻璃材料的特性及切口长度等因素来综合考虑确定。
b)刀头压力TFT屏的玻璃基板是硬度接近石英材料的高硬性玻璃,其硬度要数倍于普通平板玻璃,所以在工艺过程中,刀头的切割压力就应该调整大一些。
c)裂断时可采用机械裂断法。划线后的面板屏应在TFT面板的专用裂片机上进行,机器必须校平整,压力与速度等各种裂片仪表参数都要根据试验来调整好,裂片机头与屏面划线部分的接触必须是软接触,折断要一次进行,不可反复施压折断。若折断工艺过程正常而仍无法断开或是横向炸裂,则是切割划线的过程中出了问题。
一旦切割划线完成后,应迅速裂断,这段时间不能长,否则会产生裂片质量问题。
本发明的有益效果1、投资低、见效快、无商业风险。
2、与整套TFT-LCD生产工艺相比,切割制造法的工艺技术要简单的多,并且可以根据应用需求切割生产出任意长宽比规格的矩形液晶屏,具有一定条件的LCD模块工厂都可实施。
3、产品可达到很高的性能技术指标(这点非常重要),比如,高分辨率、高对比度、高亮度、高响应速度、宽视角----等,简言之,可以达到将来任何时候最新、最高的光电性能指标。这是因为切割法充分利用了TFT-LCD行业内正在不断进步的技术所制做出的产品,可以充分享受全世界每半年就革命一次的TFT-LCD新技术的成果,也就是可以选择高性能光电指标的TFT-LCD屏来进行切割加工,所以本技术与全球TFT-LCD产业的发展是同步的,这也是方屏切割技术最具有价值的特点之一。而这种特点对采用现有技术制造正方形TFT-LCD的工厂来说,则是无法想像的,可望而不可及。因为产品一经定型投入TFT-LCD生产线进行生产,再想改进光电性能指标就是一件很困难的事。
4、以较小的投入,扩展了有源矩阵液晶显示器的应用范围,为其它行业提供了低价格、高性能的显示器,是一次对有源矩阵液晶显示器的革命性再创造。
5、显示器的长宽比可根据需要任意调整,以满足各类需求,填补了液晶显示器产品规格中的空白。
6、本发明尤其适合于切割低温poly-Si TFT,且具有切割速度快的优点。
图1是本发明的结构示意图之一。
图2图1的B-B向剖视结构示意图。
图3是本发明的结构示意图之二。
图4是图3的C-C向剖视结构示意图。
图5本发明所采用的成品有源矩阵液晶显示器的结构示意图之一。
图6是图5的A-A向剖视结构示意图。
图7本发明所采用的成品有源矩阵液晶显示器的结构示意图之二。
图8是图7的D-D向剖视结构示意图。
图9是本发明的金刚刀轮切割装置及工作原理示意图。
图10是图9的A向视图。
下面结合附图和实施例对本发明作进一步的说明。
实施例一。
如图1、2、5、6、7、8、9、10所示。
一种正方形薄膜晶体管液晶显示器(如图1、2所示),采用如图5、6所示的行、列均为单边电极引出的成品有源矩阵液晶显示器或如图7、8所示的成品有源矩阵液晶显示器切割而成,显示器22的长宽比为1∶1(也可为任意比例),显示器22的一边为平齐形切割边,切割边上封装有封口胶14,封口胶14分别与组成显示器22的上偏振片5、上玻璃基板3、液晶材料7、下玻璃基板4、下偏振片6相接触(如图1、2所示)。
上述正方形(或长宽比为非4∶3及16∶9比例的矩形)薄膜晶体管液晶显示器的机械(金刚刀轮)切割制造方法为a、分解取长宽比为4∶3或16∶9的、行扫描电极单边引出结构(或行为单边,列为双边电极引出)的成品有源矩阵液晶显示器模块并首先将带有行、列驱动器及上、下偏振片的面板屏与成品安装模块分开;b、分离将上述面板屏上的行、列驱动器与面板屏分离;c、揭片在50~100℃温度条件下揭去与面板屏相连接的上、下偏振片,即得所需的可供研磨的面板屏。
具体实施时,上述a、b、c三步也可由成品生产企业进行而省去。
