专利名称:陶瓷多层线路板和半导体组件的制作方法本发明涉及一种新颖的陶瓷多层线路基片,特别涉及一种包括装有载体基片的陶瓷多层线路板的半导体组件,该基片上安装有半导体器件。具体地说,它涉及一种半导体组件结构,在这种结构中,可将有良好导电率的银或铜导体用于多层线路板,而且,这种半导体器件的焊接部分有很好的可靠性。为了在大型电子计算机中获得较高的运算速度,必须要在半导体器件本身以及封装器体的系统中达到较高的信号传播速度。在最近几年里,对于半导体器件,高集成技术的发展在高速和高集成度方面取得了显著的结果,而封装技术开始极大地影响运算速度的增加。至于封装技术,陶瓷多层线路基片已逐渐被应用,以取得半导体器件的高密度封装和降低电信号的延迟。以前,氧化铝通常被用作陶瓷多层线路基片的隔离材料,然而在最近几年,为了进一步提高基片特性,已经研究和发展了多种低温烧结基片材料,例如在“多层陶瓷基片”〔日本专利申请Kokoku(审查后,公开)№.22,399/84〕中所描述的材料,以及用二氧化硅与玻璃粘结形成的低介电常数的低温烧结材料,如在“陶瓷多层布线线路板”〔日本专利申请Kokai(已公开)№.11,700/84〕中描述的材料。在这些通过烧结原始材料得到的线路板材料中,达到了几乎没有微孔的紧密度,这种材料中,对获得较高运算速度有极大影响的比介电常数的最低值约在4至5之间。而且,用于隔热、减轻重量或隔音目的的多孔陶瓷材料也已经得到,例如在“合成陶瓷电子材料”〔日本专利申请Kokai(已公开)№.89,212/82〕,和“泡沫陶瓷板的制造方法”〔日本专利申请Kokai(已公开)№.83,985/84〕中所描述的。然而没有考虑过把这些基片用作需要较高信号传播速度的大型电子计算机所用的基片材料。另一方面,随着高速,高密度半导体的出现,为了促进器件的热辐射和增加器件的速度而将半导体器件直接封装在陶瓷多层线路基片上的方法已经被使用。然而,这种方法存在一个问题,即因为半导体器件尺寸的增加,在封装时由于温度的变化而产生的半导体器件材料与陶瓷多层布线线路基片材料之间的应力将增加。因此,必须努力使陶瓷多层布线线路基片的热膨胀系数接近半导体器件的热膨胀系数。然而,为使用具有低电阻的金、铜、银等作为布线导体材料以得到高密度布线,必须找到接近于这些导体材料的热膨胀系数的陶瓷隔离材料。这样,陶瓷隔离材料的热膨胀系数既要接近于半导体器件材料的热膨胀系数,又要接近于导体材料的热膨胀系数。然而,还没有就能适应于这些相互矛盾条件的封装技术作出应有的考虑。在陶瓷多层线路基片中,隔离材料需要有尽可能低的介电常数,以达较高的信号传播速度。而且,所用的导体材料需要有低的电阻。例如,在“陶瓷多层布线线路板”〔日本专利申请Kokai(已公开)№.11,700/84〕中所描述的,已经得到了由具有低介电常数的二氧化硅与玻璃结合组成的比介电常数在4至5之间的基片材料。而且,因为这种材料能在不高于1000℃的温度下烧结,因此,具有低电阻的导体材料,即金、铜、银等等都能够与此组合。此外,这种陶瓷多层线路板材料的热膨胀系数已尽可能地接近于半导体器件的热膨胀系数,而和导体材料的热膨胀系数很不相同。然而,还没有适当地注意去达到内部线路的高密度布线,也没有注意到高密度,高可靠性地安装半导体器件。本发明的目的在于提供一种封装技术,它给出一种陶瓷多层线路基片,这种基片包括具有较低的比介电常数的陶瓷隔离材料以及在其上高密度布线的,例如金、铜或银等低电阻率的导体材料,这使得有可能高密度高可靠性地安装半导体器件。