专利名称:中药浓缩液喷雾干燥设备的制作方法现有技术使用的中药药液喷雾干燥装置,是将药液用雾化器分散成雾滴,并加入热气与雾滴直接接触,使雾滴水分蒸发而被干燥成粉末状颗粒。其装置中没有设置杀菌装置,药液中含有较多的细菌,不符合药品生产的卫生要求,此外,用于干燥药液的热风过滤不充分,以及热风的温度不够高,导致药液干燥得到的颗粒洁净度低且干燥效率低。此外,现有装置由供液罐提供的药液粘稠度不均匀,造成输入喷雾干燥罐的药液喷雾不稳定,严重影响干燥成品的质量。其收集干燥成品的旋风分离器结构单一,收集效率低,最多有95%的粉剂产品能被收集,约5%或更多的粉剂随废气外排被浪费。
本实用新型的目的正是为了克服上述现有技术的不足而提供一种在喷雾干燥前能有效杀死药液中的大肠杆菌及其它细菌,干燥热风洁净,干燥效率高,能将药液粘稠度调配均匀,喷雾干燥稳定,且干燥成品收集率高的中药浓缩液喷雾干燥设备。本实用新型的目的是通过如下技术方案实现的。中药浓缩液喷雾干燥设备,是在喷雾干燥塔前设置有杀菌装置对药液进行杀菌处理;在供液罐与喷雾干燥塔的连接管路上设置有供液泵,并在供液泵后连接有一回转到供液罐的管路,在供液罐与供液泵之间形成一循环回路;在热风管路上依次设置有粗效空气过滤器、空气加热器和精密空气过滤器;旋风分离装置采用二级旋风分离器,并且第二级旋风分离器采用双旋风分离结构,所述的双旋风分离结构是一个入风口,内部分离为两个风力旋向相反的风道,对应有两个分离产品出口。本实用新型所述的加温装置为设置于供液罐与喷雾干燥塔之间连接管路上的管式加热杀菌器;所述的空气加热器是两级空气加热器;所述的两级空气加热器,其第一级是蒸汽加热的空气加热器,第二级是电加热的空气加热器;在压缩空气管路上设置有干燥过滤装置;在干燥塔的罐壁设有水冷却管路及水冷却夹套;在喷雾器上设置有冷却装置;在供液罐、喷雾干燥塔及药液经过的管路上均设置有连接清洗装置的接口。本实用新型设置加温装置对药液进行加温杀菌,可有效杀死药液中的细菌,使药液达到药品生产的卫生要求,设置循环回路对欲进行喷雾干燥的药液预先进行均质化处理,并稳定供液泵后续泵入喷雾干燥塔内的药液的流量,可使进入喷雾干燥的药液粘稠度、成分、温度均匀,便于稳定后续的雾化效果以确保干燥后的成品质量。所设置的空气两级过滤和两级加热工艺使得进入喷雾干燥塔的干燥空气清洁并保持足够高的温度,以提高被干燥成品的洁净度和提高干燥效率。喷雾干燥塔罐壁所设置的水冷却管路及水冷却夹套用于对干燥塔罐壁进行冷却降温,防止低熔点物料的热熔性粘壁。所设置的两级旋风分离装置及其双旋风分离结构可以有效地提高成品收得率。在压缩空气管路上还设置的干燥装置可以对通入附着物扫落装置中的压缩空气预先进行干燥,以免将湿气带入喷雾干燥塔。下面结合说明书附图进一步阐述本实用新型的内容。
图1是本实用新型的结构示意图;图2是图1的A-A剖视图。
