专利名称:一种硫系玻璃预形体的热压成型方法硫系玻璃(chalcogenide glass)是以硫化物,硒化物和铺化物为主要成分的玻璃。硫系玻璃对于中远红外波段的光线可透,是一种重要的红外材料。今年来,由于稀土元素,尤其是锗(Ge)的价格上升,使得原来很多用到锗单晶作为红外材料的应用开始使用成本相对较低的硫系玻璃作为替代材料。另一方面,锗单晶作为晶体材料,无法热压成型,只能用成本高昂的单点金刚石车床加工成非球面透镜。而硫系玻璃作为玻璃态的物质可以进行热压处理。现在通用的生产工艺是采用表面抛光的硫系玻璃预形体在高温下精密压型,从而直接压型出非球面透镜。相对于锗单晶的车削加工,硫系玻璃的精密成型生产效率高,适合大规模自动化生产,降低了中远红外的透镜的成本,直接导致了民用中远红外透镜市场的兴起,比如被动式汽车夜视。用于精密压型的硫系玻璃预形体一般为球透镜,双凸透镜或平凸透镜。其中球透镜使用最为普遍,一般球直径为3mm到15_。硫系玻璃的生产需要在圆形的真空石英玻璃管中熔炼,所以生产的玻璃原材料都为圆柱状,直径为50mm到200mm.目前的球透镜的加工方式为首先从大块的硫系玻璃原材料切出比球透镜略大的立方体,然后将立方体研磨成球坯,最后将球坯精磨,抛光成球透镜。这样硫系玻璃的利用率从最初玻璃原材料到最终的球透镜只有17%左右,浪费严重。考虑到硫系玻璃的市场价格约为每克10到13人民币之间,这样红外材料的成本会占到最终透镜成本的50%以上。本发明设计了一套热压成型装置,采用一种热压方法将预先切好的硫系玻璃圆盘直接压成多个球坯。然后再由球坯精磨和抛光成球透镜。这样硫系玻璃材料的利用率可由原来的17%提高到80%左右,极大地降低了红外透镜的成本。图1是热压成型装置的剖面图;图2是上下模具和上下夹具的装配示意图;图3是上模具的结构图。;下面对发明作更详细描述,类似标记表示相同或类似部件。然而,为了更好的理解,附图中所示的部件是示意性表示,它们是按比例绘制的,即该附图的部件不表示真实尺寸,这些真是尺寸对本领域普通技术人员来说都是公知的,因此无需进行详细描述。
参考图1热压成型装置的 剖面图。上模具I和下模具2都由高温不锈钢制造,其中对硫系玻璃的压型面由单点金刚石数控机床加工半球形的模穴阵列10,模穴内壁的粗糙度Ra要小于30nm,主要是为了便于拔模。上下模具1、2的直径范围在100到150mm之间。 硫系玻璃圆片8的直径取决于玻璃锭料的尺寸,但不能超过上下模具的直径。硫系玻璃圆片8的厚度要略小于最终压型后球还的直径,一般为球还直径的90%。石英玻璃罩6为圆形中空石英管,外径范围为180mm到200mm之间,厚度为T5mm之间。石英玻璃罩密封镶嵌在压型机器的上下底座7、11上,并可以通过提高上底座的高度而打开。加热电阻丝5均匀分布缠绕在石英玻璃罩外围,其总共加热功率在5kw到8kw之间。
参考图3上模具的结构图。上模具I非压型表面由中心到边缘径向分布散热气槽。 下模具2的结构与上模具I完全一致。
参考图2上下模具和夹具的装配示意图。上模具I和上夹具3的圆盘表面贴合。 上夹具3的轴为中空,与上模具I装配后轴向的空隙与散热气槽9形成通路。下模具2和下夹具4的装配于上述一致。上下夹具2、4的材质与上下模具1、2的材质相同,都为高温不锈钢,主要为了使在高温下的热膨胀系数一致。
下面具体介绍压型过程。首先打开密封的石英玻璃罩6,放置硫系玻璃圆片8在下模具2中心位置。闭合石英玻璃罩6,然后开始通过上下夹具3、4与上下模具1、2的轴间隙和散热气槽抽真空,直至内部气压达到O. 1MPA。这时加热电阻丝5开始工作,红外线穿透石英玻璃罩辐射并使得上下模具的温度达到高于硫系玻璃的转变温度Tg值100度到 120度之间。当上下模具1、2充分受热均匀后开始压型,压型时上模具I和上夹具3向下移动并对硫系玻璃圆盘8施加压力,压力为20kg到50kg之间,直到上下模具1、2闭合。这时硫系玻璃完全软化并具有非常黏滞的流动性,在压力的作用下硫系玻璃会充满整个球形模穴。模具闭合后关闭加热电阻丝5,并向下模具2和下夹具4的轴向缝隙输入氮气,氮气流过下模具2和上模具I的散热气槽,通过上模具I的与上夹具3的轴向缝隙抽出。通过控制氮气的输气速率,可以控制上下模具1、2的降温速率,降温速率控制在10度到20度每分钟。当上下模具1、2的温度降到低于硫系玻璃转变温度Tg值120度时,可以加大氮气输气量以快速降温。
当上下模具1、2冷却到室温时,抬升上模具I和上夹具3。由于硫系玻璃冷却后体积收缩,其球坯会与上模具2剥离,而留在下模具I的模穴中。打开石英 玻璃罩,用塑料镊子取出各个硫系玻璃球坯。最后用软布蘸酒精清理上下模的硫系玻璃残渣,以备下次热压成型使用。
本发明涉及一种硫系玻璃预形体的热压成型方法,特别介绍了一种加工硫系玻璃球透镜毛坯的高温成型方法;是由一套热压成型装置,采用一种热压方法将预先切好的硫系玻璃圆盘直接压成多个球坯,再由球坯精磨和抛光成球透镜。这样硫系玻璃材料的利用率可由原来的17%提高到80%左右,能极大地提高硫系玻璃的材料利用率,降低了红外透镜的成本。
一种硫系玻璃预形体的热压成型方法
- 专利详情
- 全文pdf
- 权力要求
- 说明书
- 法律状态
查看更多专利详情
下载专利文献
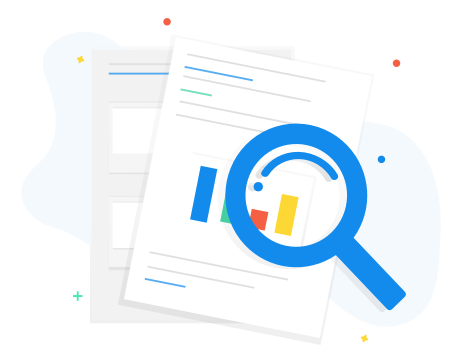
下载专利
同类推荐
-
岸本正一高伯菘, 王坤池王坤池, 王清华王坤池, 王清华彭威方晨航
您可能感兴趣的专利
-
苅谷浩幸, 前田伸广苅谷浩幸, 前田伸广秦升益秦升益秦升益秦升益吕文慧, 尹计深
专利相关信息
-
吕文慧, 尹计深肖湘东肖湘东王小锋张艺龄丁体英李延祚