一种超大超薄液晶显示面板化学蚀刻减薄方法[0002]液晶面板的减薄方法主要有物理减薄和化学蚀刻减薄两种方法,其中物理减薄平整度难以达到要求,化学蚀刻减薄具备效率高、配方简单、产量大、均匀性好等特点。随着显示面板行业的发展,液晶显示面板逐渐朝超薄方向发展,另一方面厂商从成本考虑逐渐朝超大尺寸方向发展;超大超薄产品在化学蚀刻薄化后表面存在矩阵点及凹点,按照点大小CF面0.15mm,TFT面0.25mm,抛光之前产品的良率是15_30%,因此几乎所有面板都需要进行表面抛光处理。另外,由于现有的抛光机尺寸受限,以及超大超薄产品搬运过程操作不便,因此超大超薄显示面板难以实现抛光。
[0003]为了克服现有技术的不足,提升TFT玻璃薄化后的表面效果,抑制薄化后玻璃表面矩阵点及凹点出现,本发明提供一种化学蚀刻减薄方法,该方法通过特殊配方和工艺条件改变化学反应的机理,使薄化后显示面板表面效果良好,从而无需进行抛光。[0004]为了达到上述目的,本发明采取的技术方案如下:[0005]一种超大超薄液晶显示面板化学蚀刻减薄方法,该方法包含以下步骤:[0006]1.对来料显示面板四周用UV固化胶水进行封胶保护,并洗净显示面板表面;[0007]2.通过泵依次向密闭容器 中打入浓硫酸、浓硝酸、浓盐酸及氢氟酸,在密闭容器中加热至25~30°C,同时鼓泡搅拌均匀;
[0008]3.将混合酸打入蚀刻设备中,蚀刻设备中的温度控制在28~32 °C,持续鼓泡搅拌30~60分钟至混合均匀;
[0009]4.将需要薄化的TFT基板浸泡在混合酸液中持续薄化,直至达到目标厚度;
[0010]5.待TFT基板薄化至目标厚度后,将薄化后的TFT基板浸泡在KOH溶液中,中和玻璃表面的酸液。
[0011]6.取出KOH溶液中的TFT基板,对其表面进行烘干处理,按照点大小CF面0.15mm,TFT面0.25mm标准检验表面良率。
[0012]进一步地,步骤2中浓硫酸的浓度为70%,浓硝酸的浓度为69%,浓盐酸的浓度为30%,氢氟酸浓度为40%。
[0013]进一步地,步骤2中浓硫酸体积:浓硝酸体积:浓盐酸体积:氢氟酸体积为92-96%:1 ~3%:1-2%:2-3%ο
[0014]更进一步地,步骤2中浓硫酸体积:浓硝酸体积:浓盐酸体积:氢氟酸体积为94%: 2%: 1.5%: 2.5%ο
[0015]进一步地,步骤2中密闭容器中混合酸液的温度控制在27°C。[0016]进一步地,步骤3中蚀刻设备中的温度控制在30°C,鼓泡搅拌时间为45分钟。
[0017]进一步地,步骤5中KOH的浓度为3%。
[0018]进一步地,步骤5中薄化后的TFT基板在KOH溶液中的浸泡时间为150s~200s。
[0019]更进一步地,步骤5中薄化后的TFT基板在KOH溶液中的浸泡时间为180s。
[0020]采用本发明提供的超大超薄液晶显示面板化学蚀刻减薄方法,能够有效抑制减薄后显示面板玻璃表面矩阵点以及凹点,按照点大小CF面0.15mm, TFT面0.25mm的检验规格进行检验,结果显示表面效果良好,一次良率超过97.5%。本发明的方法过程简单,易操作,无需进行抛光,适用于各种尺寸的液晶显示面板,尤其是超大超薄液晶显示面板。
[0021]图1是本发明的工艺流程图。
[0022]为了使本发明的目的、技术方案及优点更加清楚明白,下面结合附图及实施例,对本发明进行进一步详细说明。应当理解,此处所描述的具体实施例仅用以解释本发明,并不用于限定本发明。
