铁尾矿活性的提高方法、所得的铁尾矿和应用的制作方法【技术领域】,特别涉及一种铁尾矿活性的提高方法,另外,涉及铁尾矿活性提高方法在铁尾矿用做水泥混合材和混凝土掺合料的应用。[0002]铁尾矿是铁选厂在特定经济技术条件下,将原铁矿石破碎、筛分、研磨、分级、再经重选浮选或氰化等选别工艺流程、选出有用铁等金属后的剩余部分,其矿物组成主要为结构稳定的脉石矿物,如石英、长石、辉石、石榴石、角闪石等,几乎没有活性,因此,其在水泥混凝土行业常被用作集料。但随着选矿技术的提高,排出的尾矿由十几年前的中位粒径200um降至现在的40um,已不适合用作混凝土集料。采取合适的手段激发铁尾矿的化学活性,然后将其用作水泥混合材和混凝土掺合料将是铁尾矿在水泥混凝土行业发展的趋势。[0003]目前,在建筑材料行业,矿物活性的提高手段通常有机械粉磨、化学激发、热活化或者三种激发手段中任意两种复合。而铁尾矿活性的提高手段主要为机械粉磨和热活化。如发明专利CN10285001IA《一种利用铁尾矿制备活性粉末混凝土的工艺方法》采用机械粉磨手段来活化铁尾矿,使其作为活性粉末混凝土的活性粉末组分,所制铁尾矿活性粉末混凝土在常温下抗压强度为IOOMPa左右,但有研究表明机械粉磨并不能提高铁尾矿的化学活性,铁尾矿在常温下主要以物理填充效应为主。[0004]发明专 利CN101121579A《一种利用铁尾矿生产混凝土活性掺合料的方法》公开了一种利用热液蚀变反应提高磁铁石英岩型铁尾矿活性的方法,采用该方法生产的混凝土用铁尾矿活性掺合料的活性可达95 %以上,但此种方法中热液蚀变反应需先将物料制成砖坯或球状物,然后放入700~800°C高温窑中煅烧,工艺比较复杂且耗能,难于工业化生产,且其中的蚀变剂主要由硫酸盐类、硝酸盐类、碳酸盐类、氯盐类及氟盐类等14中无机盐配制而成,成分复杂,难以计量,且其饰变剂残留物对会混凝土的耐久性产生不利影响。[0005]发明专利CN103011648A《一种混凝土用改性铁尾矿活性掺合料及其制备方法》公开了一种利用聚羧酸盐减水剂对铁尾矿进行表面改性提高其活性的方法,采用该方法生产的改性铁尾矿活性掺合料的活性与二级粉煤灰相当,该方法生产工艺简单,但聚羧酸盐减水剂在其中只起分散助磨作用,仅有助于铁尾矿细度的提高,并不能激发铁尾矿的化学活性。因此,寻求另一种更广泛、更有效的铁尾矿活性改性方法显得尤为重要。[0006]另外,近年来,随着国内建筑规模的急剧扩大,水泥和混凝土用量也急剧增加,从而导致水泥生产常用的混合材和混凝土制备常用的矿物掺合料如粉煤灰、矿渣和石灰石的缺乏,因此,亟需寻求一种新型、高效的水泥混合材和混凝土用活性矿物掺合料。
[0007]本发明所要解决的技术问题是针对上述现有技术提供一种有效、实用的铁尾矿活性的提高方法,并提供一种铁尾矿活性提高方法在铁尾矿用做水泥混合材和混凝土掺合料的应用。[0008]本发明解决上述技术问题所采用的技术方案是:一种铁尾矿活性的提高方法,包括以下处理步骤:
[0009]I)选取在中高温下可释放具有极强蚀变作用的结构水和CO2的矿物为蚀变物,利用混料机将其与铁尾矿按一定质量比混合均匀;
[0010]2)将混合好的蚀变物和铁尾矿置于高温炉恒温煅烧一段时间,急冷。
[0011]按上述方案,在步骤I)中,蚀变物为煤矸石和石灰石。
[0012]按上述方案,所述煤砰石和石灰石为经过破碎机粉碎,最大粒径小于9.5mm的颗粒。
[0013]按上述方案,在步骤I)中,各原料所占的质量分数分别为铁尾矿60 %~80 %,煤石干石20%~35%和石灰石O~10*%。
[0014]按上述方案,在步骤2)中,恒温温度为500°C~800°C,恒温煅烧时间为0.5h~2h。 [0015]所述的铁尾矿活性的提高方法所得的铁尾矿。
[0016]按上述方案,所述的铁尾矿活性的提高方法所得的铁尾矿用于水泥混合材的应用。
[0017]按上述方案,所述的铁尾矿活性的提高方法所得的铁尾矿用于混凝土掺合料的应用。