如图1所示,本实用新型包括有供液罐2和喷雾干燥塔8,两者之间用管路连接。在供液罐2与喷雾干燥塔8的连接管路上设置供液泵4,并在供液泵4后连接一回转到供液罐2的管路,以在供液罐2与供液泵4之间形成一循环回路,药液可预先在该循环回路中循环流动,配之以在供液罐2内设置的搅拌装置3的搅动和向外设的加热夹套17中供入蒸汽加热,对药液进行均质化处理,以使罐内的药液温度和粘稠度均匀,便于后续的雾化处理。在喷雾干燥塔8前设置管式加热杀菌器5对药液进行加温杀菌。在喷雾干燥塔8内部设置可在塔内旋转的附着物扫落装置6,该装置与压缩空气管路18连接,在压缩空气管路18上设置干燥过滤装置19对进入扫落装置和干燥塔内的压缩空气预先进行干燥处理。在喷雾干燥塔8顶部设置喷雾器7,热风管路16与喷雾器7连接,在热风管路16上依次设置粗效空气过滤器11、空气加热器10和高效空气过滤器9,空气加热器10设置为两级,其第一级采用蒸汽加热的空气加热器将空气加热,第二级采用电加热的空气加热器将空气进一步加热达到干燥所需的温度。喷雾干燥塔8罐壁设置水冷却管路20及水冷却夹套21用于对干燥塔罐壁进行冷却降温。在喷雾干燥塔8后面连接二级旋风分离器14、15,并且第二级旋风分离器14采用双旋风分离结构,所述的双旋风分离结构如图2所示,是一个入风口,内部分离为两个风力旋向相反的风道,对应有两个分离产品出口。
操作过程如下打开蒸汽电磁阀1,蒸汽进入供液罐2的加热夹套17,对药液进行加热到55~95℃,设置在供液罐上的温度传感器将检测温度信号传输到控制系统控制蒸汽电磁阀1的通断,使药液保持稳定的温度。启动供液泵4,药液在由供液泵4沿管道连续输送到喷雾干燥塔8的过程中被加热到80℃以上杀菌,可有效杀死药液中的大肠杆菌及其它一些细菌,杀菌后的药液输送到喷雾干燥塔8顶部的离心式喷雾器7被雾化成液滴。压缩空气由鼓风机12吹入,在热风管路16上经粗效空气过滤器11、空气加热器10(蒸汽加热+电加热)、精密空气过滤器9进行两级过滤、两级加热后送入喷雾干燥塔8顶部,与液滴接触、混合,进行传热与传质,进行干燥。干燥过程中,附着物扫落装置6向干燥塔内喷吹经干燥装置19处理过的压缩空气以防止干燥后的颗粒粘壁。当干燥的物料为低熔点物料时,接通冷却水管路20,让冷却水进入罐壁的冷却夹套21,对对干燥塔罐壁进行冷却降温,防止低熔点物料的热熔性粘壁。在喷雾器7上设置有冷却系统,运转过程中要注意对喷雾器6的冷却,以免因过热而受损。喷雾器6是可拆卸式的,可拆卸下来用温水清洗。整台设备的清洗和清扫,可采用设置在罐体内的高压清洗喷头接口或通过管路接口连接清洗装置。
干燥后的气固混合物沿管道进入一级旋风分离器15,约91%的粉状颗粒从一级旋风分离器15的底部排出来,剩余粉末随空气从一级旋风分离器15顶部沿管道进入二级双旋风分离器14,有7%~8%粉状颗粒在二级双旋风分离器14被分离出来,残留不到1%~2%的粉末量随废气由排风机13排入大气。该装置使粉末收集总量达到98%~99%以上。
本实用新型也适用于食品等领域对料液的喷雾干燥处理。本实用新型可在各个环节和罐体上设置控制装置与控制系统相连,对整个工作过程进行全自动控制。
中药浓缩液喷雾干燥设备制作方法
- 专利详情
- 全文pdf
- 权力要求
- 说明书
- 法律状态
查看更多专利详情
下载专利文献
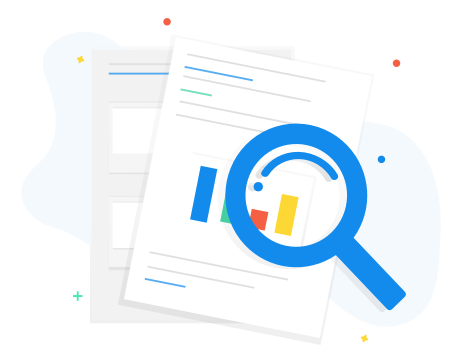
下载专利
同类推荐
-
黄云唐凤德, 蔡天革
您可能感兴趣的专利
-
唐凤德, 蔡天革黄志军黄志军李玉虎
专利相关信息
-
孙晓波瞿金玲, 瞿长宝瞿金玲, 瞿长宝王河荣