d、定位将上述经过分离、揭片后的面板屏采用真空负压法固定在有源矩阵液晶显示器专用金刚刀轮切割机的切割平台上,并将根据最终成形产品所需的长宽比计算所得的沿宽度方向的切割线位置对准金刚刀轮切割机上的刀头;e、划线启动金刚刀轮切割机,使其刀头与工作台面以30~50厘米/秒相对速度和2~3.5公斤接触压力沿上玻璃基板上的上切割定位线移动,在上玻璃基板上形成上划线,将其翻转后重新定位,以相同的速度和压力使刀头在下玻璃基板上形成下划线;上、下划线应重合。
f、裂断将上述两面划线后的面板屏置于有源液晶显示器专用裂片机上(型号可为TLY-4型高精度玻璃压断机)进行一次性折断;g、清理对上述断裂口及时进行清理,去除断裂过程中产生的玻璃粉尘及外溢的液晶,必要时应采用加压灌晶工艺重新补充液晶;h、封堵对上述断裂处用紫外光固化胶进行封口堵胶,并使堵胶后液晶盒的厚度维持在7~9微米之间,同时使胶液渗入液晶层之间的距离控制在0.3~0.7mm之间,确保封口有效;I、贴片待固化胶固化后,重新将上、下偏振片与相应的上、下玻璃基板相贴合;必要时还需进行补线操作,在面板屏的外部通过柔性连接电极将面板屏两端被切断的电极重新压接;J、连接成型将上述分离下来的行、列驱动器重新与面板屏相连,然后将其装入所需的与切割后面板屏尺寸相配的模块中,即得图1、2所示的正方形薄膜晶体管液晶显示器。
制造其它规格的显示器时,只要调整好划线的位置即可,其它步骤与上述相同。
下面对照附图作具体的说明如图9、10所示,这是金刚刀轮切割机的装置及工作原理示意图。金刚刀轮切割机可采用现有液晶显示器生产工艺中使用的TS-3型自动精密玻璃切割机,刀头30在被切割的TFT-LCD屏22表面移动过程中形成一划线,并沿切割线标定的方向定速均匀移动。图中31为切割机的切割平台,液晶显示器22是通过真空负压的方式固定在平台上的,精确对位是通过液晶显示器22上原有的对位标记来进行。待上、下玻璃基板的表面均沿切割线加工出划线后(图中h示意了切割划线的深度,h与切割压力与刀头的角度有关),再利用现有液晶显示器生产工艺中使用的高精度玻璃压断机进行一次性裂断,裂断机型号为TLY-4型高精度玻璃压断机(北京TSING产)。然后进行清理、封堵、贴片、连接成型。
如图5所示,成品TFT-LCD屏22的行驱动器8和列驱动器9采用的是单边引出方式,这是一种可供切割的前提条件,如果宽边的列驱动器9采用的是双边引出方式,如图7中的那样,也是一种可供切割的屏。但若短边(宽度方向)的行驱动器8也采用双边引出,则为不可切割。图中L-L为切割标记线(切割定位线),其位置可根据需要进行调整,若图中屏的长宽比为4∶3,平移L-L位置就可切割成长宽比为N∶3的任意长宽比的矩形屏,其中0.5<N<4。理论上讲,这种分割是连续的、任意的,但在实际应用中,还必须考虑到屏与列驱动器的分割及匹配等问题,所以这种连续性也是有条件的。现以长宽比为1∶1(在多数情况下使用的比例)为例加以说明。图5、7中2为切割前矩形屏的有效显示区,2a为切割后的有效显示区,必须注意,切割线L-L与2a的边缘不重合,其间应保留3mm的工艺尺寸。
在划线前必须做好充分准备。要去除上玻璃基片3上的上偏振片5和下玻璃基片4上的下偏振片6,使切割媒体30(金刚滚轮刀头)能正常的与上、下玻璃基板3、4接触,同时使LCD屏22被牢固的吸附于切割工作台31上。在大多数情况下,准备工作还包含要分别取下与LCD屏软性相连的行驱动器8和列驱动器9,在这两个驱动器上,都包含了柔性电路带10、多层电路板11、供屏接口用的接插件12及各类微型片状电子元器件,对TAB来说,还集成了许多供驱动用的集成电路芯片13,所以在加工过程中,要加强对8和9的静电防护措施。图6是图2沿A-A剖面线方向的剖面图,图6中在LCD屏22上,上偏振片5和下偏振片6分别贴合在上玻璃基板3和下玻璃基板4的面上,7是夹在上、下玻璃基板3、4之间的液晶材料。在与LCD屏22相连的行驱动器8上有柔性电路带10、多层电路板11、供屏接口用的接插件12和供驱动用的集成电路芯片13。
