专利名称:涤棉混纺织物与分散、活性染料同浴染色工艺的制作方法涤棉混纺织物系列产品在国际、国内市场非常普遍。其应用范围广、市场份额大; 目前受经济危机的影响,在民用品市场需求呈现出小批量、多色相、交期紧的趋势,绝大多 数印染加工企业均采用溢流染色机染色;其生产成本低、能源消耗少,非常适合小批量、多 品种的民用品的染色;但目前国内部分印染加工企业用分散与活性染料溢流机染涤棉混纺 织物多采用如图1所示的工艺方法对涤棉混纺织物进行染色,其工艺路线为未染色涤棉 混纺织物、分散染料染涤纶纤维(高温高压法)、活性染料染棉纤维(低温常压法)、酸洗 (用98% HAC)、皂洗、水洗、烘干成品布(涤棉染色布)。这种涤棉混纺织物两浴两步法染 色工艺虽然生产成本低、能耗小、人工少,但存在着生产周期偏长、劳动强度大的缺点,严重 制约着生产效率的提高;一缸涤棉混纺织物往往需要5-7个小时才能变为成品,并且由于 需要分开染涤纶纤维和棉纤维,所以工艺复杂,工人劳动强度大、生产效率偏低。
本发明的目的是针对现有分散、活性染料染涤棉混纺织物生产技术中工艺复杂、 生产周期偏长、劳动强度大、生产效率偏低的缺点,提供一种简单、高效、省时省力、更便于 操作和控制的一种涤棉混纺织物与分散、活性染料同浴染色工艺。本发明的技术方案是一种涤棉混纺织物与分散、活性染料同浴染色工艺,主要包 括对涤棉混纺织物与分散、活性染料同浴染色、酸洗、皂洗、水洗、烘干,完成染色涤棉混纺 织物成品布,其特征在于将涤棉混织物投入高温高压溢流染色机内,再将分散、活性染料 混合料液缓缓注入高温高压溢流染色机内;将Na2SO4(元明粉)溶液(浓度根据活性染料 使用量可调)、Na2CO3 (纯碱)溶液(浓度一般为Na2SO4的一半用量)缓慢加入高温高压溢 流染色机内,使涤棉混纺织物在分散、活性染料混合液中进行高温高压同浴染色;再通过酸 洗、皂洗、水洗、烘干,使涤棉染色布充分固色,完成染色全过程。本发明所述涤棉混纺织物与分散、活性染料同浴染色工艺,其工艺步骤为1、小样仿色通过实验室小样仿色,选取分散染料、活性染料;2、配制分散、活性染料染色液(染色液按不同的色相要求来配制);所用分散染料 为耐碱型分散染料;所用活性染料为耐高温双活性基B型染料;3、将涤棉混纺织物进入高温高压溢流染色机内,然后将分散与活性染料混合染色 液注入高温高压溢流染色机内,使涤棉混纺织物浸透分散与活性染料混合染色液;4、再根据所用活性染料的总用量配置Na2S04(元明粉)溶液(浓度根据活性染料 使用量可调)与Na2C03(纯碱)溶液(浓度一般为Na2SO4的一半用量),一般Na2SO4(元明 粉)溶液为活性染料用量的1 1 1. 5,将其分别注入高温高压溢流染色机内;5、升温至110—130°C,升温速率为1. 0-3. 0°C /分钟;保温10—50分钟(可根据 色度深浅选择),使分散、活性染料混合料液染涤棉混纺织物,然后以1. 0-2. 0°C /分钟的速 率缓慢降温至60°C —65°C ;6、再用 98% HAC 0. 35g/L、温度 60°C —65°C酸洗;7、用自制弱碱性洗涤剂(净洗剂SC+液体肥皂比例为2 1 1. 5)0. 5-1. 5g/L、 温度80—9(TC皂洗;8、最后用70-8(TC热水洗一次,烘干,完成整个染色过程。本发明工艺中采用Na2SO4溶液、Na2CO3溶液作为活性染料的促染剂和固色剂;所用 的分散、活性染料、助剂〔如分散剂WA、勻染剂B0F、HAC(98%以上)、Na2SO4、Na2CO3、净洗齐U、 液体肥皂〕等均为市场购买产品。本发明与现有生产技术相比,具有以下优点本发明的涤棉混纺织物与分散、活性 染料同浴染色工艺,改变了现有的两浴两步法的涤棉混纺织物染色工艺,现有的涤棉混纺 织物两浴两步法工艺不但费时费力,而且用水量大;本染色工艺将原来所需的染色时间从 5—7小时缩短为2. 5—3. 5小时,节约时间40—50%左右,降低35% —40%的耗水,并且降 低了耗电、耗汽量和工人的劳动强度,提高了企业生产效。下面结合附图和实施例对本发明作进一步说明图1是现有的涤棉混纺织物两浴两步法染色工艺路示意线图。图2是涤棉混纺织物与分散、活性染料同浴染色工艺路线示意图。
本发明实施例中按染料浓度确定各种助剂的用量;如本处方活性染料总用量为 2. 5% —2. 8%,则选择Na2SO4(元明粉)、Na2CO3(纯碱)用量分别为40g/L和20g/L。
本发明公开了一种涤棉混纺织物分散与活性同浴染色工艺,其特征在于将分散与活性染料同浴料液缓缓注入高温高压溢流机内,再将Na2SO4溶液、Na2CO3溶液缓慢加入高温高压溢流机内,使涤棉混纺织物在分散与活性染料混合料液中进行高温高压同浴染色;再通过酸洗、皂洗,水洗、烘干,使染涤棉混纺织物充分固色,完成所需染色全过程。本发明的染色工艺与涤棉混纺织物两浴两步法染色工艺相比,时间从5-7小时缩短为2.5-3.5小时,降低耗水35%-40%,并且降低了耗电、耗汽量,和工人的劳动强度,提高了企业生产效率。
涤棉混纺织物与分散、活性染料同浴染色工艺制作方法
- 专利详情
- 全文pdf
- 权力要求
- 说明书
- 法律状态
查看更多专利详情
下载专利文献
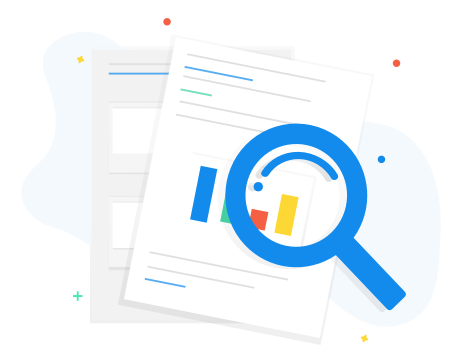
下载专利
同类推荐
-
P·D·瓦林, N·苏里奇宋伟, 许金裕宋伟, 许金裕宋伟, 许金裕曹务波, 董丽宁曹务波, 董丽宁
您可能感兴趣的专利
-
曹务波, 董丽宁曹务波, 董丽宁伦纳达斯·詹森伦纳达斯·詹森唐俊, 葛海涛
专利相关信息
-
A·R·丁格理斯宋伟, 许金裕宋伟, 许金裕宋伟, 许金裕