专利名称:用于玻璃熔体流的真空脱气法的制作方法图1(a)是本发明玻璃熔体流真空脱气法所用真空脱气设备重要部分的剖面图。图1(b)是沿图1(a)中B-B′线的剖面图。图1(c)是沿图1(a)中C-C′线的剖面图。图2是根据本发明一个实施例,玻璃熔体流真空脱气法所用真空脱气设备的剖面图。图3是根据本发明另一个实施例,玻璃熔体流真空脱气法所用真空脱气设备的剖面图。图4是实施玻璃熔体流常规真空脱气法所用真空脱气设备的剖面图。参考这些附图,将对本发明玻璃熔体流真空脱气法的一些较好实施方案进行描述。如上所述,本发明涉及在真空室内对玻璃熔体流进行真空脱气的方法,规定在真空室内连续流动的玻璃熔体的停留时间范围,从而可有效并确切地获得不含气泡的玻璃熔体。
参考附图1(a)、1(b)和1(c)对这种真空脱气法进行描述。
图1(a)-1(c)是本发明玻璃熔体流真空脱气法所用设备重要部分的图。本发明的真空脱气法主要包括下列步骤将玻璃熔体送入真空脱气步骤进行脱气的输入步骤;在减压条件下,从基本作水平状态流动的玻璃熔体中除去气泡的真空脱气步骤;以及排放在真空脱气步骤中进行了脱气的玻璃熔体的排放步骤。
图1(a)中,将储存在压力P条件下熔制器10中由玻璃原料熔制获得的玻璃熔体通过向上管道1输入到的真空脱气器12中,形成玻璃熔体流。基本作水平方向流动的玻璃熔体中所保留的气泡在减压环境下上升到玻璃熔体表面,然后在玻璃熔体表面上破裂除去,这个真空脱气步骤主要是在真空脱气器12中进行的。将在真空脱气器12中已经脱气的玻璃熔体从真空脱气器12朝后面的槽18排放,这个在向下管道16中进行。向上管道14和向下管道16以及真空脱气器12的主要部分都被真空罩壳(图中未示)覆盖着,该罩壳连接到一个真空泵,通过在真空脱气器12顶部的开口12a、12b对真空脱气器抽真空,保持恒定的减压。
上面描述中压力P的值通常为760[mmHg]。
如前所述,在此真空脱气法所用的真空脱气器12中,玻璃熔体流所含的气泡长大并上升到玻璃熔体表面,在该表面上破裂,玻璃熔体在真空脱气器12中的停留时间即玻璃熔体通过真空脱气器12的时间不能太短。甚至也很难过分缩短在输入步骤中玻璃熔体通过向上管道14上升的时间,在此输入步骤中储存于压力P[mmHg]条件下的熔制器10中的玻璃熔体被抽吸上升到减压条件下的真空脱气器12。在向上管道14下部的压力由于玻璃熔体本身的重量而较高,而向上管道14上部的压力向着真空脱气器12中的玻璃熔体表面方向逐渐变小,因此,当玻璃熔体在向上管道14中上升时,施加到玻璃熔体的压力低于熔制玻璃原料获得玻璃熔体时的操作压力P[mmHg]。结果在玻璃熔体通过向上管道14的同时,玻璃熔体中的气泡长大。而且,玻璃熔体在向上管道14中上升时,由溶解在玻璃熔体中的气体形成的新气泡在长大。
而且,也很难过分缩短玻璃熔体通过向下管道16的时间。原因如下当玻璃熔体在向下管道16中下降时,作用于玻璃熔体的压力由于玻璃熔体本身的重量而从真空脱气器12中的减压状态逐渐上升,最后恢复到上述压力P[mmHg]。然而,即使通过真空脱气器12中的减压也未能除去的气泡会溶解成玻璃熔体中的气体组分,这是因为随玻璃熔体在向下管道16中下降而压力提高的缘故。
