化学共沉淀法制备偏离化学计量比石榴石相闪烁体粉体的方法[0002]无机闪烁体材料通常用于医学成像、高能物理、工业检测和放射剂量测定等领域。当受到X射线、伽马辐射、紫外线辐射、核辐射时,闪烁体材料可以发射可见光。[0003]一类典型的无机闪烁体材料是钇铝石榴石。钇铝石榴石属于立方晶系,其光学各向同性、无双折射效应、高温蠕变小、高的热稳定性、良好的抗化学腐蚀性被广泛用作发光基质材料。[0004]多晶透明陶瓷与单晶材料相比,其化学稳定性和耐高温性要优于单晶,具有良好的机械加工性能,工艺简单,成本低,制备周期短,尺寸大,掺杂浓度高,可大批量生产等优点。[0005]陶瓷粉体是用于生产多晶透明陶瓷的重要原料。目前国内外制备陶瓷粉体的方法主要分为固相法和湿化学法两大类。其中湿化学法包括溶胶-凝胶法(K.Fujioka等,Journal of Luminescence, 13 (2010) 455-459)、共同沉淀法(Ζ.H.Chen 等,Journal ofAlloys and Compounds, 433(2007) 328-331 ;J.Li 等,Journal of the European CeramicSociety, 32 (2012) 2971-2979)、均匀沉淀法(S.Ramanathan 等,Journal of MaterialsScience Letters,20(2001)2119-2121 ;X.J.Xu 等,Journal of the American CeramicSociety, 95 (2012) 3821-3826)和水热法(Y.Hakuta 等,Materials Research Bulletin,38 (2003) 1257-1265),这些方法各自有其优缺点。[0006]目前,现有的多晶透明陶瓷基本上是符合化学计量比的,然而,有文献显示偏离化学计量比的石榴石相闪烁陶瓷的光输出及余辉性能都有很大的差异(T.Kanai等,Journalof the American Ceramic Society, 91 (2008) 456 - 462),然而,目前尚缺乏简便高效地制备高性能的、偏离化学计量比的石榴石相闪烁陶瓷的方法。[0007]综上所述,虽然目前已经有多种不同构成的陶瓷粉体及制备的多晶透明陶瓷,然而现有多晶透明陶瓷的性能尚难以令人满意,因此,本领域迫切需要开发新的陶瓷粉体、多晶透明陶瓷及其制备工艺。
[0008]本发明的目的在于提供一种偏离化学计量比石榴石相闪烁体粉体、及其制备方法和应用。
[0009] 在本发明的第一方面,提供了一种偏离化学计量比石榴石相闪烁体粉体,所述的石槽石相纳米粉体的化学结构组成如式I所示:
[0010](AB)3U12 (I)[0011]式中,
[0012]A为发光稀土元素,选自下组:Ce、Pr、Nd、Eu、Tb、或其组合;
[0013]B为选自下组的元素:Sc、Y、Gd、Tm、Yb、Lu、或其组合;
[0014]C为选自Al、Ga中的一种或两种的组合;
[0015]-0.5 ≤ δ ≤+0.5 且 δ 关 O。
[0016]在另一优选例中,0.02≤δ≤0.3或-0.3≤δ≤-0.02,较佳地0.05≤δ ≤ 0.2或-0.2 ≤ δ ≤ -0.05。
[0017]在另一优选例中,δ≥0.1或者δ ≤ -0.005。
[0018]在另一优选例中,所述元素A的掺入量为0.01~20wt%,按粉体总质量计。