根据本发明,可提供一种由陶瓷层和布线导体层交替层迭组成的陶瓷多层线路板,在此陶瓷多层线路板中,陶瓷层的热膨胀系数比布线导体层的热膨胀系数低,但不低于它的一半,此陶瓷层由软化温度不高于布线导体层熔点的玻璃形成。图1和图2各自为说明本发明的具体装置的半导体组件的纵向剖视图。在图1和图2中,参考数字1和10表示半导体器件,参考数字2和11表示以有机材料为主要成分的一种材料,数字3和12表示载体基片,数字4和13表示焊料,数字5和16表示通路孔导体材料,数字6和17表示布线导体材料,数字7和18表示陶瓷隔离材料,数字8和19表示金-锗焊料,数字9和20表示科代引线,数字14表示聚酰亚胺树脂(Polyimideresin),数字15表示铜导体布线材料。该陶瓷层具有不低于7.2×10-6/℃的热膨胀系数和在1MHz时不高于4.5的比介电常数。布线导体层由金或银或铜中的一种构成。
本发明的陶瓷多层线路板当在陶瓷层中包含有少量直径为100微米或更小的空心二氧化硅时能具有更低的介电常数。空心二氧化硅的含量最好占陶瓷层的35-60%体积比。
为了降低陶瓷隔离材料的比介电常数,这是上述目的之一,可以想到包含与玻璃结合的低介电常数的填充物的那些材料。就低介电常数的填充物而言,二氧化硅在无机材料中有最低的介电常数。然而,因为二氧化硅的比介电常数约为4,因此很难通过现有的致密地烧结陶瓷的方法得到比介电常数小于4的陶瓷隔离材料。本发明是基于这样的想法,因为空气的介电常数约为1,因此,在材料中引入微孔就可得到比介电常数小于4的陶瓷隔离材料。虽然已经知道几种包含许多用于隔热和隔音的微孔的结构材料,但这些材料中的微孔通常大到直径为几个毫米,因此这种材料不能用于多层线路板。因此,为将这种材料用于多层线路板,由于内部布线的高度集成和对短路、布线断裂的敏感性等因素,材料内部包含的微孔的微细直径应不大于100微米。
为了制备内部有微孔的陶瓷隔离材料,可以设想一种方法,例如将陶瓷粉末和发泡剂混合,然后燃烧该混合物,同时伴随着发泡,从而得到内部含有微孔的陶瓷,另一种方法是将陶瓷粉末和空心的微球体混合并烧结这些混合物。然而,因为使用发泡剂的方法很难给出大量分散在陶瓷中的均匀细微的微孔,所以只有采用混合陶瓷粉末和空心微球体的方法。关于空心的微球体,为得到尽可能低的相对介电常数,已采用了具有无机材料中最低介电常数的二氧化硅作为空心二氧化硅微粒的主要成分,并精选直径不超过100微米的微粒。因为混合物必须在一个不高于布线导体材料例如金、铜、或银的熔点的温度下烧结,所以用于和空心二氧化硅微球体结合的陶瓷,从能在不高于这个所说的熔点的温度下软化的玻璃和结晶玻璃中精选出来的。“结晶玻璃”是从加热的非晶态玻璃中析出的结晶相玻璃,它同时具有低温烧结特性和一定的强度。
本发明所用的微粒直径需不大于约100微米,该材料用下面的方法来制备。这样,通过喷雾干燥法使含有Na的二氧化硅形成空心的微粒,随后将这些空心微粒迅速加热以产生空心微球体。然后将微球体冷却,并接受酸处理,水洗等等,使Na含量不超过2%重量比。当Na含量不超过2%重量比时,这些微球体在温度不高于100℃时将不软化,因此具有足够高的热阻温度。