本发明提供一种真空室,可提供38[mmHg]-(P-50)[mmHg](相对于压力P[mmHg])范围的作用于玻璃熔体的压力,包括玻璃熔体不仅通过真空脱气器12,而且通过向上管道14和向下管道16部分的时间。真空室内压力为38[mmHg]或更高的原因是可以抑制真空室中在玻璃熔体中溶解的气体发生不希望的释放(再沸)。如前面所述。按上面所述定义的真空室对应于图1中粗的阴影部分。
为了将玻璃熔体连续输入真空室,必须为真空室设计一个流动通道,降低真空室流动通道内表面与玻璃熔体流之间的摩擦阻力,充分减小流体的压力损失。为了充分减小流体的压力损失,已经设计了真空室流动通道的合适形状和横截面积。然而,因为要求玻璃熔体中产生的气泡能在玻璃熔体连续通过的同时,能够短时间内胀大,使气泡上升到玻璃熔体表面破裂,所以认为需降低玻璃熔体的粘度,即提高玻璃熔体的温度。然而,如上面所述,当玻璃熔体温度提高时,用于真空室流动通道的材料与玻璃熔体间的反应会产生新的气泡,或者这些材料会溶解在玻璃熔体中形成条纹,结果不能保证形成产品的质量。而且,这些材料与玻璃熔体的反应加速了材料的磨蚀,缩短了真空室流动通道的使用寿命。
由玻璃熔体流引起的真空室流动通道的磨蚀速率与t/η,即时间t与玻璃熔体粘度η的比值成正比,其中t代表玻璃熔体通过流动通道的时间,η代表玻璃熔体的粘度。当气泡上升到玻璃熔体表面时,其上升距离与t/η,即玻璃熔体通过流动通道的时间除以其粘度得到的比值的平方成正比。因此,要求确定玻璃熔体粘度在磨蚀速率允许范围内尽量低些,以保持气泡充分的上升高度。
玻璃熔体粘度的较好范围为500-5000泊。而且,要将在这样粘度范围的玻璃熔体中的气泡上升到玻璃熔体表面,气泡的直径应该为10-30毫米。当气泡直径超过30毫米时,到达表面的气泡不会破裂,以泡沫层的形式留在表面。这会降低真空脱气器12中的热传递效率,玻璃熔体本身的温度下降,从而降低真空脱气的效果。
气体分析表明,气泡上升到真空脱气器12中玻璃熔体的表面,放出CO2和H2O。这种情况下,通过直接观察真空脱气器12内部后发现,在低于一定压力的条件下玻璃熔体中的溶解气体如CO2、H2O等容易发生不希望的释放(再沸)。在粘度例如为500-5000泊的玻璃熔体中,在小于0.05大气压的压力条件下会发生这样的再沸,因此,应在这个压力以上进行脱气。
而且,要增加气泡的直径,使气泡在玻璃熔体通过真空室时具有足够的浮力,就要求在真空脱气器12的减压环境下,玻璃熔体中溶解态存在的气体组分能扩散或进入包含在熔制器10的玻璃熔体中的小气泡,如直径为0.05-3毫米的气泡,而不引起再沸。其原因如下。依靠气体组分进入存在于玻璃熔体中的很小的气泡,是难以使气泡长大的,因为在制得玻璃熔体的熔制器10的压力P的条件中,气体组分具有较高的分压。而且,通过增加玻璃熔体中的气体组分来向玻璃熔体鼓泡,从而加速气体组分进入气泡,这种办法实际上并没有充分的效果。
考虑上述内容,可采用这样的方法,让玻璃熔体通过来产生玻璃熔体流;在玻璃熔体经过真空室期间让小气泡长大;在减压环境下长大的气泡上升到真空脱气器12中玻璃熔体的表面破裂,从而除去气泡,而真空脱气时未能抽吸除去的气泡则溶解于经向下管道流动的玻璃熔体中。这种情况下,根据本发明,玻璃熔体在真空室中的停留时间在0.12-4.8小时范围,0.12-0.8小时更好,在真空室中流动的玻璃熔体的重量[吨]除以玻璃熔体的流量Q[吨/小时]可获得停留时间。