[0018]按上述方案,将所述的铁尾矿活性的提高方法所得的铁尾矿和共同煅烧的蚀变物,外加水泥熟料及石膏采用球磨机共同粉磨至比表面积为350m2/kg~450m2/kg。
[0019]按上述方案,将所述的铁尾矿活性的提高方法所得的铁尾矿和共同煅烧的蚀变物,采用球磨机将其磨细至比表面积为400m2/kg~600m2/kg。采用本发明提供的铁尾矿活性提高方法,可大大提高铁尾矿的活性,从而可使其用作水泥混合材和混凝土掺合料。
[0020]本发明的基本原理:煤矸石经煅烧后活性较高,且煅烧过程中可释放一定量极性极强的CO2和化学结合水,释放的这些物质可对周边物质产生强烈的蚀变作用,降低周边物质的稳定状态,同时还可能通过固相反应生成某类介稳矿物,从而使整个体系反应活性得到改善。将其作为铁尾矿的蚀变剂,不仅可起到提高铁尾矿活性的目的,也可通过合理配制生产一种活性较高的水泥用活性混合材和混凝土用活性矿物掺合料。
[0021]本发明的有益效果是:
[0022]I)本发明采用固体废弃物煤矸石为主要蚀变物,不仅可有效提高铁尾矿的活性,而且可降低成本,提高固体废弃物的利用率,具有较高的社会、环境和经济效益。
[0023]2)本发明制得的铁尾矿-煤矸石-石灰石或铁尾矿-煤矸石复合体系具有较高的活性,其28d活性指数可达95%以上,可替代常用混凝土掺合料如矿渣、粉煤灰等日趋短缺的高活性掺合料,为混凝土提供了一种新型高效矿物掺合料,弥补了现有混凝土用掺合料的稀缺和不足。将其用作水泥混合材,所制水泥符合GB175— 2007《通用硅酸盐水泥》中42.5R级复合硅酸盐水泥的指标要求,其中铁尾矿利用率可达30%。实现了铁尾矿的资源化利用和水泥混凝土行业的可持续发展。
[0024]3)本发明铁尾矿活性提高方法简单,只需在500~800°C中低温下煅烧即可,用于水泥生产作混合材时只需与水泥熟料、石膏、其他混合材料一同粉磨,用于混凝土作矿物掺合料时只需单独粉磨至一定细度,工艺简单,有利于工业化生产。
[0025]为了更好的理解本发明,下面结合实施例进一步阐明本发明的内容,内容不仅仅局限于下面的实施例。
[0026]实施例1
[0027]将铁尾矿和煤矸石按照2:1的质量比利用混料机混合均匀,置于高温炉中以IO0C /min的速度升至750°C,恒温lh,急冷,然后采用球磨机将冷却物磨至比表面积为500m2/kg,制得混凝土用活性铁尾矿矿物掺合料,其28d活性指数为95%。在750°C下煤矸石单独煅烧粉磨至相同细度的28d活性指数为91%,铁尾矿为68%,将分别单独煅烧的煤矸石和铁尾矿28d活性指数加权平均可知其加权28d活性指数为76% <共同煅烧的95%,说明将煤矸石对铁尾矿具有极强的蚀变作用。将所制铁尾矿-煤矸石和水泥熟料及少量石膏用球磨机共同粉磨至比表面积为420m2/kg左右,所制复合水泥3d抗折和抗压强度为分别为5.6MPa, 24.5MPa, 28d抗折和抗压强度分别为8.0MPa, 47.6MPa,符合GB175— 2007《通用硅酸盐水泥》中对42.5R级复合硅酸盐水泥的强度指标要求,其中铁尾矿利用率为33%。
[0028]实施例2
[0029]将铁尾矿和煤矸石按照2:1的质量比利用混料机混合均匀,置于高温炉中以IO0C /min的速度升至550°C,恒温2h,急冷,然后采用球磨机将冷却物磨至比表面积为500m2/kg,制得混凝土用活性铁尾矿矿物掺合料,其28d活性指数为86%。在550°C下煤矸石单独煅烧粉磨至相同细度的28d活性指数为88%,铁尾矿为77%,将分别单独煅烧的煤矸石和铁尾矿28d活性指数加权平均可知其加权28d活性指数为81 %〈共同煅烧的86%,说明将煤矸石对铁尾矿具有较强的蚀变作用。将所制铁尾矿-煤矸石和水泥熟料及少量石膏用球磨机共同粉磨至比表面积为420m2/kg左右,所制复合水泥3d抗折和抗压强度为分别为5.3MPa, 22.8MPa, 28d抗折和抗压强度分别为7.8MPa, 45.6MPa,符合GB175— 2007《通用硅酸盐水泥》中对42.5R级复合硅酸盐水泥的强度指标要求,其中铁尾矿利用率为20%。