为了达到低电阻率导体材料的高密度布线,即上面提到的其他目的。陶瓷隔离材料和导体材料之间的热膨胀系数的差别应做得小些。此外,为了得到尽可能低的电阻率,导体材料最好采用纯金属。既然金、铜或银的热膨胀系数都很高,分别为1.44×10-5/℃,1.68×10-5/℃或1.92×10-5/℃,应力分析的结果表明,陶瓷隔离材料的热膨胀系数至少也应有上面提到的各系数的一半。结果,当用金作为导体材料时,陶瓷隔离材料应具有不小于7.2×10-6/℃的热膨胀系数。同样,当用铜作导体材料时,陶瓷隔离材料应有不小于8.4×10-6/℃的热膨胀系数,这样,尽管以前的倾向是使陶瓷隔离材料的热膨胀系数接近于硅半导体器件的热膨胀系数,而为了得到高密度布线,陶瓷隔离材料的热膨胀数相反地应增加,以便接近于导体材料的热膨胀系数。因此,这样得到的多层线路板具有比较大的热膨胀系数,从而很难将硅半导体器件直接安装上去。所以,应发明一些新的高密度封装硅半导体器件的方法。于是,发明了在陶瓷多层线路基片和半导体器件之间提供一个载体基片的方法,从而缓和了陶瓷多层线路板和半导体器件的热膨胀系数之间的差别。首先,半导体器件借助焊料块(Solder bump)直接安装在载体基片上。然后,将主要成分为有机材料的、热膨胀系数和焊料完全相同的材料插入半导体器件和载体基片之间。此后,将如此得到的系统借助焊料块装到陶瓷多层线路基片上就得到了组件。在这种情况中,由于载体基片和陶瓷多层线路基片仅与焊料接触,从焊接点的可靠性的观点上说,载体基片和陶瓷多层线路基片的热膨胀系数应近似相同。热循环试验和应力分析的结果表明,载体基片和陶瓷多层线路基片的热膨胀系数的差别必须不高于1×10-6/℃。另一方面,由热循环试验和应力分析已经证实,半导体器件与载体基片热膨胀系数之间的差别造成的热应力可通过在两者之间填入主要成分为有机材料的材料而得到缓解,并能在热膨胀系数的差别达到1×10-5/℃。以前维持焊接点的可靠性。作为一个结果,已经实现了一种封装方法,在该方法中,可以使用其热膨胀系数高于半导体器件热膨胀系数的陶瓷多层线路基片,而且,根据工艺要求在这些焊接中使用的焊料应有彼此不同的熔点。这样,用于焊接半导体器件和载体基片的焊料,其熔点必须高于焊接载体基片和陶瓷多层线路板所用的焊料。
有机树脂能较好地同橡胶微粒和陶瓷粉末结合。前者的数量最好是与100份重量的树脂相应有5-10份重量,后者的数量最好是占相对于全部体积的35-60%。
上述橡胶微粒最好至少选取聚丁二烯(polybutadiene)和硅橡胶中的一种。上述陶瓷粉末最好至少选取石英,碳化硅、氮化硅碳化钙及含铍碳化硅中的一种。
用于载体基片和多层线路板的陶瓷层最好含有下述成分(按重量百分比)的玻璃20-95%的SiO2及至少从25%或更少的Al2O3,15-25%的MgO,50%或更少的B2O3,15-25%的ZnO,10-25%的CaO,4-20%的Li2O中选取一种。更准确地说,下列成分是可取的(1)50-70%的SiO2,15-25%的Al2O3和15-25%的MgO。
该成分可以进一步包含有5%或更少的至少从B2O3,K2O,P2O5,ZrO2,CaF2,AlN,Cs2O和V2O5中选取的一种。
(2)70-95%的SiO2,4-15%的Li2O,1-10%的Al2O3,和5%或更少的至少从K2O,MgO和B2O3中选取的一种。
该成分可以进一步包含有5%或少一些的至少从P2O5,ZrO2CaF2,AlN,Cs2O和V2O5中选取的一种。
(3)30-50%的SiO2,30-50%的B2O3,10-25%的CaO和10-20%的Li2O。
该成分可以进一步包含有5%或少一些的至少从K2O,MgO,CaF2,P2O5,ZrO2,AlN,Cs2O和V2O5中选取的一种。