本文中,在真空室中流动的玻璃熔体的重量[吨]指真空室(即图1(a)的粗阴影部分)中玻璃熔体的总重量。
若停留时间小于0.12小时,即使玻璃熔体粘度为500-5000泊,并且作用于玻璃熔体的压力为0.05大气压即76[mmHg]或更高,玻璃熔体的气泡密度将超出优良玻璃产品所允许的范围。另一方面,若停留时间大于4.8小时,就要求加长真空室在玻璃熔体流动方向上的长度,会出现设备成本增加的问题。
小于0.8小时的停留时间提供了有效除去气泡,减少挥发性组分从玻璃熔体表面挥发的良好效果。
而且,真空脱气器12中玻璃熔体的深度H[米]和在真空室中流动的玻璃熔体的重量W[吨]应满足下式0.010米/吨<H/W<1.5米/吨H/W宜为0.012米/吨或更大,0.015米/吨或更大则更好。而且H/W宜为1.2米/吨或更小,0.9米/吨或更小则更好。
真空脱气器12中玻璃熔体深度H[米]与玻璃熔体重量W[吨]的比值应在上述范围的原因如下。
如果玻璃熔体在真空脱气器12中的深度H等于0.010×W或更小,由于玻璃熔体流的摩擦阻力引起的压力损失增加,玻璃熔体不可能以预定的流量通过。而如果深度H等于1.5×W或更大,存在于真空脱气器底部或其附近的气泡在玻璃熔体流经在真空脱气器12的时间内来不及上浮到玻璃熔体表面。而且,当玻璃熔体深度超过作为上述范围上限的1.5×W时,作用于真空脱气器底部或其附近的玻璃熔体的压力太高,这些区域玻璃熔体中的气泡的长大就太慢,来不及上升到玻璃熔体表面,就存在气泡随同玻璃熔体从真空脱气器流出的情况。
即使输入真空脱气器12的玻璃熔体达到上述脱气允许范围的上限,也能获得预定的脱气效果。然而,玻璃熔体深度宜为真空脱气器高度的一半。例如,当真空脱气器12的高度为0.2-0.6米时,玻璃熔体的深度应该在0.1-0.3米范围。
图1(a)中,真空脱气器12的内部为长方柱形,流动通道横截面的形状为长方形,玻璃熔体在真空脱气器12中的深度H[米]恒定不变。然而,本发明并不限于真空脱气器内部为长方柱的情况,本发明还可以应用于真空脱气器底面从其上游部分到下游部分逐渐或分段上升或下降,而其顶面保持一定高度的情况。这种情况下,玻璃熔体的深度H[米]是指其玻璃熔体的平均深度。
而且,真空脱气器12内部可以是圆柱体形,其流动通道横截面的形状为圆。这种情况下,玻璃熔体深度H[米]是指沿宽度方向变化的深度中最深部分的深度。此时真空脱气器12的底面从玻璃熔体流动的上游部分到下游部分可以逐渐或分段上升或下降,要确定玻璃熔体的深度H[米],就取玻璃熔体流的平均深度。
如上所述,必须保证溶解的气体尽可能多地进入气泡,使玻璃熔体中的气泡上升破裂。这种情况下,到达玻璃熔体表面的气泡若不破裂,就形成泡沫层。泡沫层具有保温作用,结果玻璃熔体表面温度降低,气泡不会破裂。当泡沫层扩张时,它会铺满真空脱气器12中的玻璃熔体,或与玻璃熔体流一起从真空脱气器12排出。
从这点来说,气泡的破裂是很重要的。然而,气泡的破裂取决于玻璃熔体表面的温度,溶解气体进入气泡的速率以及形成泡沫层每个气泡的表面张力和形成各气泡的玻璃熔体的粘度。因此,当确定了玻璃熔体的配方以及玻璃熔体的真空脱气处理温度后,必须将玻璃熔体与空气接触的表面积(气泡破裂所必需的)和玻璃熔体流量间的关系确定在一预定范围。