如图7所示,TFT-LCD屏的行驱动器8是单边引出,而列驱动器9则是双边引出,前面分析过,这种引出方式满足屏被切割的前提条件,也是一种可供切割的屏。在实际工艺过程中,这种形式要比图5的情况复杂些,增加了工艺难度和工作量,对列驱动器9的分离和再次连接也提出了更高要求。图8是图7沿D-D剖面线方向的剖面图。
如图1所示,这是图5或7的矩形屏22经切割后形成的正方形屏23。行、列驱动器8、9是在用封口胶14堵完口后再次用ACF膜热压的方法连接到屏体上去的。在连接过程中,精确对位是必不可少的,如果对位精度不高产生了连接错位,则会引起数据输送的错误、时序的紊乱,造成显示混乱。
在切割后的封盒中,控制盒厚是一个很重要的工艺过程,封口和控制盒厚必须同步进行。LCD屏经裂断后,原先的一侧封边已失去,由于伤口很长,两层屏面间(下基板4的TFT层面与上基板3的滤色器层面),基本已丧失了可靠的力学支撑,在此周围盒厚极易造到破坏。解决方法是利用封口胶14来做附加的封边支撑。在配制胶液时,可在胶中均布7-9微米粒径的有机支撑隔珠,并使隔珠通过胶液渗入屏切口内0.3-0.6mm左右,再通过加压控制盒厚的封口方法,待胶液固化后,就能起到即能保证盒厚又能维持支撑的双重作用。
实施例二。
如图3、4、5、6、7、8、9、10所示。
一种正方形薄膜晶体管液晶显示器(如图3、4),采用如图5、6所示的行、列均为单边电极引出的成品有源矩阵液晶显示器或如图7、8所示的成品有源矩阵液晶显示器切割而成,显示器22的长宽比为1∶1(也可为任意比例),显示器22的一边为台阶形切割边,在台阶形切割边上封装有封口胶14,封口胶14或与上玻璃基板3及液晶材料7相接触、或与下玻璃基板4及液晶材料7相接触,如图3、4。
上述正方形(或长宽比为非4∶3及16∶9比例的矩形)薄膜晶体管液晶显示器的金刚刀轮切割制造方法如实施例一基本相同,所不同之处是上、下划线不重合,裂断后上、下玻璃基板2、3成台阶状,如图3、4所示。
制造其它规格的显示器时,只要调整好划线的位置即可,其它步骤也与实施例一及上述相同。
下面对照附图作具体的说明如一下图9、10是金刚刀轮切割机的装置及工作原理示意图。刀头30在被切割的TFT-LCD屏22表面分别沿切割线L-L及La-La标定的方向定速均匀移动,分两次分别在上玻璃基板3和下玻璃基板4沿切割线L-L及La-La加工出相应的划线(如图5示),沿该划线将上、下玻璃基板3、4折断后即形成错层状台阶,然后进行折断、清理、封堵、贴片、连接成型等工艺。
如图5所示,成品TFT-LCD屏22的行驱动器8和列驱动器9采用的是单边引出方式,这是一种可供切割的前提条件,如果宽边的列驱动器9采用的是双边引出方式,如图7中的那样,也是一种可供切割的屏。但若短边(宽度方向)的行驱动器8也采用双边引出,则为不可切割。图中L-L为切割标记线(切割线),其位置可根据需要进行调整,若图中屏的长宽比为4∶3,平移L-L位置就可切割成长宽比为N∶3的任意长宽比的矩形屏,其中0.5<N<4。理论上讲,这种分割是连续的、任意的,但在实际应用中,还必须考虑到屏与列驱动器的分割及匹配等问题,所以这种连续性也是有条件的。现以长宽比为1∶1(在多数情况下使用的比例)为例加以说明。图5、7中2为切割前矩形屏的有效显示区,2a为切割后的有效显示区,切割线L-L与2a的边缘不重合,其间应保留3mm的工艺尺寸。图中La-La为台阶切割法中在下基板4上所做的切割标记线,它与L-L标记线在切割后就形成了切割台阶,台阶宽度为1.5mm。