(4)55-82%的SiO2,15-25%的B2O3,2-15%的Li2O,和1-10%的Al2O3。
该成分可以进一步包含有5%或少些的至少从CaF2,P2O5,ZrO2,AlN,Cs2O,V2O5、MgO以及K2O中选取的一种。
(5)55-65%的SiO2,15-25%的ZnO,和10%或少些的至少从Al2O3,Li2O和K2O中选取的一种。
该成分可以进一步包含有5%或少些的至少从B2O3,CaF2,MgO,K2O,P2O5,ZrO2,AlN,Cs2O和V2O5中选取的一种。
(6)20-30%的SiO2,10-15%的Li2O,40-50%的B2O3,和15-25%的CaO。
该成分可以进一步包含有5%或少些的至少从CaF2,Al2O3,K2O,P2O5,ZrO2,AlN,Cs2O和V2O5中选取的一种。
而且,本发明提供了一种用于陶瓷多层线路板的无定形玻璃粉末,其组分为20-95%的SiO2和至少从25%或少些的Al2O3,15-25%MgO,50%或少些的B2O3,15-25%的ZnO,10-25%的CaO,和4-20%的Li2O中选取的一种(每种均为重量百分比)。玻璃粉末最好通过将上面所列成分熔化后再淬火和研磨得到的无定形玻璃,由此得到5微米或更小的微粒直径。
陶瓷多层线路基片包括比介电常数为3.0-4.5的陶瓷隔离材料和主要由具有低电阻率的金、铜或银构成的、在其上高密度布线的布线导体材料,它具有比半导体器件高得多的热膨胀系数,因此,具有与陶瓷多层线路基片近似相同的热膨胀系数的载体基片被放在半导体器件和陶瓷多层线路基片之间,并借助焊料进行接合,一种主要成分为有机材料、热膨胀系数与焊料近似相同的材料被填在半导体器件和载体基片之间,从而使焊接部分的可靠性得到改善。这样,甚至对于具有比较高的热膨胀系数的陶瓷多层线路基片,也能得到一种封装方法,半导体器件可以用这种方法高密度地封装,也能得到焊接部分的高可靠性。此外,可以把接合装有半导体器件的载体基片和陶瓷多层线路基片的焊接部分分开,从而使半导体器件的表面能得到保护。
实例本发明将参考下面的实例来描述。在下面的叙述中,“份”意为重量的份数,“%”意为重量的百分比,除非另有规定。
实例1通过熔化表1所列成分后,再将得到的无定形玻璃淬火,研磨成5微米或更小的微粒直径,从而制备出玻璃粉末。
40份平均直径为28微米的空心二氧化硅微球体和60份表1所列成分的玻璃粉末(平均直径为1微米)的混合物中分别加上12.5份作为粘合剂的、平均聚合等级为1000的聚乙烯醇缩丁醛树脂(polyvinyl butyralresin),4份作为增塑剂的丁基邻苯二甲酰,丁基乙二醇酸酯(butylphthalyl butylglycolate)以及作为溶剂的62.0份的三氯乙烯,16.0份的四氯乙烯和22.0份的n-丁醇。把上述成分全部混合在一个湿球磨机内磨成浆,并用搅拌真空除气机把在球磨期问在浆中产生的气泡释放出去,并调节到适当的粘度。随后用刮刀法在硅处理聚脂膜支架上涂复0.2毫米厚的浆,又在干燥箱中除去溶剂而得到一种原料片。