[0019]在另一优选例中,所述元素B的掺入量为45~75wt%,所述元素C的掺入量为10~40wt%,按粉体总质量计。
[0020]在另一优选例中,所述元素A、B、C和O的质量百分比之和为100%。
[0021]在另一优选例中,所述粉体的粒径为50_200nm。
[0022]在另一优选例中,A为离子状态。
[0023]在另一优选例中,所述的组合包括两种或多种元素的任意组合。
[0024]在本发明的第二方面,提供了一种合成本发明第一方面所述的偏离化学计量比石榴石相闪烁体粉体的方法,该方法步骤如下:
[0025](a)提供第一混合溶液和沉淀剂溶液,
[0026]其中,所述的第一混合溶液是如下制备的:按权利要求1所述的偏离化学计量比石榴石相闪烁体粉体的元素的化学计量比,将元素A、B和C的氧化物或其盐溶于酸性溶液中,得到第一混合溶液;
[0027]所述的沉淀剂溶液含有碱性沉淀剂和分散剂;
[0028](b)在搅拌条件下,将第一混合溶液滴加入所述的沉淀剂溶液中,形成含沉淀物的沉淀液;
[0029](C)从所述的沉淀液中分离获得沉淀物,作为前驱体粉体;和
[0030](d)将上一步骤所得的前驱体粉体进行煅烧,得到偏离化学计量比石榴石相闪烁体粉体。
[0031] 在另一优选例中,在步骤(b)中,还包括通入高反应活性气体,较佳地高反应活性气体选自:氧气、氢气、一氧化碳、二氧化硫或其组合。
[0032]在另一优选例中,步骤(C)的分离包括:对所述沉淀液进行过滤得到沉淀物、洗涤沉淀物、干燥沉淀物、和对沉淀物任选地进行研磨,从而得到前驱体粉体。
[0033]在另一优选例中,所述的干燥方式为微波干燥法。
[0034]在另一优选例中,所述的前驱体粉体的粒径(或平均粒径)为10~lOOnm,较佳地为 15_30nm。
[0035]在另一优选例中,第一混合溶液中,盐浓度为0.01_2mol/L(较佳地为0.01-1mol/L),按A、B和C元素的总量计。
[0036]在另一优选例中,步骤(b)中,混合盐溶液的滴加速度为5_300ml/min,优选为5_150ml/min,更优选为 5-100ml/min。
[0037]在另一优选例中,所述的酸性溶液是含有以下酸的溶液:硝酸、盐酸或其组合。[0038]在另一优选例中,元素A、B和C的盐包括碳酸盐、硫酸盐、硝酸盐、氯化物、碳酸氢盐、或其组合。
[0039]在另一优选例中,沉淀剂与元素A、B和C的用量之比为Ml:M2 = 60~5:1,其中Ml为沉淀剂的摩尔量;M2为元素A、B和C的摩尔总量;和/或
[0040]分散剂与元素A、B和C的用量之比为M3:M2 = 2~0.5:100,其中M3为分散剂的摩尔量;M2为元素A、B和C的摩尔总量。
[0041]在另一优选例中,所述方法具有选自下组的一个或多个特征:
[0042](I)所述的碱性沉淀剂选自下组:氨水、碳酸氢铵或者两者的混合碱;
[0043](2)所述沉淀剂溶液中,沉淀剂的浓度为2-6mol/L;
[0044](3)所述的分散剂选自下组:聚乙烯吡咯烷酮、聚乙二醇、硫酸铵、或其组合;
[0045](4)所述沉淀剂溶液中,分散剂的浓度为2-6mol/L;
[0046](5)所述沉淀剂为氨水和碳酸氢铵的混合物,氨水和碳酸氢铵的摩尔比为1:10-10:1,优选的摩尔比为1:1-8:1 ;
[0047](6)所述沉淀剂为氨水和碳酸氢铵的混合物,该混合物的摩尔浓度为2-5mol/L ;
[0048](7)所述沉淀剂仅为氨水,其摩尔浓度为1-lOmol/L。