[0023]实施例1
[0024]取10片原材料为康宁玻璃相同厂家同一批次的显不面板,厚度为1.0OOmm,尺寸为 1100X 1300mm,依次编号为 A、B、C、D、E、F、G、H、1、J。
[0025]先在四周CF面和TFT面间隙中渗透UV胶水,再用UV光照固化,用清洗溶剂洗净玻璃表面;通过泵依次向密闭容器中打入70%的浓硫酸1860 L,69%的浓硝酸40 L,30%的浓盐酸40 L,40%的氢氟酸60 L,在密闭容器中将混合酸液加热至26°C,同时鼓泡搅拌均匀;然后将混合酸液打入蚀刻机中,蚀刻机内的温度控制在28°C,持续鼓泡搅拌60分钟至混合均匀;将需要薄化的显示面板浸泡在混合酸液中持续薄化,直至达到目标厚度0.5mm ;从混合酸液中取出薄化后的显示面板,放在3%的KOH溶液中浸泡170s,从KOH溶液中取出显示面板,对其表面进行烘干处理。
[0026]按照点大小CF面0.15mm, TFT面0.25mm标准检验薄化后显示面板的表面良率,结果如表1所示。
[0027]实施例2
[0028]取10片原材料为板硝子AN100玻璃相同厂家同一批次的显示面板,厚度为1.0OOmm,尺寸为 1100X 1300mm,依次编号为 A、B、C、D、E、F、G、H、1、J。
[0029]先在四周CF面和TFT面间隙中渗透UV胶水,再用UV光照固化,用清洗溶剂洗净玻璃表面;通过泵依次向密闭容器中打入70%的浓硫酸1900 L,69%的浓硝酸20 L,30%的浓盐酸30 L ,40%的氢氟酸50 L,在密闭容器中将混合酸液加热至28°C,同时鼓泡搅拌均匀;然后将混合酸液打入蚀刻机中,蚀刻机内的温度控制在29°C,持续鼓泡搅拌50分钟至混合均匀;将需要薄化的显示面板浸泡在混合酸液中持续薄化,直至达到目标厚度0.5mm ;从混合酸液中取出薄化后的显示面板,放在3%的KOH溶液中浸泡150s,从KOH溶液中取出显示面板,对其表面进行烘干处理。
[0030]按照点大小CF面0.15mm, TFT面0.25mm标准检验薄化后显示面板的表面良率,结果如表1所示。
[0031]实施例3
[0032]取10片原材料为康宁玻璃相同厂家同一批次的显不面板,厚度为1.0OOmm,尺寸为 1100X 1300mm,依次编号为 A、B、C、D、E、F、G、H、1、J。
[0033]先在四周CF面和TFT面间隙中渗透UV胶水,再用UV光照固化,用清洗溶剂洗净玻璃表面;通过泵依次向密闭容器中打入70%的浓硫酸1880 L,69%的浓硝酸50 L,30%的浓盐酸30 L , 40%的氢氟酸40 L,在密闭容器中将混合酸液加热至29°C,同时鼓泡搅拌均匀;然后将混合酸液打入蚀刻机中,蚀刻机内的温度控制在30°C,持续鼓泡搅拌40分钟至混合均匀;将需要薄化的显示面板浸泡在混合酸液中持续薄化,直至达到目标厚度0.5mm ;从混合酸液中取出薄化后的显示面板,放在3%的KOH溶液中浸泡190s,从KOH溶液中取出显示面板,对其表面进行烘干处理。
[0034]按照点大小CF面0.15mm, TFT面0.25mm标准检验薄化后显示面板的表面良率,结果如表1所示。 [0035]实施例4
[0036]取10片原材料为板硝子AN100玻璃相同厂家同一批次的显示面板,厚度为1.0OOmm,尺寸为 1100X 1300mm,依次编号为 A、B、C、D、E、F、G、H、1、J。