就是说,在玻璃熔体通过真空脱气器12内部期间,真空脱气器12由玻璃熔体中的气泡上升到玻璃熔体表面发生破裂,在减压条件下气泡中的气体组分排出到上部空间12s的过程中,本发明中,为使气泡破裂,在减压条件下与上部空间12s接触的玻璃熔体表面积S1[米2](图1(b)所示的粗阴影部分的面积)和玻璃熔体的流量Q[吨/小时]应满足下式0.24米2·小时/吨<S1/Q<12米2·小时/吨更好的应满足下式0.5米2·小时/吨<S1/Q<10米2·小时/吨上式成立的原因如下。如果真空脱气器12中的玻璃熔体表面积S1[米2]等于0.24×Q或更小,上升到玻璃熔体表面的许多气泡会停留在表面,形成在真空脱气器12中不会破裂的泡沫层,这样脱气效果就很差。若表面积S1[米2]等于12×Q或更大,真空脱气器12中的玻璃熔体的深度就太浅,会由于玻璃熔体流的摩擦阻力而使玻璃熔体不能以预定的流量通过。
图1(b)中,减压条件下与上部空间12s接触的玻璃熔体表面为长方形。然而,本发明中,玻璃熔体表面的形状不限于长方形,其形状可以是真空脱气器12内的宽度,可从其上游部分到其下游部分逐渐或分段变窄或变宽。
而且,玻璃熔体中气泡大上升的速率(气泡长大时上升速率增大)与气泡直径的关系取决于Stoke公式。当玻璃熔体的粘度给定时,可根据气泡大小确定气泡上升到玻璃熔体表面所需的时间。例如,若所用玻璃熔体的粘度为500-5000泊,并假定气泡上浮100厘米距离用时60分钟,在500泊情况下气泡的最小直径应该是10毫米,在5000泊情况下气泡的最小直径为30毫米。即,直径为30毫米或更大的气泡一定能在60分钟内脱气除去。这种情况下,上升速率为0.25厘米/秒或更大。
因此,为确保气泡在玻璃熔体流中上升,必须确定玻璃熔体的流量使得其流速小于0.25厘米/秒(例如,当玻璃熔体以500吨/天的流量通过时,真空脱气器12流动通道横截面的面积为9200厘米2或更大,真空脱气器12的流动通道长度约为1米)。
这种情况下,如图1(a)所示,提供向下管道16使玻璃熔体下降,在与向下管道16连接的真空脱气器12的出口或其附近形成下降的流体。当玻璃熔体中的气泡上升速率小于下降流体的下降速率时,玻璃熔体中长大的气泡就被下降流体夹带,而不能在与向下管道16连接的出口或其附近上升到玻璃熔体表面,结果存在排出的玻璃熔体中含有气泡的危险。
因此,本发明中,连接到真空脱气器12的向下管道16横截面的表面积S2[米2](图1(c)中粗阴影部分的面积)和玻璃熔体的流量Q[吨/小时]应满足下式。即,或者是仅向下管道16,或者是向下管道16和向上管道14都应满足下式0.008米2·小时/吨<S2/Q<0.96米2·小时/吨更好应满足0.01米2·小时/吨<S1/Q<0.96米2·小时/吨,尤其应满足,0.01米2·小时/吨<S1/Q<0.1米2·小时/吨应满足上式的原因如下当向下管道16的流动通道横截面面积S2[米2]等于0.008×Q或更小时,在连接向下管道16的出口或其附近,玻璃熔体流的流速的向下矢量就太大,使得气泡被向下管道16中逆向于上浮方向流动的玻璃熔体流所夹带。而流动通道横截面的面积S2[米2]等于0.96×Q或更大时,向下管道16的直径增加,设备的重量和成本增加。
图1(c)所示的实施方案中,流动通道横截面的形状为长方形。然而,本发明不限于这种形状,例如可以使用圆形。