[0049]在另一优选例中,步骤(d)的煅烧在马弗炉中进行;
[0050]较佳地,煅烧温度为700°C -1500°C,更佳地煅烧温度为750_1200°C ;保温时间为
0.5-5小时,更佳地保温时间为1-4小时。
[0051]应理解,在本发明范围内中,本发明的上述各技术特征和在下文(如实施例)中具体描述的各技术特征之间都可以互相组合,从而构成新的或优选的技术方案。限于篇幅,在
此不再一一累述。
[0052]图1显示了本发明实施例1中不同煅烧温度所合成的粉体的XRD谱图。
[0053]图2显示了本发明实施例2中不同煅烧温度所合成的粉体的扫描电镜图,其中左图为850°C,右图为9000C ο
[0054]图3显示了实施例3中使用不同比例混合的沉淀剂所合成的粉体的扫描电镜图,左图为氨水/碳酸氢铵摩尔比为1:5,右图为氨水/碳酸氢铵摩尔比为5:1。
[0055]图4显示了本发明实施例4中所述的不同煅烧温度所合成的粉体的室温光致发光谱图。图中显示,当激发波长一定时,本发明粉体的室温光致发光强度随着煅烧温度的升高而增强。
[0056]图5显示了本发明实施例1及实施例5中所述的通入高反应活性气体及不通入高反应活性气体所合成粉体的扫描电镜图。
[0057]图6显示了本发明实施例1的偏化学计量比的粉体及对比例I的符合化学计量比的粉体的室温光致发光谱图。图中显示,当激发波长一定时,本发明的偏化学计量比的粉体的室温光致发光强度较之符合化学计量比的粉体强度高。
[0058]图7显示了实施例1的偏化学计量比的粉体制备的陶瓷及对比例I的化学计量比的粉体制备的陶瓷的XRD谱图。
[0059]图8显示了实施例1的偏化学计量比的粉体制备的陶瓷及对比例I的化学计量比的粉体制备的陶瓷的相对光输出。
[0060]本发明人经过长期而深入的研究,通过改进制备工艺,首次在较低的煅烧温度下合成偏离化学计量比石榴石相闪烁体粉体。本发明的粉体不仅具有优异的分散性而且具有优良的室温光致发光强度,特别适合制备闪烁性能优异的石榴石相块体材料(包括多晶透明陶瓷)。在此基础上,发明人完成了本发明。
[0061 ] 偏离化学计量比石榴石相闪烁体粉体
[0062]如本文所用,术语“本发明粉体”、“本发明闪烁体粉体”或“偏离化学计量比石榴石相闪烁体粉体”可互换使用,指出具有式I所示结构的偏离化学计量比石榴石相闪烁体粉体:
[0063](AB)3+s C5為 (I)
[0064]式中,
[0065]A为发光稀土元素,选自下组:Ce、Pr、Nd、Eu、Tb、或其组合;
[0066]B为选自下组的元素:Sc、Y、Gd、Tm、Yb、Lu、或其组合;
[0067]C为选自Al、Ga中的一种或两种的组合;
[0068]-0.5 ≤ δ ≤ +0.5 且 δ 关 O。
[0069]优选地,0.02 ≤ δ ≤ 0.3 或-0.3 ≤ δ ( -0.02,较佳地 0.05 ≤ δ ^ 0.2或-0.2 < δ ( -0.05。
[0070]更优选地,δ≤0.1或者δ ( -0.005。
[0071]粉体原料
[0072]可用于制备本发明粉体的原料没有特别限制,只要其包括元素Α、Β和C即可,例如氧化物或其盐。
[0073]代表性的元素Α、Β和C的盐包括(但并不限于):碳酸盐、硫酸盐、硝酸盐、氯化物、碳酸氢盐、或其组合:
[0074]典型地,元素Α、B和C的氧化物或其盐包括:
[0075]⑴Ce、Pr、Nd、Eu、Tb的氧化物或其盐;