[0037]先在四周CF面和TFT面间隙中渗透UV胶水,再用UV光照固化,用清洗溶剂洗净玻璃表面;通过泵依次向密闭容器中打入70%的浓硫酸1920 L,69%的浓硝酸20 L,30%的浓盐酸20 L , 40%的氢氟酸40 L,在密闭容器中将混合酸液加热至30°C,同时鼓泡搅拌均匀;然后将混合酸液打入蚀刻机中,蚀刻机内的温度控制在32°C,持续鼓泡搅拌55分钟至混合均匀;将需要薄化的显示面板浸泡在混合酸液中持续薄化,直至达到目标厚度0.5mm ;从混合酸液中取出薄化后的显示面板,放在3%的KOH溶液中浸泡200s,从KOH溶液中取出显示面板,对其表面进行烘干处理。
[0038]按照点大小CF面0.15mm, TFT面0.25mm标准检验薄化后显示面板的表面良率,结果如表1所示。
[0039]实施例5
[0040]取10片原材料为板硝子AN100玻璃相同厂家同一批次的显示面板,厚度为
1.0OOmm,尺寸为 1100X 1300mm,依次编号为 A、B、C、D、E、F、G、H、1、J。
[0041]先在四周CF面和TFT面间隙中渗透UV胶水,再用UV光照固化,用清洗溶剂洗净玻璃表面;通过泵依次向密闭容器中打入70%的浓硫酸1840 L,69%的浓硝酸60 L,30%的浓盐酸40 L,40%的氢氟酸60 L,在密闭容器中将混合酸液加热至25°C,同时鼓泡搅拌均匀;然后将混合酸液打入蚀刻机中,蚀刻机内的温度控制在31 °C,持续鼓泡搅拌30分钟至混合均匀;将需要薄化的显示面板浸泡在混合酸液中持续薄化,直至达到目标厚度0.5mm ;从混合酸液中取出薄化后的显示面板,放在3%的KOH溶液中浸泡160s,从KOH溶液中取出显示面板,对其表面进行烘干处理。
[0042]按照点大小CF面0.15mm, TFT面0.25mm标准检验薄化后显示面板的表面良率,结果如表1所示。
[0043]实施例6
[0044]取10片原材料为康宁玻璃相同厂家同一批次的显不面板,厚度为1.0OOmm,尺寸为 1100X 1300mm,依次编号为 A、B、C、D、E、F、G、H、1、J。
[0045]先在四周CF面和TFT面间隙中渗透UV胶水,再用UV光照固化,用清洗溶剂洗净玻璃表面;通过泵依次向密闭容器中打入70%的浓硫酸1880 L,69%的浓硝酸40 L,30%的浓盐酸30 L ,40%的氢氟酸50 L,在密闭容器中将混合酸液加热至27°C,同时鼓泡搅拌均匀;然后将混合酸液打入蚀刻机中,蚀刻机内的温度控制在30°C,持续鼓泡搅拌45分钟至混合均匀;将需要薄化的显示面板浸泡在混合酸液中持续薄化,直至达到目标厚度0.5mm ;从混合酸液中取出薄化后的显示面板,放在3%的KOH溶液中浸泡180s,从KOH溶液中取出显示面板,对其表面进行烘干处理。
[0046]按照点大小CF面0.15mm, TFT面0.25mm标准检验薄化后显示面板的表面良率,结果如表1所示。
[0047]表1采用本发明的方法薄化后的显示面板玻璃表面良率
[0048]
一种超大超薄液晶显示面板化学蚀刻减薄方法
- 专利详情
- 全文pdf
- 权力要求
- 说明书
- 法律状态
查看更多专利详情
下载专利文献
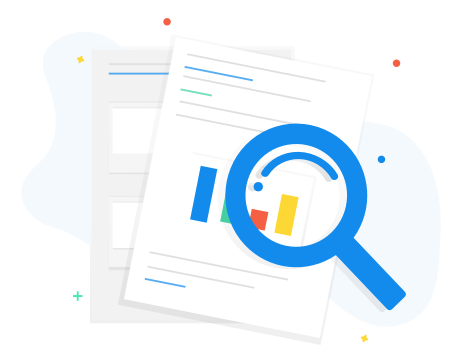
下载专利
同类推荐
-
孙显康, 黄志向J·S·德夫, T·托德
您可能感兴趣的专利
-
浅野修, 草谷拓也P·G·斯维斯茨P·G·斯维斯茨周群飞刘存海, 张佳管明贤, 冯桓任
专利相关信息
-
杨天奎张胜E.彼得斯姜文彬, 周雷