专利名称:微晶玻璃陶瓷砖及降低微晶玻璃陶瓷砖气泡的生产方法微晶石又名微晶玻璃陶瓷,属于高档装饰材料。现有的微晶类瓷砖,无论是一次烧还是二次烧、高温烧成或是低温烧成的微晶产品,都存在大量的气泡,而且气泡大小也各异,在聚光灯的照射下反光效应十分强烈。这样就严重影响了微晶玻璃类陶瓷的美感,降低了广品的品质。因此,现有技术还有待于改进和发展。
鉴于上述现有技术的不足,本发明的目的在于提供一种微晶玻璃陶瓷砖及降低微晶玻璃陶瓷砖气泡的生产方法,旨在解决目前微晶玻璃陶瓷存在气泡影响产品品质的问题。本发明的技术方案如下: 一种降低微晶玻璃陶瓷砖气泡的生产方法,其中,包括以下步骤: A、施面釉、全抛釉:在干燥好的生坯上施面釉后再施一层全抛釉; B、施微晶干粒,所述微晶干粒的过筛目数为10-80目,按照重量百分比计所述微晶干粒包括:10-30 目 40-50% ;30-60 目 30-40% ;60-80 目 15-25% ;
C、喷施固定剂;
D、一次烧成,烧成温度为1500±10°C,烧制时间为60-80分钟。所述的降低微晶玻璃陶瓷砖气泡的生产方法,其中,所述面釉施用量为800*800mm的生坯上施650-750g,比重为1.75-1.85,所述全抛釉的施用量为800*800mm的生坯上施150-250g,比重为 1.3-1.4。所述的降低微晶玻璃陶瓷砖气泡的生产方法,其中,所述微晶干粒的施用量为800*800mm的生坯上施2500-3500 g,用于制备所述微晶干粒的原料,按重量百分比计包括:
石英粉 18_27% ;
氧化铝 15-20% ;
白云石 18-25%;
硼酸5-10% ;
锂瓷石 28-38% ;钟长石 5-10 %。所述的降低微晶玻璃陶瓷砖气泡的生产方法,其中,所述固定剂为甲基水;所述甲基水为质量浓度为3-7%的羧甲基纤维素钠水溶液。所述的降低微晶玻璃陶瓷砖气泡的生产方法,其中,所述降低微晶玻璃陶瓷砖气泡的生产方法还包括以下步骤:
S5、放进窑炉进行烧制;
其中,窑炉温度稳定曲线的面温为980°C,1000 V,1025 V,1030 V,1050 V,1070 V,1095°C, 1120°C, 1145°C, 1160°C, 1170°C, 1205°C, 1205°C, 1205°C, 1205°C, 1160°C, IOOO0C ;底温为 910 °C,980 °C, 1025 °C, 1030 °C, 1060 °C, 1080 °C, 1100 °C, 1130 °C, 1160 V,118(TC,119(TC,1195 ,1195 ,1195 ,1195 ,119(TC,113(TC。一种利用如上所述的降低微晶玻璃陶瓷砖气泡的生产方法生产的微晶玻璃陶瓷砖,其中,所述微晶玻璃陶瓷砖包括砖坯、面釉层、全抛釉层和微晶干粒层,所述面釉层、全抛釉层和微晶干粒层从里到外依次设置于砖坯表面。有益效果:本发明提供一种微晶玻璃陶瓷砖及降低微晶玻璃陶瓷砖气泡的生产方法,通过针对微晶干粒成分、干粒过筛目数搭配及烧制温度的设置实现了降低微晶玻璃陶瓷砖气泡的目的,使得釉面的气泡不仅大大降低而且气泡体积也极微小,微晶层透明度高,釉面显得清澈干净。产品品质得以进一步提升。
图1为本发明的 降低微晶玻璃陶瓷砖气泡的生产方法流程图。图2为本发明的微晶玻璃陶瓷砖的结构示意图。
S1、施面釉、全抛釉:在干燥好的生坯上施面釉后再施一层全抛釉;其中,所述面釉施
用量为800*800mm的生坯上施650_750g,比重为1075-1.85,流速大约为25秒。所述全抛釉的施用量为800*800mm的生坯上150-250 g,比重为1.3-1.4。所述全抛釉优选为采用排气较好的全抛釉,是在高温下粘度较小且始熔温度较低的全抛釉,具有此种性质全抛釉为市面上购买得到。这样用此种全抛釉压住面釉和生坯能够有效使生坯和面釉中的气体排出。S2、施微晶干粒;所述微晶干粒的过筛目数为10-80目,按照重量百分比计所述微晶干粒包括:
10-30 目 40-50% ;
30-60 目 30-40% ;
60-80 目 15-25% ;