[0076](ii) Sc、Y、Gd、Tm、Yb、Lu 的氧化物或其盐;
[0077](iii) Al、Ga的氧化物或其盐。
[0078]代表性的化合物包括:碳酸铈、氧化钆、硫酸铝、氧化镓、氧化钕、氧化镥、氧化钇、
氧化镨、硫酸铝铵等。
[0079]在本发明中,元素A、B和C的氧化物或其盐宜为高纯度形式,如纯度> 98%,更佳地≤99%,如约为99.99%ο
[0080]应理解,所述的原料可以仅含有一种元素,也可以含有多种元素(如同时含有元素A和元素C)。
[0081]典型地,元素A的掺入量为0.01~20wt%,按粉体总质量计。
[0082]更佳地,元素B的掺入量为45~75wt%,元素C的掺入量为10~40wt%,按粉体总
质量计。
[0083]沉淀剂[0084]可用于制备本发明粉体的沉淀剂没有特别限制,只要其包括氨水、碳酸氢铵即可。
[0085]在本发明中,沉淀剂溶液中沉淀剂的浓度一般为Ι-lOmol/L,较佳地为2-6mol/L。
[0086]应理解,所述的沉淀剂可以是氨水、碳酸氢铵的一种,也可以是两者的混合。
[0087]典型地,沉淀剂为氨水和碳酸氢铵的混合物,氨水和碳酸氢铵的摩尔比为1:10-10:1,优选的摩尔比为1:1-8:1。
[0088]应理解,所述氨水和碳酸氢铵的摩尔比为NH3与NH4HCO3的摩尔比。
[0089]典型地,沉淀剂为氨水和碳酸氢铵的混合物,该混合物的摩尔浓度为2-5mol/L。
[0090]典型地,沉淀剂仅为氨水,其摩尔浓度为1-lOmol/L。
[0091]分散剂
[0092]可用于制备本发明粉体的原料没有特别限制,只要其包括聚乙烯吡咯烷酮、聚乙
二醇、硫酸铵即可。
[0093]在本发明中,代表性的分散剂包括(但并不限于):聚乙烯吡咯烷酮、聚乙二醇、硫酸铵、或其组合。
[0094]在本发明中,沉淀剂溶液中分散剂浓度可按其种类进行确定,通常分散剂的浓度为 l-10mol/L,较佳地为 2-6mol/L。
[0095]制法
[0096]本发明还提供了制备本发明粉体的方法。通常,该方法包括:
[0097](a)提供第一混合溶液和沉淀剂溶液,
[0098]其中,所述的第一混合溶液是如下制备的:按本发明式I所示石榴石相纳米粉体元素的化学计量比,将元素A、B和C的氧化物或其盐溶于酸性溶液中,得到第一混合溶液;
[0099]所述的沉淀剂溶液含有碱性沉淀剂和分散剂;
[0100](b)在搅拌条件下,将第一混合溶液滴加入所述的沉淀剂溶液中,形成含沉淀物的沉淀液;
[0101](C)从所述的沉淀液中分离获得沉淀物,作为前驱体粉体;
[0102](d)将上一步骤所得的前驱体粉体进行煅烧,得到偏离化学计量比石榴石相闪烁体粉体。
[0103]在另一优选例中,一种代表性的制备方法包括如下步骤:
[0104]I)按一定比例将含 Sc、Y、Gd、Tm、Yb、Lu、Ce、Pr、Nd、Eu、Tb、Al、Ga 元素的氧化物
或其他形式的盐先溶解于酸液中形成混合盐溶液,混合盐溶液浓度为0.01-1.0mol/L,记为溶液A ;
[0105]2)氨水、碳酸氢铵的一种或者两者的混合,加入去离子水,搅拌均匀,配置浓度为
0.5-15mol/L的沉淀剂溶液,记为溶液B ;
[0106]3)在溶液B中加入聚乙烯吡咯烷酮、聚乙二醇、硫酸铵、聚丙烯酸铵之一的分散剂,搅拌均匀,记为溶液C ;
[0107]4)将溶液A的混合盐溶液以5-300ml/min的速度滴加到溶液C的混合溶液中,并剧烈搅拌,得到沉淀液;
