专利名称:自粘结和预分解的玻璃配合料的制备方法传统的玻璃配合料是散状的,S卩,将具有一定粒度的石英砂、长石、白云石、石灰石、纯碱、芒硝等原料按比例混匀后,以松散的状态给入熔窑内,进行熔化作业。这种工艺存在诸多缺点,例如:(I)物料在窑内处于堆积状态,传热面积非常小,传热系数也不高。(2)在窑内引起粉尘飞扬使窑体侵蚀、堵塞蓄热室。(3)在输送、储存、卸料过程中易发生分层(或离析)破坏混合均匀度。(4)带入大量空气在玻璃熔体内产生难以去除的微气泡。(5)大量的资源得不到有效利用。为了防止入窑之后产生飞料,对原料粒度组成提出了较严格的要求,石英砂·中小于0.1mm的颗粒含量不能超过5%,这就意味着30%以上的细粉不得不分离出去,造成资源浪费。(5)碳酸盐的分解在熔窑内进行,造成能耗较高。玻璃配合料中的石灰石(CaCO3)和白云石(MgCO3)属于碳酸盐矿物,其分解温度在60(T900°C之间,是强烈的吸热反应,反应过程中伴随着大量CO2气体的产生,和其他原料一起给入窑内,由于换热速率低,能耗较高,大量的CO2气体的挥发还会造成大量的气泡,造成澄清困难。对玻璃配合料进行粒化处理可以部分解决上述问题,粒化之后的配合料不仅消除了粉尘和分层,还由于颗粒之间尤其是助熔的碱与难熔的石英砂之间的表面接触面积的大大增加,增强了低温反应程度;粒化后的配合料可使导热系数增加,进而提高熔化率;通过粒化处理,较细的石英砂也可以得到利用。因此,配合料粒化处理可以提高配合料的均匀度、提高熔化率、延长熔窑寿命、改善工作环境、提高资源的利用率。但迄今为止,玻璃配合料的粒化仍然停留在试验阶段,尚未取得大规模工业应用,许多关键技术尚未取得突破,制约了这项技术的进一步发展。瓶颈之一是玻璃配合料的粘结问题。由于玻璃原料本身不具有粘性,在粒化或压块过程中必须要加入某种粘结剂或者进行烧结,烧结的成本太高难以应用,而如果采用粘结剂的话,则要求粘结剂低价、无毒、无腐蚀性、不能含有对玻璃有害的组分,同时符合这些要求的粘结剂尚未发现。中国专利CN101913752公开了一种以膨润土、水玻璃和淀粉为粘结剂的粒化方法;中国专利(CN101318762A)公开的专利技术是用水玻璃、纸浆废液、油水废液和淀粉废液为粘结剂的粒化方法。但这些粘结剂均存在缺陷,它们不同程度存在着有毒有害、成本过高或者对玻璃有潜在危害。如果能够实现配合料的自粘结是较为理想的技术方案,本发明给出针对上述问题的一揽子解决方案。具体而言就是先将玻璃配合料中石灰石和白云石预分解成为熟石灰和方镁石,然后再与其它玻璃配合料进行混合,混合过程同时喷水,混匀后进行压块或者成球粒化。石灰石和方镁石遇水后分别生成的氢氧化钙和氢氧化镁本身都是粘结剂,可以用来实现玻璃配合料的自粘结。本发明带来的好处是:(I)不需要外加粘结剂,实现玻璃配合料粒化过程中的自粘结。氢氧化钙可以和空气中的CO2或玻璃配合料中的纯碱一碳酸钠(NaCO3)反应生产碳酸钙(CaCO3),进而实现配合料的粒化和硬化,反应式如下: Ca (OH) 2+C02=CaC03 丨 +H2O(I) Ca (OH) 2 + Na2C03=2Na0H+CaC03 丨(2) (2)将石灰石和白云石的分解过程移至熔窑外面进行,可以实现窑外分解,有利于节能。