为了使生坯和釉层排气良好,选择微晶干粒的过筛目数非常重要,干粒过粗,使烧成温度过提高,导致色釉花釉氧化分解,釉粘度较高排气不完全而存在较多的气泡而且气泡较大。微晶干粒过细烧成温度偏低,粘度过低釉过早熔融将气泡封死在釉层中,而导致有较多的气泡。因此干粒过筛目数的大小对排气有较大的影响。本发明采用微晶干粒大小过筛目数搭配混用,选取过筛目数在10目到80目之间的微晶干粒,具体过筛目数搭配为10-30目占40-50%,30-60目占30-40%,60-80目占15-25%,较佳的微晶干粒过筛目数搭配是10 30目占45%,30 60目占35%,60 80目占20%。这样大小过筛目数搭配用可以填充干粒之间的空隙,将空隙中的气体赶出,同时这样对温度的烧成范围也加大了,更有利于排气。所述微晶干粒的施用量为800*800mm的生坯上施2500_3500g,用于制备所述微晶干粒的原料,按重量百分比计包括:
石英粉 18_27% ;
氧化铝 15-20% ;
白云石 18-25%;
硼酸5-10% ;
锂瓷石 28-38% ;
钟长石 5-10 %。微晶干粒料的化学组成是影响排气的其中一个关键因素。一个排气较好的微晶干粒料必须要有一个合理的化学组成,组成中高低温组分必须搭配合理。为了使排气更充分一般将微晶干粒料制成熔块。配微晶干粒原料中,高温分解的物质少,可以减少釉泡和针孔,如果微晶干粒熔融后,高温分解的物料还未分解完全,则已形成釉泡和针孔。在微晶干粒料组成上宜配成始融温度较高,且一旦熔融,高温下粘度又较高的微晶料,这样可以使造气物质在熔融前分解完全 ,气体充分排出。微晶干粒熔融后,由于微晶的粘度高,分解的少量气体不易聚集,而埋在釉层中,这样就可以获得光滑的釉面。也可以选择始熔点较高,微晶熔体高温粘度又较小,流动性较好的微晶,使少量气体逸出微晶面产生的气孔,被熔体流动熔平而得到光滑的釉面。本发明根据这一原理采用始熔点高,高温粘度小的微晶配比结构,得到排气良好的产品。S3、嗔施固定剂。在布完微晶干粒后嗔一层甲基水固定剂固定微晶干粒。所述甲基水为质量浓度为3-7%的羧甲基纤维素钠(CMC)水溶液。S4、一次烧成,烧成温度为1500±10°C ;所述烧成的过程具体是在220米窑炉内烧制60-80分钟。微晶熔块烧成制作对工艺中排气也是很大的一个影响因素。熔制温度过高过低对后期生产陶微晶玻璃瓷砖都有很大的影响。熔制温度过高,会使配方中得易挥发成分挥发,改变釉的化学组成,使釉性变差。而温度过低反应不完全,有些造气物质尚未分解完全,在烧制成陶瓷时会使排气变差。因此在熔制熔块时应使温度控制在微晶熔块没有夹生料,接板没有气泡或存在少许气泡为宜。本发明根据自身配方的结果特点生产加工温度保持1500± 10°C,并且确保熔窑处于氧化气氛,使燃油充分不污染熔块,而产生气泡。其中,经过一次烧成后的微晶玻璃陶瓷砖,在使用前,还需要对所述微晶玻璃陶瓷砖进行炉窑烧制。针对本发明的微晶玻璃陶瓷砖的气体排放特点及烧制规律设计了窑炉烧制温度稳定曲线:面温为 980oC,1000oC,1025oC,1030oC,1050oC,1070oC,1095oC,1120°C,1145°C, 1160°C, 1170°C, 1205°C, 1205°C, 1205°C, 1205°C, 1160°C, IOOO0C ;
底温为 910 °C,980 °C, 1025 °C, 1030 °C, 1060 °C, 1080 °C, 1100 °C, 1130 °C, 1160 V,1180°C,1190°C,1195°C,1195°C,1195°C,1195°C,119(rC,113(rC。经过炉窑烧制后,所述微
晶玻璃陶瓷砖即可用于使用。如图2所示的是利用本发明的降低微晶玻璃陶瓷砖气泡的生产方法生产的微晶玻璃陶瓷砖,其中,所述微晶玻璃陶瓷砖包括砖坯100、面釉层200、全抛釉层300和微晶干粒层400,所述面釉层200、全抛釉层300和微晶干粒层400从里到外依次设置于砖坯100表面。实施例1
一种降低微晶玻璃陶瓷砖气泡的生产方法,其中,包括以下步骤:
S1、在干燥好的生坯上施面釉后再施一层全抛釉。所述面釉施用量为800*800mm的生还上施700 g,比重为1.8,所述全抛釉的施用量为800*800mm的生还上施200 g,比重为1.35。S2、施微晶干粒,所述微晶干粒的过筛目数为10-80目,按照重量百分比计所述微晶干粒包括:
10-30 目 45% ;
30-60 目 35% ;
60-80 目 20%。所述微晶干粒 的施用量为800*800mm的生坯上施3000 g,用于制备所述微晶干粒的原料,按重量百分比计包括:
石英粉 20% ;
氧化招 15% ;
白云石 21% ;
硼酸8% ;
锂瓷石 28% ;
钾长石 8 %。S3、在微晶干粒层上喷施甲基水固定剂;