把原料片切成210毫米的正方形,在100℃,5千克力/厘米2的压强下挤压以平整它的表面。然后,使用冲压机将片切成200毫米的正方形,并在那里做一个引导孔。随后利用引导孔将原料片定位,并在预先设定的位置上用电子束加工法打出直径为0.1毫米的通路孔,把由金粉、硝化棉、乙基棉、聚乙烯醇缩丁醛和三氯乙烯按100∶3∶1∶2∶23(按重量)的比例组成的导电膏填满原料片中的通孔。然后,导电膏按照预先设定的线路图形用丝网印刷方法印刷,把这样得到的50片原料片在引导孔位置上对准堆放起来,并在120℃,25千克力/厘米2的压强下层迭起来,随后经过冲切,得到150毫米见方的正方形原料片迭层。将该迭层放入烤箱在空气中于最高温度850℃到960℃烧一小时。这样,就制得了120毫米见方和7毫米厚的陶瓷多层线路基片。
除了通路孔位置和布线图形有所改变以外,载体基片按照与陶瓷多层线路基片相同的方法制得,迭层薄片的数目为7,烧制以后的载体基片的尺寸为11毫米见方和1毫米厚。
10毫米见方的半导体器件(硅)用95%的铅-5%的锡的焊料焊接到载体基片上。然后,在载体基片与半导体器件之间填充具有与焊接材料的热膨胀系数大致相同的材料,这种材料是由100份环氧树脂(商品名为EP-828)和5至10份的聚丁二烯(商品名为CTEN,1300×9)组成的有机混合物以及35-60%体积比的平均微粒直径为1微米的石英粉末掺在一起构成的。然后,把9×9=81片载体基片(焊接有半导体器件的,并已填入主要成分为有机材料的材料)用60%铅-40%锡的焊料焊接到陶瓷多层线路基片(已用金-锗焊料焊接到科伐引线)上,制得一个半导体组件。
这样制得的陶瓷多层线路基片的特性和在组件基片中的焊料接合部分的可靠性如表2所示。在陶瓷多层线路基片中使用的陶瓷隔离材料的比介电常数(在1MHz时)为3.0至4.5,电信号延迟时间为5.7至7.0毫微秒,这样,相对于以氧化铝为主要成分的陶瓷多层线路基片已使速度加快31-44%,后者有高的比介电常数(9.5),电信号的延迟时间为10.2毫微秒。因为20号陶瓷多层线路基片具有7.0-9.0×10-6/℃的热膨胀系数,因此,某些材料体系会产生内部龟裂,其原因在于内部布线材料金和陶瓷隔离材料之间热膨胀系数的差别。然而,因为21号-38号陶瓷多层线路基片有8.0-13.0×10-6/℃的热膨胀系数,它们与内部布线导体材料金匹配很好,在基片内不会引起龟裂。另一方面,在半导体组件中,甚至在反复3000次-55℃至150℃温度循环后所有的焊接部分都没有出现布线的断裂。这将完全满足大型电子计算机的寿命要求。
实例2半导体器件以与上述实例1相同的方法制得,除了以下更改用聚甲基丙烯酸酯(polymethacrylate)树脂代替平均聚合等级为1000的聚乙烯丁醛树脂。
用邻苯二甲酸二乙酯(Diethyl phthalate)代替丁基邻苯二甲酰,丁基乙二醇酸酯。
用铜粉代替金粉。
用聚甲基丙烯酸酯(polymethacrylate)代替聚乙烯醇缩丁醛。
用氯气炉代替空气炉。
这样制得的陶瓷多层线路基片的特性和组件基片中的焊接部分的可靠性如表3所示。陶瓷多层线路基片中使用的陶瓷隔离材料在1MH2时有3.0-4.5的比介电常数,以及5.7-7.0毫微秒的电信号延迟时间。这样,与氧化铝型陶瓷多层线路基片相比较已得到31-44%的速度提高。在39号,48号,54号和55号陶瓷多层线路基片中,一些材料体系的热膨胀系数低于用铜作为内部布线导体材料热膨胀系数的一半,其结果是这些陶瓷隔离材料不能与铜很好匹配,引起产生龟裂。然而,在上述这些以外的其它陶瓷多层线路基片中,没有观察到产生龟裂,陶瓷隔离材料与铜匹配得很好。另一方面,将半导体组件重复3000次-55°-150℃的温度循环试验,在44,49和52号组件的焊接部分产生了一些龟裂,这说明了在重复温度循环时有发生布线断裂的可能性。上述这些组件以外的组件在焊接部分没有改变,因此证明它们能够在实际中得到满意的使用。