[0108]5)在步骤4)中的沉淀液中通入高反应活性气体;
[0109]6)将沉淀液经压滤,洗涤,干燥,研磨得到前驱体粉;
[0110]7)将前驱体粉在700°C _1500°C保温煅烧0.5-5小时,得到石榴石相纳米粉体。[0111]本发明的主要优点包括:
[0112](a)本发明石榴石相闪烁体粉体的分散性好,不易团聚;
[0113](b)本发明石榴石相纳米粉体具有优异的室温光致发光强度。
[0114](C)本发明石榴石相纳米粉体具有优异的烧结活性。
[0115]实施例1
[0116]本实施例中,偏离化学计量比石榴石相闪烁体粉体的元素分子式为Ce0.Q2Gd3^85Al3.Q02Ga1.793012,该粉体的制备方法如下:
[0117](a)按化学计量比称取碳酸铈、氧化钆、硫酸铝、氧化镓,将其溶解于硝酸与盐酸的混合酸中,配置浓度为0.5mol/L的混合盐溶液;
[0118](b)选用氨水、碳酸氢铵的混合碱为沉淀剂,配置浓度为3mol/L的沉淀剂溶液,其中氨水/碳酸氢铵摩尔比为1:3 ;
[0119](c)在上述沉淀剂溶液中加入分散剂聚乙烯吡咯烷酮(分散剂与元素A、B和C的用量之比为0.5:100)制备得到混合沉淀剂;
[0120](d)将步骤(a)所得的混合盐溶液以30ml/min的速度滴加入步骤(C)所得的混合沉淀剂中,强 力搅拌,得到沉淀液;
[0121](f)在步骤(d)所得沉淀液中通入氢气作为高反应活性气体;
[0122](g)将步骤(f)所得沉淀液经压滤,洗涤,干燥,研磨得到前驱体粉末;
[0123](h)将步骤(g)所得前驱体粉末分别在800°C、825°C、850°C、900°C、1100°C保温煅烧3小时,得到偏离化学计量比石榴石相纳米粉体。
[0124]结果:
[0125]对制得的偏离化学计量比石榴石相纳米粉体进行物相分析、粉体形貌等检测。
[0126]不同煅烧温度所合成的粉体的XRD图见附图1,从图1可以看出当煅烧温度达到825°C时煅烧前驱体即可得到纯相的石榴石相纳米粉体。
[0127]实施例2
[0128]本实施例中,偏离化学计量比石榴石相闪烁体粉体的元素分子式为Nd0.008LuL5YL 486Al5.006012,该粉体的制备方法如下:
[0129](a)按化学计量比称取氧化钕、氧化镥、氧化钇、硝酸铝,将其溶解于硝酸与盐酸的混合酸中,配置浓度为0.3mol/L的混合盐溶液;
[0130](b)选用氨水为沉淀剂,配置浓度为5mol/L的沉淀剂溶液;
[0131](c)在上述沉淀剂溶液中加入分散剂硫酸铵(分散剂与元素A、B和C的用量之比为1.5:100)制备得到混合沉淀剂;
[0132](d)将步骤(a)所得的混合盐溶液以50ml/min的速度滴加入步骤(C)所得的混合沉淀剂中,强力搅拌,得到沉淀液;
[0133](f)在步骤(d)所得沉淀液中通入氢气作为高反应活性气体;
[0134](g)将步骤(f)所得沉淀液经压滤,洗涤,干燥,研磨得到前驱体粉末;
[0135](h)将步骤(g)所得前驱体粉末分别在8501:、9001:1:保温煅烧1.5小时,得到偏离化学计量比石榴石相纳米粉体。
[0136]结果:
[0137]不同煅烧温度所合成的粉体的微观形貌见附图2,从图2可以看出当煅烧温度为850°C时所制备的偏离化学计量比石榴石相闪烁体粉体颗粒呈类球形,大小均一;当煅烧温度为900°C时所制备的偏离化学计量比石榴石相闪烁体粉体,一部分颗粒长大成片状,对比可知煅烧温度为850°C时所制备的偏离化学计量比石榴石相闪烁体粉体具有更好的分散性。