本发明涉及对原在压力P[mmHg]条件下的玻璃熔体进行脱气的真空脱气法。然而,压力P[mmHg]并不必总是大气压的压力。例如,可以是在与大气压力隔离的封闭熔制器内熔制获得玻璃熔体的情况下采用的任意压力。而且,在压力P[mmHg]条件下的玻璃熔体可以不具有自由表面。
下面将参考实施例详细描述本发明对玻璃熔体的真空脱气法。然而,应该理解本发明不受这些具体实施例的限制。
这些实施例中,在下面所述的各种条件下进行玻璃熔体流的脱气,检测脱气处理前后玻璃熔体中所含气泡的数目,即气泡的密度。使用图2所示的真空脱气设备20进行玻璃熔体流的脱气处理。
图2所示的真空脱气设备20是能产生按图2箭头所示玻璃熔体流的设备,该玻璃熔体流是利用在前面槽21和后面的槽28中玻璃熔体的表面差引起的虹吸原理产生的,玻璃熔体则在真空脱气器22中进行脱气。设备20包括制成一体的真空罩壳23、真空脱气器22、向上管道24和向下管道26。在前面的槽21和后面的槽28充满玻璃熔体G,根据真空脱气器22的压力,适当调整真空罩壳23、真空脱气器22、向上管道24和向下管道26高度的位置。
使用的真空罩壳23由具有闸门形状的金属壳制成,用以保持真空脱气器22、向上管道24和向下管道26的气密性。真空罩壳23制成能包容真空脱气器22以及向上管道和向下管道26主要部分的结构;用外面提供的真空泵(图中未示)抽吸空气,提供22、24和26中减压条件,并通过真空脱气器22上形成的开口22a和22b,保持预定压力的减压条件。而且,在真空脱气器22、向上管道24、向下管道26和真空箱体23之间的空间中装有绝热材料27防止热量的散失。
通过对真空罩壳23抽真空,在真空脱气器22、向上管道24、向下管道26中形成大于38[mmHg](0.05大气压)但小于(P0-50)[mmHg](相对于大气压力P0[mmHg])压力的真空室。具体而言,在容器22、向上管道24和向下管道26中形成真空室,比熔化器25中玻璃熔体G液面高Z1距离的水平面以上的所有部分。因此,在真空室中流动的玻璃熔体的重量对应于向上管道24、真空脱气器22和向下管道26中,从比熔化器25中玻璃熔体G液面高Z1距离的水平面直到真空脱气器22中玻璃熔体G表面的区域中所含的玻璃熔体(即存在于图2粗阴影部分中的玻璃熔体)的总重量。
此实施例中,真空脱气器22、向上管道24和向下管道26中流动通道的横截面形状可为圆形或长方形。玻璃熔体流的深度在玻璃熔体流动方向上保持不变。而且,使玻璃熔体流的宽度保持不变,以便在减压条件下与上部空间22s接触的玻璃熔体流表面的形状为长方形。
在表1所示的实施例1-6中,由字母A-E表示玻璃熔体的种类,其组成(%(重量))列于表2,使用上述真空脱气设备20在表1的玻璃熔体温度[℃]下进行脱气处理。
所有实施例1-6中,在开始脱气处理的正常操作之后,在前面槽21和后面槽28抽取玻璃熔体样品,采用边缘光线法检测气泡密度是否在允许的范围。这种情况下,气泡密度的允许范围为1[个/千克]以下。
表1
表2
所有实施例1-6中,如表1所示,真空脱气处理后单位重量中的气泡数目很小,在允许范围以内,不会引起玻璃产品质量的下降。
由上述这些实施例可见,气泡密度都在允许的范围之内,通过提供如下的条件可以有效并确切地获得脱气效果。即将玻璃熔体送入真空室,真空室使玻璃熔体受到的压力大于38[mmHg]但小于(P0-50)[mmHg],在真空室内进行玻璃熔体的脱气,脱气后的玻璃熔体在压力P0[mmHg]的推动下以流量Q[吨/小时]排放,由在真空室流动的玻璃熔体重量W[吨]除以玻璃熔体流量Q[吨/小时]获得的玻璃熔体在真空室中的停留时间在0.12-4.8小时范围。