在划线前必须做好充分准备。要去除上玻璃基片3上的上偏振片5和下玻璃基片4上的下偏振片6,使切割媒体30(金刚滚轮刀头)能正常的与上、下玻璃基板3、4接触,同时使LCD屏22被牢固的吸附于切割工作台31上。在大多数情况下,准备工作还包含要分别取下与LCD屏软性相连的行驱动器8和列驱动器9,在这两个驱动器上,都包含了柔性电路带10、多层电路板11、供屏接口用的接插件12及各类微型片状电子元器件,对TAB来说,还集成了许多供驱动用的集成电路芯片13,所以在加工过程中,要加强对8和9的静电防护措施。图6是图2沿A-A剖面线方向的剖面图。
如图7所示,TFT-LCD屏的行驱动器8是单边引出,而列驱动器9则是双边引出,前面分析过,这种引出方式满足屏被切割的前提条件,也是一种可供切割的屏。在实际工艺过程中,这种形式要比图5的情况复杂些,增加了工艺难度和工作量,对列驱动器9的分离和再次连接也提出了更高要求。图8是图7沿D-D剖面线方向的剖面图。
如图1所示,这是图5或7的矩形屏22经切割后形成的正方形屏23。行、列驱动器8、9是在用封口胶14堵完口后再次用ACF膜热压的方法连接到屏体上去的。在连接过程中,精确对位是必不可少的,如果对位精度不高产生了连接错位,则会引起数据输送的错误、时序的紊乱,造成显示混乱。
在切割后的封盒中,控制盒厚是一个很重要的工艺过程,封口和控制盒厚必须同步进行。LCD屏经裂断后,原先的一侧封边已失去,由于伤口很长,两层屏面间(下基板4的TFT层面与上基板3的滤色器层面),基本已丧失了可靠的力学支撑,在此周围盒厚极易造到破坏。解决方法是利用封口胶14来做附加的封边支撑。在配制胶液时,可在胶中均布7-9微米粒径的有机支撑隔珠,并使隔珠通过胶液渗入屏切口内0.3-0.6mm左右,再通过加压控制盒厚的封口方法,待胶液固化后,就能起到即能保证盒厚又能维持支撑的双重作用。
如图3所示,这是图5或7中的矩形屏通过台阶式的错位划线法切割后形成的正方形屏23,图中示意了在台阶缺口处采用的柔性补线带15。为了有利于后工序的补线,在绝大多数情况下,切口都应形成台阶的形式,如图5或7中的L-L和La-La两条标记线所示。通常,在形成台阶时,TFT矩阵板(即下玻璃基板4)的尺寸应大于上玻璃基板3,因为被切断的电极引线大部分位于4上(也有不同情形),这样在形成台阶后,被切断的电极引线就可暴露于下玻璃基板4的表面了,可以方便补线。台阶范围控制为1.5mm。工艺顺序上,当封口、偏振片等工序完成后,才可用柔性补线带15将屏内部被断开的电极线条在屏的外部重新连接起来,恢复屏内部电路的原有功能。在此之后,就可以采用ACF热压工艺恢复TAB或COG封装的行、列驱动器8、9的功能,完成全部切割工艺。图4所示是图3沿C-C剖面线方向的剖面图,图中示意了台阶的形成及补线方法。
本发明公开了一种长宽比为1∶1的正方形或其它任意比例的非标尺寸薄膜晶体管液晶显示器及其机械切割制造方法。它无需投巨资即可直接生产正方形或其它非标比例的TFT液晶显示器,充分利用了目前市场上大量生产的、已商品化的矩形屏幕(4∶3或16∶9)的TFT-LCD,在原来的基础上,通过分解、定位、划线、裂断、封堵、连接成形等步骤即可加工出正方形或是其它矩形的TFT-LCD。
一种薄膜晶体管液晶显示器及其机械切割制造方法
- 专利详情
- 全文pdf
- 权力要求
- 说明书
- 法律状态
查看更多专利详情
下载专利文献
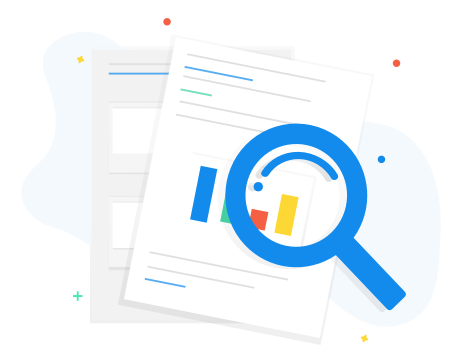
下载专利
同类推荐
-
A·韦恩迪杰克A·韦恩迪杰克许艾莎, 颜伟桂辉辉, 祝仲凯堀光彦浅利大介
您可能感兴趣的专利
-
刘兵D·布洛默特, J·安德烈L·范皮特森, S·阿斯瓦迪L·范皮特森, S·阿斯瓦迪
专利相关信息
-
堀光彦王美龄王美龄王美龄伊夫林·维奥尔伊夫林·维奥尔伊夫林·维奥尔