S4、一次烧成,烧成温度为1500°C,烧制时间为70分钟。S5、放进窑炉进行烧制:窑炉温度稳定曲线:面温为980°C,1000°C,1025°C,1030°C, 1050°C, 1070°C, 1095°C, 1120°C, 1145°C, 1160°C, 1170°C, 1205°C, 1205°C, 1205°C,1205°C, 1160°C, IOOO0C ;
底温为 910 °C,980 °C, 1025 °C, 1030 °C, 1060 °C, 1080 °C, 1100 °C, 1130 °C, 1160 V,118(TC,119(TC,1195 ,1195 ,1195 ,1195 ,119(TC,113(TC。本实施例所得的微晶玻璃陶瓷砖,800*800mm的砖中,小于0.05毫米的小气泡不超过5个,大于0.05毫米的气泡没有,小毛孔很少,釉面较为清澈干净。实施例2
一种降低微晶玻璃陶瓷砖气泡的生产方法,其中,包括以下步骤:
S1、在干燥好的生坯上施面釉后再施一层全抛釉。所述面釉施用量为800*800mm的生还上施650g,比重为1.75,所述全抛釉的施用量为800*800mm的生还上施150 g,比重为
1.3。S2、施微晶干粒,所述微晶干粒的过筛目数为10-80目,按照重量百分比计所述微晶干粒包括:
10-30 目 40% ;
30-60 目 35% ;
60-80 目 25%。所述微晶干粒的施用量为800*800mm的生还上施3500g,用于制备所述微晶干粒的原料,按重量百分比计包括:
石英粉 25% ;
氧化招 17% ;
白z 石 18% ;
硼酸5% ;
锂瓷石 30% ;
钾长石 5 %。S3、在微晶干粒层上喷施甲基水固定剂;
S4、一次烧成,烧成温度为1500°C,烧制时间为80分钟。S5、放进窑炉进行烧制:窑炉温度稳定曲线:面温为980°C,1000°C,1025°C,1030°C, 1050°C, 1 070°C, 1095°C, 1120°C, 1145°C, 1160°C, 1170°C, 1205°C, 1205°C, 1205°C,1205°C, 1160°C, IOOO0C ;
底温为 910 °C,980 °C, 1025 °C, 1030 °C, 1060 °C, 1080 °C, 1100 °C, 1130 °C, 1160 V,118(TC,119(TC,1195 ,1195 ,1195 ,1195 ,119(TC,113(TC。本实施例所得的微晶玻璃陶瓷砖,800*800mm的砖中,小于0.05毫米的小气泡不超过5个,大于0.05毫米的气泡没有,小毛孔很少,釉面较为清澈干净。本发明提供一种微晶玻璃陶瓷砖及降低微晶玻璃陶瓷砖气泡的生产方法,通过针对微晶干粒成分、干粒过筛目数搭配及烧制温度的设置实现了降低微晶玻璃陶瓷砖气泡的目的,使得釉面的气泡不仅大大降低而且气泡体积也极微小,微晶层透明度高,釉面显得清澈干净,产品品质得以进一步提升。应当理解的是,本发明的应用不限于上述的举例,对本领域普通技术人员来说,可以根据上述说明加以改进或变换,所有这些改进和变换都应属于本发明所附权利要求的保护范围。
本发明公开微晶玻璃陶瓷砖及降低微晶玻璃陶瓷砖气泡的生产方法,所述方法为在生坯上施面釉、全抛釉;然后施微晶干粒,使微晶干粒的过筛目数为10-80目,其按重量百分比计包括10-30目40-50%;30-60目30-40%;60-80目15-25%;喷施固定剂后一次烧成,烧成温度为1500±10℃,烧制时间为60-80分钟。本发明通过针对微晶干粒成分、干粒过筛目数搭配及烧制温度的设置实现了降低微晶玻璃陶瓷砖气泡的目的,使得釉面的气泡不仅大大降低而且气泡体积也极微小,微晶玻璃陶瓷砖的微晶层透明度高,釉面显得清澈干净。产品品质得以进一步提升。
微晶玻璃陶瓷砖及降低微晶玻璃陶瓷砖气泡的生产方法
- 专利详情
- 全文pdf
- 权力要求
- 说明书
- 法律状态
查看更多专利详情
下载专利文献
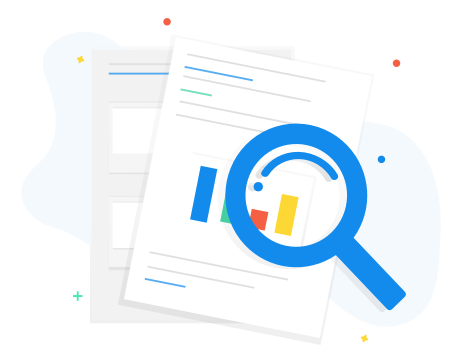
下载专利
同类推荐
-
何维恭岸本正一高伯菘, 王坤池王坤池, 王清华王坤池, 王清华
您可能感兴趣的专利
-
王坤池, 王清华方晨航苅谷浩幸, 前田伸广汤玉斐
专利相关信息
-
吕文慧, 尹计深吕文慧, 尹计深吕文慧, 尹计深吕文慧, 尹计深肖湘东陈秀丽