众所周知,碳酸盐的分解是个剧烈的吸热过程,化学反应为: CaCO3 — CaO + CO2 i _1645J/g (890°C时)(3) MgCO3 — MgO + C02 -1047 -1214J/g (590°C时) (4) 按照传统的给料方法,颗粒是堆积在一起的,传热效率很低,而窑外分解可以在悬浮预热器和预分解炉内进行,由于在悬浮预热器和预分解炉内的热气流是旋转上升的,事先粉磨过的碳酸盐颗粒在里面实现了高度分散、基本上可以看作单颗粒,传热系数较大,特别是传热面积非常大,可以迅速换热,在几秒内分解率就可以达到85、5%,可以大大降低碳酸盐分解的能耗。这种方法在水泥行业已经普及。(3)碳酸盐的窑外分解可以降低玻璃液中的气泡含量,缩短澄清过程,减少玻璃产品中的气泡量。按照传统方法,碳酸盐的分解过程在熔窑内进行,剧烈的分解过程伴随大量的气泡,而玻璃液的粘度非常大,里面的气泡不容易上浮到表面,容易滞留在内部最终形成缺陷。而窑外分解就避免的这种情况,熔化过程中的气泡量大为减少。《中国专利》公开的“玻璃配合料预烧处理工艺及其设备”(CN102320715),是将玻璃配合料预先压制成球体,再进行预热和预分解。这种方法虽然也是窑外分解,但不足之处在于,一是将所有原料同时预热不利于节能。碳酸盐矿物在玻璃配合料中的比例只有20%左右,把它们和其它不发生分解反应的硅酸盐矿物一起进行窑外分解,会增加不必要的能耗。二是预先压成料球会使得碳酸盐颗粒包裹其中,传热面积受限,严重制约热量传递和质量的传递。 (4)可以利用碱-硅酸反应强化自粘结过程。人们已经知道,许多矿物都具有潜在活性,在某些特定的条件下,这种活性可以被激发出来,碱性激发剂的存在就是激发其活性的有效方法。玻璃配合料中的纯碱和CaO,这些都是强碱性组份,在适当条件下,会与活性SiO2发生碱-硅酸反应,产生具有胶凝性的硅酸钠。玻璃配合料中的石英和碎玻璃中都含有大量的SiO2,特别是后者当中的SiO2是无定形态的,其活性较高,在有碱性组份的情况下,活性SiO2可以与碱性组分发生反应,可以产生碱-硅酸反应,形成具有胶凝性的硅酸钠和硅酸钙。2R0H + nSi02 + H2O — R20.nSi02.nH20(5) (5)本发明可以使原料得到充分利用,是一种资源节约和环境友好的方法。按照传统的散状给入熔窑的方法,玻璃原料中的细粉含量需要严格控制,使得大约30%的资源得不到利用,不仅浪费资源,而且产生新的环境污染。按照本发明的方法,不需要对细粉含量进行控制,并且可以直接使用细粉,甚至进一步粉磨,配合料在经过粉磨后,随着原料粒度的降低,熔化温度会下降、熔化速率会加速,进而减少能源消耗、延长耐火材料寿命,使熔化成本减少。(6)按照本发明的方法,纯碱可以使用轻质碱,可进一步降低原料成本。目前,玻璃配合料中纯碱普遍使用颗粒重碱,主要是为了防止入窑后飞扬。粒化后的玻璃配合料不会飞扬,完全可以采用更便宜的轻质碱。本发明包括碳酸盐窑外分解和原料粒化自粘结二大部分,采用悬浮预热器和窑外分解炉进行碳酸盐的窑外分解;将玻璃原料和碎玻璃一起进行粉磨,利用碱-硅酸反应和机械力化学效应,实现玻璃配合料的自粘结。
本发明的目的在于提供一种自粘结和预分解的玻璃配合料的制备方法,该发明不同于传统的玻璃配合料制备方法,这种方法在不外加其他粘结剂的情况下即可实现玻璃配合料粒化过程中的自粘结,同时,可实现高效的碳酸盐的窑外分解。这种方法具有资源节约和环境友好等优点。为了实现上述目的,本发明采用了如下技术方案:
(1)先将石灰石和白云石粉磨至80μ m以下;
(2)采用悬浮预热器和窑外分解炉对碳酸盐矿物进行窑外分解;