[0030]实施例3
[0031]将铁尾矿和煤矸石按照3:1的质量比利用混料机混合均匀,置于高温炉中以IO0C /min的速度升至750°C,恒温lh,急冷,然后采用球磨机将冷却物磨至比表面积为500m2/kg,制得混凝土用活性铁尾矿矿物掺合料,其28d活性指数为90%。在750°C下煤矸石单独煅烧粉磨至相同细度的28d活性指数为91%,铁尾矿为68%,将分别单独煅烧的煤矸石和铁尾矿28d活性指数加权平均可知其加权28d活性指数为74%〈共同煅烧的90%,说明将煤矸石对铁尾矿具有极强的蚀变作用。将所制铁尾矿-煤矸石和水泥熟料及少量石膏用球磨机共同粉磨至比表面积为420m2/kg左右,所制复合水泥3d抗折和抗压强度为分别为5.0MPa, 21.4MPa,28d抗折和抗压强度分别为7.5MPa,44.3MPa,符合GB175— 2007《通用硅酸盐水泥》中对42.5R级复合硅酸盐水泥的强度指标要求,其中铁尾矿利用率为37.5%。
[0032]实施例4
[0033] 将铁尾矿,煤矸石和石灰石按照6:3:1的质量比利用混料机混合均匀,置于高温炉中以10°C /min的速度升至550°C,恒温2h,急冷,然后采用球磨机将冷却物磨至比表面积为500m2/kg,制得混凝土用活性铁尾矿矿物掺合料,其28d活性指数为97%。550°C下煤矸石单独煅烧粉磨至相同细度的28d活性指数为88%,铁尾矿为77%,石灰石为60%,将分别单独煅烧的铁尾矿,煤矸石和石灰石28d活性指数加权平均可知其加权28d活性指数为79% <共同煅烧的97%,说明将煤矸石和石灰石对铁尾矿具有极强的蚀变作用。将所制铁尾矿-煤矸石-石灰石和水泥熟料及少量石膏用球磨机共同粉磨至比表面积为420m2/kg左右,所制复合水泥3d抗折和抗压强度为分别为6.0MPa, 26.4MPa,28d抗折和抗压强度分别为8.3MPa,50.0MPa,符合GB175—2007《通用硅酸盐水泥》中对42.5R级复合硅酸盐水泥的强度指标要求,其中铁尾矿利用率为30%。
[0034]实施例5
[0035]将铁尾矿,煤矸石和石灰石按照7:2:1的质量比利用混料机混合均匀,置于高温炉中以10°C /min的速度升至750°C,恒温lh,急冷,然后采用球磨机将冷却物磨至比表面积为500m2/kg,制得混凝土用活性铁尾矿矿物掺合料,其28d活性指数为98%。750°C下煤矸石单独煅烧粉磨至相同细度的28d活性指数为91%,铁尾矿为68%,石灰石为64%,将分别单独煅烧的铁尾矿,煤矸石和石灰石28d活性指数加权平均可知其加权28d活性指数为72%〈共同煅烧的98%,说明煤矸石和石灰石对铁尾矿具有极强的蚀变作用。将所制铁尾矿-煤矸石-石灰石和水泥熟料及少量石膏用球磨机共同粉磨至比表面积为420m2/kg左右,所制复合水泥3d抗折和抗压强度为分别为6.0MPa, 26.4MPa,28d抗折和抗压强度分别为8.3MPa,50.0MPa,符合GB175—2007《通用硅酸盐水泥》中对42.5R级复合硅酸盐水泥的强度指标要求,其中铁尾矿利用率为35%。
铁尾矿活性的提高方法、所得的铁尾矿和应用制作方法
- 专利详情
- 全文pdf
- 权力要求
- 说明书
- 法律状态
查看更多专利详情
下载专利文献
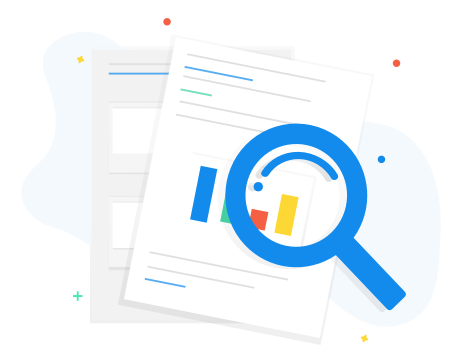
下载专利
同类推荐
-
T.B.霍尔贝切宋伟, 许金裕宋伟, 许金裕宋伟, 许金裕
您可能感兴趣的专利
-
宋伟, 许金裕宋伟, 许金裕宋伟, 许金裕李庆华亓培实
专利相关信息
-
顾喆栋樊传刚, 高元宝宋伟, 许金裕宋伟, 许金裕宋伟, 许金裕