这些实施例还表明,玻璃熔体在真空脱气器中的深度和表面积,以及其在向上管道或向下管道中流动通道横截面的面积是在预定范围之内。
在比较例中,当玻璃熔体流量Q为16.667[吨/小时](即约400吨/天)时,要求玻璃熔体在真空室内的重量W为13.8[吨];W/Q为0.828[小时],其它条件值列于表1的比较例中。
上面已经详细描述了本发明的玻璃熔体脱气法。然而,本发明不限于上述实施例。例如,如图3所示,真空脱气设备30由熔化器35、进料管34、真空脱气器32、排料管36和后面的槽38构成一整体设备;在进料管34中装有螺杆泵31,用来控制玻璃熔体G的流量;在排料管36中装有螺杆泵39,用来加速玻璃熔体G的排放,结果真空脱气器32中玻璃熔体的表面始终与熔化器35中玻璃熔体G的表面在一水平面上。
由于真空罩壳33内减压的结果,在向上管道34a、真空脱气器32和向下管道36a的部分(即图3粗阴影部分表示的部分)形成能提供大于38[mmHg]但小于(P0-50)[mmHg](相对于大气压力P0)压力的真空室,该部分为熔制器35中的玻璃熔体G的表面到比该表面低距离Z2的水平面之间的区域。因此,在比熔化器35玻璃熔体G的表面低的部分中形成提供(P0-50)[mmHg]或更小压力的真空室,这是由于通过螺杆泵31、39控制玻璃熔体的流量,改变玻璃熔体压力的结果。
因此,在真空室流动的玻璃熔体的重量W[吨]对应于从熔化器35中玻璃熔体G表面与比该玻璃熔体G表面低距离Z2的水平面之间玻璃熔体的重量(图中粗阴影部分的玻璃熔体重量)。
对于本发明,可以在本发明范围进行各种改进和变动。
如上所述,根据本发明进行玻璃熔体流脱气,是将玻璃熔体送入真空室进行玻璃熔体的脱气,该真空室可提供大于38[mmHg]但小于(P0-50)[mmHg](相对于大气压力P0)的压力,脱气后的玻璃熔体在压力P[mmHg]下以流量Q[吨/小时]排放,由在真空室流动的玻璃熔体重量W除以玻璃熔体流量Q[吨/小时]获得的玻璃熔体在真空室内的停留时间为0.12-4.8小时范围,从而可有效并确切地制得不含夹带气泡的玻璃熔体。
而且,将真空脱气器中玻璃熔体的深度和表面的面积以及在向下管道中流动通道的横截面积设置在一预定范围,可有效并确切地制得不含气泡的玻璃熔体。
在压力P[mmHg]下将玻璃熔体输入真空室,使玻璃熔体所受的压力在38[mmHg]-(P-50)[mmHg]范围,对玻璃熔体进行脱气时,玻璃熔体在真空室中的停留时间在0.12—4.8小时范围,从而可达到对玻璃熔体有效脱气的作用。
用于玻璃熔体流的真空脱气法制作方法
- 专利详情
- 全文pdf
- 权力要求
- 说明书
- 法律状态
查看更多专利详情
下载专利文献
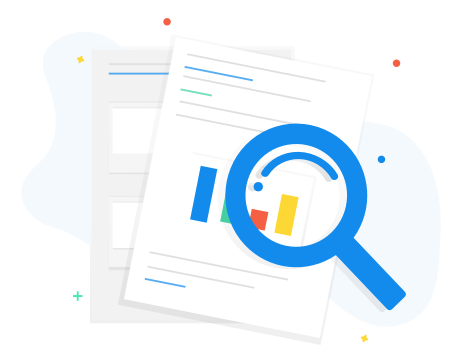
下载专利
同类推荐
-
岸本正一高伯菘, 王坤池王坤池, 王清华王坤池, 王清华方晨航
您可能感兴趣的专利
-
苅谷浩幸, 前田伸广苅谷浩幸, 前田伸广苅谷浩幸, 前田伸广吕文慧, 尹计深吕文慧, 尹计深
专利相关信息
-
李章雨肖湘东朴淳五张艺龄丁体英