(3)将分解后得到的氧化钙和氧化镁与石英砂、长石粉、碎玻璃、纯碱、芒硝和碳粉,按一定比例给入混合机混合;在混合过程中加入8 20wt%的水。(4)采用成球机或压块机将混合后的配合料,进行粒化成球或压块。(5)将粒化的配合料放置72小时以上,待其水化硬化。(6)将硬化后的配合料投入熔窑。步骤1、3中的粉磨机械需采用非铁质衬板和磨矿介质,例如用石料做衬板、球磨介质为卵石,以防铁的掺入。步骤2中的悬浮预热器和预分解炉可在市场采购或自制,热气流可利用废气、预热器内温度为50(T 600°C,预分解窑内温度为80(T IOOO0C ,燃料可为重油、煤气、天然气。步骤3中的各种原料的用量是根据不同玻璃品种的化学成分表计算后得到的,且不限于上述原料种类,允许存在硝酸钠、萤石等各种小料。步骤4中的成球机或压块机可采用圆盘式成球机或表面带有半圆凹面的棍式压球机。步骤5中的放置时间可根据环境温度和料球的强度决定,时间越长,温度越高,强度越大。步骤1、2并非本发明的必要步骤,玻璃厂也可以直接外购氧化钙和氧化镁。本发明的有益效果是:(I)在玻璃配合料中,引入氧化钙(CaO)和氧化镁(MgO)代替碳酸钙(CaCO3)和碳酸镁(MgCO3),在不外加粘结剂的前提下,实现玻璃配合料粒化的自粘结,消除了外加粘结剂带来的潜在危害;(2)将耗热量巨大的碳酸盐分解过程从熔窑移出,在窑外采用悬浮预热器和预分解炉进行,实现高效节能;(3)减少了气泡数量,可以减少澄清时间,减少玻璃中的气泡缺陷;(4)无需对石英砂粒度下限进行控制,降低了原料成本,提高了资源的有效利用率。
图1是自粘结和预分解的玻璃配合料的制备方法工艺流程图。
实施例1将石英砂、长石、石灰石、白云石、轻质纯碱、芒硝按照表I的成分进行配料;再将其中的碳酸钙和碳酸镁事先煅烧成为熟石灰和方镁石;熟石灰和方镁石加水生成Ca(OH)2和Mg (OH) 2 ;将已经得到的粉末状的Ca (OH) 2和Mg (OH) 2与石英砂、长石、白云石、纯碱、芒硝在强制混合机内混合15分钟,混合过程中加水10wt% ;将后的粉体喷水后压成Φ32πιπιΧ 16mm块状。经检测,放置3天后,抗压强度达到17.3MPa,可以满足给料的要求。经过X射线衍射分析,证明水化硅酸钙和氢氧化钙出现。将压制成的块料进行熔化试验并采用高温显微镜观察,证明出现液相的温度为635°C,比传统方法降低了 67.8°C。进行玻璃熔化试验,得到的玻璃澄清透明,气泡含量少于传统方法。表I玻璃配合料的成分表
本发明公开一种自粘结和预分解的玻璃配合料制备方法,所述方法的步骤是将碳酸盐预先进行窑外分解,得到熟石灰和方镁石,再与其它玻璃配合料按照适当配比一起加入混合机械中进行混合,在此过程中加入8~20wt%的水,然后将混合后配合料进行粒化,静置72小时以上,经过水化硬化,可得到具有一定强度的粒化玻璃配合料。本发明将碳酸盐分解过程在窑外完成,可大大降低热耗;原料的粒度下限无需限制,可最大程度利用资源;使用轻质纯碱,降低原料成本;无需外加粘结剂就可以实现玻璃配合料的粒化,因此,本发明具有熔化速度提高、熔化温度下降和熔化效率高等优点。
自粘结和预分解的玻璃配合料的制备方法
- 专利详情
- 全文pdf
- 权力要求
- 说明书
- 法律状态
查看更多专利详情
下载专利文献
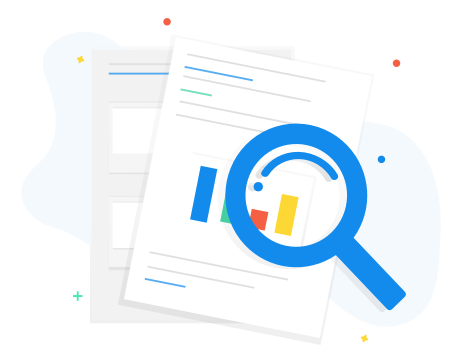
下载专利
同类推荐
-
岸本正一高伯菘, 王坤池王坤池, 王清华王坤池, 王清华
您可能感兴趣的专利
-
王坤池, 王清华方晨航苅谷浩幸, 前田伸广李鹏程吕文慧, 尹计深
专利相关信息
-
吕文慧, 尹计深肖湘东