一种碳化硅石墨复合材料及其制备方法【技术领域】[0001]本发明属于材料制备【技术领域】,尤其涉及一种粉末冶金、热压烧结制备碳化硅石墨复合材料及其制备方法。[0002][0003]石墨材料具有许多独特的性能,如:是热和电的良导体、高化学稳定性、无熔点、耐高温、热膨胀系数小、抗热震性强等特点,是一种重要的无机非金属材料。石墨本身特殊的层状结构在其沿着C轴方向仅有弱的范德华力结合,层与层之间很容易滑动,使石墨材料具有很优异的润滑性能。[0004]石墨材料传统生产工艺是利用焦炭等固体原料和煤浙青等粘结剂,经混合、磨粉、压制、焙烧、浸溃、石墨化等工序来制造的。制品气孔率高,导致材料的强度低、承载能力下降、耐磨性低以及摩擦失稳,寿命难预测,关键问题是制品生产周期长,成品率不容易控制。应用受到极大限制。通过在石墨材料中加入其它组元可以提高石墨材料的性能,为了提高石墨强度和耐磨蚀性,硅化石墨被大量研究。硅化石墨它不仅具有碳化硅的抗氧化、高硬度、耐化学腐蚀等优点还具有石墨材料的导电导热性、良好的自润滑性及抗热震性广泛地应用于化工、冶金及宇航和核工业领域。另外石墨和碳化硅都属于共价键结合化合物,所以硅化石墨的化学性质非常稳定。除强氧化气体、熔融碱之外,硅化石墨几乎耐所有酸碱腐蚀。此外它的抗电化腐蚀能力也很强。[0005]目前制造硅化石墨的方法有化学气相沉积(CVD)法;化学气相反应法(CVR)和液硅渗透反应法三种。日本已有的专利技术,如特公昭48 -26597、特开昭49- 83706、特开昭 50- 130363、特公昭 48- 26597、特开昭 49- 83706、特开昭 50-130363、特公平 5- 83517等均是在石墨基体材料上形成碳化硅层薄膜,存在的问题是材料表面和内部成分不均匀。美国专利 N0.2,907,972.N0.4,312,954,N0.4,124,667,N0.4,346,049 采用硅和碳化硅 / 碳混合物反应烧结得到复合材料产品,存在游离硅含量高,影响高温使用性能。N0.4,525,461采用无压烧结制备碳化硅石墨复合材料,产品相对密度仅能达到75%左右。
[0006]本发明要解决的技术问题是,现有技术中碳化硅石墨制备方法的原因导致材料的成分不均匀、相对密度低等缺点;本发明采用粉末冶金技术,通过原料种类、粒度、配比的优化,配合热压烧结,制备出超细碳化硅陶瓷粉体弥散强化的石墨复合材料,得到高强度、耐磨损复合石墨材料。
[0007]为实现上述目的,本发明采用如下的技术方案。
[0008]1、一种碳化硅石墨复合材料的制备方法,制备原料为石墨粉末、碳化硅粉末、烧结助剂经球磨混料、干燥、破碎、过筛后模压成型,成型后经脱胶处理后热压烧结,此烧结为控温控压两段保压烧结,随炉冷却得到碳化硅石墨复合材料。[0009]2、上述制备方法的优选方案为,包括以下的制备步骤:
1)将2.2wt9T4.lwt%的烧结助剂,24.3wt%^45.0wt%的碳化硅粉末,其余为石墨粉末的原料与球磨介质进行球磨混料后,经过干燥、破碎、过100-200目筛获得混合粉末;
2)将步骤I)制得的混合粉末模压成型,得到素坯;
3)将步骤2)得到的素坯在氩气环境下,750^8500C,保温3(T60min后冷却至室温进行脱胶;
4)热压烧结,将步骤3)得到的坯料置于热压烧结炉中,在真空状态下,升温至1750°C施加20MPa压力,1800°C施加40MPa压力,随炉冷却得到碳化硅石墨复合材料。
[0010]3、上述制备方法的优选方案为,所述步骤4)的热压工艺为,在真空状态下,以10~15°C /min 升温至 1200°C,以 8~10。。/min 升温至 1600°C,以 5~8°C /min 升温至 1800°C,在1750°C施加20MPa压力,1800°C施加40MPa压力,将真空气氛切换至氩气气氛,保温I~2h进行压力烧结,温度降至1600°C时卸压。采用此种先快速升温再慢速升温方式的目的,是防止样品开裂;而前期真空状态下加压使得坯料更致密化,后期氩气气氛更有利于碳化硅的
烧结
[0011]4、上述制备方法的优选方案为,所述步骤3)在氩气环境下,以5~10°C /min的速度的从室温升温至75(T850°C,保温3(T60min,然后以8~10°C /min降至室温。
[0012]5、上述制备方法的优选方案为,步骤I)中所述碳化硅粉末纯度> 98%,平均粒径小于0.5μπι;石墨粉末纯度≥96%,粒度为1200~1500目胶体石墨。
[0013]6、上述制备方法的优选方案为,步骤I)中所述烧结助剂为氧化铝、氧化钇中的一种或两种任意比例的组合,其粒度为微米级。
[0014]7、上述制备方法的优选方案为,步骤I)中所述球磨介质为无水乙醇。