实例3除了下列更改外,按照实例1和实例2同样的方法制得组件为了制备载体基片,把由7个原料片层迭起来,然后用燃烧法得到的白基片(没有通路孔也没有布线图形)截成11毫米见方。然后,用激光在白基片上产生0.1毫米直径的孔后,再用镀敷法在孔里填满铜而制得载体基片。
这样制得的组件给出与实例1和实例2相似的结果。
实例4使用铜和聚酰亚胺的多层布线线路是在实例1和实例2制备的陶瓷多层线路基片上形成的。陶瓷多层线路基片包含26层。
在陶瓷多层线路基片上,用真空淀积的方法形成0.03微米厚的铬膜和0.1微米厚的铜膜。然后,在表面涂复22微米厚的正光致抗蚀剂,形成布线图形。用电解电镀的方法形成20微米厚的铜布线层。接着涂复22微米厚的正光致抗蚀剂,形成一个内层电路图形,再用电解电镀法形成20微米厚的铜的内层电路投影。除去正光致抗蚀剂后,铜膜和铬膜的多余部分用氩离子刻蚀法除去。接着,用热膨胀低的聚酰亚胺型树脂涂复50微米厚,形成一个隔离层。然后,把热膨胀系数低的聚酰亚胺型树脂层表面用表面抛光法弄光滑。而且,对内层电路的投影由联氨水合物-乙二胺(hydrazine hydratecfhylenediamine)的液态混合物用湿刻法使之曝光。接着以与第一层布线相同的方法形成又一层20微米厚的铜布线层。以这样的方法,在陶瓷多层线路基片上形成3层铜布线层。
半导体器件和载体基片按照与例1至例3同样的方法安装,这样,就制成了组件基片。
按这个例子制备的组件基片的信号传播延迟时间比按例1到例3制备的组件基片减少大约5%。这是由于低热膨胀的聚酰亚胺隔离材料具有3.5的比介电常数。焊接部分的可靠性与例1至例3中的大体相同。这是因为,既然陶瓷多层线路基片上形成的聚酰亚胺和铜的多层布线线路的厚度小,热膨胀系数的改变也就小的缘故。
根据本发明,由于使用的陶瓷隔离材料具有相对高的热膨胀系数,这使得以有低电阻率的金、铜或银等为主要成分的布线导体材料能够高密度地布线。而且,找到了一种封装方法,按照这种封装方法,半导体器件高密度地封装,在焊接部分也能达到高的可靠性,甚至对于具有高的热膨胀系数的陶瓷多层线路基片来说只要在半导体器件和陶瓷多层线路基片之间插入载体基片,它们之间用焊料焊接,并用以有机材料为主要成分的热膨胀系数与半导体器件和载体基片之间焊料大体相同的材料进行隔离,也可以做到上述各点。
一种由陶瓷层和布线导体层交替层迭组成的陶瓷多层线路板,陶瓷层有较布线导体层低的热膨胀系数,但不低于导体层热膨胀系数的一半。陶瓷层由软化温度不高于布线导体层熔点的玻璃形成。一种半导体组件,该组件的焊料接合部分有高的可靠性,它包括上述装着陶瓷载体基片的陶瓷多层线路板(陶瓷基片上装有半导体器件)和能用具有良好电导率的银或铜导体做的板,以及一种用于所说的陶瓷多层线路板的无定形玻璃粉末。
陶瓷多层线路板和半导体组件制作方法
- 专利详情
- 全文pdf
- 权力要求
- 说明书
- 法律状态
查看更多专利详情
下载专利文献
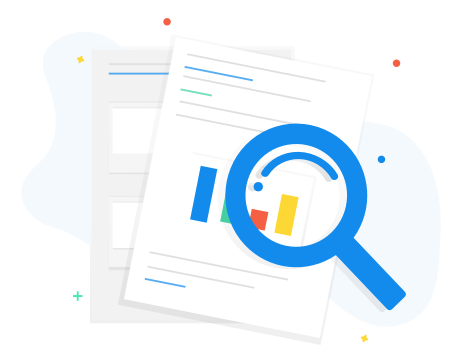
下载专利
同类推荐
-
牛房信之李向民名取荣治汤玉斐杨建
您可能感兴趣的专利
-
杨建张晨, 张森林李章雨
专利相关信息
-
J.D.克罗斯J.D.克罗斯J.D.克罗斯J.D.克罗斯J.D.克罗斯J·伊罗拉