[0138]此外,XRD测试也表明,制备的粉体为纯相的石榴石相。
[0139]实施例3
[0140]本实施例中,偏离化学计量比石榴石相闪烁体粉体的元素分子式为Pr0.0isGd3.285AI2.875^^1.825。12, 该粉体的制备方法如下:
[0141](a)按化学计量比称取氧化镨、氧化钆、硫酸铝铵、氧化镓,将其溶解于硝酸中,配置浓度为0.3mol/L的混合盐溶液;
[0142](b)选用氨水、碳酸氢铵的混合碱为沉淀剂,配置浓度为3mol/L的沉淀剂溶液,其中氨水/碳酸氢铵摩尔比为1:5及5:1 ;
[0143](c)在上述沉淀剂溶液中加入分散剂聚乙二醇(分散剂与元素A、B和C的用量之比为0.7:100)制备得到混合沉淀剂;
[0144](d)将步骤(a)所得的混合盐溶液以40ml/min的速度滴加入步骤(C)所得的混合沉淀剂中,强力搅拌,得到沉淀液;
[0145](f)在步骤(d)所得沉淀液中通入氧气作为高反应活性气体;
[0146](g)将步骤(f)所得沉淀液经压滤,洗涤,干燥,研磨得到前驱体粉末;
[0147](h)将步骤(g)所得前驱体粉末分别在950°C保温煅烧1.5小时,得到偏离化学计量比石榴石相纳米粉体。
[0148]结果:
[0149]使用按不同比例混合的两种混合沉淀剂所制备粉体的微观形貌见附图3,其中左图为氨水/碳酸氢铵摩尔比为1: 5,从图中可以看出所得粉体颗粒大小不均一,粒径为50~150nm;右图为氨水/碳酸氢铵摩尔比为5:1,从图中可以看出所得粉体颗粒大小均一,粒径约为lOOnm。
[0150]实施例4:
[0151]本实施例中,偏离化学计量比石榴石相闪烁体粉体的元素分子式为Ce0.008Gd2.5Y0.486AI5.0O6O12,该粉体的制备方法如下:
[0152](a)按化学计量比称取碳酸铈、氧化钆、氧化钇、硫酸铝,将其溶解于硝酸中,配置浓度为0.lmol/L的混合盐溶液;
[0153](b)选用氨水、碳酸氢铵的混合碱为沉淀剂,配置浓度为3mol/L的沉淀剂溶液,其中氨水/碳酸氢铵摩尔比为1:3 ;
[0154](c)在上述沉淀剂溶液中加入分散剂聚乙二醇(分散剂与元素A、B和C的用量之比为1:100)制备得到混合沉淀剂;
[0155](d)将步骤(a)所得的混合盐溶液以15ml/min的速度滴加入步骤(C)所得的混合沉淀剂中,强力搅拌,得到沉淀液;
[0156](f)在步骤(d)所得沉淀液中通入二氧化硫作为高反应活性气体;
[0157](g)将步骤(f)所得沉淀液经压滤,洗涤,干燥,研磨得到前驱体粉末;
[0158](h)将步骤(g)所得前驱体粉末分别在850°C、950°C、105(rC、110(rC保温煅烧2小时,得到偏离化学计量比石榴石相纳米粉体。
[0159]结果:
[0160]对本实施例所制备的偏离化学计量比石榴石相纳米粉体进行室温光致发光测试,结果如附图4所示。预设输出光波长为Xem=540nm时,得到不同煅烧温度所合成的偏化学计量比的石榴石相粉体的发光谱图如图4左侧所示,可知当输入光波长在λ = 450nm处时偏化学计量比的石榴石相粉体的发光强度最优;当设定输入光波长为λ ex=450nm时,得到不同煅烧温度所合成的偏化学计量比的石榴石相粉体的发光谱图如图4右侧所示。从图4右侧谱图中可以看出,随着煅烧温度的升高,所得粉体的室温光致发光强度逐渐增大。
[0161]实施例5:
[0162]不通入高反应活性气体
[0163]重复实施例1,不同点在于,在步骤(d)所得沉淀液中不通入高反应活性气体。[0164]结果:
[0165]实施例1和实施例5所制备的粉体的微观形貌见附图5,左图为实施例1中在步骤(d)所得沉淀液中通入高反应活性气体所得粉体的微观形貌图,右图为实施例5中在步骤(d)所得沉淀液中不通入高反应活性气体所得粉体的微观形貌图,对比可知未通入高反应活性气体所制备得到的粉体的颗粒大小不均一,有较多团聚。
[0166]这表明,在通入高反应活性气体时所制备得到的粉体的质量更优。
[0167]对比例1:
[0168]符合化学计量比石榴石相闪烁体粉体
[0169]制法同实施例1,不同点在于,石榴石相闪烁体粉体的元素分子式为Ce0.02^?2.98-ΑΙ3.1sgGa^861O12Q
[0170]结果:
[0171]对实施例1所制备的偏离化学计量比的粉体和对比例I所制备的符合化学计量比的粉体进行室温光致发光测试,所得结果如附图6。预设输出光波长为λ em=540nm时,得到偏化学计量比和化学计量比的石榴石相粉体的发光谱图如图6左侧所示,可知当输入光波长在λ =450nm处时偏化学计量比和化学计量比的石榴石相粉体的发光强度最优;当设定输入光波长为λ ex=450nm时,得到偏化学计量比和化学计量比的石榴石相粉体的发光谱图如图6右侧所示。从图6右侧谱图中可以看出偏化学计量比的粉体具有更高的室温光致发光强度,相比与化学计量比的石榴石相粉体的室温光致发光强度,偏化学计量比的石榴石相粉体的室温光致发光强度增加了 125%。
[0172]实施例6
[0173]制备块状多晶陶瓷
[0174]将实施例1和对比例I的粉体进行如下后处理:
[0175](I)将煅烧所得粉体进行干压成型得到片体;
[0176](2)将已成型的片体进行冷等静压处理;
[0177](3)将已冷等静压的素坯进行烧结,得到陶瓷块体。
[0178]结果:
[0179]分别对使用实施例1及对比例I的粉体所制备的陶瓷块体进行物相分析,其XRD谱图见附图7,从图7中可以看出使用实施例1的粉体所制备的陶瓷主要为石榴石相(G相),同时也检测到微量的钙钛矿相(P相),而使用对比例I的粉体所制备的陶瓷仅包含石榴石相(G相)。
[0180]分别对使用实施例1及对比例I的粉体所制备的陶瓷块体进行光输出测试,其相对光输出谱图见附图8,从附图8中可以看出使用实施例1的粉体所制备的陶瓷比使用对比例I的粉体所制备的陶瓷具有更高的光输出强度,相比于使用对比例I的粉体所制备的陶瓷的光输出强度,使用实施例1的粉体所制备的陶瓷的光输出强度增强了 28%。[0181]在本发明提及的所有文献都在本申请中引用作为参考,就如同每一篇文献被单独引用作为参考那样。此外应理解,在阅读了本发明的上述讲授内容之后,本领域技术人员可以对本发明作各种改动或修改,这些等价形式同样落于本申请所附权利要求书所限定的范围。
化学共沉淀法制备偏离化学计量比石榴石相闪烁体粉体的方法
- 专利详情
- 全文pdf
- 权力要求
- 说明书
- 法律状态
查看更多专利详情
下载专利文献
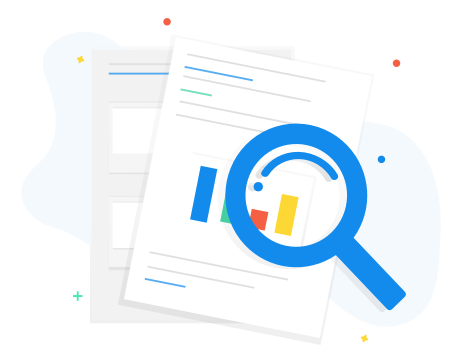
下载专利
同类推荐
-
J·S·德夫, T·托德
您可能感兴趣的专利
-
S·L·多尔, S·文卡塔拉曼尼陈凯, 陈树德陈凯, 陈树德陈凯, 陈树德李明照
专利相关信息
-
埃胡德·马罗姆, 迈克尔·米治里特斯基I·基拉伊徐菊梅