[0015]8、上述制备方法的优选方案为,步骤I)中所述干燥温度为10(T13(TC,干燥时间为3~5小时。
[0016]9、上述制备方法的优选方案为,步骤2)中所述模压成型的压力为15(T250MPa。
[0017]10、本发明还涉及上述任一种方法制得的碳化硅石墨复合材料,所述材料为超细碳化硅陶瓷粉体弥散强化的石墨复合材料,其抗弯强度大于llOMPa、材料相对密度大于95%。
[0018]本发明的有益效果在于:该方法采用鳞片石墨、碳化硅颗粒为原料,避免了最终产品需要石墨化的过程,大幅度缩减了生产周期,提高了产成品率;采用亚微米碳化硅粉末、氧化铝及氧化钇作为烧结助剂进行液相压力烧结,保证制品高密度、低气孔率,提高了制品的高强度高耐磨性能,同时不含游离硅增加了制品的耐腐蚀性能;又在关键区段进行升温、保温控制,抑制和消除了烧结过程中的裂纹、变形等缺陷。本制备工艺耗时短48~72h,制品强度高其抗弯强度可达到181MPa,相对密度达到95%。
[0019]
[0020]本发明所采用的原材料为胶体石墨1200-1500目,碳化硅粉末D50:0.45um,烧结助剂氧化铝(a-A1203,d50=2.02μπι)和氧化钇(d50=5ym);球磨介质为无水乙醇。
[0021]实施例1将600g粒径为1200目的胶体石墨、200g碳化硅粉末、18g氧化铝,加入1200mL无水乙醇,球磨混料6h,获得混合均匀的浆料待用;
将球磨后的浆料置于鼓风干燥箱中,调节温度到100°C,干燥5个小时,然后粉碎,过200目筛子,得到混合细粉待用;
筛分后的混合料装入钢模中,在压机施加150MPa的单向压力,保压30s,脱模得到素
坯;
将素坯放到真空管式炉中,通入氩气,以5°C /min的速度的从室温升温至800°C,保温Ih脱胶,然后以8°C /min降至室温;
脱胶后的素坯置于真空烧结炉中,在真空状态下以10°C /min升温至1200°C,以8V /min升温至1600°C,以5°C /min升温至1800°C,在1750°C施加20MPa压力,1800°C施加40MPa压力,真空气氛切换至氩气气氛,保温2h进行压力烧结,保温结束后,随炉温冷却至室温得到制品。最终制品抗弯强度达到113MPa。[0022]实施例2
将510g粒径为1500目的胶体石墨、300g碳化娃粉末、20g氧化乾,加入1000mL无水乙醇,球磨混料6h,获得混合均匀的浆料待用;
将球磨后的浆料置于鼓风干燥箱中,调节温度到130°C,干燥3个小时,然后粉碎,过200目筛子,得到混合细粉待用;
筛分后的混合料装入钢模中,在压机施加200MPa的单向压力,保压30s,脱模得到素
坯;
将素坯放到真空管式炉中,通入氩气,以8°C /min的速度的从室温升温至800°C,保温Ih脱胶,然后以8°C /min降至室温;
脱胶后的素坯置于真空烧结炉中,在真空状态下以15°C /min升温至1200°C,以10°C /min升温至1600°C,以8°C /min升温至1800°C,在1750°C施加20MPa压力,1800°C施加40MPa压力,真空气氛切换至氩气气氛,保温Ih进行压力烧结,保温结束后,随炉温冷却至室温得到制品。最终制品抗弯强度达到136MPa。
[0023]实施例3
将170g粒径为1200目的胶体石墨、150g碳化硅粉末、9g氧化铝,4.5g氧化钇,加入1000mL无水乙醇,球磨混料6h,获得混合均匀的衆料待用;
将球磨后的浆料置于鼓风干燥箱中,调节温度到120°C,干燥4个小时,然后粉碎,过200目筛子,得到混合细粉待用;
筛分后的混合料装入钢模中,在压机施加250MPa的单向压力,保压30s,脱模得到素
坯;
将素坯放到真空管式炉中,通入氩气,以10°C /min的速度的从室温升温至750°C,保温30min脱胶,然后以10O /min降至室温;
脱胶后的素坯置于真空烧结炉中,在真空状态下以15°C /min升温至1200°C,以10°C /min升温至1600°C,以8°C /min升温至1800°C,在1750°C施加20MPa压力,1800°C施加40MPa压力,真空气氛切换至氩气气氛,保温Ih进行压力烧结,保温结束后,随炉温冷却至室温得到制品。最终制品抗弯强度达到181MPa。
一种碳化硅石墨复合材料及其制备方法
- 专利详情
- 全文pdf
- 权力要求
- 说明书
- 法律状态
查看更多专利详情
下载专利文献
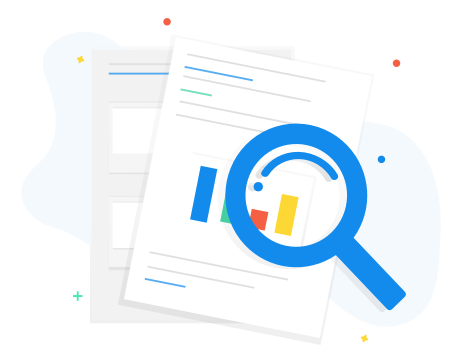
下载专利
同类推荐
-
燕青芝
您可能感兴趣的专利
-
范颖芳, 张世义范颖芳, 张世义丁玉生
专利相关信息
-
邓树军陈凯, 陈树德刘友举方宁象李明照